Last week, DirectIndustry visited emPrinte, SPIE Batignolles’ 3D concrete printing workshop near Lyon, France. Launched in December, emPrinte is printing concrete pieces for the construction sector using Lafarge concrete and an ABB robot equipped with an Xtree printing head. The aim is to reduce CO2 emissions by 30 to 50% compared to traditional construction methods. Here’s our report.
SPIE’s President, Jean-Charles Robin, along with its partners, including Lafarge’s Managing Director for France Xavier Guesnu and Xtree’s CEO Dominic Corvez, was in Lyon last week to officially inaugurate SPIE Batignolles’ new 3D printing workshop, emPrinte. This is the group’s second 3D printing facility, following the first one in Ollainville, near Paris, which opened in 2021.
Since the beginning of 2024, SPIE Batignolles has been printing on this site construction components (like formworks and reservation boxes), urban furniture (such as trash cans and benches), and custom-made products—all from concrete supplied by Lafarge.
DirectIndustry visited the 3D printing workshop to learn more about the production techniques employed, and to understand the prospects for this site and the broader construction industry.
Mathilde the Robot
The workshop spans 340 square meters, and at its center stands Mathilde. Mathilde is an ABB Foundry 2 Plus 7-axis robot, standing two meters tall and equipped with a 70-kilogram Xtree printing head. SPIE Batignolles acquired it earlier this year and installed it on a 7.7-meter sliding track with a reach of 3.5 meters to minimize vibrations. Mathilde can 3D print concrete structures as well as geopolymer and clay elements.
These structures can range from construction elements like formwork (such as reservation boxes or shower bases) to urban furniture for local communities, like benches or planters. Complex elements such as columns are also possible. For example, the Fort d’Aubervilliers Aquatic Center, which will serve as an Olympic training pool, has 29 concrete columns of varying heights supporting its steel framework, with concrete formwork-type coverings.
When we arrived at the workshop, Mathilde was printing a prototype C60 facade panel. To the left, there were four freshly printed concrete bases for a regional construction project. To the right, a two-meter column, printed two weeks earlier with a low-carbon C60 concrete, was drying.
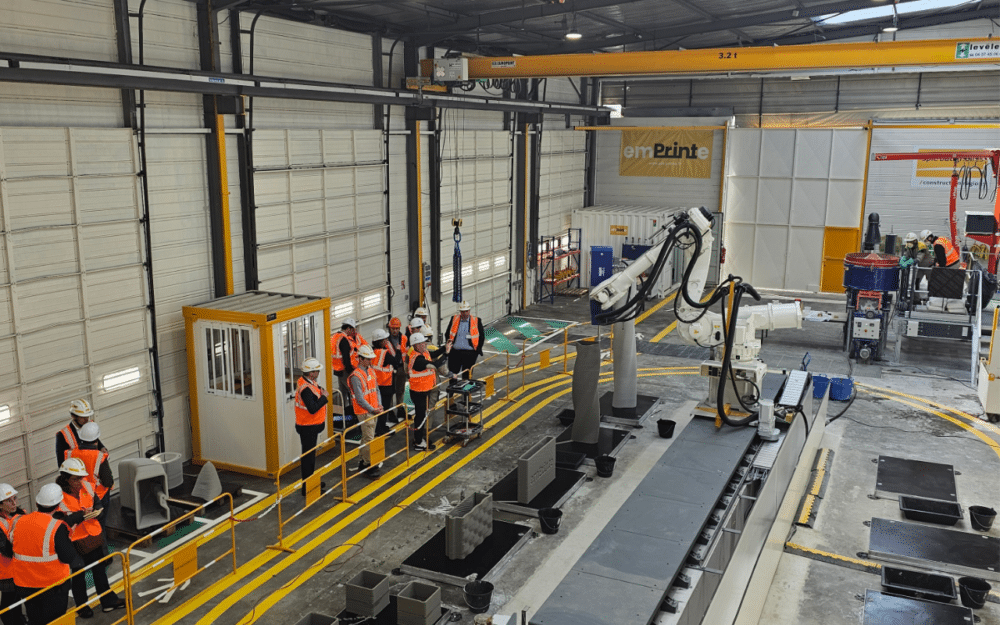

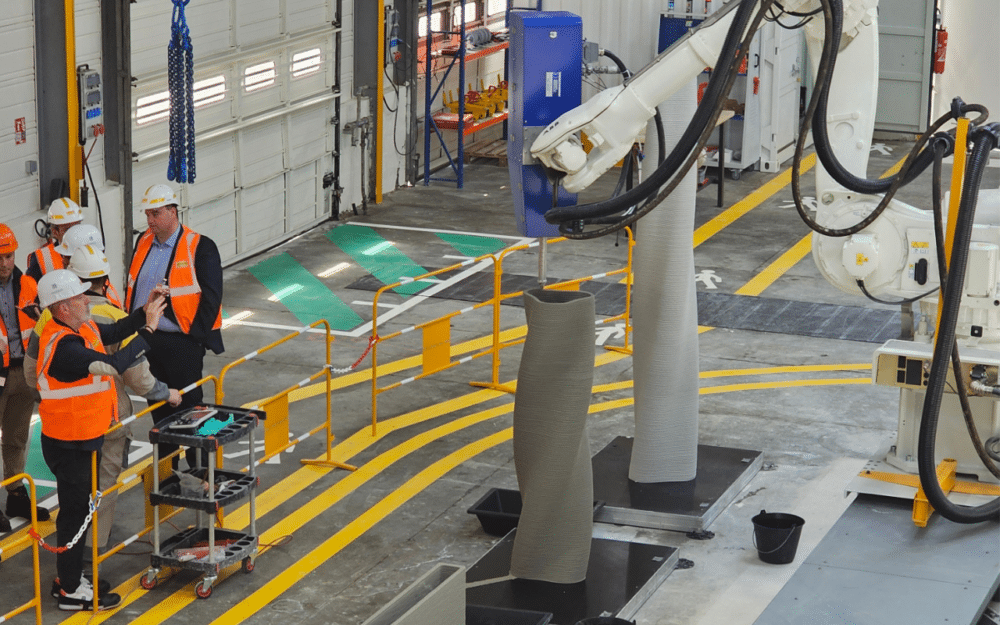
The Production Line
The production process starts with mortar, a special formula patented by Lafarge. It arrives in 25-kilogram bags or one-ton bulk bags. A vacuum system lifts the bags, allowing operators to avoid heavy lifting.
Pierre Couque, Operations Manager at SPIE Batignolles emPrinte, walked us through the process:
“The mortar is first mixed with water in the mixer, then it flows through a chute into a feeding pump. This pump transports the mortar through hoses to the print head. Inside the print head, dosage pumps, along with setting accelerators, control the flow and speed of printing while maintaining the right material consistency. These adjustments depend on the quantity of material available and the type of pieces being produced.”
To build a fast-rising column, more setting accelerators are required compared to slower-rising elements with longer production times.
“To simplify the operators’ work, we adjust batch sizes according to the target flow rates. If we’re aiming for flows of 3, 5, or 10 liters per minute, we prepare increasingly large batches to meet these faster rates. By enlarging the batches, we make the most of the time during which the material is usable. This means that the higher the target flow, the larger the batch must be to ensure continuous and efficient production.”
The print head’s capacity varies depending on the flow rate, handling between 50 and 400 kilograms of material, with various nozzles for 15 or 40-millimeter cords of concrete.
The robot follows a print path designed by the engineering team and lays down the concrete on floor-mounted support. As layers build up, the final piece takes shape. Mathilde can print structures up to three meters tall.
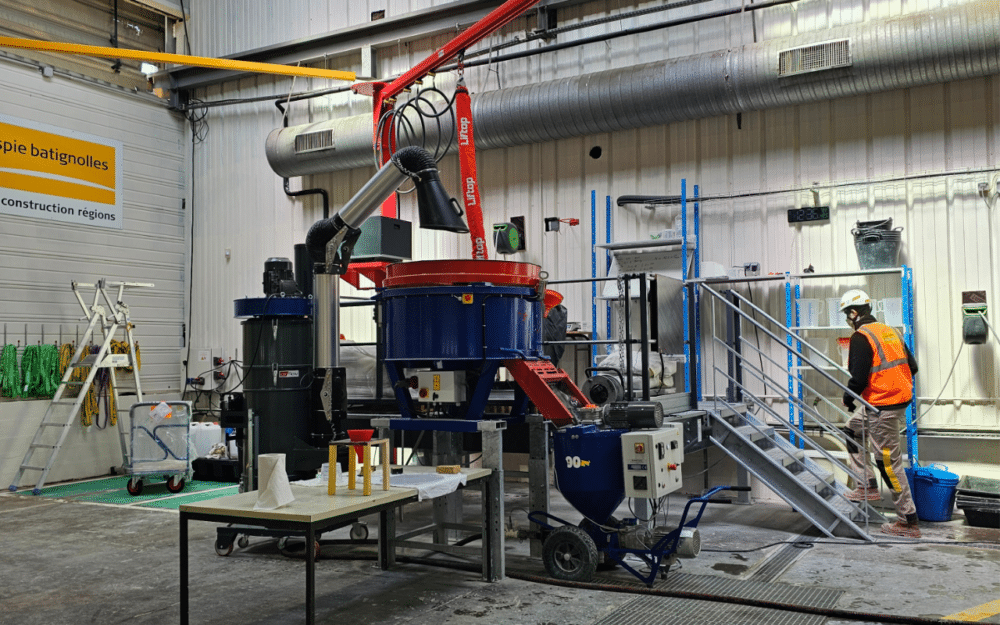
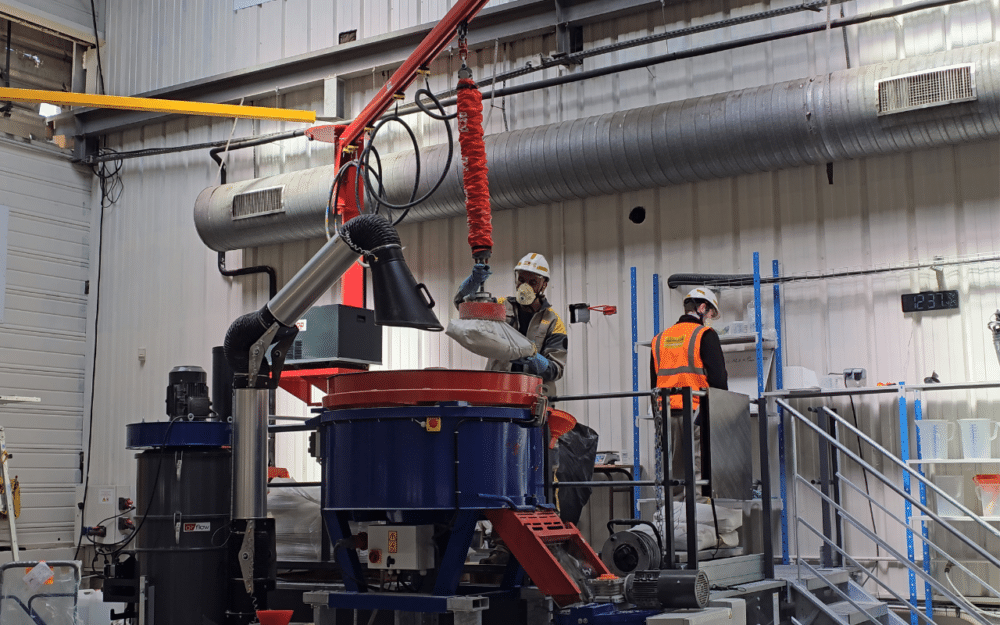
Cage-Free Robot
Regarding safety, Mathilde is not a collaborative robot (cobot) and does not work inside a cage. However, operators can still work nearby, occasionally needing to approach the print head to change nozzles or retrieve parts.
In industrial settings, multiple safety levels are typical, with robots equipped with sensors to detect people and automatically stop. However, this production line does not feature such measures. Despite this, Pierre assures us that safety is still a priority.
“Working with wet material requires manual interventions, whereas, in other industries, tool changes are automated. Currently, in manual mode, the maximum speed limit is 250 millimeters per second. In automatic mode, it can go up to 500 millimeters per second. This gives operators time to react if the robot moves unexpectedly, even though thorough checks are performed beforehand.”
Pierre explains that if an operator is two meters away from the robot, he has about four seconds to react in the event of a sudden acceleration.
Multiple Projects
Depending on the size of the objects, Mathilde can complete multiple projects with the same concrete mix. The print head can operate continuously for six hours, with a maximum flow rate of 8 to 10 liters per minute.
However, when the robot finishes a project, it pauses before repositioning for the next one. During this time, the concrete continues to flow, which can lead to waste. SPIE is working on a solution to enable automatic transitions between projects, reducing downtime and minimizing material waste. Once the concrete hits the floor, it hardens quickly and cannot be reused.
“In the long term, we aim to have a print support system covering the entire area, enabling seamless transitions between projects. However, this raises safety concerns. As long as the robot isn’t caged, either physically or with virtual barriers, we can’t move forward with full automation.”
It takes about one hour to print a column or a wall, and around 30 minutes for a planter at a flow rate of 5 liters per minute. Mathilde’s daily print capacity is 2 tons. Currently, the robot operates only during the day, requiring three to four people to run the production unit.
Once printed, the pieces must dry for one week before they can be sent for post-production, delivered to construction sites, or shipped to clients.
At the end of each day, the entire production line is disassembled, cleaned, and reassembled for the next day. This process includes cleaning the hoses, mixers, and all internal components of the print head. It takes two people about 30 minutes to complete this task.
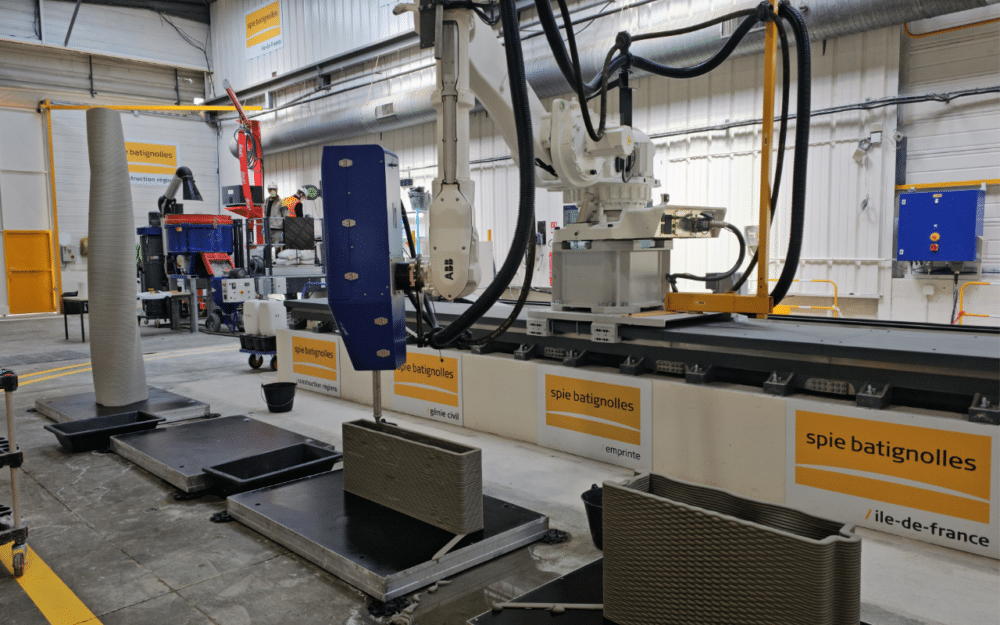
Tector Inks and Decarbonization
The print head is the core component of Mathilde. However, it can only function if the inks, or concrete, are available. Although the print head can work with other materials like earth or plaster, the focus here is on printing with mortars and concrete.
To achieve this, SPIE and XTree collaborated with Lafarge to develop low-carbon inks that are also cost-effective. Lafarge created Tector, a range of white and gray C60 inks with strengths ranging from 20 to 90 MPa.
These inks contain aggregates, which help improve the carbon footprint, although they are still quite cement-heavy, explains Dominique Corvez, CEO of XTree:
“We work with mortar, which typically contains more cement than concrete. However, the Tector inks are designed to optimize material density and clinker utilization. In terms of carbon footprint, these mortars are nearly comparable to low-carbon concrete, yet they offer superior strength. Ultimately, this results in a product with much lower carbon content than other materials, as it uses less material. We can reduce material usage by two or even three times. The C-S-H levels remain consistent but are utilized much more efficiently because we place the material precisely where it’s needed.”
Indeed, there’s no need for high-strength concrete like Ductal when producing reservation boxes.
Xavier Guesni, the Director of Lafarge France, told us about ongoing efforts to create inks from recycled concrete. The company has already produced 2,200 tons of recycled concrete at its Altkirch cement plant in eastern France. We interviewed them about this topic last year.
“We are testing the use of recycled concrete in inks and mortars in general. It’s a promising application because it allows for the reuse of materials from construction demolition, such as metal wires and concrete fragments, in prefabrication. There are no significant technical or technological barriers. However, some regulatory constraints limit the use of more than 5% recycled materials in certain types of construction.”
SPIE’s decision to establish a presence in the Lyon region is partly to be closer to its construction sites, reducing its carbon footprint.
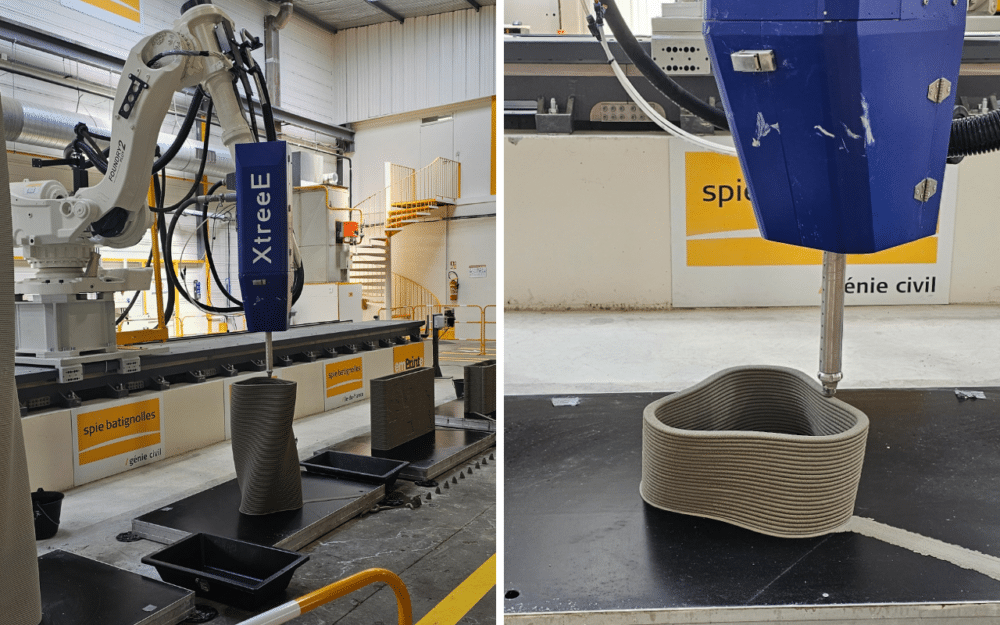
Improving Safety and Productivity
Mathilde isn’t the first 3D printing robot acquired by SPIE Batignolles. In 2021, the group acquired its first, named Ernest, after the founder of SPIE (Mathilde is named after his wife), and launched its first additive manufacturing workshop in Ollainville, near Paris. Over the past few years, SPIE has focused on 3D concrete printing for the construction industry, investing around one million euros in the Ollainville workshop and a similar amount in the Lyon site. Currently, a team of fourteen is distributed across the two locations, with a third workshop planned for 2025 in southwestern France. The projected revenue for this segment in 2024 is 800,000 euros.
emPrinte is the result of a collaboration with XTree, which designed the print head, and Lafarge, which developed the C60 concrete formula. The goal for SPIE is to provide a solution for the prefabrication of construction elements (beam joints, reservation boxes), precast walls, and urban furniture that are often time-consuming and resource-intensive when made manually.
For example, creating a slope for water drainage in showers for houses, apartments, or hotels typically involves digging an area and installing a wooden formwork. According to Alexis Hermet, Director of Quality and Technical Innovation at SPIE Batignolles,
“This traditional process requires an operator to cut wooden boards, nail them together to create the formwork, and then pour the concrete. Once the concrete hardens, the operator must use a crowbar to remove the wood, a process that can be time-consuming and generates waste, as the removed wood is often discarded. With 3D printing, the process is much simpler and cleaner. Prefabricated blocks are printed in the workshop, brought to the construction site, and installed with a crane. Once in place, concrete is poured directly into the block, which remains in place without needing removal. This eliminates the need for dismantling formwork, reducing both time and waste, resulting in a cleaner, more efficient construction site with fewer interventions.”
The idea to eliminate unnecessary or dangerous tasks came from the ground up, from masons and site managers. Permanent formwork means no need for removal, leading to productivity gains and fewer accidents.
A Promising Market
SPIE’s first clients are their own construction sites. Last year, around 50 SPIE projects used 3D-printed concrete elements. Dominique from XTree predicts that the demand for this type of solution will continue to grow in the future:
“Modern buildings contain more conduits and ventilation systems, like double-flow VMC, which require the installation of many reservation boxes of various sizes. This 3D printing solution allows for custom-made boxes that fit each conduit dimension. These boxes don’t need formwork, further simplifying the installation process.”
SPIE’s products are targeted at various clients, including project owners, municipalities, engineering firms, mayors, and developers. In terms of pricing, Cédric Reicher, the commercial director, mentions that 3D-printed products aren’t necessarily cheaper, but they offer added value:
“If we want to justify a slightly higher price due to our innovation, we need to be able to deliver quickly and cleanly. We’re never three months behind on delivery, for instance. This is also because of our local network, allowing us to deliver to sites near our production locations.”
RELATED ARTICLE
A New Mode of Construction
3D printing has been used in various industries for years, often to create optimized parts for aerospace and automotive applications. In construction, it is gaining traction, with 3D-printed houses becoming more common. NASA even uses 3D printing to create space habitats. The range of printable materials has expanded, from plastics to titanium, biomaterials, and multi-component compounds. Despite this, the concept is still struggling to fully integrate into industrial settings, largely because printing speeds don’t meet the high production rates required for mass manufacturing. Instead, 3D printing is used as a supplement to traditional machining for smaller production runs.
However, in construction, 3D printing holds significant potential, according to Jean Charles Robin, CEO of SPIE Batignolles. He describes it as a new mode of construction, signaling a major shift in the industry, which is undergoing an industrial revolution as a whole new sector emerges.
“We’re not here just to experiment. We’re here to transform construction methods and offer new, effective, and simple tools to those on the ground and those designing buildings. I believe that with digitalization, new construction methods, and decarbonization, the construction industry is probably experiencing its most significant revolution in 50 years,” he says.
Dominique from XTree sees this as the beginning of the industrial revolution for the building sector. He explains,
“While the productivity of the manufacturing sector has doubled over the last 30 years, construction productivity has only increased by 15 to 20%. This is why we’re at a critical juncture, where major changes must happen, especially to address the decarbonization challenges. These environmental concerns call for innovative solutions and radically different approaches.”
Lafarge also believes that 3D printing has the potential to address other challenges beyond decarbonization, such as the labor shortage in the construction industry. For Xavier from Lafarge,
“The key now is to foster the adoption of this technology on construction sites, among contractors and prefab manufacturers.”
Prefabricators are beginning to explore 3D printing to produce parts of prefabricated walls. In the United States, more and more house walls are being 3D-printed.
Will SPIE enter the market for 3D-printed buildings? Jean-Claude Robin states,
“It’s not our primary focus. We concentrate on specific objects and improving existing structures.”
The group aims to gradually integrate 3D printing into new construction methods, alongside the use of low-carbon materials. This incremental approach precedes any move towards full structural 3D printing.