Wastewater management is a cornerstone of modern urban infrastructure, balancing environmental responsibility with public health. As cities grow and populations increase, managing this critical resource becomes even more essential. This challenge is precisely what the Inland Empire Utilities Agency (IEUA) in Los Angeles is addressing. DirectIndustry had the opportunity to visit this unique treatment plant, which serves as a prime example of how wastewater treatment can be reimagined to meet future challenges.
We could say we’ve never been this close to the stars! Located at Regional Plant 5 (RP5) of the Inland Empire Utilities Agency (IEUA), in the greater Los Angeles area, this facility processes a significant portion of Southern California’s wastewater — perhaps even that of Hollywood and Beverly Hills!
A Growing Need for Advanced Solutions
The IEUA opened its doors to DirectIndustry for a full tour of RP5, one of its key facilities. This site is currently undergoing significant expansion to address pressing regional challenges: a growing population, more frequent droughts, and the need for more sustainable and environmentally friendly wastewater treatment processes. Automating the plant is a cornerstone of the agency’s long-term strategy.
The Inland Empire Utilities Agency: A Pioneer in Water Resource Management
Established in 1950 as a municipal water district, the IEUA initially aimed to tackle groundwater overdraft issues. By connecting to imported water systems, the organization played a pivotal role in securing the region’s water future.
Over the decades, IEUA has transformed into a regional wastewater treatment agency, serving seven customer agencies across a 242-square-mile service area. Today, it provides services to 935,000 residents, encompassing water supply and wastewater treatment.
The agency treats over 51 million gallons (193 million liters) of wastewater daily across five regional plants (RP1 to RP5). Additionally, it produces and sells 34,000 acre-feet (42 million cubic meters) of recycled water annually and generates 230,000 cubic yards (176,000 cubic meters) of compost each year.
The RP5 Expansion Project
RP5, the most critical facility within IEUA, was built in 2003 to manage liquid wastewater treatment, while other facilities handled solids processing. Today, the plant is evolving to meet growing regional demands, explains Principal Engineer Brian Wilson:
“The RP5 plant is currently capable of processing 16.3 million gallons (61 million liters) of wastewater per day (MGD) for approximately 200,000 residents. It was designed to handle the needs of the region at the time of its construction. However, population growth and the increasing use of water-saving technologies—such as high-efficiency faucets and appliances—meant that the plant needed to expand.”
The ongoing $330 million (€310 million) RP5 Expansion Project, launched in 2020 aims to increase the facility’s capacity to 22.5 MGD. It also adapts to changes in incoming wastewater composition, including higher concentrations of solids resulting from increased water conservation efforts.
“We are building both the liquid expansion of the plant as well as the solid expansion of the plant.”
Key elements of this project include enhancing existing treatment systems and constructing a biosolids facility to centralize processing, digestion, and composting of waste solids.
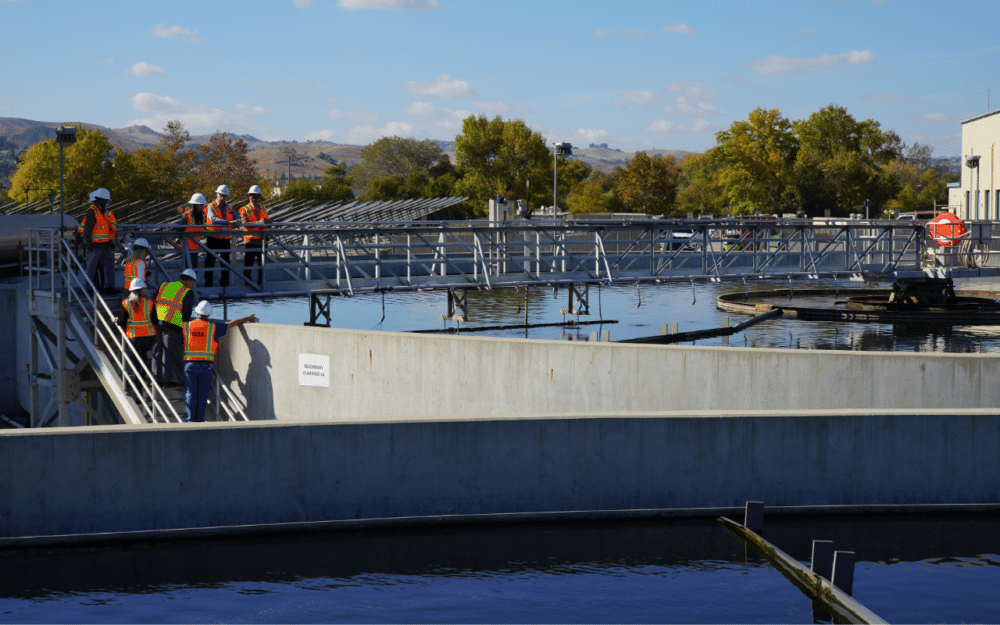
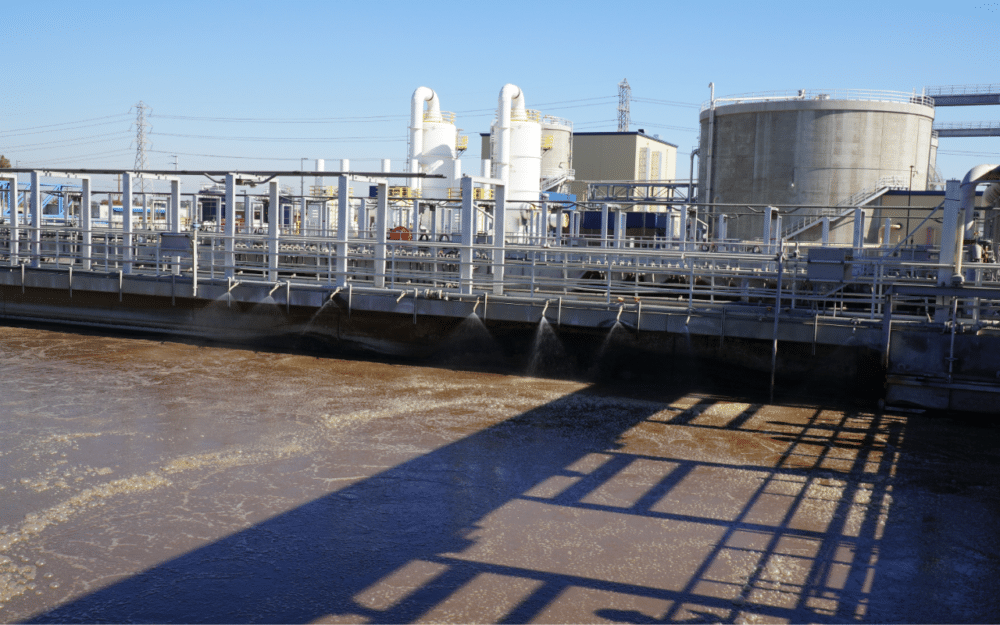
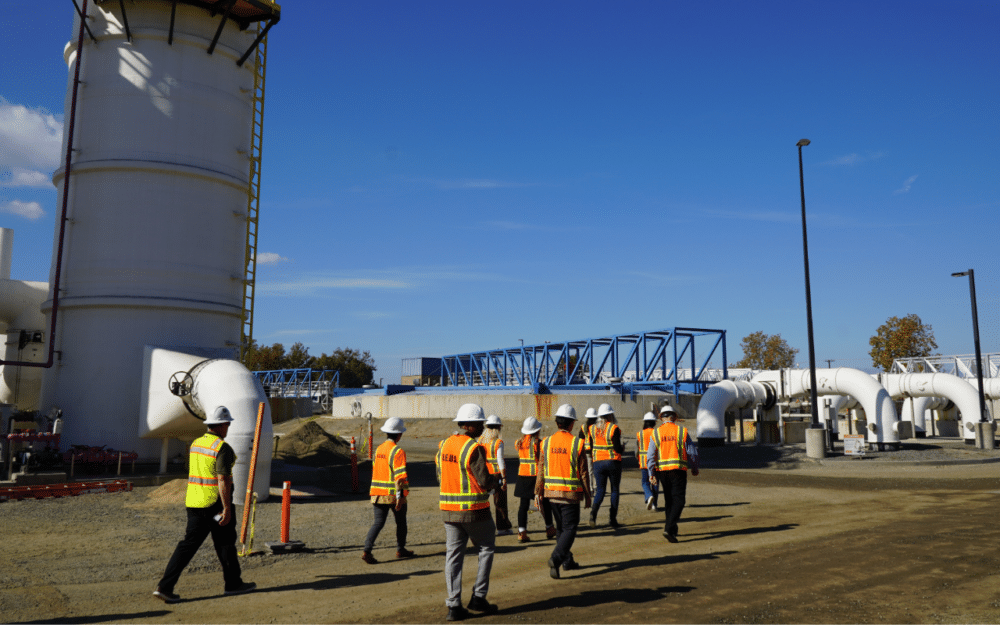
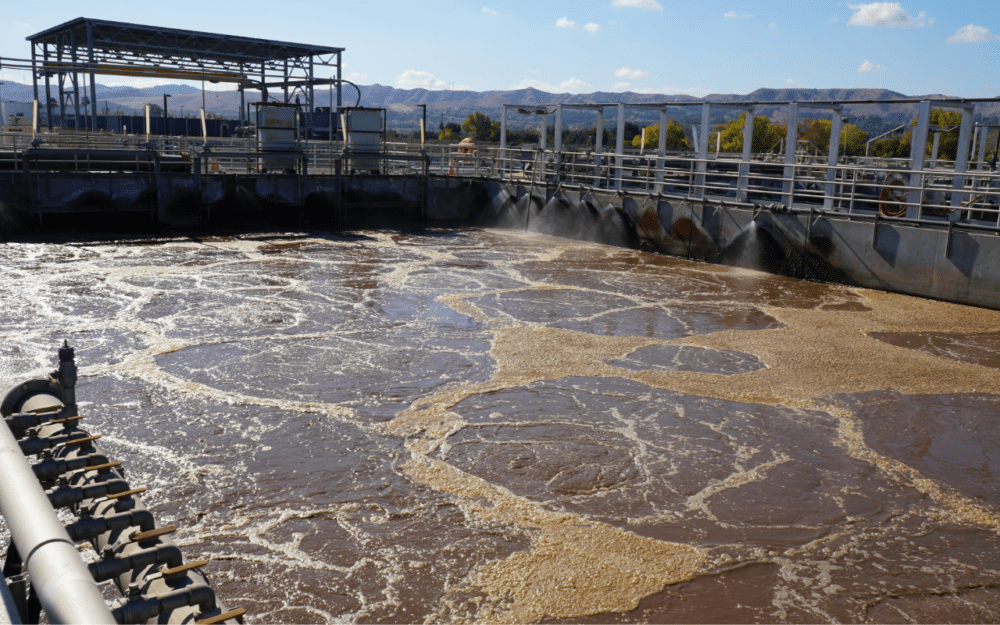
The Wastewater Treatment Process
To achieve its goals, the RP5 Expansion Project integrates a variety of advanced technologies designed to optimize both the efficiency and effectiveness of wastewater treatment. Before diving deeper into these innovations, it is important to understand the wastewater treatment process used at the site.
Primary Clarification, Biological Treatment, Disinfection
The process begins when wastewater flows into the plant through a gravity-fed system, ensuring the sewage is elevated to levels where treatment systems can manage it effectively. Once inside the plant, the wastewater undergoes initial screening to remove larger debris. As Brian explained,
“We remove and screen that sewage with bar screens. After the bar screens, we remove grit with a grit removal system.”
Bar screens trap large objects, while the grit removal system filters out heavier materials like sand or small rocks, which could damage equipment or clog pipelines.
After this preliminary cleaning, the wastewater passes through finer screens with two-millimeter openings, removing sharp items or other materials that could compromise downstream processes. This stage is critical for ensuring the efficiency of the next steps.
“Then we go through our primary clarifier where we gravity-settle the sludge out. The sludge that comes off of that process is sent over to the digestion process.”
At this point, the sludge (solid waste) is separated from the liquid, marking the first significant division in the treatment process.
The liquid from the primary clarifier, which engineers refer to as “chocolate milk” due to its appearance, flows into aeration basins for biological treatment. Oxygen is introduced during aeration to encourage the growth of microorganisms that break down organic pollutants, while non-aerated basins facilitate further biological processing in oxygen-free environments.
At the secondary treatment stage, advanced technologies are being introduced as part of the plant’s expansion. To meet modern efficiency and capacity requirements, IEUA is indeed replacing traditional secondary clarifiers with new membrane bioreactors (MBRs). These systems use dense networks of microscopic strands to filter water, producing significantly higher-quality effluent. This technology ensures compliance with future regulatory requirements and enhances overall treatment efficiency.
“That will allow us to treat a higher concentration of solids in our wastewater flow. And we can treat more wastewater in the same footprint.”
Following MBR treatment, the purified water moves to the disinfection system, where it passes through a chlorine contact basin. After dechlorination, the treated water is either discharged into a nearby stream or repurposed for irrigation and industrial use through the reclaimed water system, identified by purple pipes.
RELATED ARTICLE
Solid Waste Processing
While the liquid undergoes purification, solid waste (sludge) is processed in parallel. The process begins in a thickening building under construction, where solids are concentrated from less than 1% to about 6%. The thickened sludge then enters a two-phase digestion process designed to destroy pathogens and reduce volume.
“There is first the acid phase digester where the sludge sits at 140°F (60°C) and it’s mixed for about a day. Then the sludge is transferred over to our gas phase digesters where it’s at about 100 degrees for about 12 to 15 days. That destroys the solids content to approximately 2% and releases the water in it.”
This controlled decomposition produces methane gas, which is captured and used for energy.
Finally, the treated sludge is dewatered to further reduce its volume.
“That sludge then goes from about 6% solids down to about 2% solids. That 2% solid sludge is then transferred over to our dewatering building where we dewater the solids and concentrate it up to about 20% solids or more.”
The concentrated sludge is then sent to a composting facility, where it is transformed into a nutrient-rich product suitable for agricultural use.
Innovation and Automation
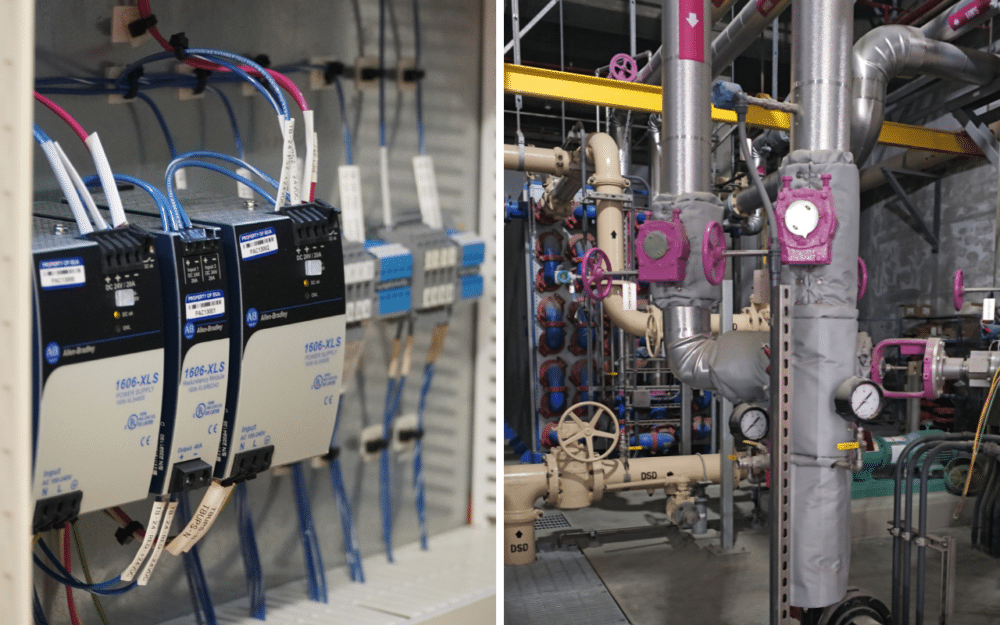
As we have seen, to adapt to the growing population, one of the innovations being implemented is the use of membrane bioreactors (MBRs). MBRs offer numerous advantages. First, the water treated by MBRs is of exceptionally high quality due to the integration of biological treatment with advanced membrane filtration. Additionally, MBRs have a compact design. They require less space than traditional systems, which is particularly beneficial in high-density urban areas. Moreover, the membranes’ long lifespan ensures durability and cost-effectiveness over time.
RP5 is also transitioning to advanced biofilter systems to better manage air quality around the facility. These systems effectively minimize odors, ensuring that the local community is not negatively impacted by the plant’s operations. During our site visit, we can confirm that we were not disturbed by unpleasant ambient odors, even near the aeration basin where the so-called “chocolate milk” flows.
However, one of the critical pillars of this wastewater management system is automation. Automation systems, powered by Rockwell Automation technology, play a vital role in ensuring that RP5 operates efficiently with minimal operator intervention.
As Brian Wilson explains,
“Our system is highly automated, with operations staff on-site only 10 hours a day. For the remaining 14 hours, the plant operates unmanned but is fully automated, monitored, and controlled remotely. The automation ensures continuous treatment, allowing operators to troubleshoot remotely if needed, even in the middle of the night.”
The plant’s smart monitoring systems are designed to detect issues early, ensuring uninterrupted treatment. The next phase of RP5’s automation strategy involves integrating sensors on critical equipment. These sensors will predict maintenance needs and optimize the plant’s resource consumption, aligning its operations with emerging trends in artificial intelligence and predictive maintenance.