At Logiconomi 2025, held last week in Marseille by Toyota Material Handling Europe, one message rang clear: Artificial Intelligence is no longer an option in logistics. From generative and agentic AI to autonomous robots and simulation-based physical AI, the technologies shaping tomorrow’s supply chains are arriving faster than most companies can adapt. As global supply chains confront volatility, labor shortages, and climate mandates, logistics leaders gathered to explore one question: How can intelligent automation become the core engine of resilience and growth? Here’s what we learned.
As global supply chains grow more complex, the logistics industry finds itself at a pivotal crossroads—where the pressure to perform meets the imperative to transform. Logiconomi 2025, hosted by Toyota Material Handling Europe last week, brought together industry leaders, technology innovators, and strategic thinkers in Marseille, France, last week to explore how logistics can evolve to meet the challenges of today and tomorrow.
Held in a time of unprecedented disruption—from post-pandemic recovery and labor shortages to energy volatility, environmental urgency, and geopolitical tension—the event, previously exclusive to Toyota’s clients and now for the first time open to the media, served as a laboratory of ideas and technologies.
From advanced robotics and AI-driven operations to the emerging frontier of Physical AI, the conference provided a glimpse into the smart systems that will define the next era of logistics.Through insights from thought leaders at Toyota Material Handling, Microsoft, Boston Dynamics, Gideon, and NVIDIA, we examine how intelligent automation is not only transforming warehouse floors—but also reshaping the very DNA of global supply chains.
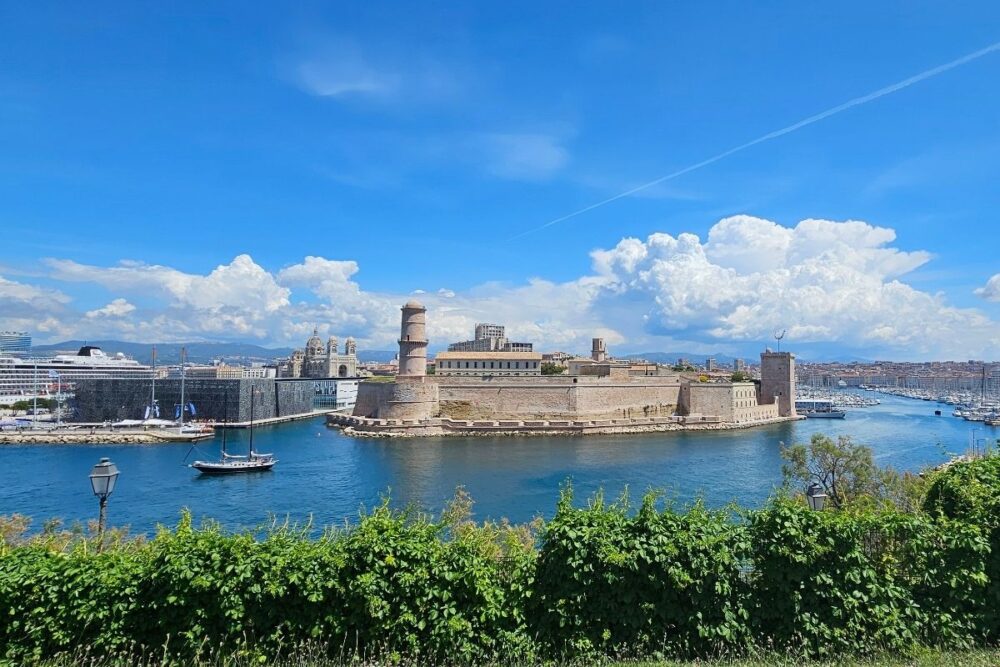
A Sector Under Pressure: Why Logistics Can’t Wait to Reinvent Itself
“If we were being tested in 2022, we are being tested again today—perhaps even more seriously.”
With these words, Ernesto Dominguez, CEO of Toyota Material Handling Europe, set the tone for Logiconomi 2025, acknowledging the relentless waves of disruption that continue to reshape the logistics landscape.
From pandemic recovery to the energy crisis, inflation surges, and a war at the edge of Europe, the logistics industry has had little time to breathe. And just as some challenges—like stock shortages and unstable supply chains—seem to recede, new threats emerge: global trade tensions, rising protectionism, and climate commitments being questioned or rolled back.
Meanwhile, labor shortages continue to grow. Experts predict a significant labor deficit—around 11%—within the next five years, potentially leading to an $8.5 trillion economic impact. This shortfall will heavily affect labor-intensive sectors like logistics.
Besides, the need to meet higher sustainability standards is more urgent than ever.
But for Dominguez, these are not just obstacles—they are catalysts for deep transformation. The industry can no longer afford to rely on legacy systems or incremental improvements.
“It’s not just about automation anymore,” he said. “It’s about rethinking the entire logistics model.”
At the heart of this shift lies a critical question: How can technology—and in particular, artificial intelligence—help logistics adapt, perform, and grow in a world defined by complexity and uncertainty?
That’s exactly where the conversation turned next. Taking the stage after Dominguez, Microsoft offered a powerful snapshot of where AI stands today—what it can already do for logistics, and how companies are using it to unlock real-time decision-making, predictive capabilities, and smarter resource management.
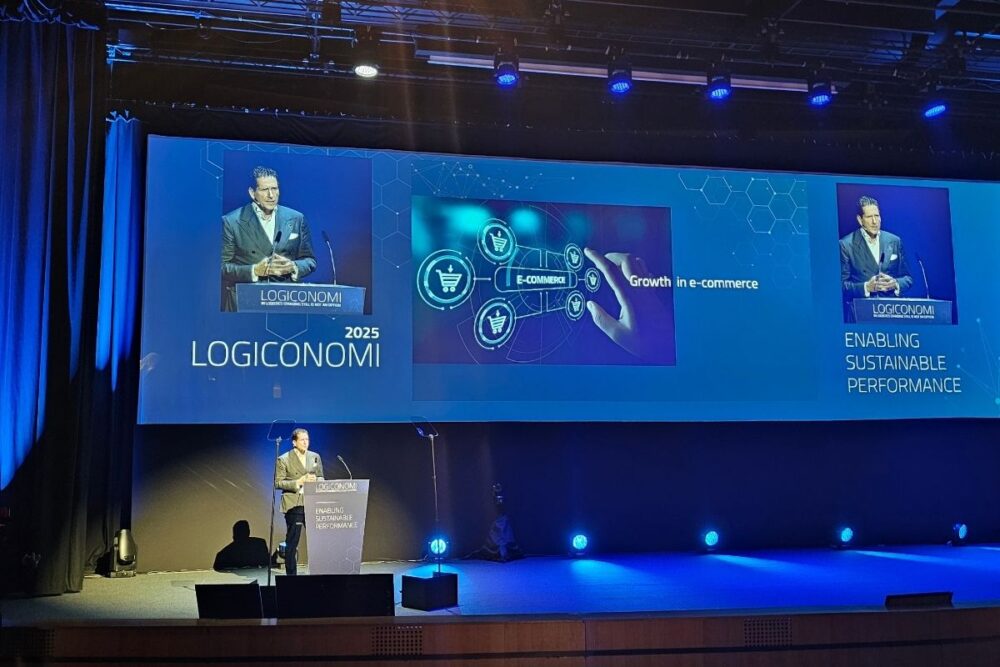
Interested in logistics? Check out our article on how Toyota Material Handling managed the entire logistics operation during last year’s Paris Olympics.
Artificial Intelligence as the Brain of the Supply Chain
Once confined to research labs, artificial intelligence is now at the heart of the world’s most advanced supply chains. Supply chains used to be reactive. Today, thanks to AI, they’re anticipatory, adaptive, and increasingly self-optimizing. AI is not just a tool, but the cognitive engine driving end-to-end supply chain transformation.
At the event, Ygal Levy, EMEA Manufacturing Managing Director at Microsoft laid out a compelling vision where generative AI doesn’t just support supply chains—it transforms them.
“What’s actually coming is agentic AI. AI is moving from copilots to autonomous agents. It’s not just assisting workers — it’s executing decisions, coordinating systems, and adapting in real-time. The use of generative AI to automate actions and reshape business processes, “says Ygal Levy.
In contrast to co-pilot-style assistance, the next frontier is AI that acts autonomously, dynamically adapting to disruptions, data inputs, and operational goals in real time.
That vision isn’t speculative—it’s already taking shape. Toyota Motors, for instance, has implemented a Virtual Obeya Room, an AI-powered collaboration space populated by specialized agents in areas like acoustics, customer feedback, and mechanical engineering. Employees can interact with these agents in natural language, brainstorm solutions, and accelerate problem-solving across departments.
At the warehouse level, companies like DHL and BMW are deploying generative AI for intelligent logistics orchestration.
DHL uses generative AI to manage its robotic fleet and simplify warehouse operations. At BMW, AI is used to orchestrate an entire fleet of logistics robots. Powered by digital twins, the system calculates trajectories, optimizes space, and enables seamless collaboration between heterogeneous robots — with zero human input.
This shift is driven by three enablers: the rise of universal interfaces (AI that anyone can use, no-code), contextualization capabilities, and advanced reasoning. Together, they allow AI to tackle the core pain points of logistics:
- Forecasting and Planning: AI-enhanced tools can now integrate external variables such as weather and geopolitical events for hyper-accurate demand forecasting.
- Fleet and Route Optimization: GenAI enables real-time route reshaping and fleet performance management with minimal manual input.
- Procurement and Supplier Management: Microsoft’s own supply chain has benefited from copilots that automate supplier scouting, summarize and compare contracts, and even assist in negotiation strategies.
“You see both productivity and accuracy gains—technology now supports insight-driven procurement,” Levy said.
These AI agents are also reshaping the daily workflow of logistics managers. With tools like Microsoft 365 Co-pilot Studio, logistics planners can auto-generate partner communications, update transport management systems (TMS), and simulate disruption scenarios—all without writing a single line of code.
Meanwhile, for warehouse managers, AI copilots can predict maintenance needs, optimize staff scheduling, and even monitor EHS compliance using computer vision.
“AI can now detect if a worker isn’t wearing the right gear and instantly trigger safety alerts,” said Levy, highlighting how automation supports not just efficiency but well-being on the floor.
As Levy put it, this is a “step change” moment—AI doesn’t just accelerate existing processes, it bends the curve of innovation. It’s already happening. Microsoft’s own supply chain leverages these AI copilots.
READ ALSO
AMRs: Intelligence on the Move
If generative AI is the new brain of the supply chain, then Autonomous Mobile Robots (AMRs) are its arms and legs—powerful, adaptive, and increasingly independent. Josip Ćesić, co-founder and CEO of robotics company Gideon, laid out his vision for the future of AMRs in logistics.
“When we think about the future of a logistics hub, we really think about specific use cases,” Ćesić explained. “Loading, unloading, replenishment, order fulfillment—these are the operations where AMRs can exponentially increase human capacity.”
For Ćesić, the future of mobile robotics isn’t just about automation—it’s about perception. Gideon’s robots rely on 3D visual autonomy, using stereo cameras to emulate human vision and understand depth, structure, and semantics of their environments.
“We believe the future of autonomous mobile robotics is about AI and 3D visual perception,” he said. “A robot must understand not just that there’s a pallet, but which pallet, what type, and its exact 3D pose.”
That level of detail is critical for high-precision tasks like unloading trailers—spaces where floor levels are uneven, visibility is limited, and no two shipments are the same.
“The unloading side rarely knows what happened on the loading side,” Ćesić noted. “So the robot must quickly assess each pallet, understand how deep to drive under it, and adapt for stability.”
Gideon’s robots are able to build and update dense 3D maps of facilities in real-time, learning new environments within hours—not weeks.
“We need robots that are able to learn new objects in minutes and hours, or we would never be able to deliver commercial projects effectively,” he emphasized.
Indeed, a major challenge in scaling AMRs has long been deployment speed. Traditional systems could take weeks—or months—to roll out. Gideon compresses that timeline to hours.
“Deploying a robot to unload trucks doesn’t have to be complicated,” said Ćesić. “Drive the robot around once to map the warehouse, mark your dock doors and staging areas, and set up missions. Anyone who can use a smartphone can configure a loading pattern. It literally takes an hour.”
This low-friction setup is crucial in an industry plagued by labor shortages and high turnover. Automation needs to be plug-and-play, not a PhD project.
READ ALSO
From Wheels to Legs: Boston Dynamics and the AI-Powered Robots Reshaping Warehousing
Over the past decade, AMRs have revolutionized logistics, but a new wave of intelligent robots is pushing automation even further—led by Boston Dynamics. Known for its agile robot dog Spot, the company now focuses on giving robots not just legs, but brains.
For Nicolas de Keijser, Director of Sales at Boston Dynamics,
“Warehouses are filled with conveyors, forklifts, AMRs, and now increasingly, robots. These systems need to work together,” says de Keijser. To orchestrate this collaboration, Boston Dynamics created Orbit, its robot fleet management and AI analytics platform.
The trailer-unloading robot Stretch, for instance, has already been deployed with major players like DHL and Maersk. It is able to autonomously unload trailers, regardless of the shape, size, or condition of the freight.
“It’s not just about grabbing boxes,” de Keijser says. “It’s about placing them correctly based on where the label is, adapting to slight damages, and handling real-world variety—not just uniform brown boxes.”
Spot, for instance, can autonomously inspect facilities, identify leaks or anomalies, and even execute voice-commanded tasks, all while feeding insights back to Orbit AI. This shifts inspections from periodic to continuous, proactive monitoring.
“You can give Spot a natural language task—like, ‘Find any water puddles near the loading dock’—and it’ll do it. It’s scene understanding at the edge,” de Keijser explains.
READ ALSO
And Spot is just the beginning. Perhaps the most ambitious element of Boston Dynamics’ roadmap is Atlas, its humanoid robot. Still in its early development phase, Atlas is poised to address the most challenging, variable tasks in logistics—those that cannot be solved by fixed automation or even traditional AMRs.
“Warehouses are built for humans,” says de Keijser. “So a robot that moves and thinks like a person fits naturally. We’re doing behavior control through AI. We’re teaching robots like Atlas to act more like people—to understand ladders, hoses on the floor, or objects with wheels. It’s about real-world reasoning.”
Thanks to reinforcement learning, powerful simulation environments, and data gathered from thousands of deployed robots, Atlas is learning at exponential speed.
“Being able to teach a humanoid robot a new task in just a few days—that’s a game changer,” he says.
The vision is to create robots that are not just tools, but adaptable partners. With AI-enhanced decision-making, real-time perception, and human-like dexterity, humanoids could soon take on tasks like mixed-case palletizing, unstructured item picking, and even on-the-fly problem solving during peak surges.
“We’re now building a foundation where robots can navigate a warehouse, identify the right box, plan how to stack it on a multi-layer pallet, and avoid risks—all without hardcoding every step,” says de Keijser. “That’s fundamentally different from the past.”
With humanoids entering the scene, AMRs growing more capable, and AI becoming increasingly predictive, the warehouse of the future looks less like a machine shop—and more like an ecosystem.
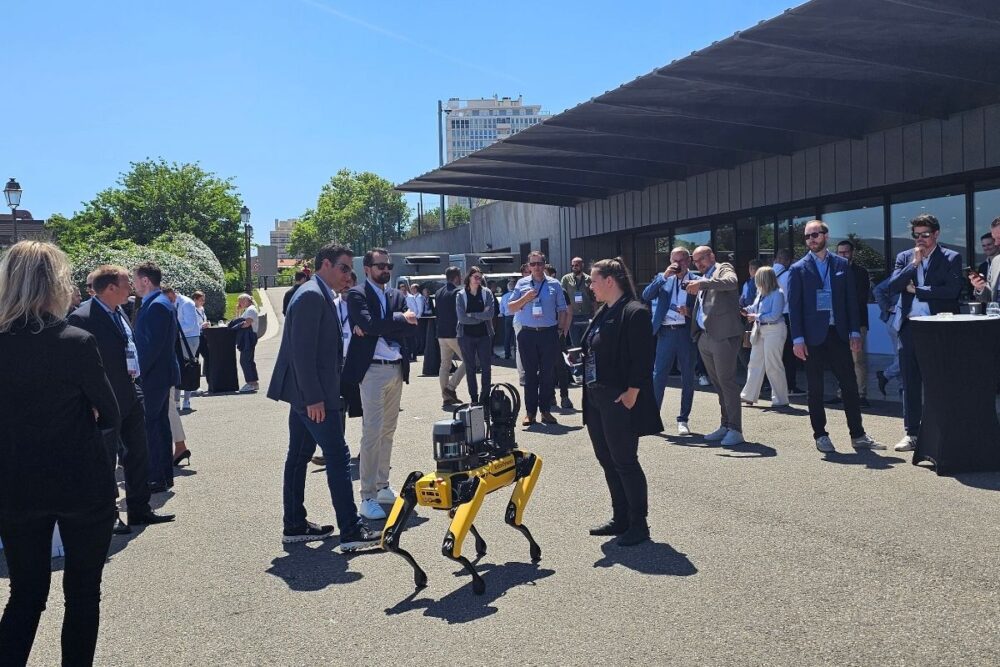
The Next Logistics Frontier: Physical AI
As Boston Dynamics pushes the boundaries of embodied intelligence—robots that move, perceive, and adapt—another critical layer is emerging: physical AI. This is where intelligence isn’t just deployed on robots, but born in the cloud, trained in simulation, and refined through real-world feedback. According to Tua Asplund, Product Sales Specialist for Omniverse at Nvidia, this represents the next evolution of robotics.
“Robots don’t just need to think—they need to act in unpredictable environments,” says Asplund. “And that starts in simulation, not on the warehouse floor.”
At the heart of this approach is Nvidia’s physical AI ecosystem, which combines three tightly integrated systems:
- AI Supercomputers, where foundational models—language, vision, and robotic agents—are trained.
- Omniverse + Cosmos, a simulation platform and physics-trained world model used to build high-fidelity digital twins of physical environments.
- Edge Deployment through Isaac (robot control) and Metropolis (vision AI), enabling robots to interpret and act in real time.
Together, these systems allow companies to train AI in synthetic environments that replicate the physics and chaos of the real world—without ever risking hardware. Using Cosmos, for instance, a virtual 100,000-square-foot warehouse can be reskinned with different lighting, weather, or layouts to generate vast amounts of training data.
“Instead of sending a robot into the wild to gather experience, we give it millions of simulated lives,” explains Asplund.
This simulation-first approach solves a major bottleneck: data scarcity. It also makes AI agents more robust by preparing them for rare, high-risk edge cases—before deployment. Robots can fail safely, learn faster, and adapt better.
The result is agentic AI—a distributed intelligence system where multiple specialized agents (vision, motion, decision-making) work together in real time. These agents can turn multimodal inputs—like language, video, or lidar—into action, planning, and collaboration.
“Imagine an AMR rerouting mid-task because Metropolis detected an obstacle and updated the map in real time. Or a human operator asking, “Why did the robot stop?” and receiving a visual, AI-powered answer. All of this is tested in the digital twin before it hits the real world.”
Once deployed, real-world data loops back into the system, continuously improving performance. It’s a closed, adaptive cycle—train in the cloud, act at the edge, learn everywhere.
As robots like Atlas and Spot become more capable in physical space, Nvidia’s physical AI ensures such robots also grow more intelligent—through digital worlds designed to teach, test, and optimize. Together, they’re building a future where machines don’t just pull their weight—they understand where to carry it, and why.