Since 1853, Hutchinson, the French rubber expert, has been supporting the major players in industry in their technical challenges by designing and manufacturing highly technical sealing solutions. Our unique expertise in materials science enables us to respond to changing markets by constantly formulating new materials in our laboratories and research and innovation centers.
Content provided by Hutchinson Precision Sealing Systems
Industrial markets are constantly evolving. Mobility is undergoing a lasting transformation towards electric mobility. Players in these markets need to adapt their products and solutions to best meet new market challenges and requirements.
Thanks to its mastery of material formulations, Hutchinson offers a wide range of approved elastomer formulations. They are compatible with market specifications and approved by the main OEMs and manufacturers in the various industrial sectors.
The development teams are supported by the Hutchinson Research and Innovation Center in Montargis, France. They work in close collaboration with their local laboratories. This enables them to be more agile and ahead of the game on projects thanks to calculations, tests, and simulations.
Committed to major developments in the sector, Hutchinson teams are working on new materials designed for electric and hybrid vehicles. These include new refrigerant gases and more sustainable materials…
Fire-Resistant, Halogen-Free Epdm for Sealing Battery Packs in Electric Vehicles
With the rise of e-mobility, battery safety has become a major issue for automakers. Sealing materials must meet stringent standards in terms of fire resistance, durability and chemical compatibility. Faced with these challenges, Hutchinson chemists have formulated a new EPDM. It complies with UL94, V-0, the strictest level of fire resistance. Unlike other materials on the market, this EPDM contains no halogens, making it safer and more durable.
Intended for battery pack gaskets and seals for the battery pack cooling circuit (quick connectors, sensors), this material offers optimum sealing, good fire resistance and chemical compatibility, as well as excellent low-temperature performance. It thus contributes to making the new mobility safer and more respectful of the environment.
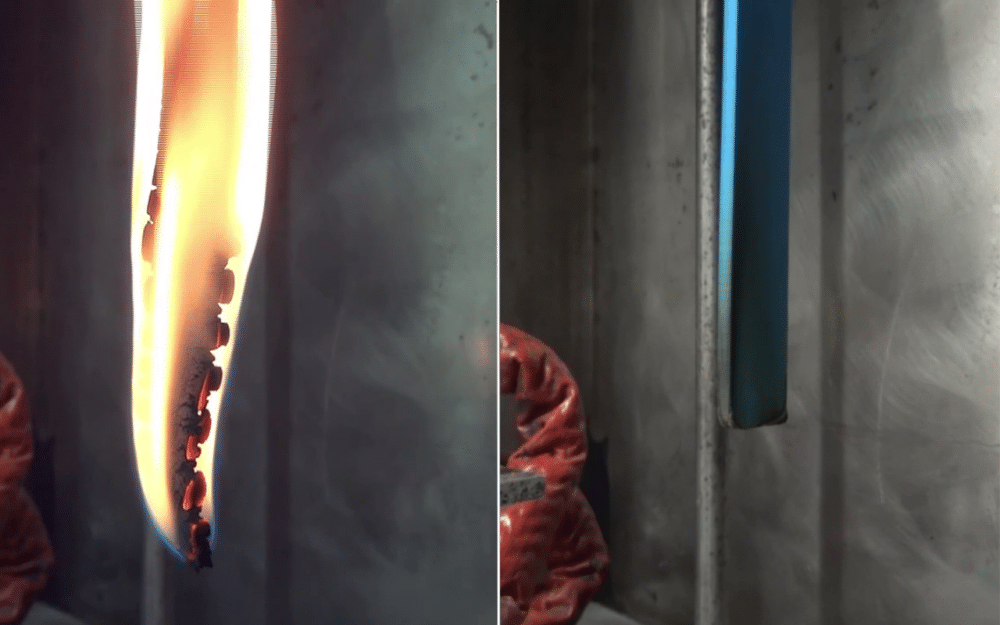
A New Elastomer Formulation Dedicated to R744 Refrigerant Gas
Hutchinson has also developed an elastomer compound specially designed to meet the sealing needs of components used in electric vehicle heat pump applications (valves, compressors, etc.) using the refrigerant R744. This refrigerant is of growing interest to automakers and equipment manufacturers as a response to environmental issues and vehicle autonomy.
Indeed, R744 (CO2) is a natural, non-flammable fluid. It is by definition PFAS-free. And it has a GWP (Global Warming Potential) of 1, far better than the R1234Y currently in use.
The development of this innovative material was made possible thanks to the expertise of Hutchinson’s teams in the formulation of elastomer materials and close collaboration with the Volkswagen Group and a major thermal management equipment manufacturer.
In addition to laboratory tests, functional validations were carried out with expert appraisal of the parts. This confirmed the technical solution in the EPDM 8EP3411 compound.
This elastomer compound offers enhanced thermal performance, with a temperature range from -40°C to +165°C and a hardness of 90 Shore A. It can withstand high pressures of up to 130 bar. Specific tests were carried out on resistance to explosive decompression to achieve the final formulation, in compliance with Norsok M710: Rating 0, confirming the absence of defects after exposure. Indeed, resistance to explosive decompression is a critical characteristic for elastomers to avoid physical degradation of joints (cracking, crazing, bubbling).
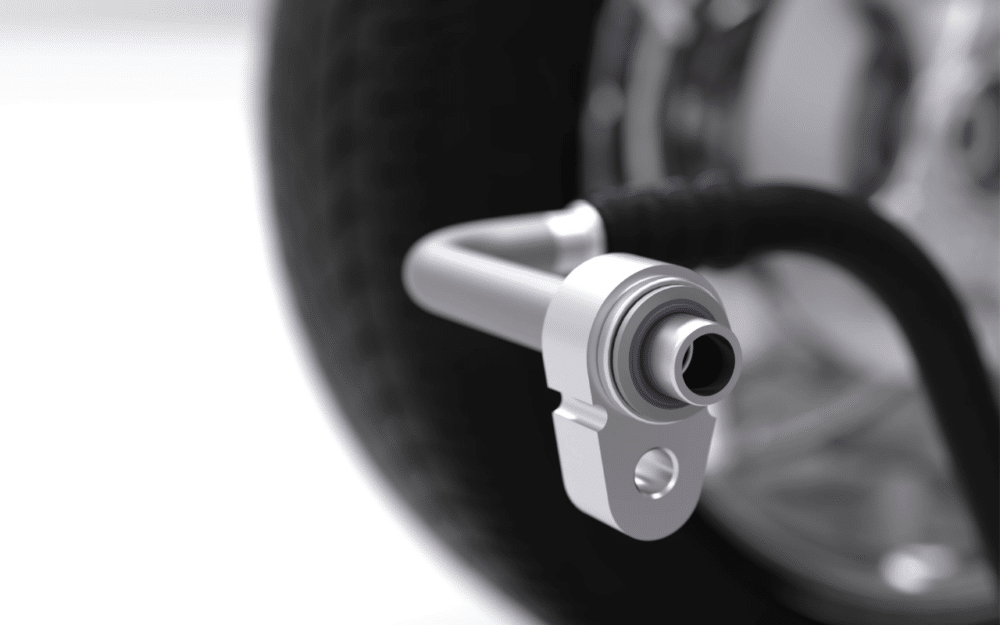
On the Road Towards More Sustainable Materials
To achieve Hutchinson’s sustainable development objectives, our teams and laboratories are actively working to develop new, more sustainable materials. These include recycled materials in our rubber formulations. We are also making progress regarding product life-cycle analysis.