At this year’s Automation Fair in Anaheim, California, Blake Moret, CEO of Rockwell Automation, delivered an inspiring keynote address on the future of manufacturing and the pivotal role of automation in industrial processes. He also shared Rockwell’s ambitious vision of transitioning from industrial automation to industrial autonomy. Several partners joined him on stage, including Matt Rendall, the CEO of OTTO Motors. Here are the key takeaways from this presentation.
Making It Matter
10,000 people made the trip to California for Automation Fair, Rockwell Automation’s annual event. DirectIndustry was again invited to cover the fair. The theme of this year’s edition, Making It Matter, highlights how manufacturing is essential to solving global challenges. From ensuring access to food, clean water, and medicine to providing sustainable energy solutions, Blake Moret underscored the critical role of manufacturing in expanding human possibilities.
Over the past few years, Rockwell Automation has focused on resilience, acquiring and building world-class assets to optimize production, empower people, enhance sustainability, and accelerate digital transformation. Now, the company’s current focus is integration. Instead of adding entirely new capabilities, Rockwell is refining its existing portfolio to create seamless systems that reduce risk and make automation implementation simpler and more efficient.
“Certainly a big piece of that is the use of artificial intelligence we strongly feel and this is based on conversations with many customers that our best opportunities for adding real value to A I is making it a part of existing workflows. not to go in and to look at requiring ripping out existing processes because that’s just too risky.
Risk is indeed a significant barrier to investing in new technology. However, integrating AI into traditional value streams can, according to Moret, mitigate this challenge. For instance, AI can be applied at the sensor level through vision AI processing techniques, at the logic level with Logix AI, and at the software level using Guardian AI.
“These tools can extract information directly from drives and feed it into asset management platforms like Fiix within PLEX, enabling more effective demand planning.”
RELATED ARTICLE
From Industrial Automation to Industrial Autonomy
When Cyril Perducat, CTO of Rockwell Automation, joined the stage, he framed industrial autonomy as the next step in the evolution of automation. Drawing parallels to previous industrial revolutions, he described this shift as a natural progression driven by advances in AI, edge computing, data integration, and robotics.
This transformation aims to create self-organizing, flexible production systems that can adapt in real-time. By leveraging data from sensors, machines, and processes, these systems empower operators to focus on high-value tasks, while routine functions are autonomously managed.
“We’ve witnessed multiple iterations of industrial technology, but this moment represents an inflection point. The move from automation to autonomy is about building systems that adapt in real time and enable operators to make critical decisions.”
A recurring theme in his address was the importance of making technology intuitive and accessible. He emphasized that innovation should empower workers, not replace them. Technology should be designed to enhance human capabilities, not create fear or a sense of obsolescence.
“AI gives people superpowers. It’s about enabling workers to maximize their potential, removing the burden of unsafe, monotonous, or risky tasks, and allowing them to focus on the more engaging aspects of their work.”
He argued that human-centered design is not only an ethical choice but also a business advantage, helping manufacturers attract and retain talent in a competitive job market.
The Convergence of Technologies
Perducat also highlighted the convergence of several key technologies—AI, integrated robotics, edge computing, and cloud solutions—as the foundation for the future of industrial operations. However, he warned that simply collecting data or deploying advanced tools is insufficient.
“Data alone doesn’t solve problems. We need to find the right balance between edge and cloud computing, based on the application and context.”
This balanced approach allows manufacturers to process data locally when low latency is crucial while leveraging the cloud for broader insights and scalability.
A key challenge, according to Perducat, is creating systems that are both flexible and optimized for different needs. He discussed Rockwell Automation’s commitment to open standards and interoperability, ensuring customers can seamlessly integrate new technologies.
“We want a world where customers choose technology because it’s the right fit, not because they’re locked into a specific system.”
Integrated Robotics and AMRs
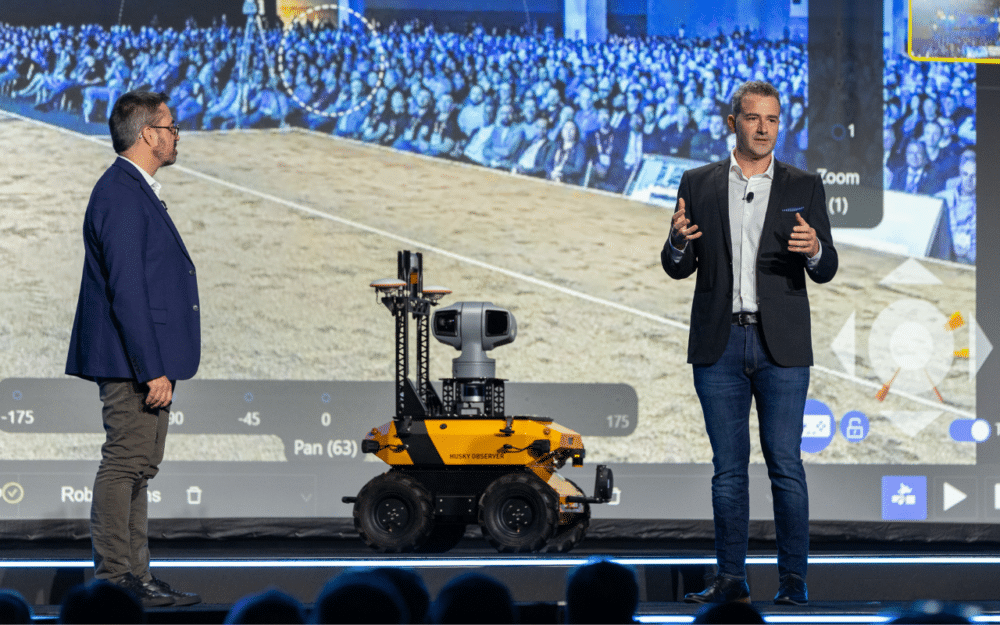
A Tool to Amplify Human Potential
After Cyril, Matt Rendall, CEO of OTTO Motors—a recent Rockwell Automation acquisition—delivered a presentation on the transformative potential of robotics in industrial operations. His keynote highlighted how autonomous mobile robots (AMRs) and advanced robotics are shaping safer, more efficient, and human-centered workplaces.
Matt emphasized that the true power of advanced robotics lies in its ability to elevate human capabilities. Drawing a parallel to excavators, he explained how technology can fundamentally transform productivity:
“By taking on dull, dirty, and dangerous tasks, robots enable workers to focus on higher-value activities like creativity, continuous improvement, and quality control (…) An excavator allows one person to do in an hour what once took 20 people an entire day. Similarly, AMRs in factories and warehouses can optimize material handling, reduce repetitive strain injuries, and make workplaces safer and more productive.”
Addressing Workforce Challenges with AMR
Matt highlighted the labor shortages faced by manufacturers, noting that many struggle to fill roles critical to maintaining operations.
“One of our Fortune 500 customers had to operate at only 75% productivity on a production line due to staffing issues. With OTTO, they reallocated their workforce, restored full capacity, and avoided shutting down operations.”
AMRs: Beyond Material Movement
While AMRs are often associated with simply moving materials from point A to point B, OTTO Motors envisions a much broader role for these robots. Equipped with state-of-the-art sensors, computing power, and software, OTTO’s AMRs are not just capable of transportation but also data collection and processing. These robots are data machines, constantly gathering information as they perform their tasks, providing valuable insights into production processes.
“Each AMR is essentially a data collection device, helping manufacturers pinpoint inefficiencies and bottlenecks in their workflows.”
For example, by tracking the movements of materials across the production floor, OTTO’s robots can identify where slowdowns are occurring and highlight areas for continuous improvement.
“When you combine an AMR with a data platform, you can uncover insights that were previously not possible.”
Mobile Manipulation: The Next Frontier
Taking the capabilities of AMRs a step further, OTTO Motors is exploring the concept of mobile manipulation—integrating AMRs with industrial robots to perform tasks that require both mobility and precision.
“By adding a robotic arm to our AMRs, we can enable them to not only move materials but also interact with the environment in meaningful ways.”
This innovation has significant applications across various industries. For instance, OTTO’s robots are being used to tend to chemical processes or high-value parts in manufacturing environments where traditional industrial robots might not be feasible due to space constraints.
One notable use case involves a bimanual industrial robot mounted on an OTTO AMR, allowing it to tend to machines in a CNC operation. This combination allows manufacturers to deploy robotic solutions without the need for significant infrastructure changes, making advanced robotics more accessible to a wider range of operations.
Husky: Pushing the Boundaries of Robotics
Matt also shared how OTTO Motors’ Husky platform is extending the reach of robotics beyond factories. Husky, which was invited on stage, is being used in rail yards, solar farms, and even Antarctic expeditions to study Emperor Penguins.
“Husky’s versatility shows how robotics can adapt to diverse environments for tasks like monitoring power grids and collecting data in extreme conditions.”
AI: Practical Applications
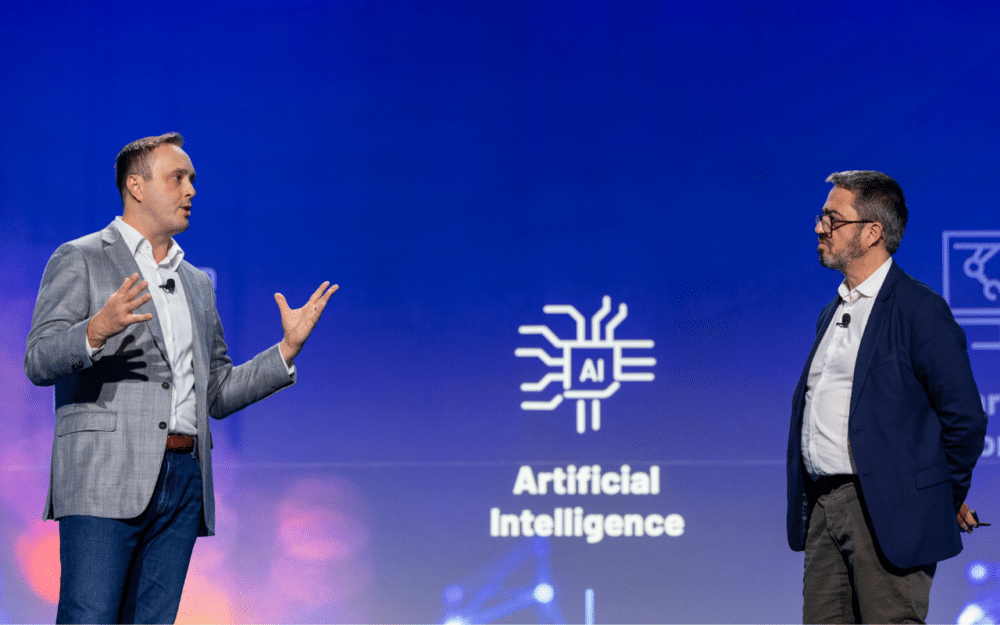
Jordan Reynolds, VP of AI at Rockwell Automation, offered a pragmatic and inspiring look into how artificial intelligence is transforming industrial operations. Far from theoretical, Rockwell’s AI solutions aim to address real-world challenges in design, runtime operations, and maintenance.
“What we’re fundamentally interested in is incorporating AI’s capabilities into the production functions we serve, enabling self-learning systems that adapt to changing conditions and solve complex optimization problems.”
The focus is on making AI practical and accessible across every stage of the production lifecycle, from design to operations and maintenance.
Design is indeed one of the most labor-intensive stages in manufacturing, often involving painstaking decision-making and programming. Rockwell is simplifying this with tools like the Emulate 3D platform, which creates digital twins that simulate production processes and test automation logic in a virtual environment.
The digital twin acts as a training gym for AI agents. And this enables systems to learn and adapt even in the absence of historical data. Adding to this is the FactoryTalk Design Studio Copilot, Rockwell’s AI-driven PLC programming tool.
“You can simply issue a natural language prompt, like ‘Write me a process to automate this bottling procedure,’ and it generates the code for you.”
The integration of generative AI with digital twins allows for faster design validation, creating a feedback loop that continuously improves system performance.
New FactoryTalk Analytics Vision AI
AI’s role extends into runtime operations. Jordan introduced Rockwell Automation’s very first machine vision system for quality inspection. FactoryTalk Analytics Vision AI is a neural network-based quality inspection system. Using cameras to detect defects on production lines, the system learns from examples of “good” and “bad” products rather than relying on pre-programmed rules.
“Once defects are detected, LogixAI steps in to determine what parameters to adjust to eliminate those defects.”
This integration between sensing and control creates autonomous closed-loop systems that optimize production processes in real-time.
Revolutionizing Maintenance with Predictive AI
Predictive maintenance has long been a challenge in manufacturing, often requiring extensive sensor installations and historical data. Rockwell’s Guardian AI simplifies this by leveraging existing sensors, like those embedded in variable frequency drives (VFDs), to detect anomalies in motor behavior.
“Guardian AI plugs into VFDs, performing anomaly detection without requiring additional sensors.”
When paired with Rockwell’s Fiix platform, maintenance planning becomes proactive and optimized.
“Fiix uses machine learning to recommend the best maintenance strategies, from scheduling repairs to allocating resources.”
SDA (Software-Defined Architecture) as the Future of Automation
The final topic discussed during this year’s keynote presentation was the transformative potential of Software-Defined Architecture (SDA) in industrial automation. The keynote was presented by Dan DeYoung, VP of Rockwell Automation. SDA promises to revolutionize how automation systems are designed, deployed, and scaled.
What is SDA?
SDA represents a shift in how automation systems are conceived, moving away from hardware-centric models toward software-centric solutions. As there is a tremendous amount of data in motion today, there is an urgent need for computing capabilities that go beyond traditional systems. But, Dan clarified,
“SDA isn’t just about creating another type of virtual PLC. It’s about decoupling functions from hardware, allowing scalability and flexibility while reducing complexity in design and operation.”
Traditional automation systems often begin with the selection of hardware components like sensors, PLCs, and motors. DeYoung explained how SDA flips this paradigm.
“Automation engineers and designers typically start the design process knowing what hardware they will use. With SDA, we begin with software and programmatically define the architecture, leveraging modern tools like copilots, version management, and cloud computing, before even selecting the hardware.”
Key Advantages: Scalability, Adaptability, and Resiliency
One of the core advantages of SDA is its ability to scale, adapt, and remain resilient in the face of rapidly changing industrial demands.
The flexibility of SDA is especially evident in its ability to be tailored to industry-specific needs. DeYoung highlighted how SDA could revolutionize operations across different sectors, from life sciences to manufacturing.
“In life sciences, we can scale up from pharmaceutical manufacturing in large bio-reactors to small, tabletop bioreactors for personalized medicine. This can be achieved with common development, testing, and validation processes.”
This adaptability extends beyond scalability.
“Different industries have different needs, SDA enables us to tailor automation for industry variations in ways we couldn’t before, creating scalable solutions from small setups to massive industrial data centers.”
The Role of Edge Computing
Another critical element of SDA is its integration with the edge. DeYoung explained that Logix in industrial automation is now often applied at the edge of operations, where critical decisions are made.
“Logix isn’t just in control systems anymore. It’s in data centers, distribution centers, and even in everyday applications like grocery store checkout lanes. It’s where the most critical decisions are made, and SDA is designed to enable those decisions at the edge.”
This edge computing capability allows industrial systems to make real-time decisions without relying solely on centralized data centers. It also ensures that industrial applications can remain agile, responding to changing conditions quickly and efficiently.
Dan concluded by emphasizing that SDA is not a distant concept but a tangible reality.
“Everything we’re discussing today is real and ready for use.”