What is the current situation regarding 3D printing/additive manufacturing, its current impact, and what else we can expect from the technology in the future?
By Henrike Wonneberger, COO and Co-Founder of secure 3D printing platform provider, Replique
Manufacturers are facing some critical challenges that are reshaping the industry landscape. One of the most pressing concerns is the impact of climate change and the growing customer demand for sustainability. Consumers and subsequently regulatory bodies request more eco-friendly products, and this trend is driving manufacturers to reevaluate their processes and adopt more sustainable practices. However, implementing these changes while maintaining cost-effectiveness remains a challenge for many companies.
Another major challenge is the ongoing disruptions in the supply chain. The past few years have witnessed unprecedented events, from natural disasters to global health crises, that have severely impacted the manufacturing industry. These disruptions have highlighted the need for more agile and resilient supply chain processes. Manufacturers now face the pressure of minimizing lead times, ensuring consistent availability of critical parts, and optimizing production to cope with unexpected shifts in demand.
By adopting additive manufacturing (AM), we can pave the way for more sustainable and resilient processes. AM allows the production of parts on demand. Combined with a digital inventory, it further eliminates the need for physical warehousing and enables manufacturers to produce only the quantity of parts required, precisely when and where they are needed.
Furthermore, this approach greatly reduces waste, on the one hand, by eliminating overproduction and obsolescence in inventory, on the other hand, during the usage phase of products. The availability of spare parts on demand means that machines and consumer products can be maintained for longer periods. This extension of product lifetime contributes significantly to the Repair pillar of sustainability, alongside other principles like reuse, reduction, and recyclability.
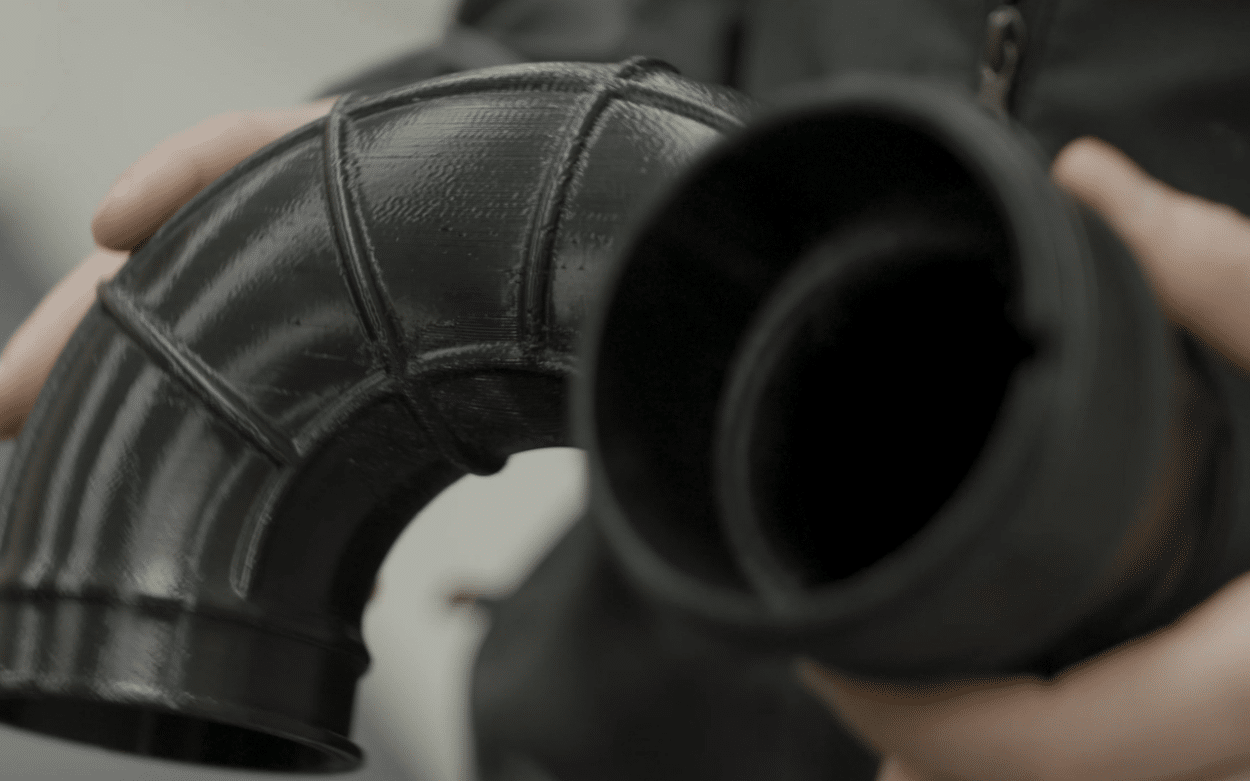
Opportunities for Manufacturers
The world of production has undergone a remarkable transformation. Personalized products and limited editions have become significantly more relevant and part variety rises continuously. The power of 3D printing lies in its ability to facilitate this challenge. Mass customization allows manufacturers to create products tailored to the unique needs and preferences of individual customers.
Unlike traditional manufacturing methods that need costly production molds, 3D printing offers the advantage of low ramp-up costs and rapid prototyping. Only a 3D printable design is needed to start production.
And by that, it also allows manufacturers to reproduce spare parts that were not available anymore, without the burden of having to create highly expensive molds.
Another key benefit of 3D printing is the freedom it provides in design. 3D printing enables the design of intricate structures that were not possible with conventional manufacturing methods. As a result, manufacturers can now explore new design possibilities and innovate with sustainability in mind, by creating lighter and more efficient products.
Lastly, 3D printing also empowers a reevaluation of supply chain strategies, from make-to-stock to production on-demand. This newfound flexibility allows manufacturers to respond rapidly to changing market demands and optimize their production processes for higher efficiency.
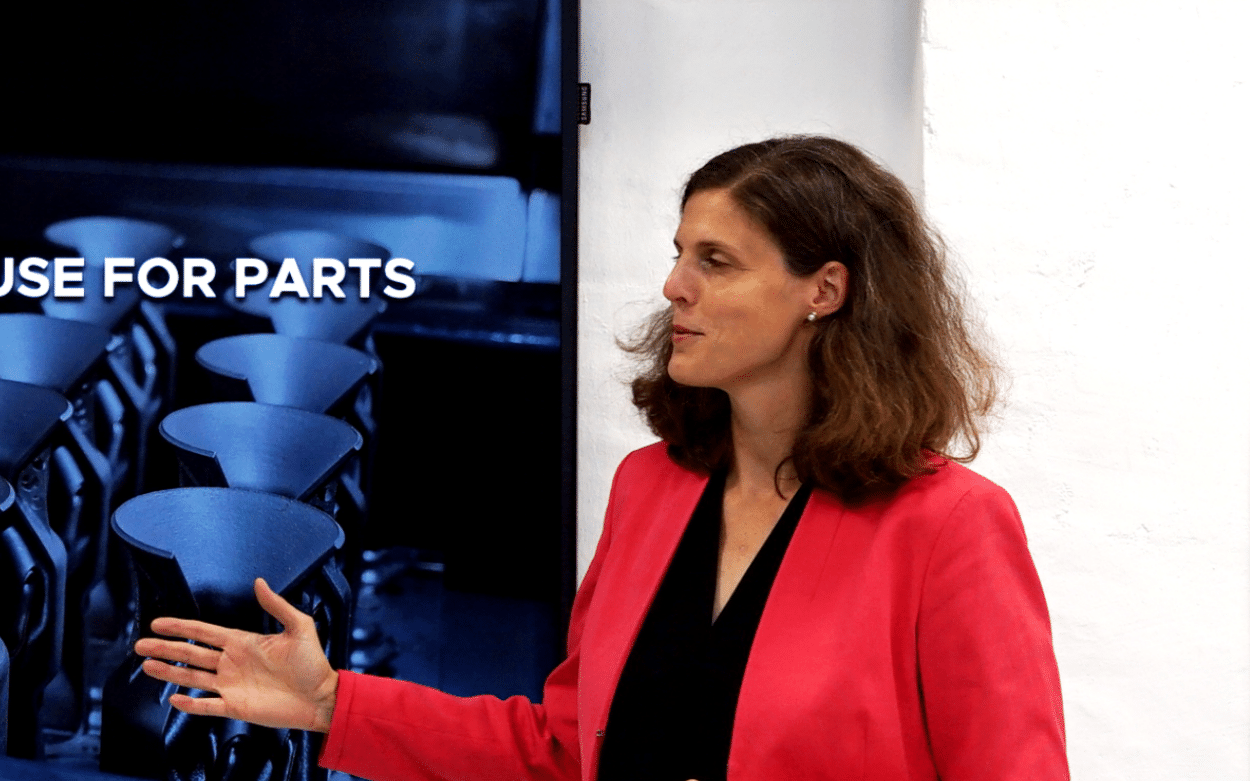
The Next Era of Additive Manufacturing
The next significant change in AM will be driven by advancements in materials and process automation. As new materials evolve and enhance properties, AM will gain broader industry acceptance.
In addition, costs must come down for 3D printing to be used in larger series. Pellet printing exemplifies innovative cost reduction by simplifying the material manufacturing process in polymer printing. Real-time monitoring, a top priority for industrial firms to ensure quality, will further drive widespread adoption during the printing process. This will help solve any issues as they arise and maintain the desired level of quality.
Nevertheless, in the coming years, more training and education in companies and universities will be required to truly scale up.
It is fascinating to see how things are already changing in the manufacturing industry right now. More and more companies are starting to realize the potential of 3D printing. They are reaching out to us for support, whether it’s for small series or spare part production.
For the next five years, I see an even stronger uptake of AM among manufacturers. As 3D printing continues to evolve, parts will be intentionally designed for it from the outset. It will become an integral aspect of supply chains and a standard practice across various industries. This shift will enable companies to achieve more sustainable and cost-effective manufacturing processes.
For that change, standardization and process qualification will play a crucial role in enabling additive production according to industrial standards.