The K trade show was held last October in Dusseldorf, Germany. This fair is dedicated to the plastics industry and is held every 3 years. This year, the focus was on recycling. Our industry analyst Francesco D’Amore went there. Here are the key elements he brought back from his tour.
Global plastic production is around 380 million metric tons every year, according to Plastic Oceans. For Statista, the year 2021 saw an increase in that number with a total of 390 million metric tons of plastic being produced.
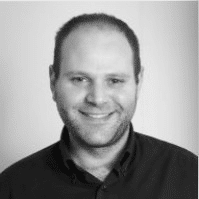
Consequently, plastic pollution is growing as waste management and recycling fall short, says OECD. Million tons of plastic bags and plastic bottles are still polluting our oceans. The organization estimates that globally, only 9% of plastic waste is recycled while 22% is mismanaged.
K is a German fair dedicated to the plastics industry. If the production of plastic remains a successful business model for many companies, an increasing number of them are taking the problem of plastic waste and pollution seriously. And are taking action to bring solutions to it.
Our DirectIndustry expert Francesco D’Amore visited the fair and discovered how the plastic industry is moving towards a circular economic future.

What were the major trends you saw at the K show and which one stood out to you the most?
Francesco d’Amore: There were three major trends during the show: circular economy, sustainability, and digitalization.
The main topic, in my opinion, was the circular economy with an entire pavilion dedicated to the topic. It was organized by VDMA, the German mechanical and plant engineering association, and involved major players in the plastics industry such as Arburg and Engel, and in plastics recycling such as Erema.
The concept of the circular economy is the following: plastic is produced, used, and recycled. And it is the processing of the used and recycled plastics that is important. The plastic has to be reformed so that it can be used again in the manufacturing process.
Plastic material changes properties in the processing of recycling. It is transformed. This is the tricky part of the process because in order to be used again, the properties of plastic materials must change as little as possible.
Erema is one of the leaders in plastic recycling and their goal is “we close the loop” and I thought that was very strong. They take used plastic, recycle about ten different materials and produce 60 different types of new products, from toys to shampoo bottles.
The Ellen MacArthur Foundation also gives more information about the concept of the circular economy if you want to know more about it.
In terms of sustainability, the efficiency of the machines such as granulators was a key topic.
And in terms of digitization, I found Engel’s new solution very interesting.
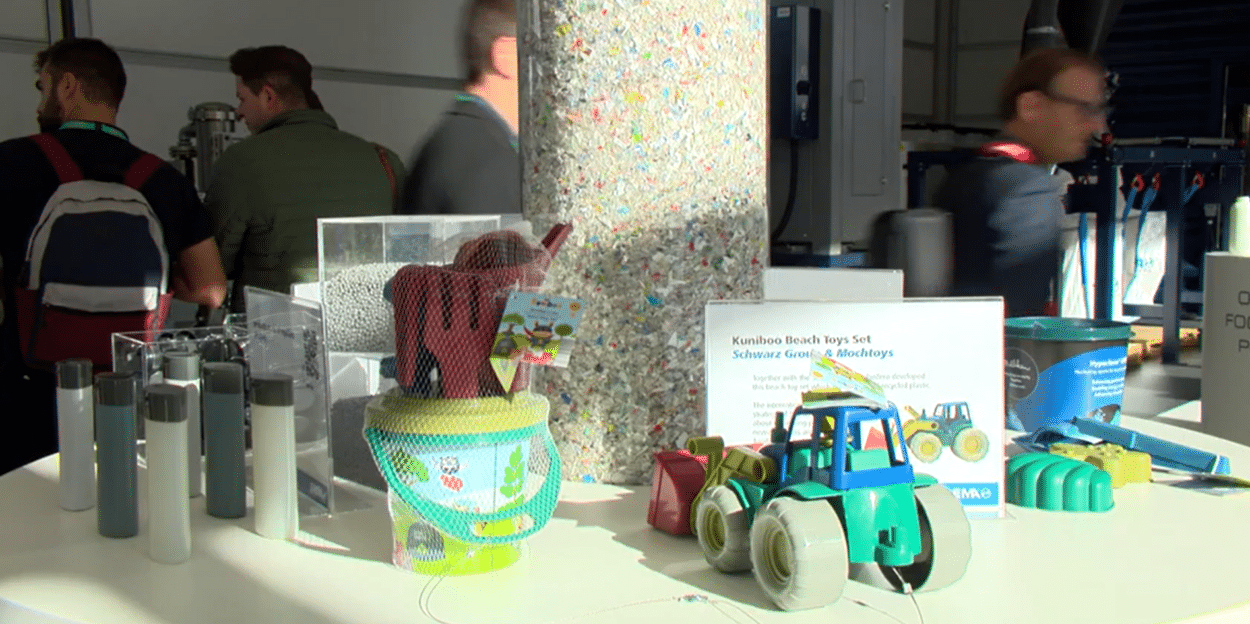

Can you tell us why this digital innovation has impressed you the most?
Francesco d’Amore: What impressed me the most was the innovation unveiled by Engel, one of the world leaders in plastics processing. Like Erema, they are developing the concept of the circular economy. But they are also developing digitalization and process monitoring.
They presented their Inject 4.0 solution, a software for monitoring and controlling the injection molding machine. It allows one to control step by step the machine parameters and to modify them according to what is happening (weight, mold closing movement, temperatures…). For example, if the closing force is not adapted, there can be anomalies in the pieces (slime or burnt material). With this system, the software automatically calculates the mold breathing and adapts the closing force according to it. In this way, it is possible to considerably reduce scraps.
This solution has been integrated into a machine dedicated to the manufacture of thin-walled plastic packaging. It has allowed the machine to be more efficient with cycle times of less than 3 seconds and the ability to handle thin-walled geometries.
What I find interesting is that this digitization system improves performance and the quality of the products they manufacture afterward.

What did you learn about the role of color sensing in the plastics industry?
Francesco d’Amore: I could understand the importance of color sensing for this sector, especially with the solution developed by Konica Minolta. Color sensing is key to defining the color and brightness of plastic.
Konica Minolta introduced for the first time a spectrophotometer equipped with a 60° gloss sensor that allows a simultaneous measurement of color and gloss that improves work efficiency. Until now, the company produced spectrophotometers on one side and gloss meters on the other. Now they have combined these two functions into one device.
It is more convenient for the operator. In only one action, he or she can measure both the color and brightness of the surface of the plastic sample. The measurement is therefore more precise and efficient.
They use a diagram developed by CIELAB, that allows the characterization of surface colors. Each color has its own number and is no longer subjective. The color chart allows defining the brightness and two parameters to define the distance of the measured color of a gray surface with the same brightness. And they set up their device according to this color chart.
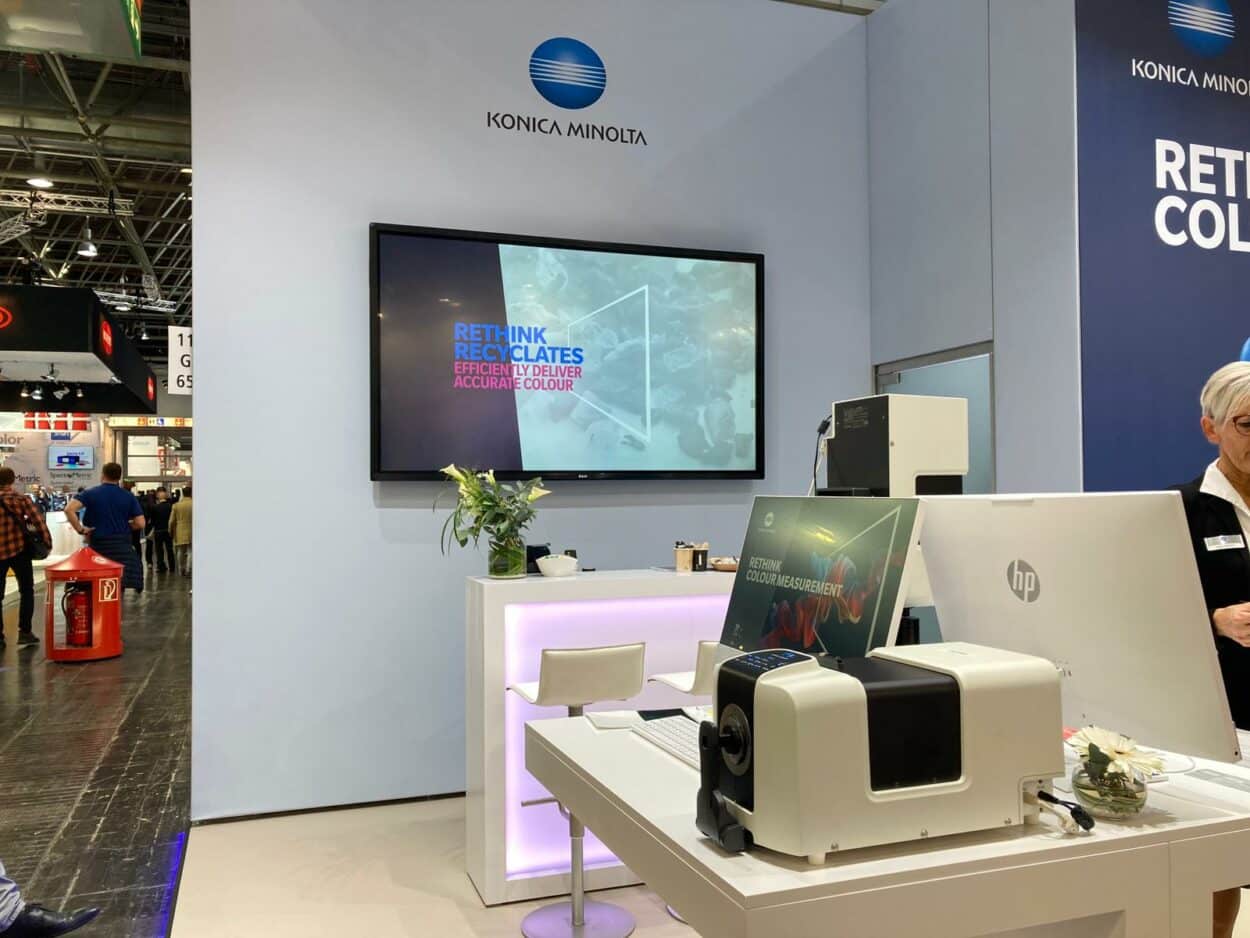
About Francesco d’Amore | Francesco d’Amore is an Italian mechanical engineer with a major in industrial production and manufacturing processes. He started his career in the automotive sector at PCMA, an Italian company of the Magneti Marelli group specializing in plastic injection systems. His team was supervising the manufacturing of plastic components like pedals and hand brakes. He joined DirectIndustry in 2012 as Industry Expert in charge of selecting the best industrial products. |