Fikret Kalay, Senior Manager for Autodesk Research’s Manufacturing Industry Futures group, explains how generative design has revolutionized the way the automotive industry designs parts. Autodesk is collaborating with several car manufacturers including General Motors and Volkswagen.

What is generative design, and how is it different from traditional design methods?
Fikret Kalay: Generative design is an AI-based design approach that allows designers to input constraints such as points of fixation, loads, and materials. The algorithm then explores an infinite number of design possibilities within these constraints and presents several solutions. The designer then chooses the best solutions and modifies them based on practical considerations such as size, weight, and maximum deformation.
The key difference between generative design and traditional design methods is that generative design starts with a set of constraints and explores all possible design solutions within those constraints. Traditional design, on the other hand, starts with a preconceived notion of the final product and works to achieve that outcome.
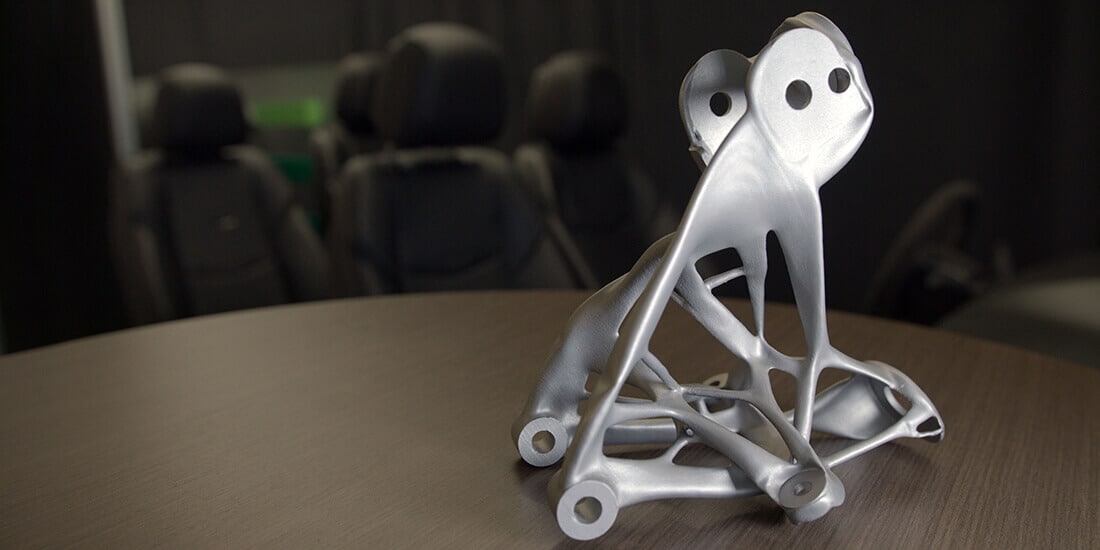

How has generative design impacted the automotive industry, and why are companies like General Motors interested in it?
Fikret Kalay: The automotive industry has been one of the biggest beneficiaries of generative design. Companies like General Motors have been interested in generative design because it allows them to optimize their designs to reduce weight and increase strength. For example, GM wanted to design a vehicle with 100% 3D-printed parts. However, printing each component separately would not be cost-effective or industrially feasible. Thus, GM approached Autodesk to develop an optimization tool that would allow them to create a design that meets their requirements.

What kind of tool did you develop for them?
Fikret Kalay: The part GM wanted to produce is a seat attachment, which is made of aluminum, and gathers in one piece the equivalent of 9 components. Our algorithm was able to design a piece that keeps the fixing points as if it was made of 9 parts but it is a single part. Besides, the new piece is 40% lighter and 20% stronger than the original one. So it’s a huge gain for the manufacturer.

What are the benefits of using generative design in manufacturing?
Fikret Kalay: The benefits of using generative design in manufacturing are numerous. It allows companies to explore an infinite number of design possibilities within specific constraints. This results in designs that are more optimized and efficient and parts that are lighter but stronger. Companies can also manufacture more complex parts that would be difficult or even impossible to make using traditional manufacturing methods.


What are the limitations of using generative design in manufacturing?
Fikret Kalay: While generative design offers many benefits, it also has limitations. Not all parts can be manufactured using additive manufacturing, and some parts may require a combination of additive and traditional manufacturing methods such as machining and plastic injection. We decided to integrate the manufacturing process as a constraint into the system.
For example, if I want to machine a part with a 3-axis machine, the algorithm integrates these manufacturing constraints and explores the design possibilities with these constraints. As a result, instead of having a very organic, slender shape, we will have a heavier, more compact part, which is manufactured but also more optimized. The algorithm can output the design according to the manufacturing methods.

What are your future projects?
Fikret Kalay: In the future, we would like to embed sensors and IoT in the components, to retrieve information and automatically feed the generative design engine with data so that the next iterations are even more optimized, respond better to problems, and perform better. We are working on R&D projects for the next few years.
We are also working on a generative design that integrates sound constraints. Let’s take the example of a sound wall to protect a house on the side of a freeway. We could optimize these walls according to the sounds we hear, and build custom walls that can absorb the sound and give the most optimized shape. It is the same with car engines that make noise. Generative design could allow us to design parts that absorb those sounds.
For electric vehicles, generative design can help manage the number of electrical cables that run from the front to the back of a car. Today, this is manually assembled. Tomorrow, we could use 3D printing, and print the electrical networks directly on the parts of the car.