In the race to decarbonize hydrogen production, most attention is directed toward electrolysis. However, French deeptech startup Sakowin is pursuing a different path: methane plasmalysis. By employing plasma to split methane molecules into clean hydrogen, Sakowin’s innovation offers a more energy-efficient and scalable route to low-carbon hydrogen—without emitting CO₂. The company is preparing to install its first industrial pilot at Swiss appliance manufacturer V-ZUG.
Why Clean Hydrogen Needs New Technology
Hydrogen has long been hailed as the energy of the future—a clean, decarbonized fuel poised to revolutionize energy-intensive industries. Yet, producing clean hydrogen remains a significant challenge. While “green hydrogen” generated via renewable-powered electrolysis is ideal in theory, it is currently expensive and energy-intensive. As a result, today, over 95% of global hydrogen is produced from fossil fuels (“grey hydrogen“), resulting in substantial CO₂ emissions.
Sakowin’s approach aims to decarbonize industrial processes by offering an alternative to electrolysis. The company has focused since 2017 on developing a system capable of producing hydrogen without CO₂ emissions, at large volumes, and at competitive costs.
To achieve this, Sakowin turned to methane (CH₄), the primary component of natural gas. In an interview with DirectIndustry, Pierre-Arnaud Sarda, Head of Sales at Sakowin, said that:
“Notably, producing hydrogen from methane requires five times less energy compared to splitting water molecules.”
The method developed by the start-up to achieve this result is called methane plasmalysis by microwaves. It allows the production of low-carbon hydrogen (turquoise hydrogen) from fossil gas (or biomethane).
Explore our infographics on the French hydrogen sector
How Plasma Produces Clean Hydrogen
How does this concretely work? Sakowin’s proprietary process utilizes plasma reactors to decompose CH₄ (methane) molecules into H₂ (hydrogen) and solid carbon. Plasma, the fourth state of matter, facilitates the decomposition of methane using microwaves.
“There is no combustion, no oxygen involved, and thus no CO₂. Instead, we obtain hydrogen and a fine carbon powder that can be reused in industrial applications,” explains Mr. Sarda.
Describing the Process with Technological Imagery
The equipment is based on a 100-kilowatt microwave system, where the reaction occurs. Electromagnetic waves are generated and directed into the reactor, generating the plasma. Methane gas is injected into the reactor, where it undergoes decomposition through over 400 intermediate steps, involving both thermal and electronic actions managed by the electromagnetic waves
At the reactor’s outlet, a secondary system separates the resulting carbon powder from the gas, yielding solid carbon and hydrogen gas ready for industrial use.
From four kilograms of CH₄, the process yields one kilogram of hydrogen and three kilograms of solid carbon, specifically a form known as carbon black (we’ll see later how this material is used).
One unit of equipment can produce two hundred kilograms of hydrogen per day, equivalent to half a megawatt-scale electrolyzer. Depending on the company’s needs, it can install multiple modules—for example, five modules if it plans to produce one ton.
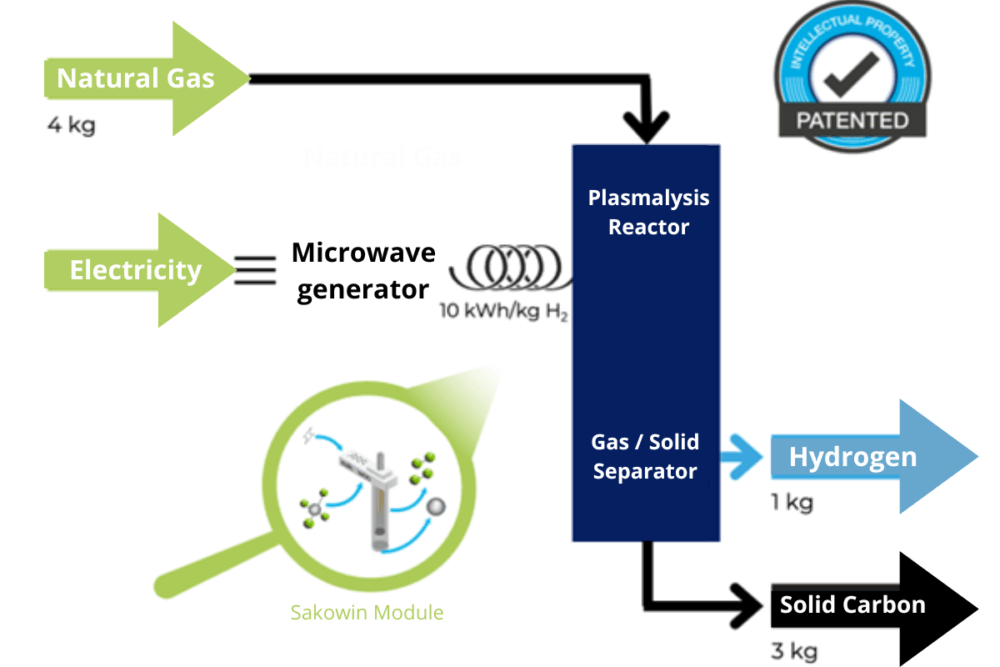
Advantages of the Process
One significant advantage of Sakowin’s process is the absence of electrodes or catalysts, which can degrade over time and contaminate the carbon product.
“Additionally, the use of microwave technology—a well-established industrial tool—facilitates rapid scaling and industrialization.”
The process is modular and scalable: small units can be deployed on-site near industrial users, reducing transport, storage, and infrastructure costs. These units can be housed in containers or dedicated rooms. But the technology is also available on-demand.
“This is a key advantage of our technology: it can be switched on and off almost instantly, which makes it perfectly compatible with intermittent renewable energy sources like solar or wind. In just thirty seconds, it starts producing hydrogen. If you need to stop, you can shut it down, and restart it just as quickly—without causing wear or damage to the equipment. That’s not the case with many other hydrogen production technologies, which often require continuous operation and are sensitive to frequent power cycling.”
Sakowin aims for an energy consumption of 10 to 15 kilowatt-hours per kilogram of hydrogen produced. In Europe, the company claims it can produce hydrogen for less than three euros per kilogram without subsidies.
From Lab to Industry
After years of R&D and successful lab testing, Sakowin is entering the industrialization phase. The company has developed an industrial pilot, presented to the press in late March, and is set to deliver it by the end of May to Swiss appliance manufacturer V-ZUG. This pilot, resembling a large container, will produce decarbonized hydrogen on-site, injected directly into the enameling furnace to reduce CO₂ emissions.
Sakowin’s technology is particularly suited for decentralized hydrogen production strategies, benefiting industries such as refineries, steel manufacturing, and glass producers. Industries reliant on natural gas flames for heat can integrate Sakowin’s technology at the end of their gas lines, capturing carbon in solid form and injecting hydrogen directly into furnaces, maintaining existing infrastructure while reducing CO₂ emissions.

And What About Carbon?
If Sakowin’s process doesn’t emit CO₂, what happens to the solid carbon produced alongside the hydrogen?
For the startup, this byproduct isn’t waste—it’s a valuable resource. The resulting carbon black, a fine solid carbon powder, represents a 12-million-ton global market.
“Carbon black is far from a liability,” Mr. Sarda explains. “It’s an industrial material in high demand.”
Currently selling for around €1,000 per ton, carbon black is primarily used in the manufacturing of industrial rubber, especially tires, which account for nearly 80% of its usage. It’s also essential in asphalt production, where manufacturers need both high heat and lower CO₂ emissions.
“In these industries, Sakowin’s technology could kill two birds with one stone—helping them generate clean hydrogen energy while also supplying a key raw material for their primary activity.”
Some may even see it as an opportunity to diversify. With Sakowin’s modular setup, industries can operate independently, producing both hydrogen and usable carbon on-site.
For companies interested solely in hydrogen, Sakowin offers a full-service model—handling the carbon black collection, logistics, and resale to carbon black manufacturers, all as part of a value-added service. Beyond tires and asphalt, this carbon could also be used in new concrete formulations, appealing to the construction industry.
“We won’t scale this technology unless we find a viable solution for the carbon byproduct,” Mr. Sarda emphasizes. “We’re already involved in EU-funded programs exploring large-scale applications for carbon black.”
Sakowin is also collaborating with companies like Eramet to explore closed-loop systems, where both carbon black and clean hydrogen are reused internally to help decarbonize silicon and manganese production.
And what’s the bottom line for industrial clients?
“At under €5 per kilogram of hydrogen, they start paying serious attention,” Mr. Sarda says.
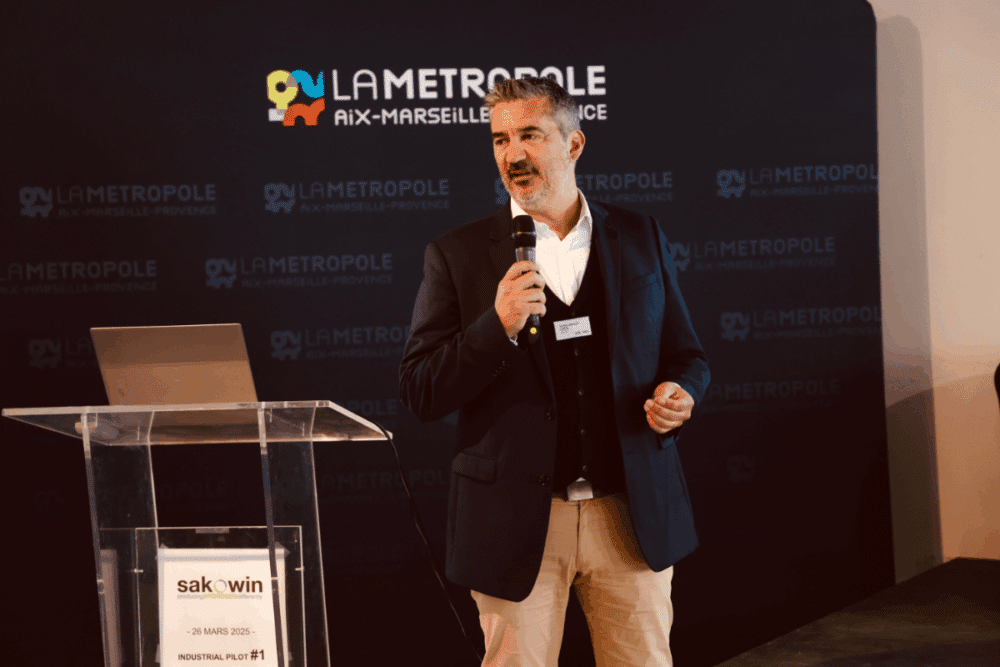
What’s Next for Sakowin?
With patents secured and key industrial partners on board, Sakowin is now shifting into scale-up mode, aiming for commercial deployment by 2026. The company plans to manufacture 60 hydrogen units per year, and in addition to the Swiss pilot project, three more pilots have been signed, with around twenty additional deployments planned across Europe, the U.S., and Canada.
Despite environmental policy shifts in the U.S. — including under the new Trump administration less focused on clean energy — Sakowin remains confident in the American market.
“Individual U.S. states often set their own energy agendas, independently from the federal government,” says Mr. Sarda. “And there’s another huge advantage: natural gas prices in the U.S. are very low, which makes our hydrogen extremely cost-competitive.”
Canada is also high on their radar, especially for mobility applications like trucks and cars, where cold climates make electrification more difficult.
“Hydrogen becomes a particularly attractive energy vector in cold environments,” he explains. “And Canada offers two major advantages: abundant natural gas and mostly hydro-powered, green electricity.”
To support its next phase of growth, Sakowin is currently raising funds to build its first full-scale factory in southern France, targeting a production capacity of 600 machines per year by 2027.
Interested in hydrogen innovation and clean tech? Read our previous stories: