The global food and beverage industry faces ongoing challenges in maintaining strict hygiene standards and minimizing the risk of contamination. Pyure’s air and surface purification system, which uses natural hydroxyl radicals, provides a unique solution by continuously sanitizing both the air and surfaces within food processing environments. We spoke with Mahyar Khosravi, CEO of Pyure, to explore how the company’s technology is revolutionizing pathogen control in food and beverage facilities. We also discussed the scalability and versatility of the technology, which makes it applicable to a variety of industrial settings.
We first encountered Pyure’s technology at Automation Fair, where the company was an OEM partner of Rockwell Automation. During the event, we met with Steve McCafee, Vice President of Sales, to learn more about the device that replicates the sun’s natural effects to purify air and surfaces.
Now, we wanted to explore the topic further, particularly regarding air purification in industrial settings like the food industry. To gain deeper insights, we interviewed Pyure’s CEO, Mahyar Khosravi, who leads a small but rapidly growing team of 50 employees. Pyure has developed an innovative air and surface purification technology that is transforming how industries approach hygiene and pathogen control.
Pyure has developed an air and surface purification technology that uses natural hydroxyl radicals.
Mahyar Khosravi: “We replicate what the sun does outdoors in sanitizing the air and surfaces indoors. The technology we’ve developed has been implemented across multiple sectors. In general, we treat pathogens, bacteria, mold, and VOCs in a highly scalable and safe manner.”
What are the differences between your device and other purification systems?
Mahyar Khosravi: “One of the differentiators is the fundamental mechanism of action: we are an active air purification technology, meaning that we are not just treating the air that passes through our systems. Rather, we use the air that goes through our systems to carry, in this case, hydroxyl radicals out into the occupied space. These radicals continuously break down pathogens and other pollutants in the area.
This is different from other technologies, like filtration or UV lights, where the mechanism of action and purification only occurs as the air passes by the media—whether that media is a filter, catalyst, or light source. So, that is one of the fundamental differences between passive and active air purification.
However, beyond that, within the active air purification domain, finding systems that are scalable, cost-effective, safe, and capable of delivering efficacy at any scale is very challenging. You need the right mechanisms in place, such as feedback loops with sensors to monitor the rate of chemical production and account for environmental factors that influence the process.
Delivering efficacy at any scale—while ensuring safety—is particularly difficult in industrial and other unique environments, like healthcare, where there is a combination of very high pollutant loads (such as VOCs, airborne viruses, bacteria, or mold) alongside high airflow rates and other environmental factors.
Finding air purification technology that can scale to this level and adapt to environmental conditions is not an easy task.”
How did Pyure manage to develop a scalable, safe, and effective solution for such a wide range of environments?
Mahyar Khosravi: “The development of our technology took over 15 years of engineering work. The key to its success lies in our patented hydroxyl radical generation process, which dynamically adjusts to environmental conditions. This allows us to produce the right concentration of radicals in real-time, ensuring effective air and surface purification. Our technology also uses sensors to monitor and adjust production, allowing us to scale safely and efficiently across different environments.”
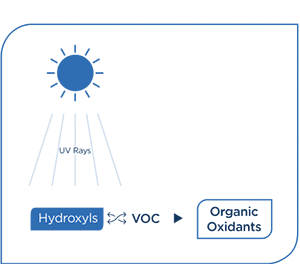
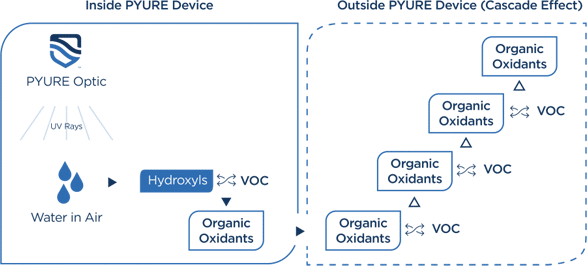
Your technology is used in the healthcare sector (read our story in our sister publication, MedicalExpo e-magazine). Can you tell us how your technology is applied in the food and beverage industry? What makes it unique compared to other solutions in this market?
Mahyar Khosravi: “It’s actually very similar to healthcare in many ways. In both sectors, you deal with a very high load of pathogens and pollutants. Whether it’s an operating room or a food processing facility, you have a lot of different equipment, tools, and surfaces that interact with high levels of pollutants and pathogens. In healthcare, it might be a patient in surgery or an ICU; in food processing, it’s equipment or surfaces that can harbor harmful bacteria.
However, in the food and beverage industry, the main concern is air quality, as air is the largest contact surface with food, equipment, and surfaces. Air interacts with the food, the equipment, and the environment itself. The challenge, however, is that no matter what treatments are in place—whether it’s filtration, HEPA systems, or other media—air that is recirculated into the room is only slightly cleaner after filtration. Once it’s back in space, contaminants like airborne viruses, dormant bacteria, or pollutants can quickly reintroduce risk.
Traditional solutions in the food and beverage industry, like point-in-time sanitization (e.g., hydrogen peroxide or other chemical treatments), come with significant drawbacks. These methods can be harmful to equipment, people, and the environment. They also require shutting down production lines, resulting in lost productivity.
What makes our technology unique is its ability to actively and continuously treat the air, surfaces, and equipment. It’s safe for people, highly effective, and doesn’t require downtime. This allows us to minimize risks such as salmonella, E. coli, or other dangerous pathogens.
This means our technology helps maintain a clean environment 24/7 and offers a much higher level of efficacy compared to wiping down surfaces, which only has a short-term effect. By neutralizing pathogens in real-time, we address critical issues like biofilm formation and contamination, ultimately delivering significant value to the food and beverage industry. This minimizes downtime and ensures consistent production without the need to shut down for cleaning or sanitization.”
In addition to pathogen neutralization, how does your technology impact other aspects of food processing, like spoilage or mold formation?
Mahyar Khosravi: “That’s a great point. One of the key advantages of our technology is that it can help reduce food spoilage by controlling the environment in which food is stored and processed. For example, we can install portable units in walk-in coolers to prevent mold formation or control ethylene gas, which is responsible for the ripening and spoilage of fruits and vegetables. This not only extends the shelf life of produce but also minimizes waste, reduces the environmental impact of food spoilage and helps reduce recalls.”
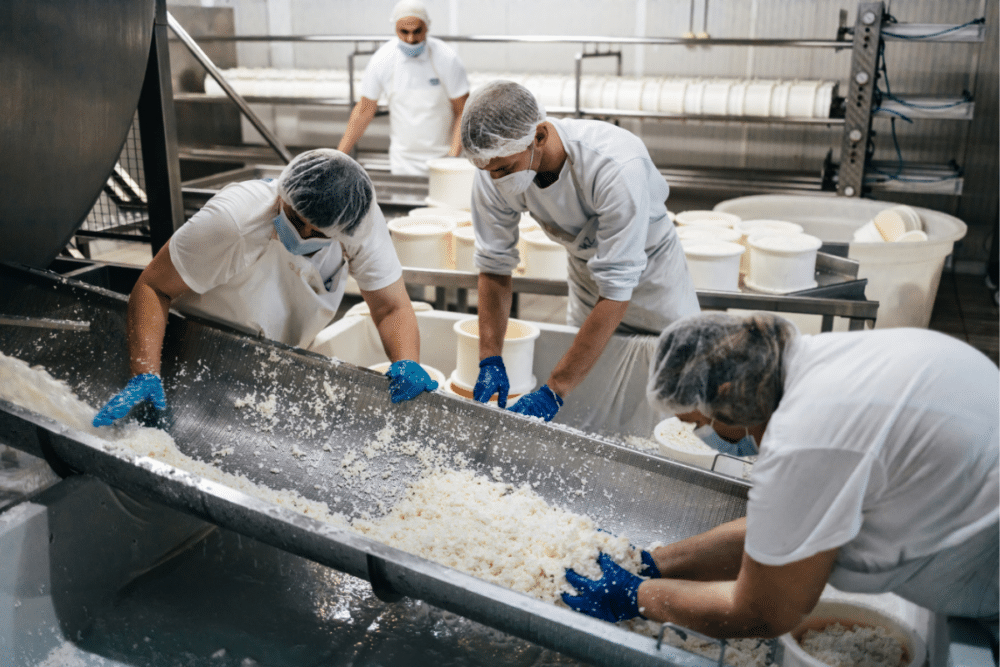
Can you explain how your technology works in a large-scale food production facility versus smaller food service operations?
Mahyar Khosravi: “In larger food production facilities, we would typically deploy some of our larger, integrated products that can tie into rooftop units or air handlers. These systems can treat 30,000, 40,000, or even 50,000 square feet or more, without the need for constant manual intervention.
For food service facilities, such as fast-food restaurants or food packaging environments, we often use smaller units that can be either integrated or portable. These environments have significant amounts of surfaces that come into contact with raw or cooked products, as well as staff handling high volumes of production, processing, or serving. In such cases, shutting down the entire workspace for sanitization is not practical.”
Are there any industries or environments where your technology is not suitable?
Mahyar Khosravi: “Not that we have really come across yet. For example, one of the areas where we are quite widely deployed is wastewater and water treatment facilities. In these environments, we treat harmful gases like hydrogen sulfide and ammonia, which are not only hazardous to human health but also highly damaging to equipment due to corrosion and, of course, create significant odor issues.
The only exception would be environments with extreme concentrations of harmful gases. When we neutralize hydrogen sulfide or ammonia, there is a concentration beyond which our solution may not be cost-effective. For instance, in the oil and gas sector, particularly in gas processing, there are areas with extremely high concentrations of hydrogen sulfide. In some cases, we can treat this effectively, but in areas where concentrations reach the high hundreds or low thousands of parts per million, it may not be cost-effective to treat those environments.
That said, high humidity is actually beneficial for our technology—the higher the humidity, the better it works because of the mechanism of action. Temperature is generally not an issue either, as long as it remains within the equipment’s operating limits on both the low and high ends. So, no significant challenges otherwise.”
Talking about treatment plants, do you also consider decontaminating water and adapting your technology for water treatment? For example, some companies use UV light to disinfect water.
Mahyar Khosravi: “The use of hydroxyl radicals in water treatment has been increasing over the past decade, and several companies are utilizing them for treating water. However, this is not an area we are currently focusing on. While it could be a possibility in the future, at the moment, our primary focus remains on air and surface treatment.”
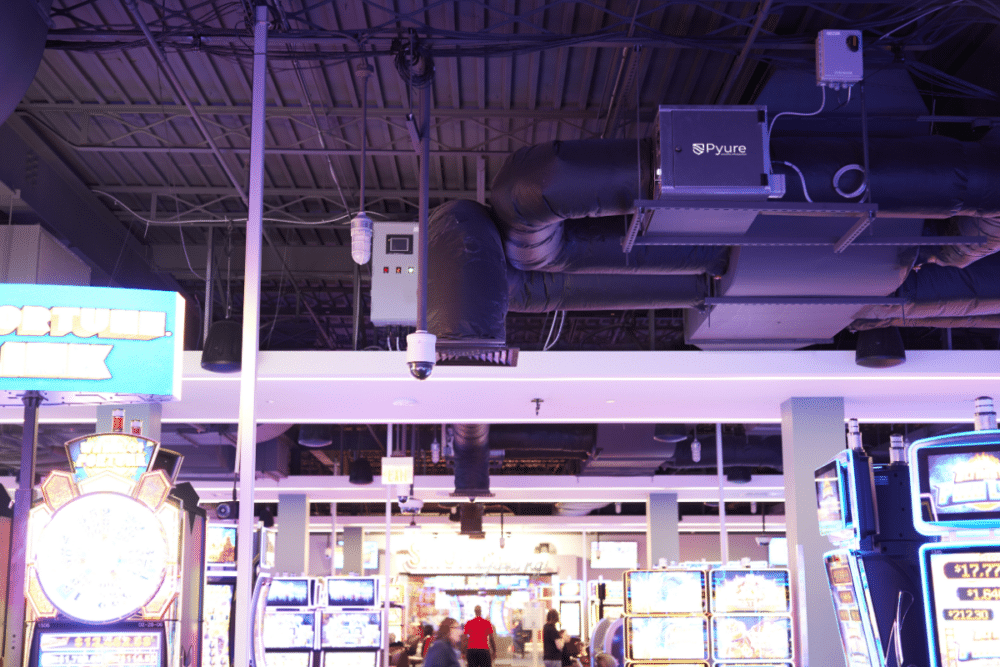
Can you tell us about your strategy for market expansion?
Mahyar Khosravi: “It’s really quite broad and widespread. We have an installed base all around the world, with higher concentrations in North America due to our headquarters being here. However, our installations span across the globe. In terms of industries, we have a very diverse presence. A significant portion of our work is in the remediation and restoration sector, with both permanent and temporary installations. We’ve also had considerable involvement in the food and beverage processing and services industries.
Our solutions have been used in agriculture, particularly in live animal facilities, to combat diseases like avian flu, swine flu, and others. We have numerous installations in smoking venues, such as casinos and smoking lounges, to address VOCs, smoke odor, and hazardous substances like nicotine. Additionally, we are active in the marine industry, where we combat both corrosion and odor issues aboard ships, including cruise ships.
In healthcare, we’ve already discussed our work, and we also have installations in wastewater and water treatment plants. We also have deployments in solid waste sorting facilities, particularly in high-density urban areas where we tackle issues like rodent infestations.
In the automotive sector, we’ve been involved as well, and we also support critical infrastructure, especially in environments with low population density but a highly specialized workforce. This is crucial for preventing the spread of illnesses like influenza or COVID-19, which could impact a large number of specialized personnel in critical infrastructure sectors.
Additionally, we’re constantly exploring new markets. Recently, we’ve looked into industries like tire manufacturing and pulp and paper, where air quality and the neutralization of harmful gases is essential.”
How do you see the future of your technology and company in the next 5 to 10 years?
Mahyar Khosravi: “Over the next five to ten years, we’re focused on expanding our global reach and continuing to innovate with our technology. One of the key areas we’re working on is the concept of Indoor Air Quality as a Service (IAQaaS). More and more customers are looking for outcomes, not just products. They want to understand how the environment is affecting their operations, such as optimizing production, minimizing sick days, and reducing waste. Our technology will play a big role in providing that intelligence through real-time data on air quality, pathogen levels, and environmental parameters. We’re also looking at ways to help companies reduce energy consumption and minimize their carbon footprint by optimizing air circulation and fresh air intake. This shift towards data-driven solutions will be a big part of our future, and we are already testing pilot projects in this space.”