Otto Motors has become a key player in the development and deployment of Autonomous Mobile Robots (AMRs). With over 15 years of experience in the automation sector, the company has pioneered solutions that streamline material handling in manufacturing environments. They were acquired by automation leader Rockwell Automation. We met with Sheldon Zimmerman, Director of the Automotive Team at Otto Motors, during Rockwell’s Automation Fair in California last month.
The Foundation of Otto Motors
Otto Motors, a company dedicated to revolutionizing material handling, specializes in autonomous mobile robots (AMRs). These robots, autonomous forklifts and mobile platforms with various payloads, are designed to autonomously move materials in manufacturing settings. The goal is to reduce the need for manual labor and enhance operational efficiency. With a history spanning over 15 years, Otto Motors has amassed over 7 million hours of operations in mission-critical environments, earning a reputation as a pioneer in the AMR industry.
We met with Sheldon Zimmerman, Director of the Automotive Team at Otto Motors, during Automation Fair in California last month. He shared insights into the company’s journey and its vision for the future.
According to him,
“We often joke that we need to count in ‘dog years.’ The pace of innovation is rapid, and Otto Motors is proud to be at the forefront of this transformation.”
READ ALSO
The Role of Otto Motors in Production Logistics
Otto Motors has emerged as a critical player in production logistics, especially after being acquired by Rockwell Automation last year. This acquisition aligns with Rockwell’s vision of creating a fully connected factory floor, where AMRs serve as the essential physical link in material handling processes.
According to Zimmerman,
“Every piece of automation, every device, and every piece of software functions as a bespoke tool in the manufacturing toolbox. Production logistics enables the integration of all these tools into a cohesive and holistic system, streamlining automation across the manufacturing environment. For instance, we utilize a palletizing robot that loads pallets onto AMRs, which then efficiently deliver materials to where they’re needed. Otto serves as the critical physical connection within this system.”
In many manufacturing environments, tools and automation systems often operate in silos, limiting efficiency. Otto Motors bridges these gaps, enabling a seamless flow of goods across the factory floor by transporting materials between these disconnected “islands of automation.”
Digital Integration: The Backbone of Production Efficiency
While the physical movement of materials is fundamental, Otto Motors also emphasizes the importance of digital integration to optimize production processes. The integration of AMRs with systems like ERP (Enterprise Resource Planning), predictive maintenance tools, and fleet management software enables smooth, synchronized communication across operations.
At the center of this integration lies Optix, a middleware platform that Zimmerman describes as the “Rosetta Stone” of the factory floor. Optix facilitates seamless communication between diverse systems and devices.
For example, it manages key tasks such as optimizing routes and coordinating intersections to avoid bottlenecks. It ensures materials arrive at the correct time and place and maintains production flow. It also acts as a “traffic cop” that prioritizes critical deliveries, coordinates workflows, and keeps material movement synchronized to avoid mismatches.
Zimmerman explains,
“In production logistics, the goal is not just moving materials; it’s ensuring they arrive at the right place at the right time, without disrupting the flow of production.”
The Optix Layer also manages integration with other bespoke automation systems. This includes communicating with Programmable Logic Controllers (PLCs), robotic arms, and collaborative robots (cobots), ensuring safe and efficient collaboration.
“It facilitates the handshake needed for integration, ensuring that the system knows when it’s safe for the AMRs to enter and work alongside other devices.”
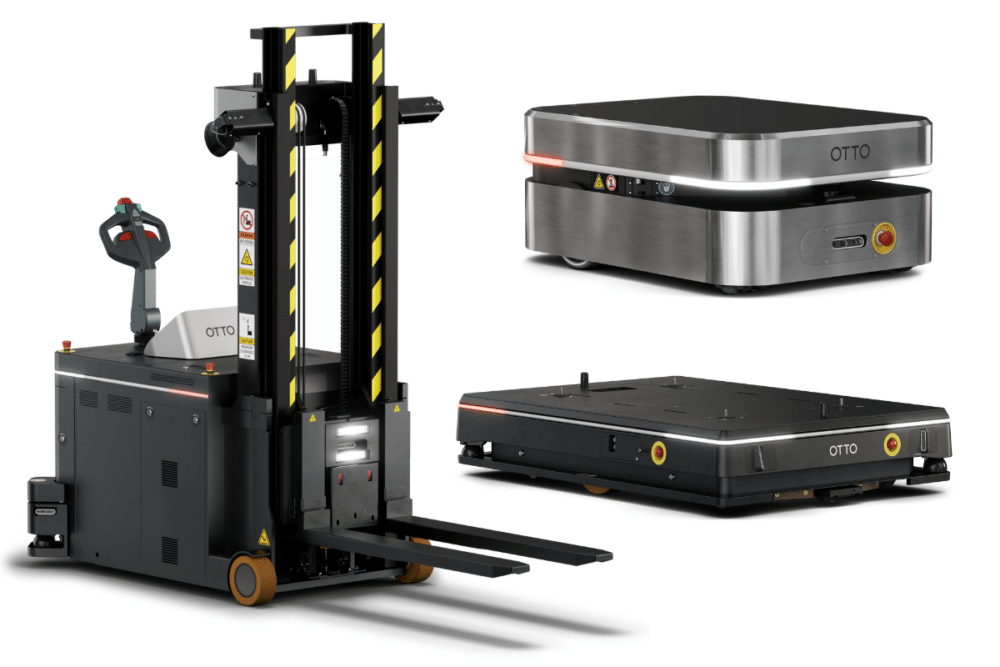
Optimizing Manufacturing Through Connectivity and Collaboration
The true strength of Otto Motors lies in its ability to enhance connectivity across the factory floor. AMRs communicate through a fleet management software layer that governs AMR-to-AMR interactions and optimizes workflows. Beyond internal communication, Optix enables interoperability between AMRs and external systems, forklifts, conveyors, and other automated tools.
At its core, production logistics relies on a middleware logic layer that governs communication and synchronization across all devices and automation lines. Above this layer, the ERP system provides job instructions and material requirements, while the middleware determines how and when materials are delivered.
Zimmerman emphasizes the broader vision, stating,
“Connectivity is the future of manufacturing. Our vision for production logistics is not just about adding robots to a factory; it’s about ensuring that everything – from AMRs to robotic arms to ERP systems – is connected and can work together seamlessly.”
Through its integration with Rockwell Automation, Otto Motors enhances production throughput, optimizes floor space, and improves overall operational efficiency. By bridging the physical and digital layers of production logistics, Otto Motors delivers a solution that enables manufacturers to scale, adapt, and optimize their operations in a connected, collaborative manufacturing environment.
Case Studies: Real-World Impact
Otto Motors’ AMRs have already made a significant impact in real-world applications. For instance, Mauser Packaging, one of Otto Motors’ clients, achieved a 600% increase in throughput after implementing Otto’s AMRs in its production process. Similarly, GE Aviation leveraged Otto Motors’ technology to integrate AMRs with collaborative robots (Cobots), saving $1.3 million in the first year of operation.
These case studies demonstrate the tangible benefits of implementing AMRs in manufacturing, from reducing costs to increasing productivity.
Otto Motors is now expanding its business and working with some of the largest automotive companies, including a top 10 global automotive manufacturer. For Zimmerman, collaborating with such organizations requires extensive upfront planning. This involves meticulously preparing for implementation and deployment to ensure a smooth transition. Minimal operational disruption is also a top priority.
“For example, over a long weekend this past September, we executed a two-day deployment of 12 AMRs in their body-in-white area. This rapid implementation showcases our ability to deliver results quickly and efficiently. Building on this success, they are now planning to expand with an additional 75 AMRs in the coming calendar year.”
This speed of implementation, combined with the ability to integrate solutions without disrupting ongoing production, is indeed critical for manufacturing companies which must maintain continuous production while deploying new technologies.
Watch our no comment video filmed at Automation Fair
Future Outlook: Expanding Capabilities and Advancing Technology
Looking ahead, Otto Motors plans to expand its range of AMRs, offering higher payload capacities and more diverse applications for industries across the globe. Zimmerman notes that Otto Motors is continuously innovating to meet the evolving needs of the manufacturing sector. The company is also exploring advanced technologies, including improved connectivity solutions, to further enhance the functionality and efficiency of its robots.
“The future of manufacturing is not just about more robots, but smarter robots that can work in a connected, optimized system,” says Zimmerman. “Our goal is to provide manufacturers with a flexible, scalable solution that can evolve with their needs.”
Price
Regarding the price, Zimmerman said
“Pricing is always solution-based, as it depends on several factors, including the complexity of the material movement, the type of attachments or tooling required for material transfer, and the overall integration complexities. Each solution is tailored to the customer’s specific needs, so there isn’t a fixed price.”
Pricing can also vary based on the number of vehicles needed, the type of material transfer, and the communication layers required for system integration. But Zimmerman was able to provide us with a base price for single vehicles without additional costs. For example: the list price for the Otto 100 starts at approximately $39,000 USD. The Otto Lifter is priced around $169,000 USD. The larger Otto 1500 is approximately $89,000 USD.