At first glance, fashion and industry may not seem connected. Yet, Dutch artist and designer Iris Van Herpen has successfully bridged the two worlds. By borrowing production techniques from industry such as 3D printing, laser cutting, and robotics, the artist aims to be a pioneer in applying new technologies to haute couture. Her work is currently showcased at the Musée des Arts Décoratifs in Paris (until April 28th). We visited the exhibition and found elements that resonate with the industrial professionals in our readership.
At DirectIndustry, we are more accustomed to discussing technological innovations applied to the industrial world than to the fashion sector. However, after attending the Iris Van Herpen exhibition at the Musée des Arts Décoratifs in Paris, it is clear that we have found multiple connections between the world of industry and the world of haute couture.
Art and Industry
With her breathtaking dresses featuring unique designs, 39-year-old Dutch artist Iris Van Herpen bridges the worlds of art, science, architecture, and industry. She has collaborated with several companies and organizations that we often interview, such as Stratasys, MIT, NASA, and Delft University. She even designed the Phantom Syntopia, a unique couture car model for the Rolls-Royce automobile brand.
The designer creates her dresses not with traditional sewing techniques and materials, but with tools more commonly found in factories (laser cutting machines, 3D printers, robots) than in designer studios.
We realized that if the artist uses industrial processes to create unique works, the industrialist is also capable of creating aesthetic, almost artistic pieces. Software like Autodesk‘s, equipped with AI, now offers highly optimized car part designs for car manufacturers, intended for 3D printing. Strangely, the resulting parts always have very geometric, organic, and even artistic shapes. Art and industry are ultimately not so far apart.
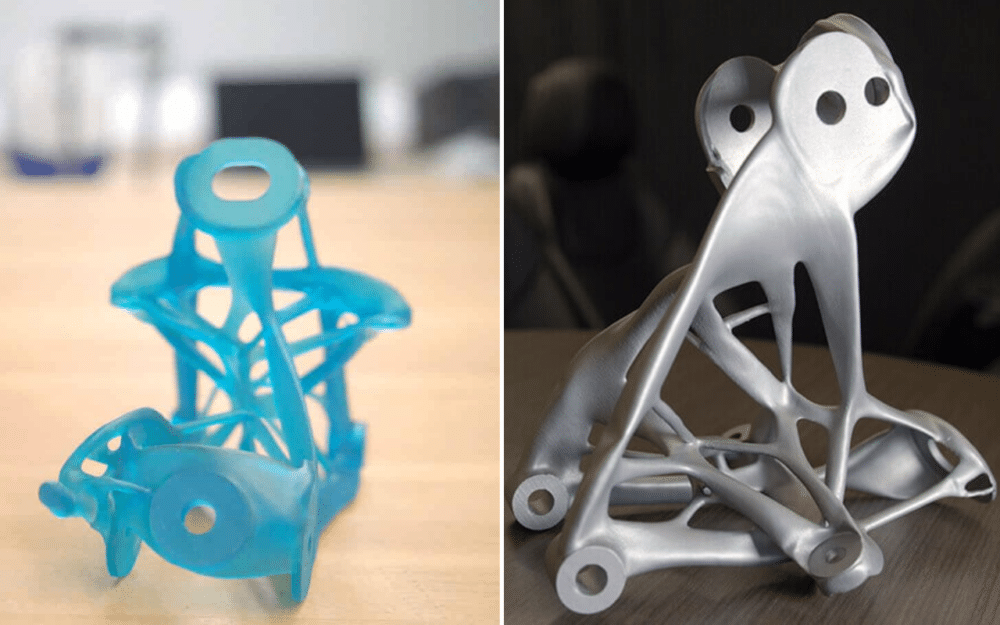
Therefore, we have decided to offer you this article on the technical and technological innovations mobilized by Iris Van Herpen to produce her magnificent dresses. Made from materials ranging from blown glass to Plexiglas, laser-cut metal, and biodegradable materials printed in 3D, these dresses are more than just haute couture. They stand at the intersection of science, design, architecture, art, and fashion.
Speaking of architecture, in 2019, the artist notably participated in the design of the wall facade of a building in Leiden (the Netherlands), the Naturalis Biodiversity Center. The building consists of 262 panels molded from concrete and marble powder.
Craftolution
Iris Van Herpen aims to be a pioneer in the use of new technologies applied to the world of haute couture. Until now, no artist has so seamlessly blended science, technology, and fashion.
Through numerous collaborations with researchers, architects, and engineers, Iris Van Herpen has succeeded in creating unique fashion pieces inspired by nature, the human body, marine biology, and even the Gothic architecture of her country. But she also draws inspiration from industry. The particle accelerator at CERN and colorful images taken by the James Webb telescope are just a few sources of inspiration for composing her works.
Aware that the fashion industry and the textile industry in general are extremely polluting, she also seeks to use biodegradable textiles, such as banana peels and cocoa.
For her, technology is a creative tool. She speaks of “craftolution”, a mix of artisans and innovation. Because it is thanks to the possibilities offered by new technologies that she has been able to translate into works of art things as subtle and complex to reproduce as the movements of the human body or the movement of water.
We have selected different types of industrial processes that she uses for her creations.
Thermoforming
In the Splash Dress, the splash is a hand-formed plexiglass plate by the designer to give it the appearance of moving liquid. Using scissors, and pliers, she cuts, distorts, stretches, and shapes an inherently elusive and unattainable element, pushing the boundaries of creativity in fashion even further.
Blown Glass
The Dimensionism dress is made of borosilicate glass, a glass highly resistant to heat. It has been thermoformed and worked with a flame. For this, the designer could rely on the expertise of a master glassblower, Bernard Weinmayer.
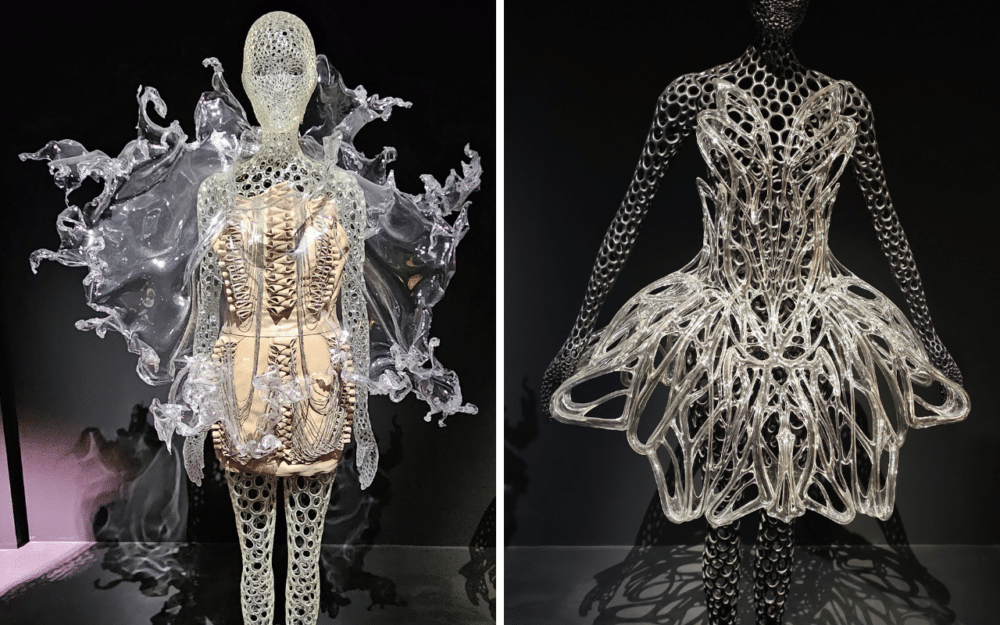
Laser Cutting and Water Jet Cutting
Many of Iris Van Herpen’s creations employ laser cutting or water jet cutting.
For example, the Aeriform creation contains a set of geodesic spheres made of galvanized steel that was cut with a water jet. This collection was inspired in part by CERN and the question of the energy that results from particle acceleration.
With the Magnetosphere dress, the artist uses plastic debris. Cut with a laser, this plastic found on beaches then forms layers of lace.
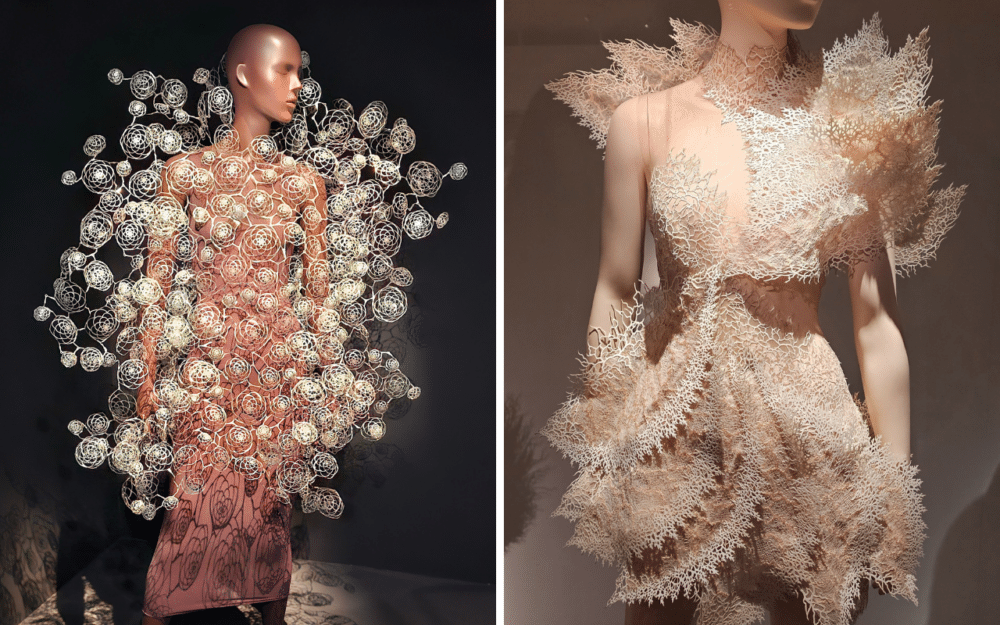
Robotics
In 2015, the artist enlisted three robots to print and weave a dress live during a fashion week event, worn by the Game of Thrones actress Gwendoline Christie.
The artist detailed the techniques used in a press release:
“The live process blends different techniques – laser cutting, hand weaving, and 3D printing into one dress, which spreads from the center, quaquaversal in its geometries.”
For the occasion, three ABB IRB 2600 robotic arms were used. She collaborated with the University of Innsbruck and their REXILAB robotic experimentation lab to enable this demonstration.
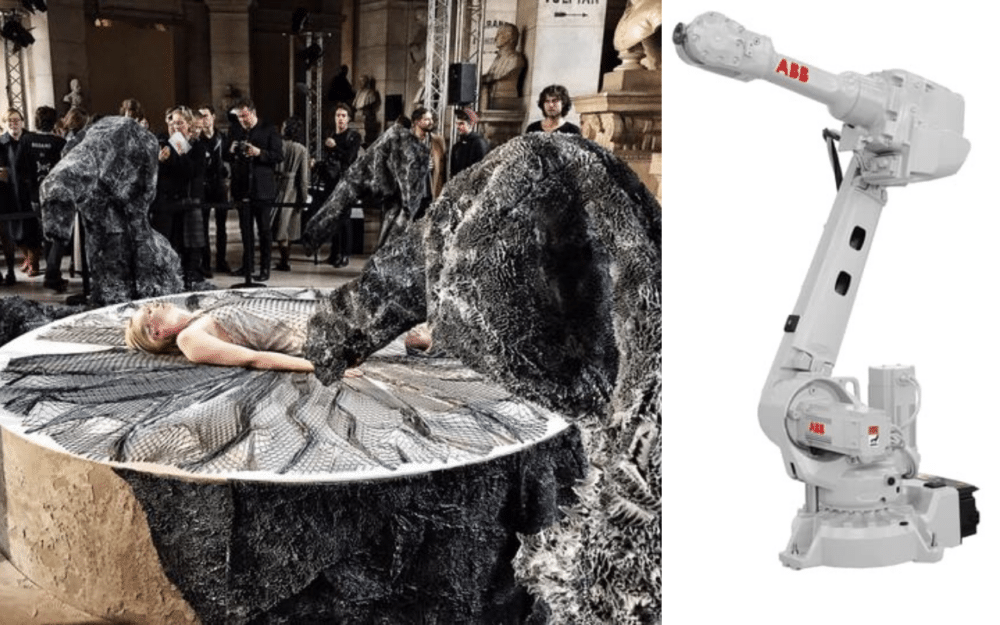
3D Printing
Iris Van Herpen began experimenting with additive manufacturing in the 2010s. At the time, she wanted to create a water dress but didn’t know how to achieve the liquid effect with available textiles.
“I couldn’t make the water dress in any way with a needle and a thread. About the same time, I saw architects making their maquettes with 3D printers. I became fascinated by this pioneering process and thought this could be my solution,” she recounted in an interview with Hans Ulrich Obrist.
Today, Iris Van Herpen is the designer who uses 3D printing the most in her work.
Here are some examples of 3D-printed creations and the different printing technologies involved.
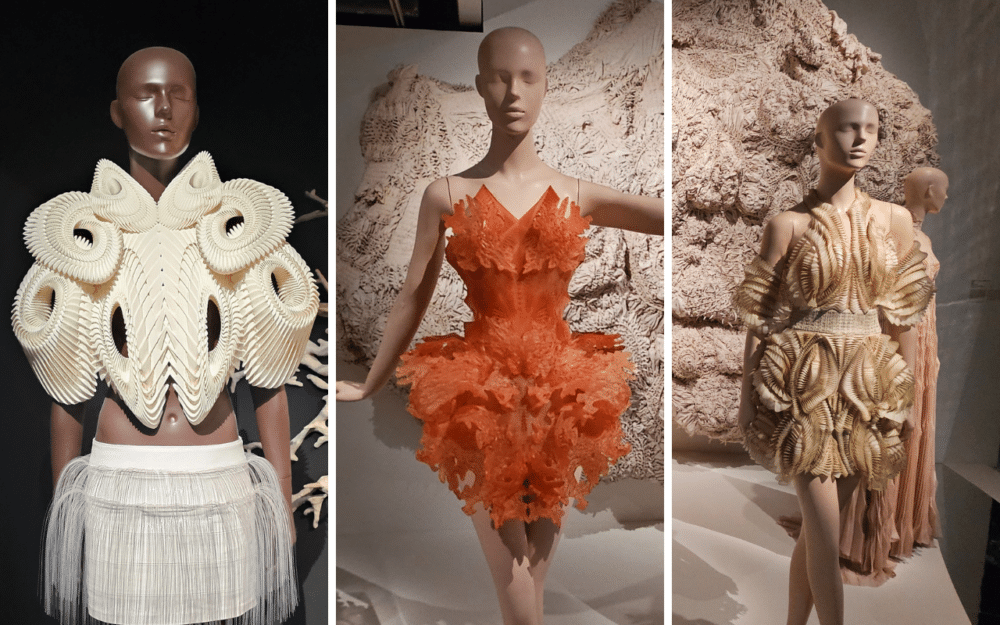
Crystallization: SLS Technology
In 2010, she collaborated with architect Daniel Widrig and digital manufacturers MGX by Materialise. The idea was to explore digital design techniques and digital fabrication applied to the world of haute couture. The first 3D-printed accessory, the ‘Crystallization‘ top, was unveiled at Amsterdam Fashion Week in 2010. Inspired by shell structures and fossils, it is 3D-printed from white polyamide using SLS (Selective Laser Sintering) technology at 0.1 mm thickness. It took 6 full days to print the garment.
In 2013, she presented two 3D-printed ensembles at Paris Fashion Week in acrylic and polyurethane inspired by coral. The skirt and cape were produced using Stratasys’ unique Objet Connex multi-material 3D printing technology. This allowed a variety of material properties to be printed in a single build. Both hard and soft materials were incorporated within the design.
To achieve this feat, she collaborated with Neri Oxman. At the time, he managed the no longer active Mediated Matter Group at MIT in Boston.
Hybrid Holism: Mammoth Stereolithography
In 2012, she collaborated with the company Materialise to use a new technique, Mammoth Stereolithography (MSL). This 3D printing technology uses UV rays to harden polymer materials. Thanks to this technology, it was possible to obtain honeycomb patterns.
Foliage: PolyJet
In 2018, Iris Van Herpen collaborated with the Delft University of Technology to use a process capable of simultaneously printing different materials, a property of the company Stratasys, called PolyJet technology. This technique allowed for the creation of a dress in which petal-shaped patterns of 0.8 mm were directly 3D printed onto tulle. 260 hours were required to print the dress.
Digital Modeling
In 2020, the artist also turned to modeling tools to virtually create her dresses. This practice is commonly found in architecture or industry.
For the Morphogenesis dress, for example, she relied on the Rhinoceros tool.
Printing with Eco-Friendly Materials
The textile industry, to which haute couture belongs, is one of the most polluting in the world. We have previously reported on the havoc wreaked by this industry in terms of water resource wastage and dye pollution. Additionally, garments, composed of materials that are not fully recyclable, often end up in overcrowded landfills in third-world countries.
Aware of the environmental impact of her field, Iris Van Herpen seeks alternative materials. She already incorporates plastic waste, particularly through collaboration with Parley For the Ocean. But she also explores other possibilities, including more organic, biodegradable textiles for her creations. Here again, technology comes to the rescue to make this possible.
For her 2022 project, Singularity, the artist teamed up with Eric Klarenbeek and Maartje Dros. Together, they developed a biotechnological method for 3D printing organic substances such as algae and mycelium. This collaboration resulted in several dresses made from leftover cacao bean shells transformed into biopolymers and printed as filaments.
For her Metamorphism creation, she designed dresses composed of sustainable off-white banana leaf fabrics.
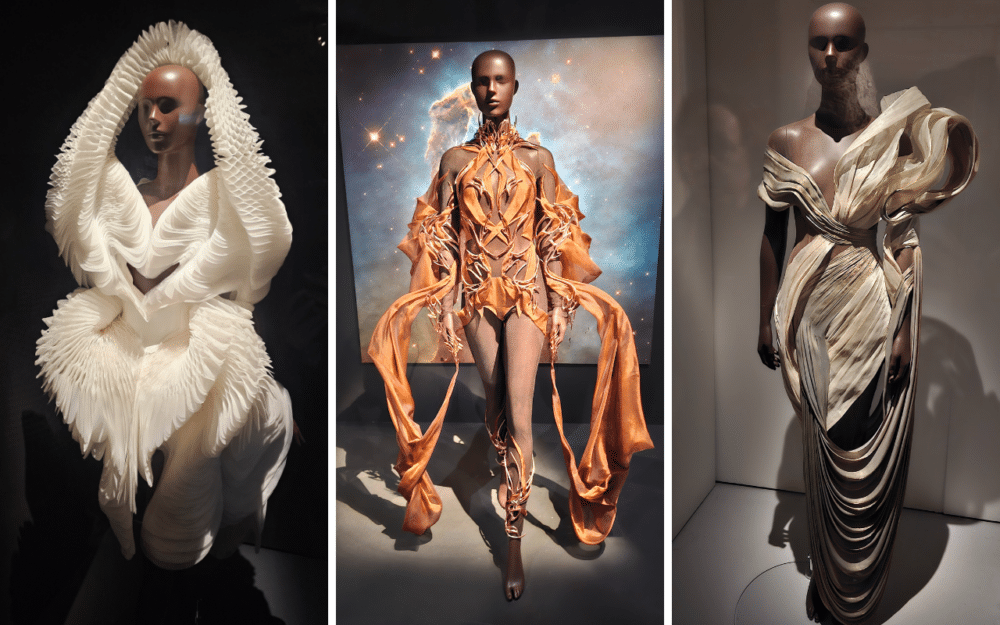
And Tomorrow, 4D Printing?
Iris Van Herpen is now exploring 4D printing. A few years ago, we published an article about the established Self-Assembly Lab of MIT and two of the biggest names in printing—Stratasys and Autodesk.
On their website, the Self-Assembly Lab detailed the 4D printing concept.
“With a single multi-material print, a product or mechanism can transform from any 1D strand into 3D shape, 2D surface into 3D shape, or morph from one 3D shape into another. Using only water, heat, light, or other simple energy input, this technique offers adaptability and dynamic response for structures and systems of all sizes.”
For Iris Van Herpen, the idea is to create dresses whose materials are capable of evolving over time, responding to movement, much like plants, for example. She collaborates notably with Philip Beesley, the designer of the living architecture system or hylozoism.
While 4D printing technologies are still under development, both the artist and industrialists closely monitor innovations in this sector.