To meet the surging demand for submarine cables, Alcatel Submarine Networks (ASN), a Nokia subsidiary, has implemented a robust 5G digital strategy. This strategy is anchored in the digital continuity of all operations, facilitated by cutting-edge PTC software solutions.
Content provided by PTC
In a steadfast commitment to Industry 4.0 principles, ASN has digitized its product literature and seamlessly orchestrated the coordination of PLM, ERP, and MOM systems, culminating in a harmonious digital continuum.
Alcatel Submarine Networks (ASN), leads the industry in terms of transmission capacity and installed base with more than 650,000 km of optical submarine systems deployed worldwide. The company designs, manufactures, installs, and maintains submarine cables and ancillary equipment with its fleet of ships to deliver fiber optics all over the world.
ASN has two factories, one located in Calais – the biggest – which manufactures cables, and the other in Greenwich which produces amplifiers and repeaters. In the face of a steep rise in market demand stemming from the increased need for reliable network transmission and Cloud and deep-water oil and gas exploration services, ASN wanted to improve its operational performance while still maintaining optimal quality.
Synchronizing Tools for Seamless Operations
The project is the result of a series of productive meetings between the management of the various departments; they pinpointed the fact that the main challenge lay in the management of paper documents. It was often time-consuming and caused issues in product traceability and training new members of the workforce. So with the strong growth in ASN product sales, it was becoming difficult for the sales department to centralize information and circulate it upstream or downstream to process several requests.
Drawing on these insights, the project team decided to create a digital thread through which information can flow easily from one system to another. It is based on three fully synchronized key elements designed to centralize data: PLM, MOM, and ERP.
The digital thread begins with design data from Creo CAD software. Windchill PLM solution centralizes and manages all product software. The ThingWorx industrial IoT platform that ASN uses for its MOM, is the integration platform between Windchill data and ERP manufacturing data.
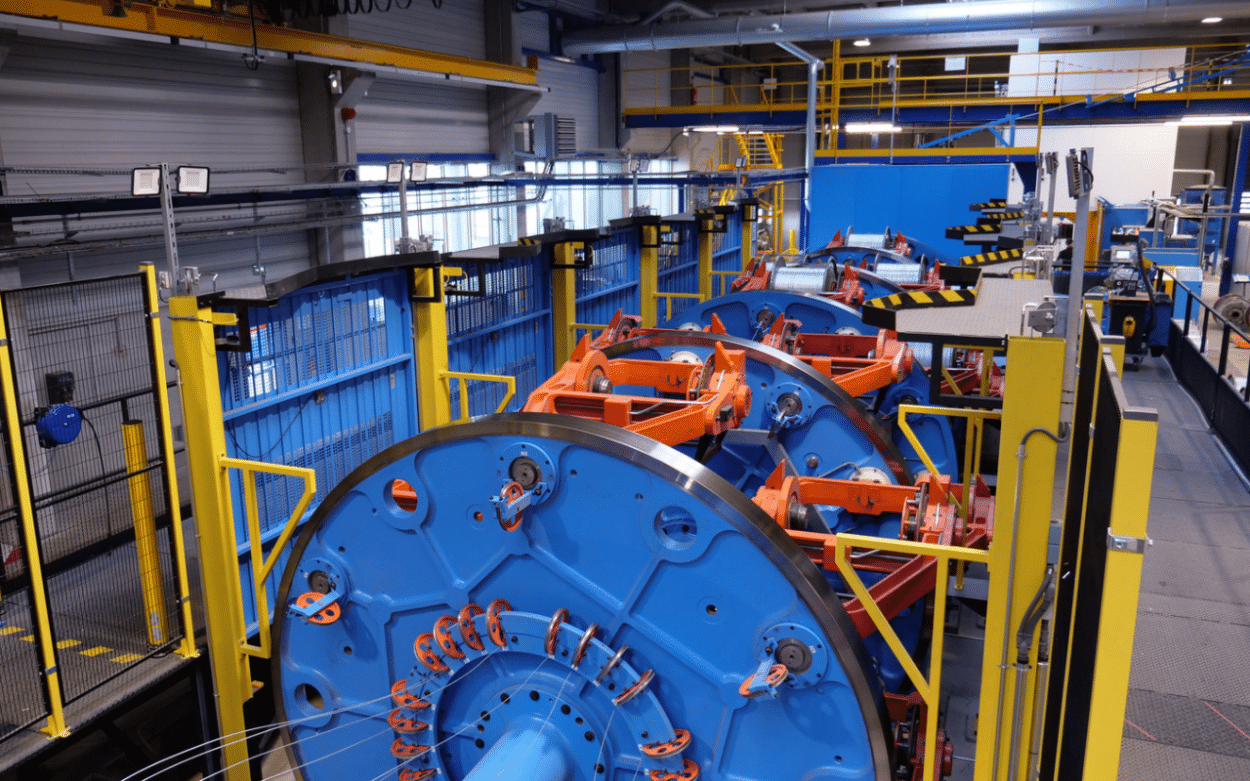
Initial Results Conclusive on a Pilot Product
For Omar Bougad, ASN’s engineering supply chain manager,
“We have embarked upon a far-reaching transformation to make gains in efficiency and respond to the changes of a rapidly expanding market. A bold industry 4.0 program based on 5G and digital continuity underpins our pursuit of innovation and good performance at the service of our customers.”
Project implementation started on one product in particular: PRM, a new system of permanent oil slick (reservoir) monitoring, the result of collaborative manufacturing between the Trondheim R&D site in Norway and the factories in Greenwich and Calais. The initial design phases were carried out by the teams in Trondheim. Design data was loaded into Windchill to be shared in real-time with the Greenwich plant, where the PRM system is assembled, and then Calais, where it is finalized.
Previously, production data, only available in hard copy form, did not leave the factory, but now the
full product information stream is available for the teams in the two plants at all times, within a single ecosystem, thanks to the synchronization of tools.
Specifically, this is data on product specifications, the manufacturing machines used, the date of manufacture, and any information necessary for traceability. ERP, on the other hand, provides information on the raw materials and sub-assemblies used and suppliers.
This continuous digital chain rolled out over the whole process has wide-ranging benefits. It can also use PLM and ERP data to generate manufacturing procedures and instructions.
At the moment, thanks to the commitment of all stakeholders, the project team, PTC and, above all, ASN staff who have been deeply involved from the very beginning of the project, the first stage is being rolled out on production sites.
Integration of the ecosystem as a whole will be fully functional on the PRM system by late 2023. The idea now is to roll out this digital thread over the whole range of ASN products and services.