Carbon Blue aims to recycle plastic waste. Founded by Stéphane Testa, the company transforms used plastic sourced from the Marseille area into unique furniture, sold locally. They plan to replicate this model throughout France and internationally. Carbon Blue’s microplastic recycling factories are already being set up in Bordeaux and maybe soon in Africa. We visited the Testa family at their pilot micro-factory in Gémenos, near Marseille.
Sébastien Killian contributed to this report.
Plastic, a cornerstone of 20th-century industrialization, is now a major pollutant. The UN warns of a “toxic tidal wave” with 400 million tonnes of plastic waste generated annually. This waste pollutes oceans, soil, and the food chain, posing a significant environmental threat alongside global warming.
The Single-Use Plastic (SUP) Directive targets plastic pollution by mandating all packaging be reusable or recyclable by 2030. However, plastic production continues due to its utility in packaging, storage, and transportation, leading to an accumulation of waste.
Watch our video report
Recycled Plastic Furniture
Stéphane Testa addresses plastic waste by giving it new life through his company, Carbon Blue, based in Gémenos, near Marseille. They collect plastic packaging from Marseille-area businesses and transform it into wood-like panels, then craft it into colorful furniture sold locally.
This concept isn’t entirely new, as recycled plastic furniture is appearing in decor stores. Stéphane himself comes from MP Industries, a company that has been working with plastics for 70 years and with recycled plastics for the past 30 years.
Carbon Blue’s unique goal is to create additional micro-recycling factories like the one in Gémenos, both in France and globally. Instead of expanding the Gémenos facility, Carbon Blue aims to sell its concept of transforming plastic waste into finished products, such as furniture, with a focus on local management of plastic waste.
Dorian Testa, Stéphane’s son and Director of the Gémenos micro-factory, believes effective plastic waste management requires local treatment, countering the trend of mega-factories:
“We believe that the problem with plastic waste management worldwide is that it is handled too globally. For it to be truly effective, plastic needs to be managed locally.”
We visited their pilot factory in Gémenos to learn about their recycling process and the benefits of local micro-factories in combating plastic pollution.
Inside Carbon Blue Gémenos
Upon arriving at the Carbon Blue workshop, we observe the delivery of large blue containers from a nearby perfume factory. These containers, along with colorful plastic caps already collected, will undergo an on-site transformation process to soon become tables and chairs. These will then be sold locally as final products.
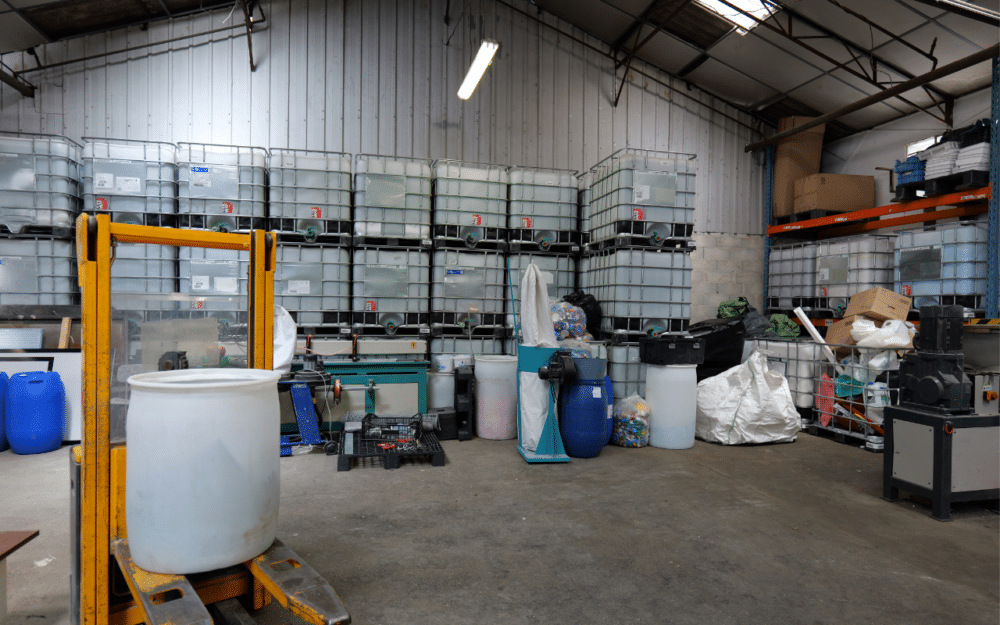
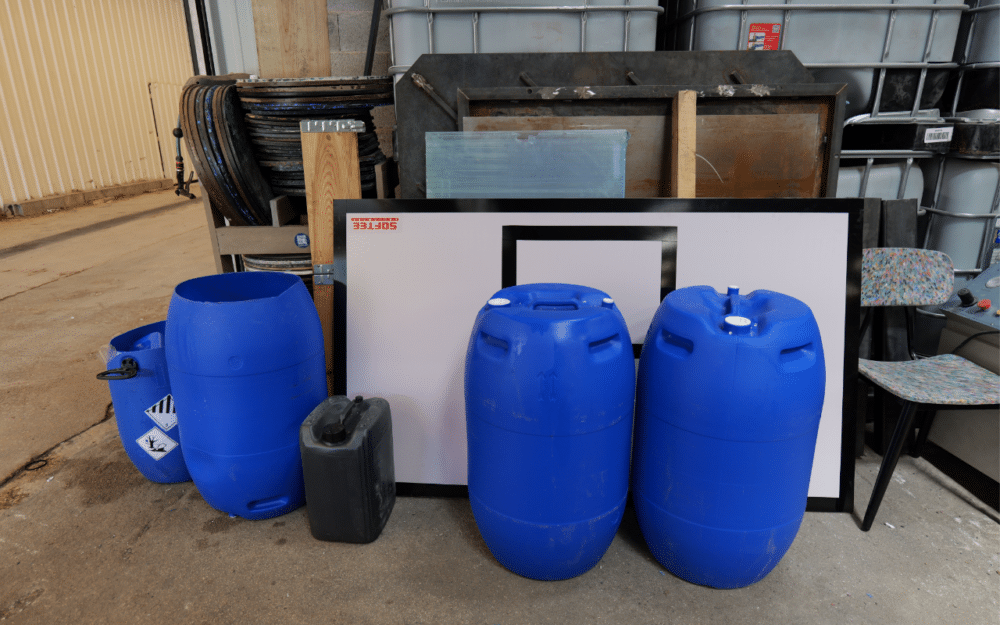
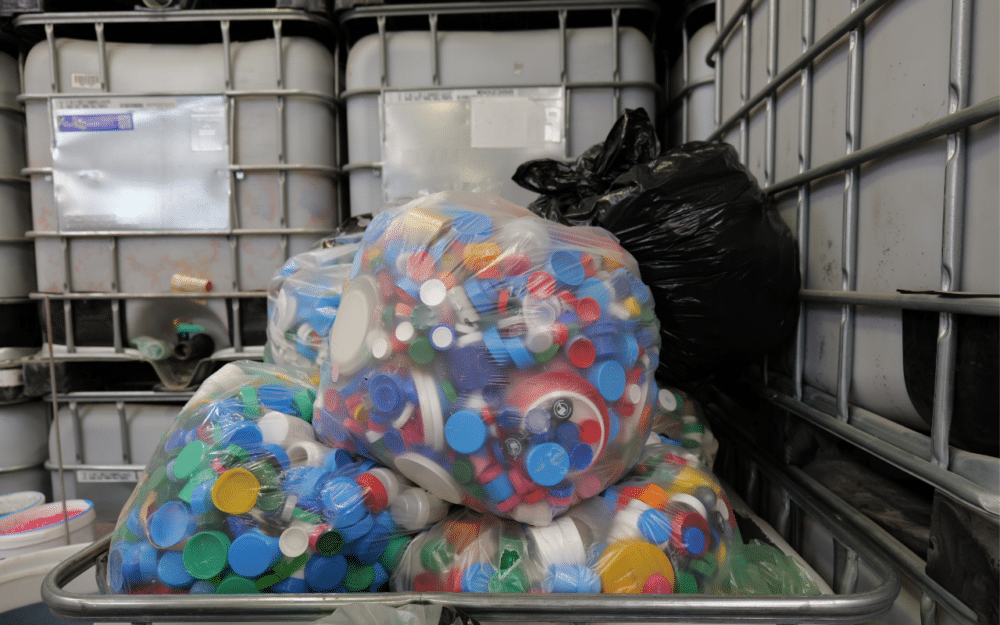
Plastic Collection
The process starts with the free collection of plastic waste from local industries like Sartorius and Decathlon. Stéphane Testa developed this micro recycling factory concept:
“The idea behind this workshop is to collect waste within a 50-kilometer radius. We believe that 50 kilometers is a reasonable distance for plastic waste collection, allowing a micro-factory like this to process 30 tonnes of plastic per year.”
Collected post-consumer plastics include caps, drums, and pallets, but exclude contaminated items due to the absence of a washing process.
“We don’t use any water for washing. Washing water ends up more contaminated, and managing it is complex. So, we only accept products that aren’t dangerously soiled. For example, containers that contained chlorine are pre-washed by the industries before we collect them. The products we receive are residue-free, odorless, and neutral.”
The factory also requires labels to be removed before processing. In exchange for the waste, Carbon Blue provides a receipt confirming its commitment to recycling the materials.
Plastic Sorting
The plastics are sorted and categorized by color and polymer type. The main polymers are HDPE (high-density polyethylene), LDPE (low-density polyethylene), and polypropylene. According to Stéphane:
“The plastics we receive come with technical documentation identifying their composition. We ensure we know the material. If a product is unknown or complex, we prefer not to take it.”
Different polymers transform differently, affecting the process due to varying melting points.
Manufacturing Process
We followed Stéphane as he detailed the various stages of transforming raw plastic material into sheets and then into furniture. This process, which he developed himself, follows three steps: reduction, fusion, and fabrication.
1/ Reduction
As the name suggests, the first reduction step consists of reducing the material. This involves first shredding the plastic waste, for example, the blue container from the perfumery, into pieces measuring two centimeters by fifteen centimeters. This step is carried out using a conventional shredder. The workshop has two types with different teeth and points to handle all types and sizes of waste.
The shredded container is then ground in a grinder to obtain six to eight millimeters of plastic chips.
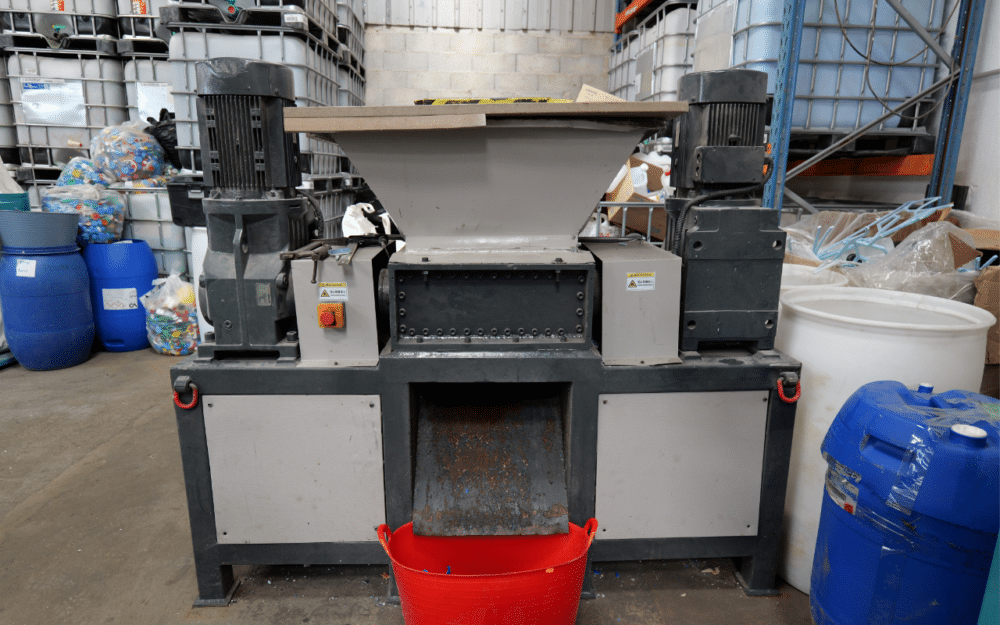
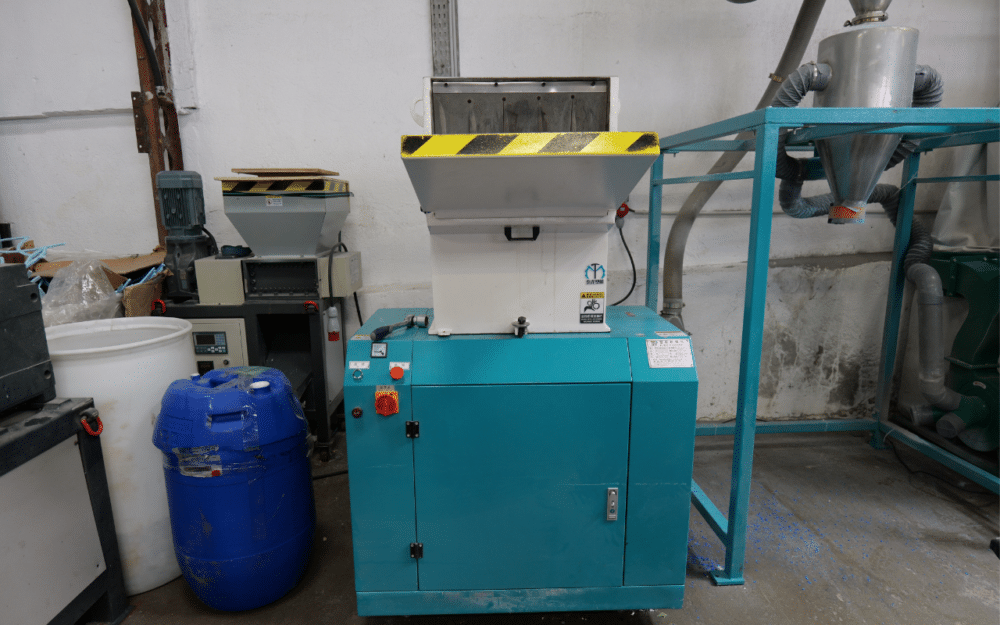
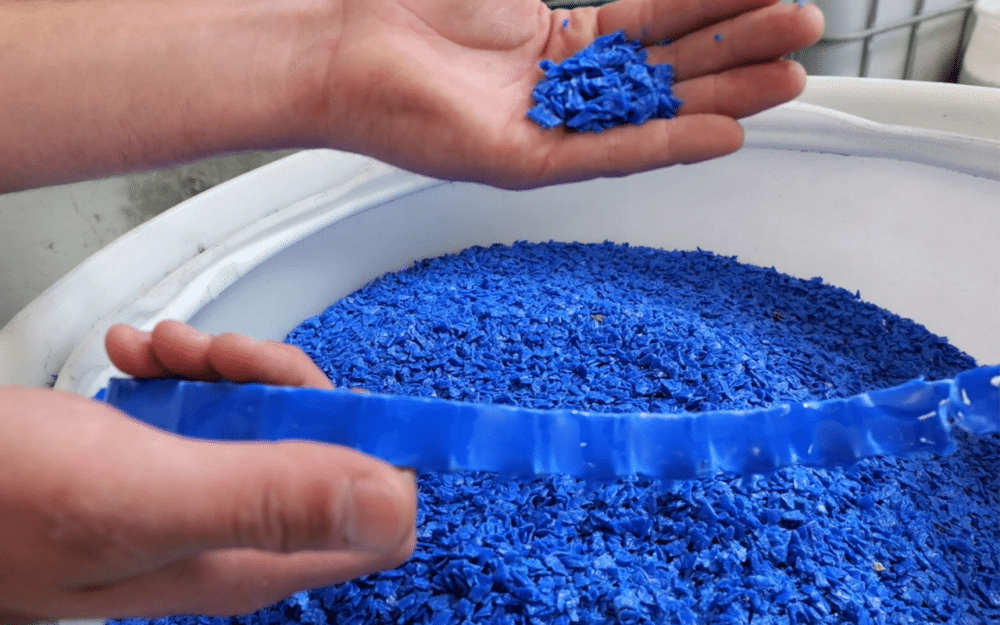
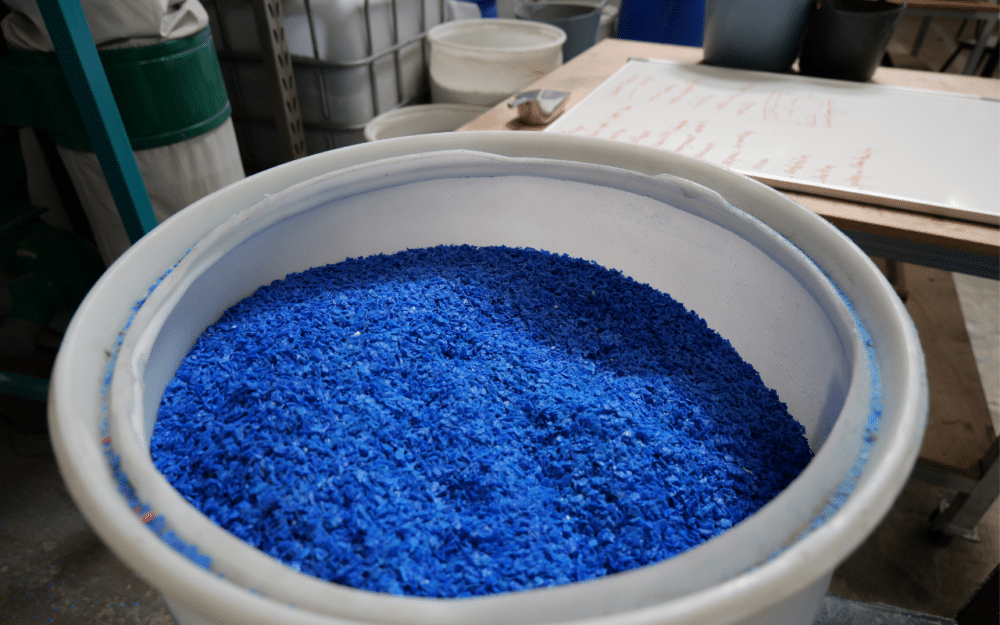
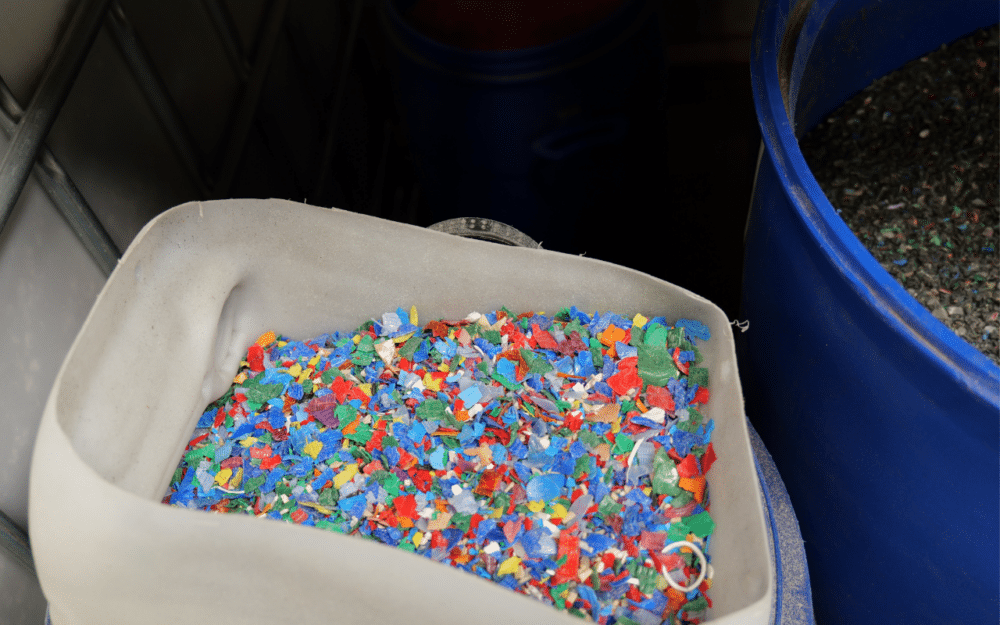
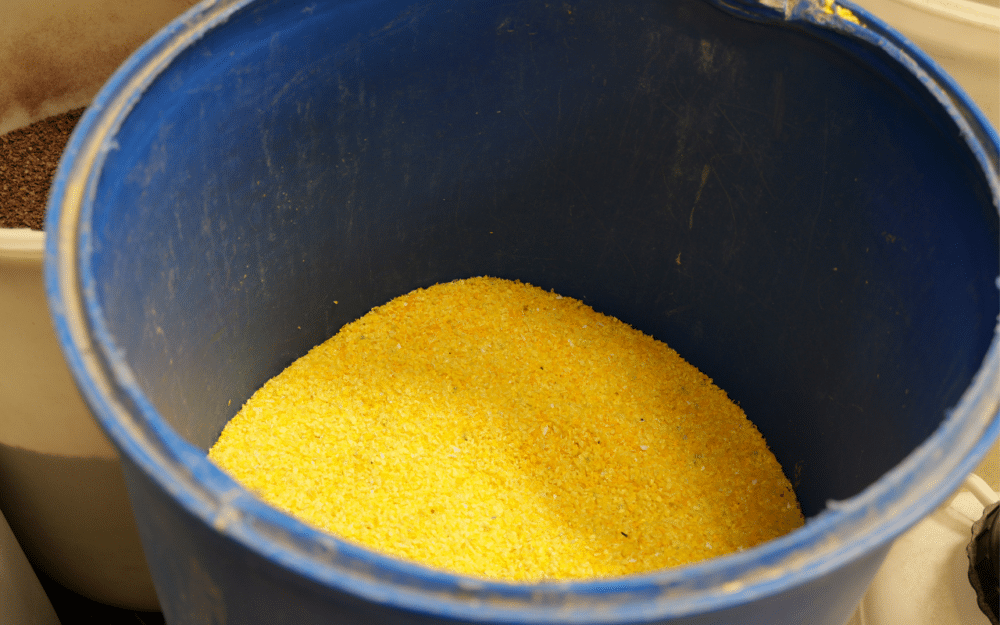
If there is no water washing of the plastic waste, Carbon Blue has nevertheless provided a system for cleaning with hot air, as explained by Dorian:
“When we receive plastic caps, sometimes there are metallic parts. Now, this metal damages the teeth of our grinder. So, we developed a suction technology, called the cyclone, to suck with hot air most of the products that could interfere with the final material. And we installed a magnet at the exit of this suction to recover all the metal so that it does not end up in our plastic sheets.”
The shredder is capable of handling approximately 150 to 180 kilograms of plastic per hour. The grinder, around 120 to 130 kilograms per hour.
2/ Fusion
The second step, fusion, involves heating the shredded plastic to make the famous plastic sheets from which the finished products will be manufactured. For this, the shredded plastic is placed in a mold measuring 1.20 x 1.20 meters and 25 millimeters thick, itself placed in a heating press. It takes 45 minutes to an hour to heat to 250 to 300°C.
Once the heating is completed, the sheet is cooled in a cold press. Cooling time is twice the heating time. Once cooled, the sheets are as rigid as wood and ready to be worked.
According to pull-out tests conducted on-site, a sheet made from pallets will withstand a pulling force of 290 kilograms.
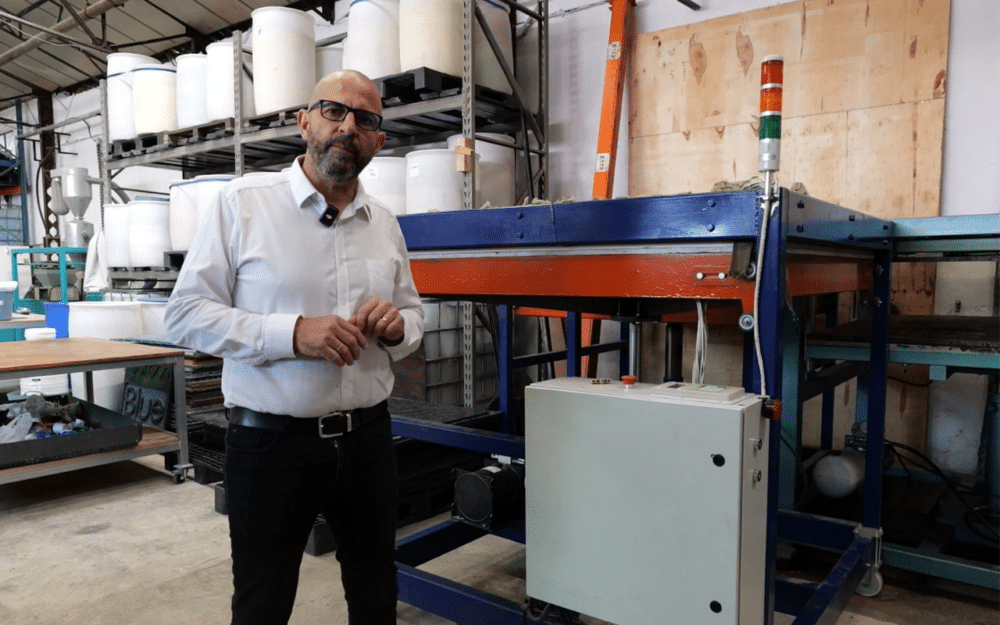
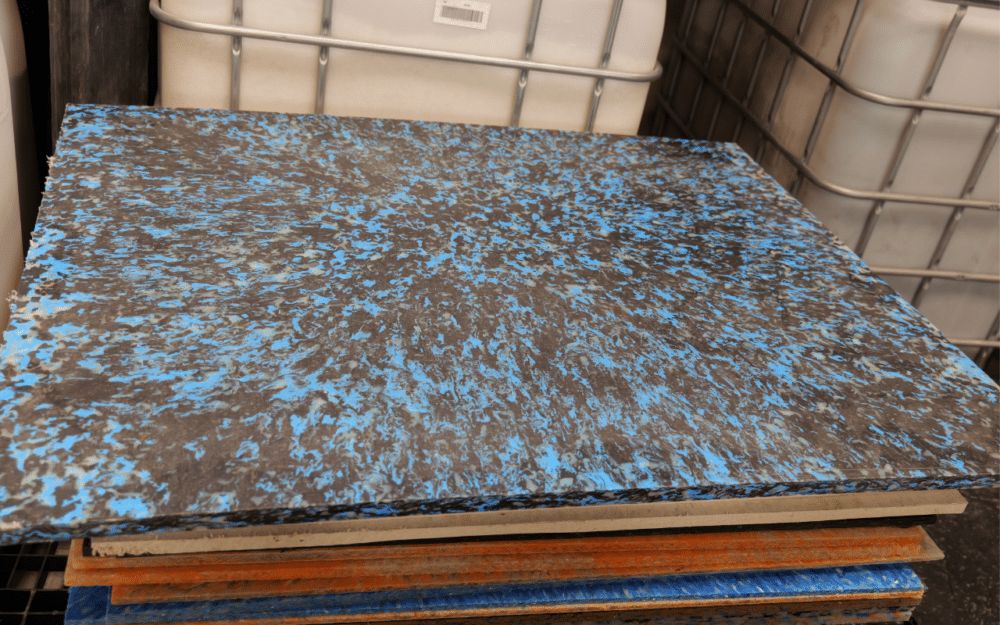
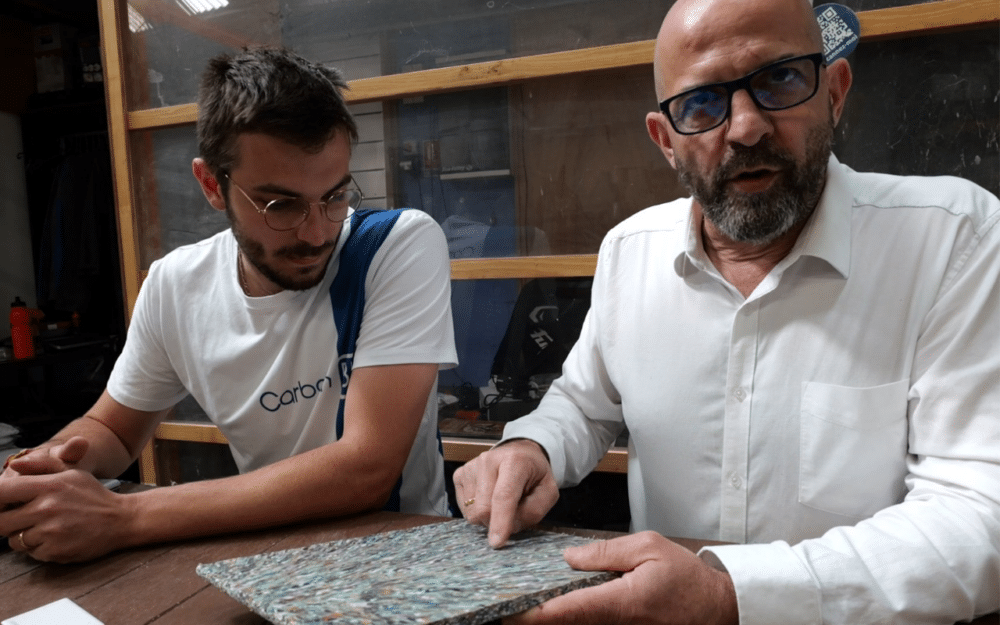
3/ Fabrication
Finally comes the last step, that of fabrication. This is where the plastic cabinetmakers, as Stéphane has dubbed them, will produce products, tables, chairs, and plastic sheets, recounts Stéphane:
“For this step, 3 pieces of equipment are involved: a planer to refine the thickness of the sheet, a combined machine to cut the sheets and work on the edges (for example, to create rounded edges), and a CNC cutting machine to optimize the cuts and thus be able to produce both the backrest and frame of a chair from the same 1.20 x 1.20 sheet.”
It requires 10 kilograms of plastic to make a chair, while an armchair necessitates 35 kilograms of waste.
The plastic obtained is recyclable once again. Carbon Blue even tells us that they systematically recycle scraps and even plastic sawdust. According to Stéphane,
“We assume that all plastics are recyclable and can be recycled indefinitely.”
They also have requests for recycling products made of PET or PVC. For now, the company can only recycle the three polymers mentioned earlier. Polyvinyl chloride indeed releases hydrochloric acid when heated, making its transformation incompatible with the current process, especially the fusion step. The company tells us they are working to find solutions to transform these other polymers.
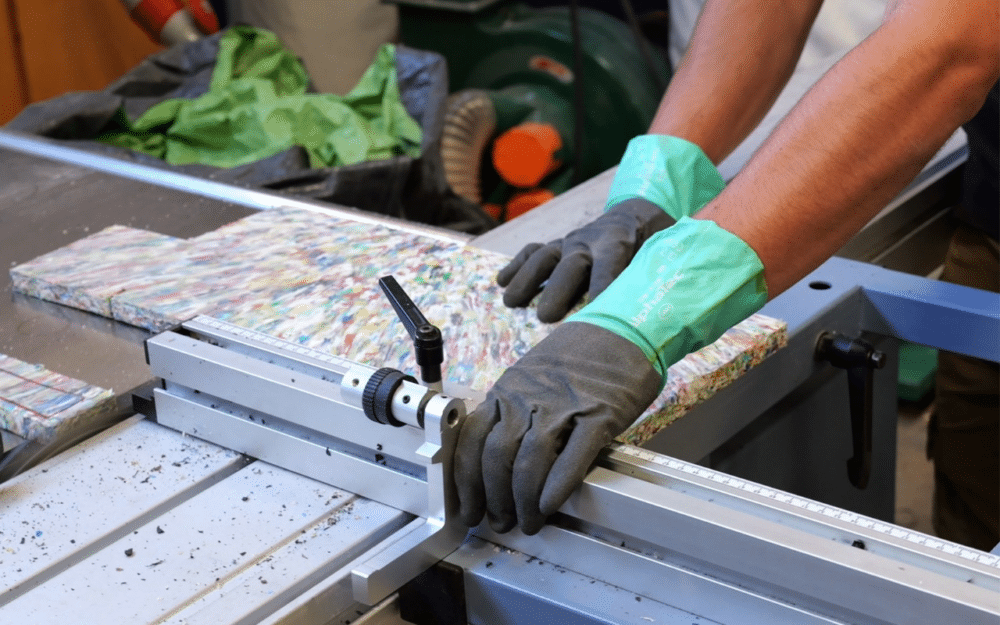
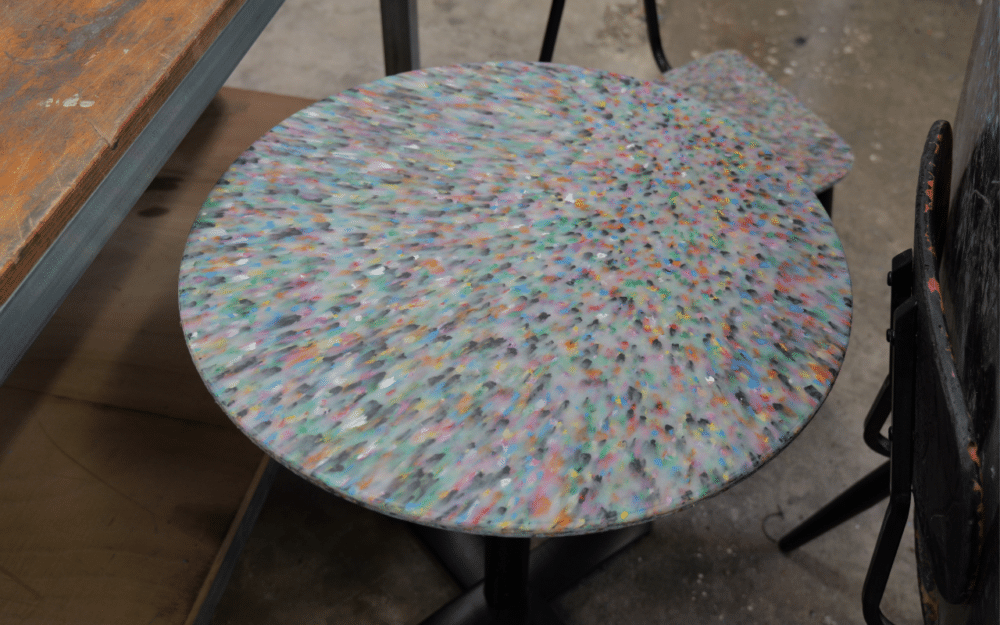
Plastic Quality
In any case, Stéphane assures us that they apply no treatment or additive to the plastic at any point in this process.
“We don’t change the chemical aspects at all. The output product has the same characteristics as the initial plastic waste, neither better nor worse. For example, we are currently working with the port of La Ciotat to transform plastic tarps used to protect yachts. Some of these tarps have an M0 category, meaning fire-resistant. Since we don’t alter the molecular structure of this polymer, nor do we add other additives, the products we produce will also be categorized as M0.”
This is notably the case with a white table that is for sale at the workshop.
However, Dorian tells us that they are working to add composite elements to their sheets. The company is particularly working with Decathlon to manufacture sheets made from crushed rubber tennis balls mixed with pallets. The advantage of the new material is a greater load capacity. Another project is to add bamboo waste:
“It adds rigidity in the central torsion while reducing weight because bamboo is lighter. This allows us to have a new material with different characteristics while remaining recyclable. Because when we grind it again for recycling, the bamboo will be sucked in by the global suction system we talked about earlier.”
Traceability Solution
Regarding traceability, Dorian explains that Carbon Blue is working on a traceability solution, Ecotrace, to trace every plastic waste entrusted to them that has been used in a finished product.
“The idea is to be able to say that this table was produced with 70% PEHD from a certain location and 20% PEBD from another location.”
Replicating the Concept
At the Gémenos factory, Stéphane and Dorian have chosen to manufacture furniture. A table costs 230€ and a chair costs 220€. Just last week, French nuclear company EDF bought several tables to equip one of its sites. Carbon Blue also sells shredded plastic for 20€ per kilogram.
But Stéphane is enthusiastic:
“Plastic material is available in all our territories and for free. It is abundant where wood, iron, or metal are subject to market fluctuations and the law of supply and demand. Every day we can create new products with recycled plastic, to prevent it from being buried or burned.”
Public benches, urban furniture, children’s playgrounds, lighting fixtures, soundproof panels, fire doors… The possibilities are endless.
And for Stéphane, the future of Carbon Blue lies in duplicating its concept. Instead of selling various recycled plastic products all over France, why not install turnkey micro-factories everywhere in France to locally transform used plastic into new finished products?
The idea is for each local micro-factory to collect around 30 to 40 tons of locally sourced plastics, as is done in Gémenos, to manufacture and then sell new finished products that address local issues.
“The finished products will not be the same depending on the geographical area and the available raw materials.”
When asked if the franchise model would be suitable, Stéphane says no:
“We tried to imagine a franchise principle, and in fact, we realized that the issues are different in Nice, Bordeaux, La Ciotat. It’s difficult to franchise the concept. We prefer to sell it.”
Towards Micro Factories in France and Africa
Carbon Blue has already installed the first micro-factory at the port of La Ciotat equipped with a shredder and a grinder, the same as in Gémenos, and an agglomerator that allows for the processing of flexible plastics such as tarps. The goal: to collect and shred on-site the white tarps that protect yachts. The shredded material will then be used elsewhere to manufacture fire doors or impact protection elements for boats.
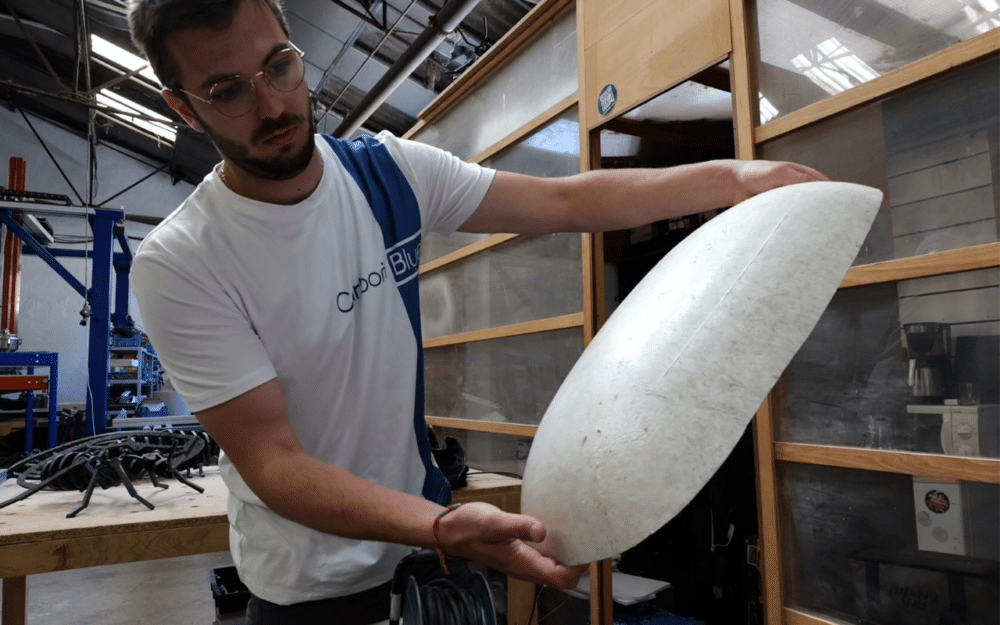
Another micro-factory is being deployed in Bordeaux. This one will be used to manufacture lockers from carpets. Nice is also interested in the concept.
The company is also working on projects in Africa (Chad, Senegal, Mali) to create the same types of micro-factories but in containers. The team has also developed a 3-axis 3D printer capable of printing recycled plastic. With it, they have made round basins similar to African baskets. In Senegal, some are already interested in the concept.
Stéphane wants these micro-factories to be adapted to local issues but also modular. The idea is for customers to choose the machines they want, as is the case in La Ciotat.
For a turnkey workshop based on the Gémenos model, the cost is around €200,000. The price includes project study (understanding the local ecosystem, assistance in learning to recognize plastics, and installation of equipment up to the manufacture of finished products).
The basic equipment includes two shredders, a grinder, a hot and cold press, and three manufacturing machines. Designed by Stéphane, the machines are manufactured in China.
“If we were to take German, French, or Italian equipment, our concept would be between eight and ten times more expensive. The idea is to develop the concept to recycle as much plastic as possible and create employment. We estimate that 10 tons of plastic can generate a full-time job. Our goal is to have nationwide coverage. We aim for about a hundred workshops, each time with local partners who, within a fifty-kilometer radius, will collect the plastic.”
For a complete installation of the micro-factory, it takes 9 months. 3 people are needed to operate the workshop. According to Stéphane, the return on investment for companies is 3 to 4 years.
Next year, they plan to enhance their equipment by offering new machines such as a compactor, a dryer, a folding system, a conveyor belt, and the famous 3D printer.
Carbon Blue currently has a turnover of €200,000, but Stéphane hopes to reach €400,000 this year.
Other Applications
Stéphane envisions several other outlets for his concept, such as trade shows and festivals.
“In the case of a trade show like the Cannes Film Festival, we could set up a mobile micro-factory on-site, for example, in a container. And at the end of the event, the organizer would be able to collect the waste generated there (carpets, tarps…), and shred them directly on-site. The same goes for supermarket waste. For us, the goal is to be as mobile as possible to go where the waste is.”
Another project is to install a Carbon Blue micro-factory directly in recycling centers and waste disposal sites.
For Stéphane, the ultimate concept would be to install a micro-factory next to a city responsible for collecting all its plastic waste. With this setup, the local Carbon Blue factory would manufacture urban furniture, and when it needed replacement, it would take it back. Tables, chairs, and other public benches would be shredded, fused, and shaped into new products again. The very concept of circularity designed at the local level.