DirectIndustry attended JIMTOF last week, exploring the latest innovations in the machine tools industry. One of the companies we visited was Makino, which showcased a range of machines, including vertical and horizontal machining centers with three, four, and five axis, as well as an EDM (Electrical Discharge Machining) machine. Makino also introduced several automation solutions.
At Makino’s booth at Tokyo Big Sight, DirectIndustry spoke with Ryosuke Endo, the General Manager in charge of sales. This was a valuable opportunity to discuss their new releases and, more broadly, to delve into the future of the machining industry.
What types of machines are you presenting at JIMTOF this year?
Ryosuke Endo: “This year, we have three brand-new machines. One of them, the A500 IR, is a horizontal five-axis machine, designed as a general-purpose solution. It accommodates a variety of spindles for different applications, allowing it to machine titanium parts and aluminum structural components for the aerospace industry. We believe it’s ideal for mid-sized products.”
Is this machine already on the market, or is it a new release?
Ryosuke Endo: “It’s a recent release; we launched it in September, and it was first presented at the IMTS show. This is its debut in the Japanese market, but it’s now available worldwide after initial showcases in the U.S. and Europe.”
How do customer demands differ between the U.S. and Japan?
Ryosuke Endo: “The demands are increasingly similar. Across regions, companies face labor shortages and seek to reduce operator involvement through automation. A five-axis machine, for instance, allows greater machining versatility with less manual intervention, which is valuable given the global shortage of skilled labor. Both U.S. and Japanese clients are now looking for solutions that minimize operator input. This creates a strong demand for automation.”
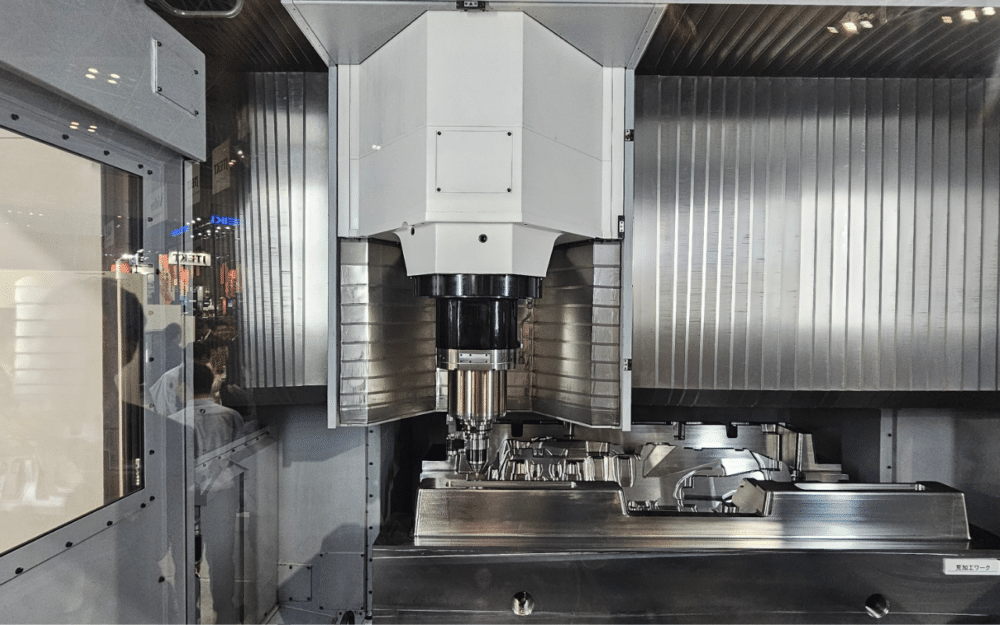
Japan also faces a demographic shift with an aging workforce. How does that impact automation?
Ryosuke Endo: “Precisely. With many skilled workers approaching retirement and fewer people entering the workforce, there’s a significant push for automation. We offer various automation solutions, like our pallet magazine systems, which allow the automated machining of multiple pallets on a single machine. We also have pallet rail systems with stackers, controlled by proprietary software that manages priorities and tasks. We also offer collaborative robots (cobots) for additional automation. The robotic arm we use is from Fanuc, while the rest of the system is designed by Makino.”
Are you considering developing AMRs (Autonomous Mobile Robots)? Many machine tool manufacturers are exploring this market.
Ryosuke Endo: “Yes, we’ve introduced a Makino AMR, currently available only in the Japanese market. With many AMR manufacturers already in the market, we’re initially focusing on Japan to gauge market response and identify the unique value we can offer.”
What has the market response been so far?
Ryosuke Endo: “There’s growing interest as people recognize the benefits. A few years ago, the perception was that AMRs were expensive and that labor was still more affordable. But now, with the labor shortage, the value and advantages of automation, including AMRs, are becoming clearer.”
Are you incorporating additive manufacturing into your machines?
Ryosuke Endo: “Not yet in Japan, but we have R&D efforts in Singapore exploring additive manufacturing. We see this as a valuable manufacturing solution for the future. Currently, we focus on subtractive processes like milling and EDM, but we recognize that additive manufacturing will become increasingly important, especially regarding material flexibility.”
How is Makino addressing environmental concerns, like energy and water consumption?
Ryosuke Endo: “Sustainability is a priority for us. We’ve incorporated sensors and limit switches that help reduce energy usage. For example, if certain machine functions aren’t in use, we can automatically idle those motors or hydraulic systems. Additionally, many of our facilities are equipped with solar panels, reducing our CO2 emissions in the manufacturing process.”
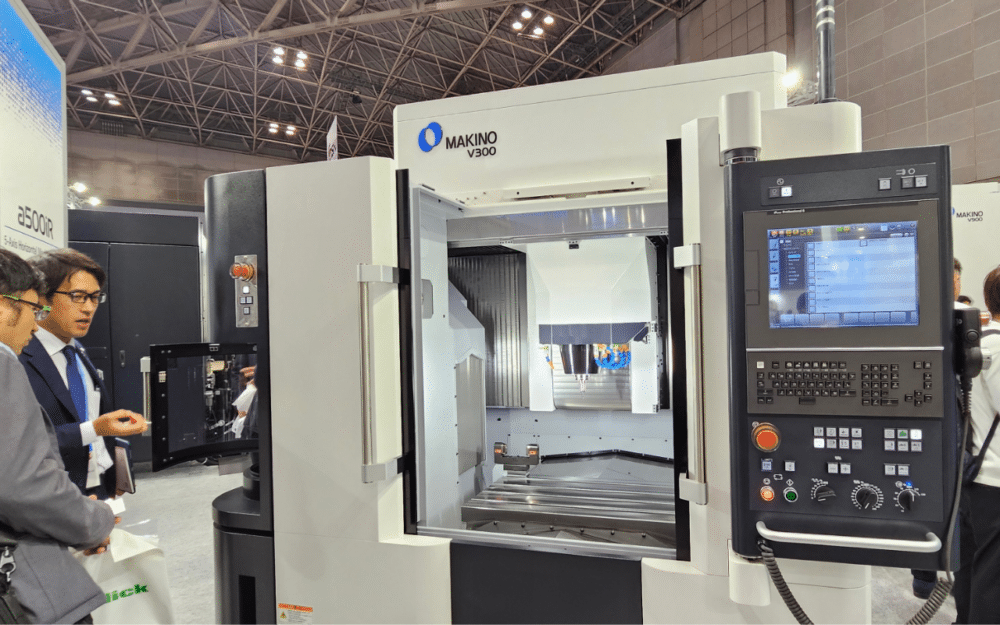
Are you integrating AI into your machines?
Ryosuke Endo: “Yes, we’re using AI primarily for maintenance and service support. For example, if a part malfunctions, our AI system can assist by retrieving maintenance information and helping operators troubleshoot. Many customers, however, prefer maintaining some level of manual control, so while AI assists in areas like maintenance, it doesn’t automate the entire machining process.”
Beyond addressing the labor shortage, what future innovations do you foresee for the machine tool sector?
Ryosuke Endo: “I think automation will continue to grow in importance. Not just in machine operations, but also in offline processes. For instance, tasks like part preparation and programming could be handled on PCs and simulated before production, making the production process faster and more efficient. This could lead to closer integration between remote programming and on-site manufacturing through Internet and software connections.”
Do you find it useful to design machine tools for specific sectors?
Ryosuke Endo: “Absolutely. One of Makino’s guiding principles is to listen closely to our customers and develop products that deliver real value to their specific industries. We don’t just make machines and suggest they be used anywhere—we tailor our machines and features to meet the unique needs of each sector. Whether it’s construction, aerospace, or other industries, we prioritize aligning each machine’s benefits with specific applications.”
Is aerospace particularly challenging due to material diversity?
Ryosuke Endo: “Each sector has its own unique challenges. Aerospace can indeed be complex, especially when clients need to machine difficult materials or highly intricate parts. Other challenges arise in mass production or machining complex geometries. Each of these requires a different approach, so understanding the specific needs of each sector is crucial to our process.”