The coronavirus crisis has revealed how fragile the global supply chain is and how crucial it has become to rethink parts sourcing and production strategies. In the United States, a significant number of businesses are now nearshoring or reshoring their manufacturing, such as VCC, an American electronic components manufacturer. Andy Zanelli, CEO at VCC, shared his insights into how the COVID-19 and tariffs on Chinese imports are leading American businesses to rebuild their supply chain.
Is COVID-19 acting as a wake-up call for the manufacturing industry? In any case, in a few months, the coronavirus pandemic has reshuffled the cards of globalization as never before. It has revealed the fragilities of our global production system and how dependent our economies have become on manufacturing chains scattered across the planet. In Europe and in the US, an increasing number of businesses are now thinking about shortening their supply chain and reestablishing connections for a more localized industrial base.
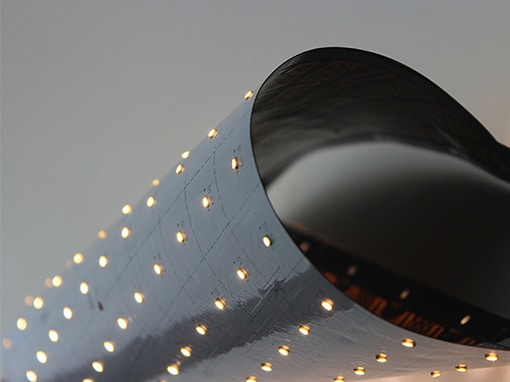
Andy Zanelli, CEO at California-based company VCC, shared his experience with us. VCC designs and manufactures electronic components for human and machine interfaces. Based in Southern California, they have a major manufacturing facility in Mexico. VCC was founded 45 years ago and now counts 220 employees. The company decided in early 2019 to build a new supply chain strategy. They are now looking to help US companies secure their supply chains in North America to ensure manufacturing self-sufficiency following the COVID-19 pandemic.
DirectIndustry magazine: You started nearshoring in early 2019, before the pandemic. What made you make the switch?
Andy Zanelli: We all know that when it comes to electronic components, the overwhelming capacities are in Asia. Yet, in early 2019, we started thinking about a global supply chain very differently. The big shock was the tariffs that were implemented by the US in 2018. We realized that the US still has robust manufacturing capacities, even if they transferred their manufacturing capacities to Asia, with highly cost-competitive manufactured products. And also, costs have been rising in Asia, in China specifically. So we realized that there are new variables in the total cost discussion. Having your supply closer to you reduces lead times and inventory carrying costs, making our business more responsive and valuable to our own customers. So we started making this shift and reshore to the US and Mexico.
DirectIndustry magazine: And when you fast forward to 2020 this seems like it was a good idea.
Andy Zanelli: Many US companies are now learning painful lessons about the vulnerabilities of their supply chain. COVID-19 hit the business world on an unprecedented scale and with unprecedented speed. Before COVID, cost, quality and delivery were the primary drivers of businesses making decisions about how they were going to run their supply chain. And what we all have learned is that natural disasters, geopolitical tensions and the capacity to respond faster need to be considered in your supply chain decisions now. It’s not just about material costs for shipping. There are other risk variables that need to be considered which include trade war risks and pandemic risks. Cost, quality and delivery still matter, but in addition to these factors businesses should also look at how resilient and responsive their supply chain is. Can they reconfigure their supply chain quickly? How close are their suppliers geographically? These are some of the questions they should now ask themselves.
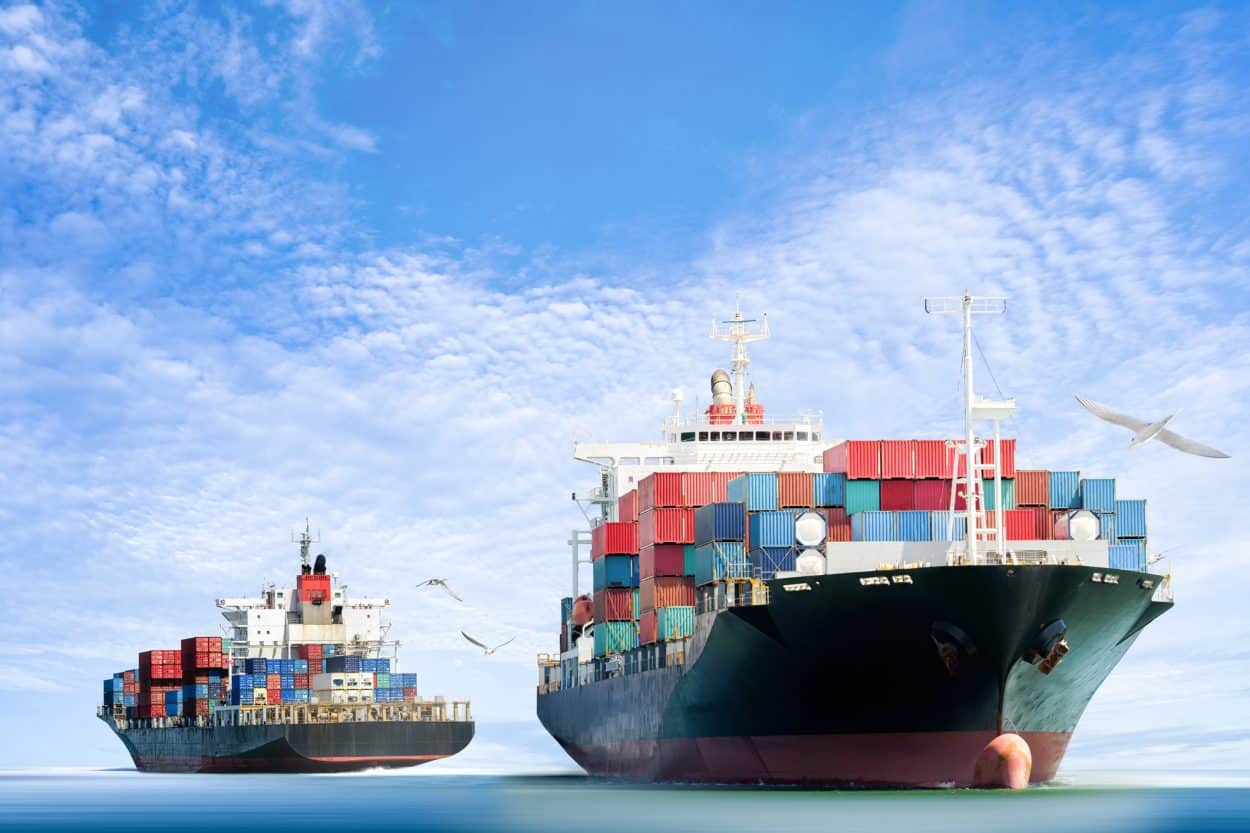
DirectIndustry magazine: Do you think this nearshore strategy is attractive?
Andy Zanelli: It is very attractive for many businesses in the electronics sector around the world. But we expect shifts in other industries such as the food industry for example. In the US there are discussions on potentially putting legislation in place on the grounds of national security. Questions are being raised about how in the US we outsource critical medical device and drug medication manufacturing overseas. This could be seen as a national security threat. So I expect we are going to see some shifts in the medium term. And there are robust manufacturing industries in the US and in Mexico that are ready to help customers that want to reshore manufacturing. We are already seeing a significant increase in nearshoring and reshoring as a result of the tumult we’ve all gone through in the last 24 months.
DirectIndustry magazine: Companies once offshored to Asia because it was cost-competitive, mainly because of cheap labor costs. Do you think businesses are now ready to operate a paradigm shift?
Andy Zanelli: When you talk about the competitive advantage in China, I would argue that in fact, the labor cost in China has increased a lot and is now at a level that Mexico is highly competitive with. Why would I want to manufacture halfway around the world and manage all the complexity of this supply chain and the potential costs (shipping costs, lean time, inventory) when I can reduce that significantly by manufacturing just south of the US in Mexico? That is a very frequent conversations we have with our customers and also with new potential customers. Total costs are close enough now. And when you factor in a pandemic and a trade war that brings tariffs on the table, businesses don’t want to manage the complexity. They are going to shift and nearshore their manufacturing. But plenty of others will want to build redundancy into their supply chain so that they still may have a majority of their components coming from Asia with meaningful capacity in North America. We see both of those scenarios today.
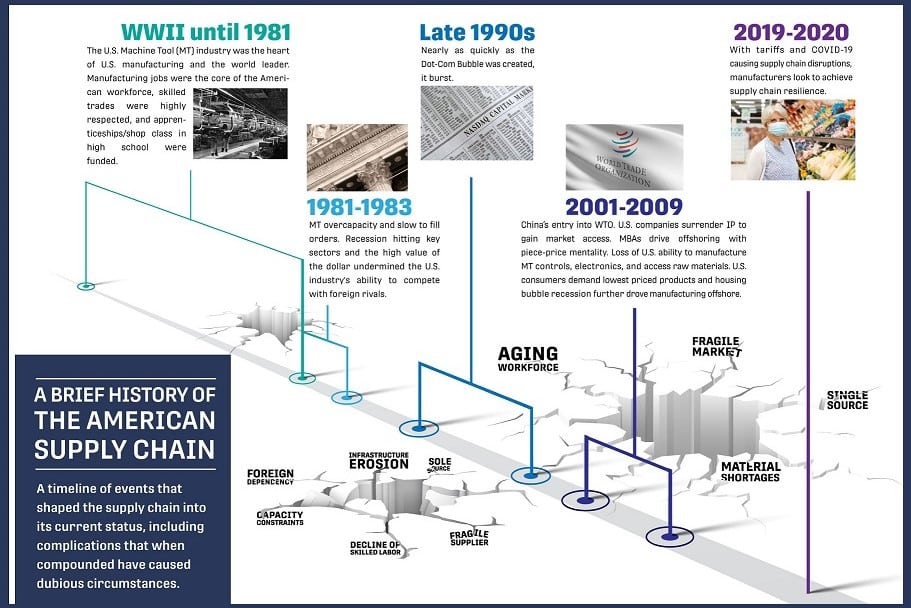
DirectIndustry magazine: What are some of the biggest challenges you see in the near future for establishing a new nearshore strategy?
Andy Zanelli: There are some types of industries where manufacturing capabilities don’t exist in the US anymore. For them it is going to be tough. There are also large companies like Apple which are working within China and Taiwan and I don’t think this is going to change. There is also a structural problem. When manufacturing left the US, the technical schools that were training people to work in manufacturing closed. That is one of the challenges that we will automatically have: as manufacturing jobs come back, there will be a lack of technical people to fill these jobs. I do think that in the short term that could be a challenge. Maybe not nationwide. In some areas like in the Midwest for example, and a part of the south there are still robust manufacturing sites. But in other parts of the country where manufacturing has some catching up to do I think there is going to be a lack of labor in order to ramp the manufacturing fast. And lastly, nearshoring is also happening in Europe. We all have to be prepared that costs are going to go up. As consumers, as governments and as industries we will have to deal with increased costs.