The rise of ‘sustainable’ plastics holds the potential to mitigate the global carbon footprint associated with conventional plastics. However, this innovative class of plastics still carries a substantial environmental footprint.
Plastic was a cornerstone of 20th-century industrialization but it is also one of the world’s most toxic pollutants, with the United Nations warning of a “toxic tidal wave” as the world generates 400 million tonnes of plastic waste each year.
Plastic, microplastics, and the hazardous substances they contain are gradually choking the oceans, polluting the soil, and seeping into the food chain – creating one of the world’s most pressing environmental issues, alongside global warming.
To combat plastic pollution, the European Union has issued a Single-Use Plastic (SUP) Directive targeted at food packaging and cutlery. Looking at the big picture, it is also pushing for plastic to have a more circular and sustainable lifecycle. For example, all packaging in the EU must be reusable or recyclable in an economically viable way by 2030.
The Challenges of Bioplastics
Traditionally, plastic has been made from fossil fuel-based chemicals like natural gas and petroleum. The first generation of new “bioplastics” are more environmentally friendly because they are made from crops like corn or sugarcane, similar to first-generation biofuels designed to provide a substitute for petrol and diesel.
While this new approach to making plastic reduces its overall carbon footprint, that doesn’t change the fact that most bioplastic is still just as toxic as traditional plastic, according to a study from Goethe University Frankfurt and PlastX Research Group.
Like traditional plastic, some bioplastics can be recycled to mitigate plastic pollution. However, the recycling process for bioplastics often necessitates specialized facilities and mandates that they not be mixed with other plastic materials. If the plastics are not sorted correctly, recycling batches can become contaminated, potentially leading to their disposal in landfills. This outcome can result in the leaching of harmful toxins into the environment.
READ ALSO
Not all bioplastics are biodegradable and, even those which are biodegradable are not necessarily as environmentally friendly as they seem. Most biodegradable bioplastics require very specific conditions of temperature and humidity which are only fit for industrial processing plants, rather than home composting.
The term bioplastics is also open to very wide interpretation as plastic makers attempt to appear more environmentally friendly. For example, some bioplastics are actually still made from fossil fuels and only called bioplastics because they are biodegradable. Adding to the confusion, some so-called biodegradable plastics only break down into toxic microplastics, rather than into environmentally friendly substances.
Likewise, some plastics are called “sustainable” not because they are bioplastics, but simply because they prevent waste from ending up in landfills.
UBQ Materials
Israeli company UBQ Materials makes durable sustainable plastics from unsorted household waste that cannot be recycled, such as food waste, unrecyclable plastics, and dirty cardboard. By keeping this waste material from landfills, it reduces methane emissions and the leakage of toxic substances into the soil.
When it comes to actual bioplastics, made from more environmentally-friendly sources than household waste, there are still significant challenges.
The crops for first-generation bioplastics compete for available farming land and could put pressure on global food supplies, similar to first-generation biofuels also made from crops. For this reason, the European Union has committed to start phasing out first-generation biofuels in 2030 and it could also turn its attention to first-generation bioplastics for the same reasons.
New second-generation bioplastics don’t compete with edible crops. Instead, they are made from non-food renewables like wood biomass, non-food vegetable oils, and bagasse from sugarcane.
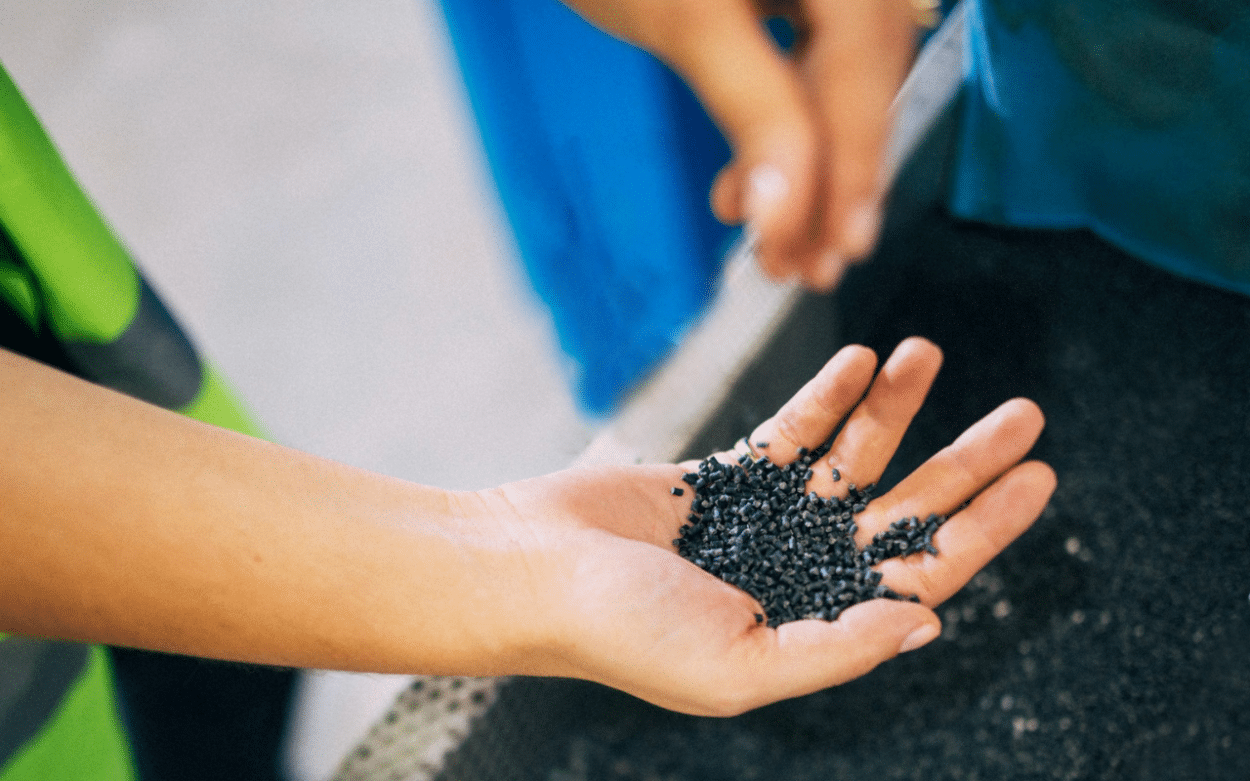
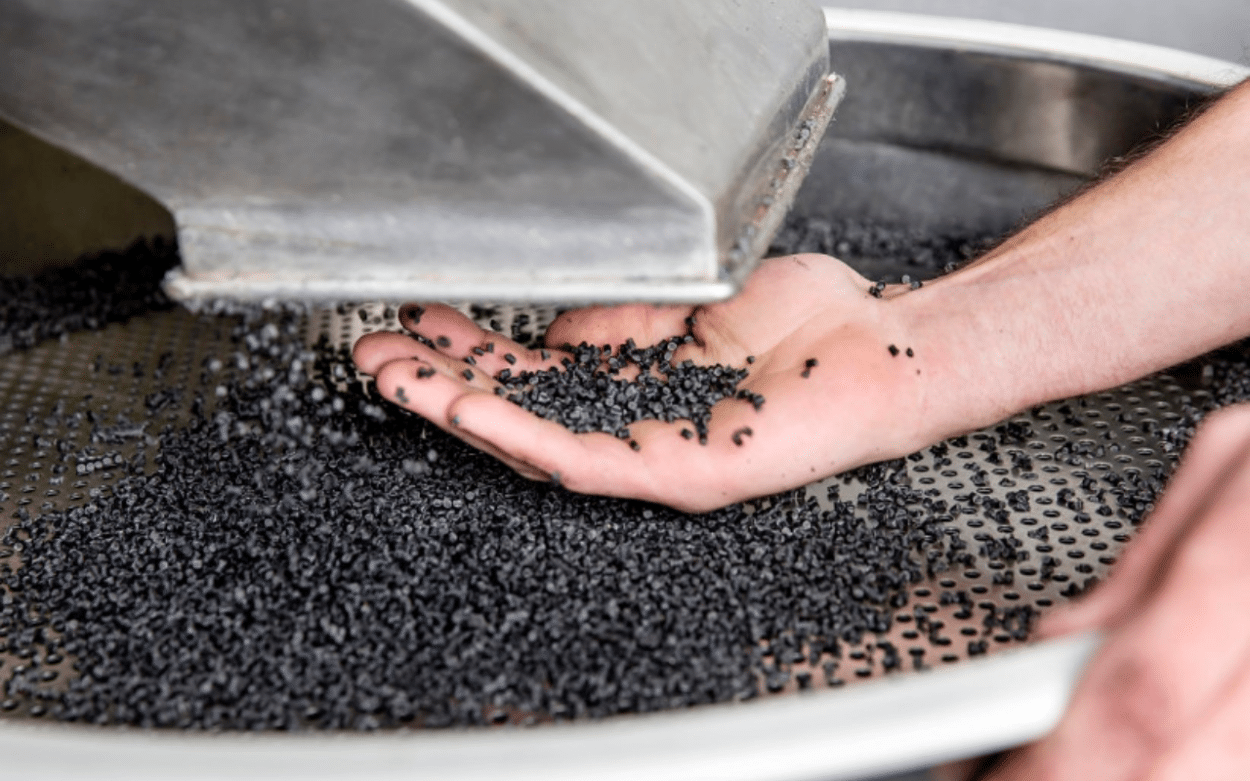
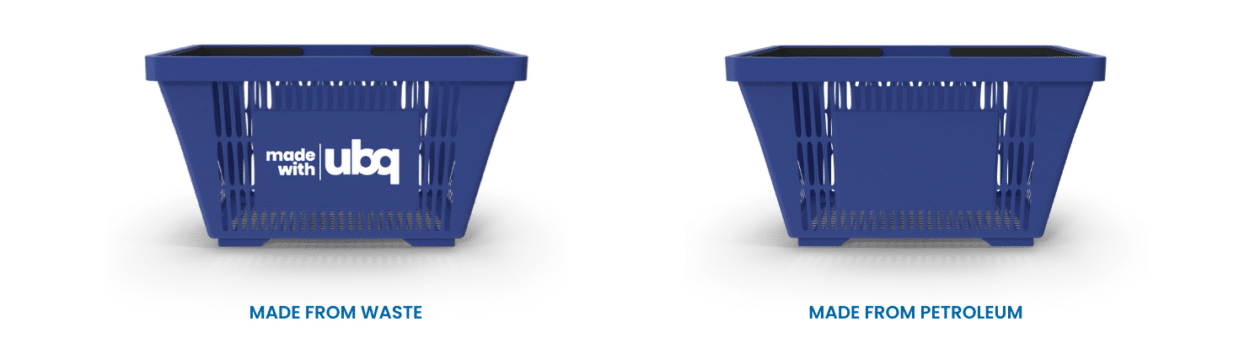
ABMT
Canada’s Advanced Bio-Material Technologies (AdvancedBMT) harnesses agricultural waste to create high-performance bioplastics. It uses the leftover stalks from flax and hemp seed crops, of which more than 1 million tons are currently burned annually in North America rather than being put to better use.
If AdvancedBMT expands to use other crop waste, like corn or wheat straw, the available supply increases to more than 20 million tonnes annually.
Going forward, third-generation bioplastics will be made using soil-less farming and non-food crops, such as bacteria, micro-algae, yeasts, and wastewater.
The most sustainable bioplastic initiatives focus on not just the raw materials but the full lifecycle of the product. This is sometimes referred to as the “circular plastic economy”, although this is another term that is open to abuse.
Shellworks
The United Kingdom’s Shellworks makes bioplastic from recycled seafood shells. After collecting seafood waste from restaurants, the company’s manufacturing plant extracts chitin from crushed seafood shells, a fibrous substance that makes up the exoskeleton of crustaceans and the cell walls of fungi.
The chitin is crushed into a fine white powder which is mixed with household vinegar to create a liquid bioplastic that is used to make a range of products. Once dried, the material can later be turned back into the original bioplastic solution, making it infinitely recyclable.
Alternatively, it can be poured onto the soil in its liquid form as a natural, non-polluting fertilizer. On average, it takes around a year for a Shellworks plastic product to break down, in contrast to petroleum-based plastics which can take up to 500 years to decompose.
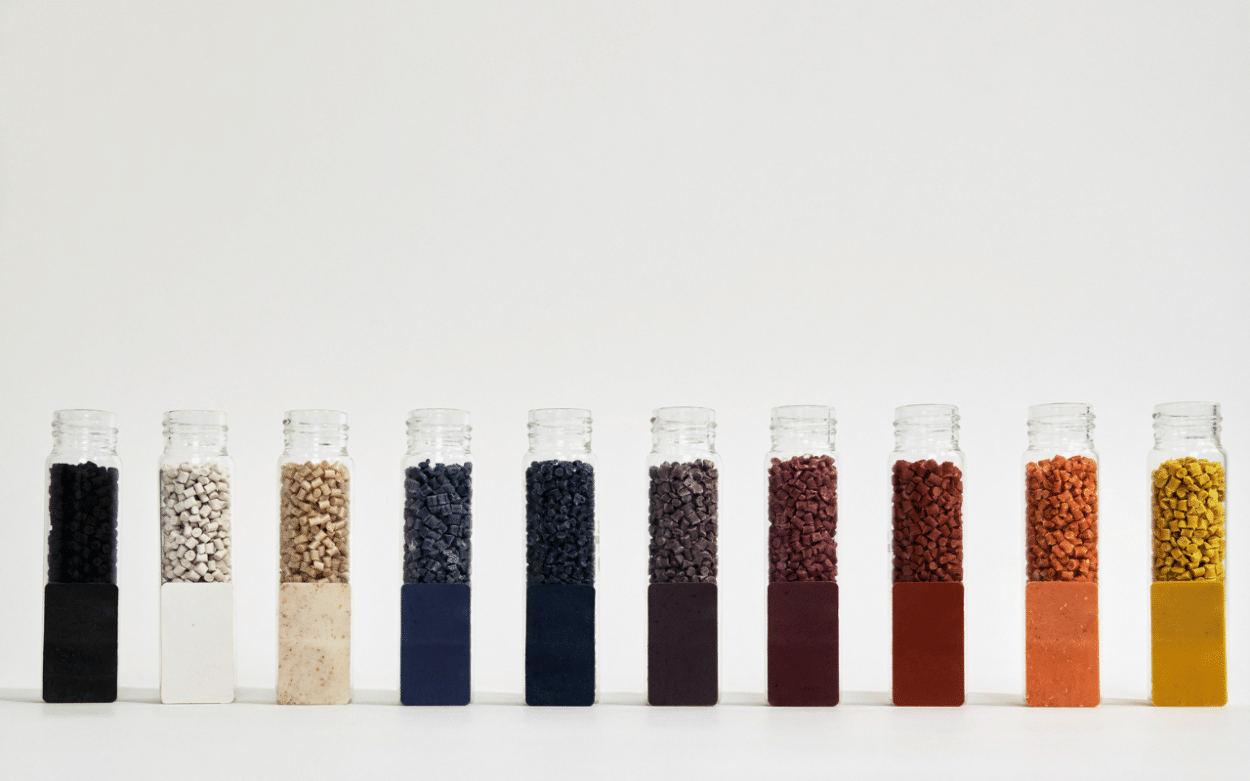
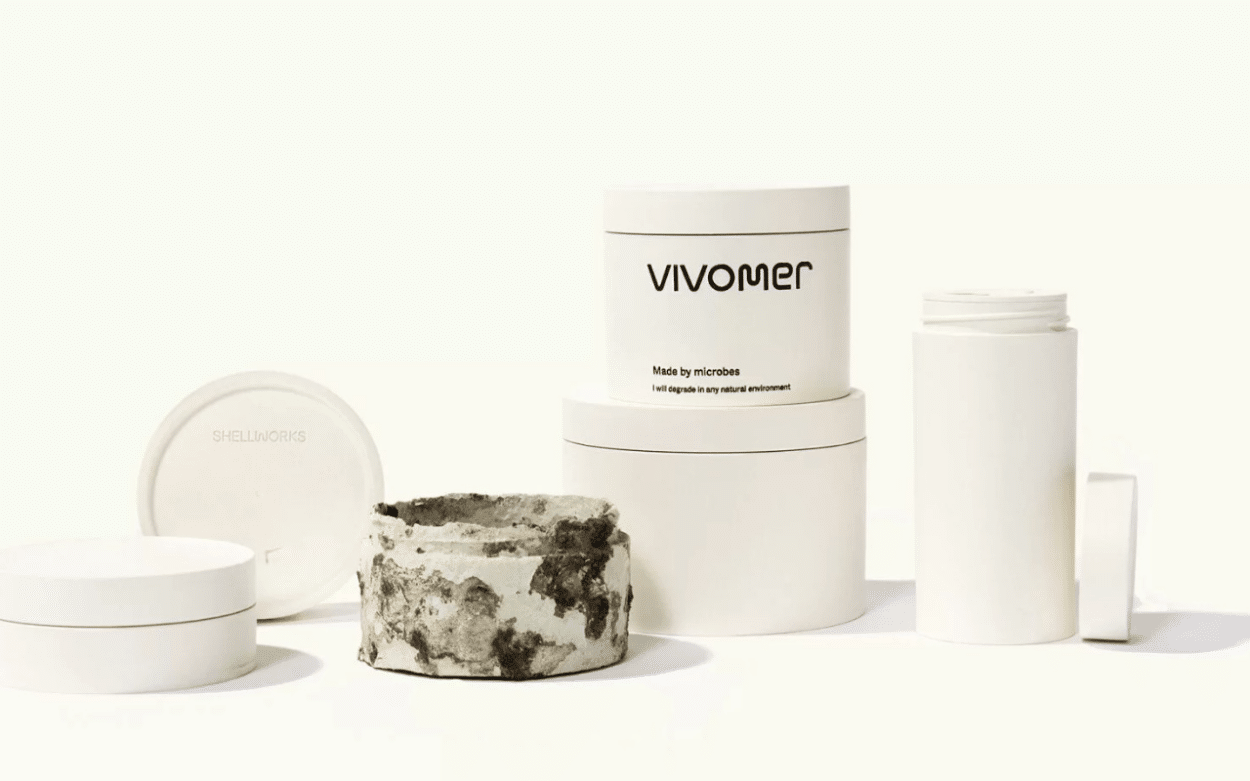
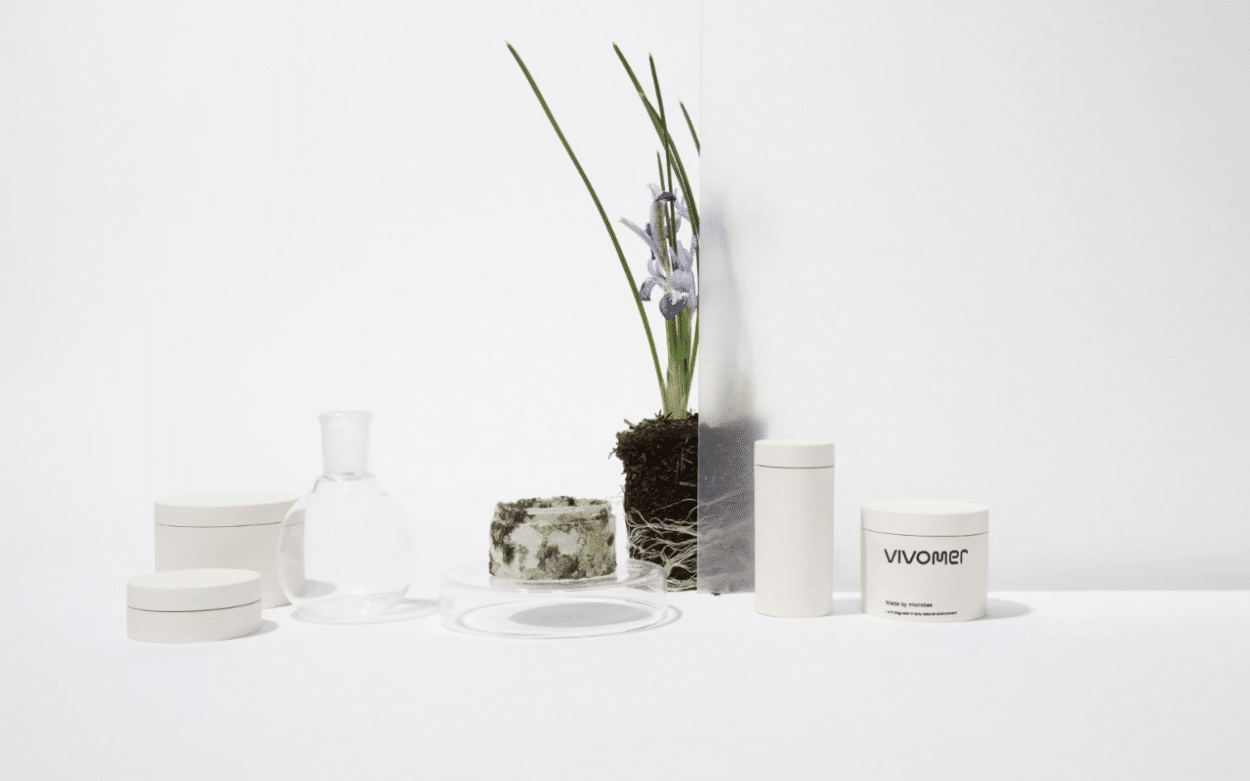