How is wastewater treated in France? We visited a treatment plant near Lyon that processes the wastewater of 300,000 people daily. This plant has a unique feature. In addition to treating the wastewater and returning it to the Rhône River, it produces biomethane. Here’s our report.
The site is located between the north of Lyon and the Rhône River. Here, wastewater from several towns around Lyon, as well as rainwater, is treated. Built by Suez in 2010 and operational since 2011, Aqualyon treats and returns 91,000 m³ of wastewater—equivalent to that of 300,000 residents—to the Rhône.
Sixteen people work on site. The operators manage the arrival of effluents, screening, and lifting, sand and grease removal, primary sedimentation, biological treatment, clarification, returning water to the natural environment with quantitative and qualitative monitoring, sludge thickening, digestion, dewatering, drying, and gas management from the digester.
The plant produces 4,620 Nm³ of biogas per day from the sludge. Since 2018, the plant has been operating a biomethane injection module from this digested biogas.
We followed Thierry Lebrun, the manager of the Suez-operated plant, through the main stages of the process.
Treatment of Wastewater and Rainwater
Treating wastewater is crucial for protecting public health and the environment. Wastewater often contains contaminants, bacteria, chemicals, and waste that can pollute rivers, lakes, and oceans if not properly treated.
The role of a wastewater treatment plant is to purify this wastewater before it is released back into nature. This purification process involves several stages: filtration to remove large debris, biological degradation to eliminate organic matter, and disinfection to kill harmful microorganisms.
Step 1: Screening
Effluents arrive at the plant through the East Plain outfall and undergo screening to remove the largest debris, explains Thierry Lebrun, the site manager:
“Wastewater is loaded with pollutants such as phosphorus and nitrogen, as well as solid materials and micro-debris like plastics. If these wastes pass through the system, they can damage equipment, clog pipes, and hinder the water treatment process.”
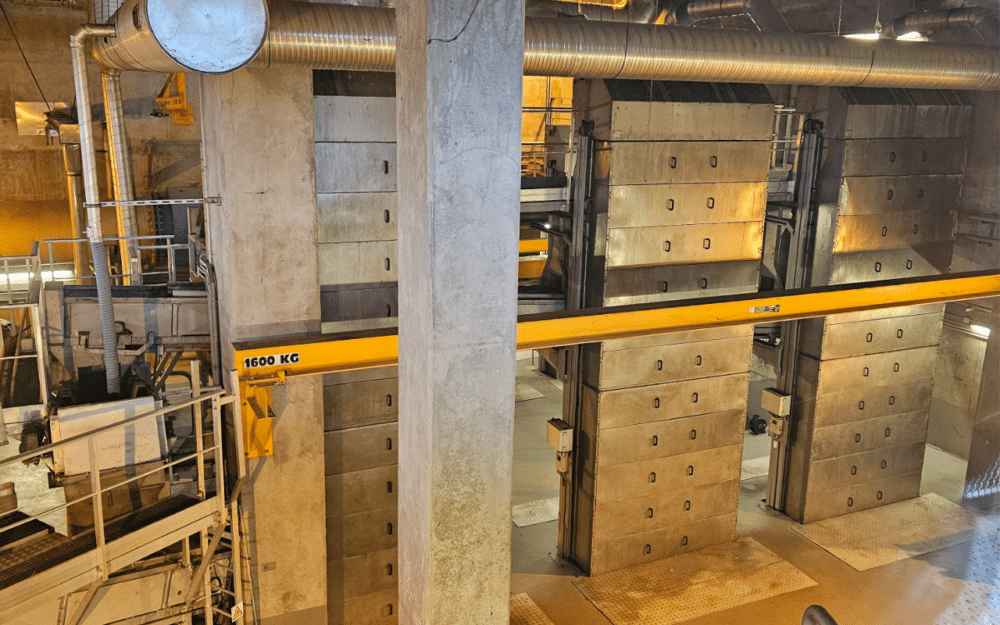
Therefore, the polluted water passes through specific equipment to remove these solid wastes. First, a grit trap captures high-density solid debris. Then, large screening towers with 15-meter high bars, known as coarse screens, remove solid waste larger than 5 cm, such as wood, cans, and sometimes dead animals.
This specific screening during rainy weather has a capacity of 12m³/s.
The fine screen then processes the effluents screened at 5 cm to capture debris between 1 and 2 centimeters. In this fine screen, both wastewater and rainwater are treated at a flow rate of up to 1.7m³/s.
The trapped waste is collected by conveyor belts and stored in bins. It is then disposed of in the household waste incineration plants of Greater Lyon, where it is converted into energy.
“Eighty percent of the refuse from the screens consists of wipes. Unfortunately, we cannot capture all of them, which leads to blockages—a real disaster.”
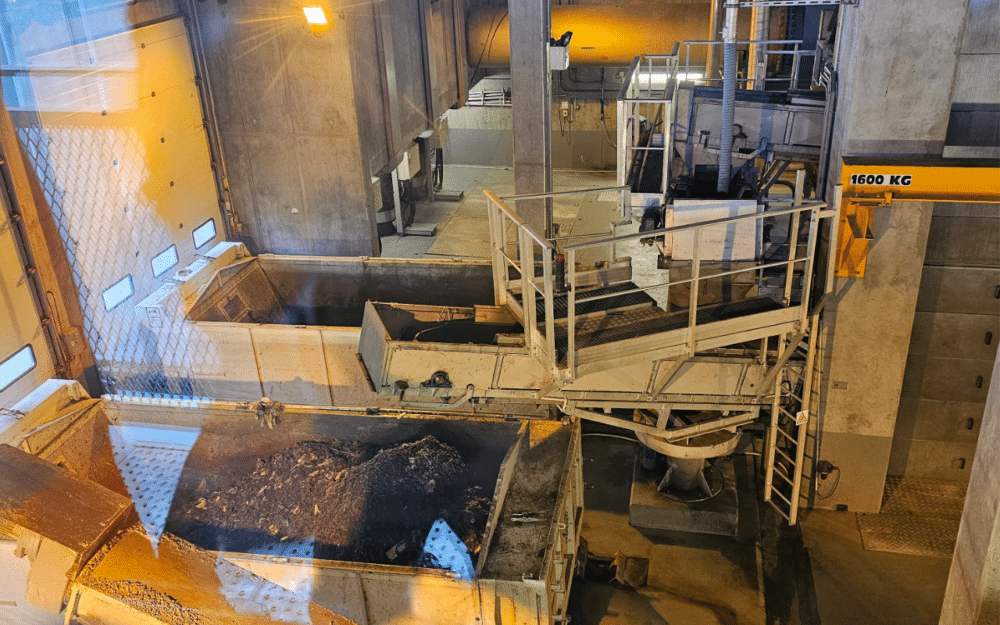
Step 2: Sand Removal, De-greasing, and Decantation
After screening, the wastewater undergoes sand removal, de-oiling/de-greasing, and primary decantation. The goal of this stage is to eliminate as many particles, sand, grease, and carbonaceous materials as possible.
This process takes place in a closed rectangular structure. Grease, aided by aeration of the water, rises to the surface and is skimmed off. The sand that settles at the bottom of the basin is also recovered to be cleaned, dehydrated, and reused, particularly in sewer network projects.
“Next, we inject microbubbles to make the grease float and collect it. Grease is rich in biogas, so we must not lose it.”
The water then undergoes primary settling to remove suspended solids. The principle applied here is lamellar settling. Under the influence of gravity, liquid-solid separation is accelerated by an inclined plate settler set at sixty degrees. The sludge accumulates at the bottom, is scraped, and directed towards a specific treatment path. This primary sludge will also be used to produce biogas.
“The removal efficiency here is quite good. The clarified water loses about 70% of its suspended solids. At this stage, the water already looks very clear. This water is collected to be sent for secondary treatment.”
The maximum flow rate is 6000m³/h. In this plant, the treatment units are adjusted based on the flow rate to avoid excessively long sludge retention times. Thierry says they have a precise satellite monitoring system with three-hour forecasts, allowing them to adjust operations based on dry weather or rain.
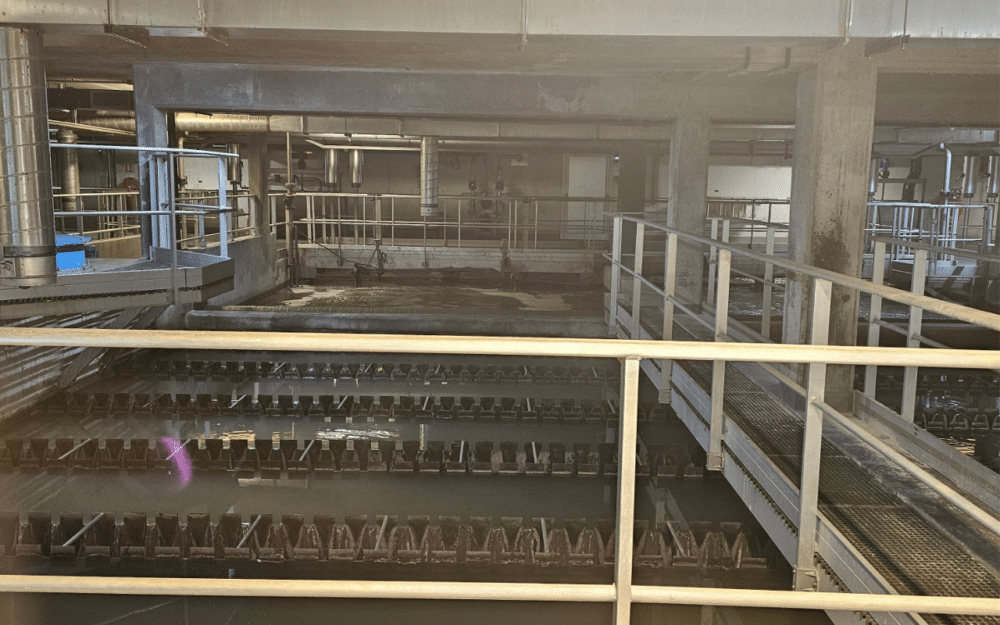
Step 3: Biological Treatment
The once-settled and clarified water moves on to the next stage: biological treatment. The goal here is to reduce the dissolved carbon and nitrogen pollution in the water. This process takes place in outdoor aeration basins. Pollutants come into contact with microorganisms that degrade and transform them.
The water exiting the primary clarifier is mixed with bacteria in a combined culture, with a contact time of around ten hours. By the end of this period, the bacteria have eliminated all soluble pollutants.
The introduction of oxygen and agitation in the three aeration basins accelerates this natural biological process. However, this activity results in a loss of bacteria, requiring the reinjection of sludge to renew them.
Next, the biological sludge must be separated from the water via clarification basins. The clarifiers are large structures with a very laminar flow, minimizing turbulence to allow the sludge to settle. In these rectangular clarifiers, six thousand cubic meters of water pass through each hour.
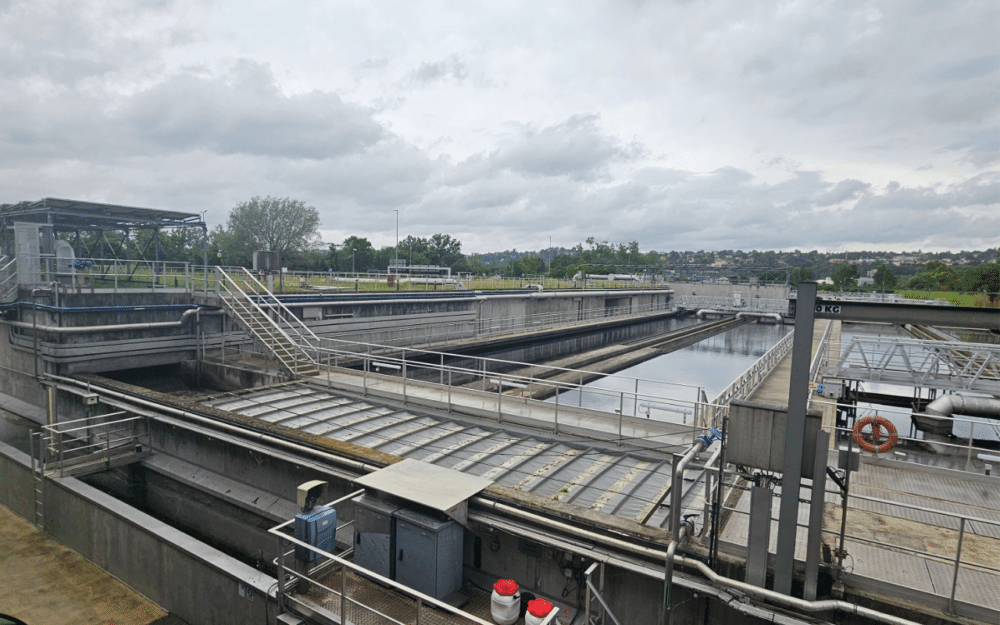
This biological sludge is then redirected to the head of the station and is also used to produce biogas.
The purified water is then directed to the discharge conduit that returns it to the natural environment, the Rhône River.
“A particle of water that enters will take 24 hours to exit.”
Aqualyon, like all wastewater treatment plants, is not tasked with treating 100% of the pollutants found in wastewater and rainwater. According to current European regulations (the 1991 Urban Waste Water Treatment Directive), treatment plants must remove between 82% and 95% of pollutants. For example, at Aqualyon, while nitrogen and carbon are effectively treated, phosphate is not among the targeted pollutants.
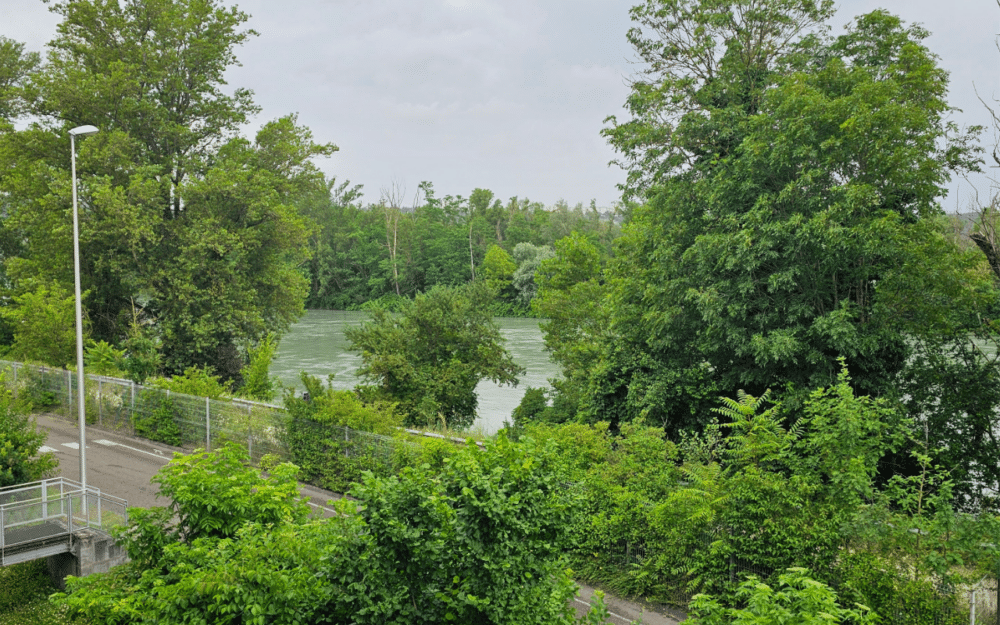
Valorization of Sludge
The sludge produced during the various stages of wastewater treatment constitutes another crucial component of the purification process that is happening at this station. Each cubic meter of wastewater generates up to 400 grams of sludge, amounting to 2.4 tons per hour.
Primary decantation yields sludge with a very high water content. A static thickener equipped with a rake concentrates the sludge by gravity, and it is enclosed to control odors. The thickened sludge undergoes conditioning to reduce its volume through final drying.
The biological treatment produces a mixture of water and organic sludge, which is separated by clarification. The sludge then follows a conditioning circuit to reduce its water content, with centrifugation concentrating 6.6 tons of material per day.
Biogas Production
The primary sludge then goes to a digester. In this heated facility, a defined fermentation period stabilizes the sludge and renders it inert. Being primarily organic, the sludge releases combustible methane. This methane is stored in a double-envelope gas holder and used as an energy source.
“The sludge from the water treatment plant is sent to the digester, where selected bacteria perform all the steps of methanization. To cultivate these archaebacteria, which are very delicate, the environment must be oxygen-free, maintained at temperatures between 35 and 37 degrees Celsius, and free of nitrate, as nitrate inhibits fermentation. The residence time is relatively long, around twenty days, as the bacteria take time to break down the material. By following the precise recipe and operational conditions, about 40% of the mass is converted into biogas.”
This biogas is rich in methane, comprising approximately 63%, with the remainder being CO2 and various impurities, including volatile organic compounds (VOCs).
However, this raw gas cannot be injected into the GRDF network until the methane content reaches 97%, with all impurities removed. The gas holder acts as a buffer to align energy demands with production, preventing service interruptions. Excess gas is managed by a flare system.
Most of the biogas is processed on-site. First, it passes through blue filters with activated carbon to trap H2S. The gas is then dried, VOCs are eliminated, and it is compressed to about 14 bars. The gas is then passed through membranes for molecular sieving, separating CO2 from CH4. With this technique, the methane content reaches the required 97%.
This purified biogas is used to maintain the digester’s temperature and to dry the sludge.
Conversion to Biomethane
In 2018, the metropolitan area decided to upgrade its biogas to biomethane. This led to an investment in a biogas purification unit and a system to reinject methane into the GRDF network.
Annually, 6.2 GWh of biomethane is injected into the GRDF network, equivalent to the gas consumption of 520 households or 28 CNG buses.
“The facility is fully operational, and 99% of the produced biogas is converted into biomethane. Over the past three years, we have been producing between 5 and 5.5 GWh of biomethane, while our total energy consumption, including electricity, has been around 7 to 8 GWh.”
After biomethane production, the sludge is sent for dehydration.
The dehydration process involves a large machine similar to a salad spinner to remove water. Polymers are added to the sludge to aggregate it, making it easier to dehydrate.
Currently, the drying units are not in operation. Instead, the sludge is directed towards composting and soil return rather than being used as fuel, as was the case until 2021.
“The focus now is on returning nutrients to the soil. Until 2021, we produced dried sludge with a calorific value similar to wood, used in cement kilns as a substitute for coal. The metropolitan area has decided to concentrate all biogas towards reinjection into the grid.”