The AgiProbot project (Agile Production System Using Mobile, Learning Robots with Multi-Sensor Technology for Uncertain Product Specifications) aims to automate the disassembly of components for remanufacturing purposes. This 12-year project, led by the German Karlsruhe Institute of Technology (KIT), could one day find significant applications for the disassembly of electric car batteries.
Remanufacturing involves carefully disassembling a product to reuse its components. These parts can then be incorporated into new production cycles or used to construct identical products. It can also mean reworking certain components of the product and then reassembling it to restore around 60% of its functionality.
Circular Economy
Remanufacturing aligns perfectly with the principles of the circular economy and a more environmentally friendly process. Indeed, by extending the useful life of components that would otherwise be discarded, it reduces the need for raw materials and minimizes waste. It also contributes to a more sustainable economy by conserving resources, lowering energy consumption, and decreasing greenhouse gas emissions. Besides, remanufactured products often cost less than new ones, making them an attractive option for businesses and consumers.
Let’s take the example of the starter motor of a car with 100,000 kilometers on the odometer. If it malfunctions and you need to replace it, a new starter motor isn’t necessary. Opting for a reworked, used one is ideal as it conserves materials and reduces CO2 emissions.
However, as M. Sc. Jan-Philipp KAISER, Research Associate at the German Karlsruhe Institute of Technology (KIT) told DirectIndustry,
“The primary issue lies in the manual nature of the disassembly, rework, and reassembly processes, particularly in low-wage countries. Our objective is to automate these processes using robots, which is why we’re researching it. However, it’s challenging due to the variability of product conditions and numerous variants. By automating these processes, we aim to reduce costs and make remanufacturing financially viable in high-wage countries like Germany. This would render it feasible for a wide range of industries.”
Kaiser is part of AgiProbot, a 12-year-old project whose goal is to automate the disassembly of components for remanufacturing purposes. The project focuses on two areas: first, inspection with the help of AI to identify used products for remanufacturing, and second, disassembly where the system learns the process from humans and a cobot then reproduces the disassembly tasks one by one.
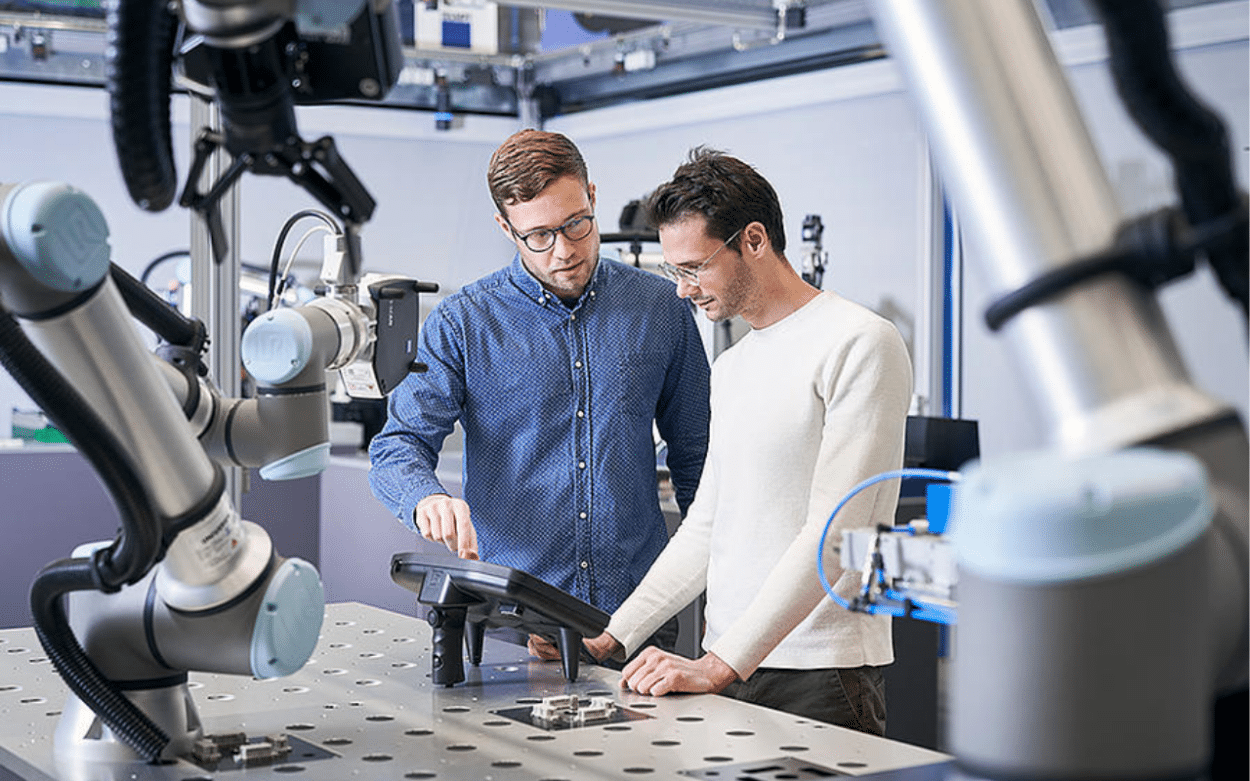
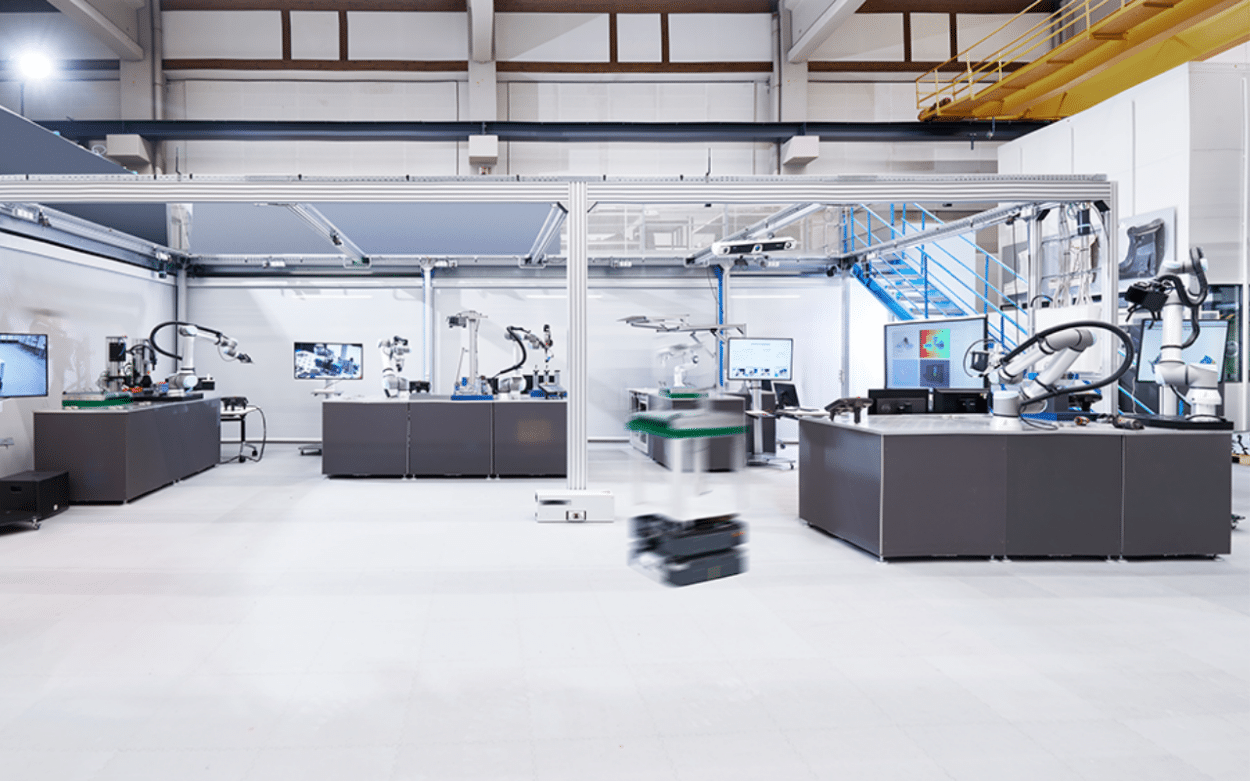
An Inspection Station With the Help of AI
Before a used product is remanufactured, its components are first inspected to verify that their states are adapted to reuse. Sometimes, some used products are so damaged that none of their components can be remanufactured. To save costs, those unfit products must be removed from the process at an early stage. However, this inspection task is often manual. And human inspection can be very tedious and may overlook certain flaws or not recognize minor defects. This very manual task can be automated. Hence the inspection station.
“When a product is returned, it needs to be checked for defects and other factors to determine if it’s worthwhile to disassemble and rework it to salvage the product. We can assess the quality of the component to determine if it’s feasible to proceed with the process. This eliminates the need for human involvement. We aim to fully optimize the process by relying on artificial intelligence, which can reliably detect various defects such as corrosion, damage, cracks, etc.”
What the KIT researchers have developed is an inspection station composed of a rotary table, robotic arms, and a camera system. The camera captures image and geometry data of the used product. The algorithms can then detect the defects.
A Disassembly Station That Learns From Humans
The second part of the project is to automate the disassembly process based on human techniques.
“This involves observing the movements performed by humans during disassembly, such as using a screwdriver to remove screws. Cameras mounted on the robots record these actions, capturing the human’s gaze, hand movements, and other relevant details. This information is used to learn the steps required for disassembly and generate robot code automatically for another robot to execute the task autonomously. This represents a significant advancement in automation.”
No programming is required. The video feed captures the hands’ movements and the eye movements to determine the disassembly sequence and temporal task models to understand the order of actions. AI identifies the tools being used (a screwdriver, a screw) and the tasks being performed (for example, holding the motor while unscrewing the gearbox simultaneously). Each action is translated into code, based on a disassembly graph that outlines the sequence of steps required. This information is then fed into the AI system, which comprehends these actions, compiles them, and can replicate them perfectly.
The future solution, explains M. Sc. Jan-Philipp KAISER, lies in vision systems where workers handle the disassembly of unknown products while the system learns from their actions.
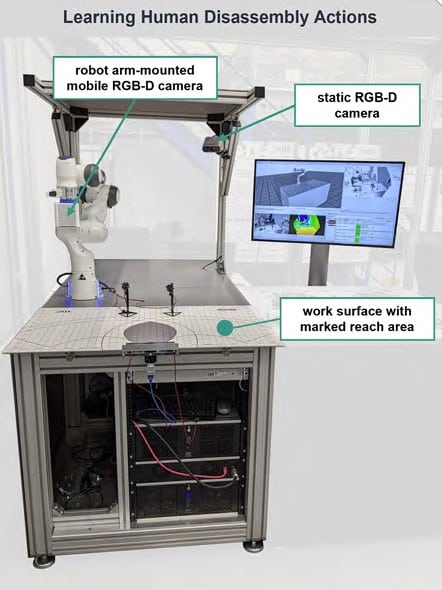
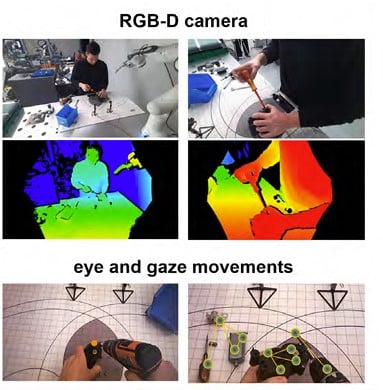
“Once the system learns how to disassemble a product, another station automatically performs the task, relieving workers from disassembling every product. Workers only handle products that are difficult to disassemble, while the system autonomously manages the rest. Ultimately, the goal is to transfer this knowledge to fully autonomous robots, enabling them to execute the task sequentially based on available tools and resources.”
When a new product type is encountered, if the system hasn’t learned it yet, it is routed to a human for handling. The system learns from this interaction and adds it to its library for future reference. This reduces the need for human intervention in disassembly processes while ensuring everything operates smoothly despite the diversity of product types encountered in remanufacturing.
Applications in the Automotive Industry
KIT’s goal is to integrate this solution into industrial factory buildings. The automotive sector is their first target. Starter motors are already undergoing remanufacturing. However, as the automotive industry is shifting to electric vehicles, remanufacturing battery modules will be a better focus for them.
“Battery modules hold greater relevance, particularly for repurposing battery cells for stationary applications from cars. This transition will significantly impact the sector, given the mechanical nature of these products. Over the next 12 years, our focus will be on products like angle grinders whose components can be reused in new product generations. These products undergo rapid technological advancements every nine months, posing challenges for remanufacturing implementation due to the constant changes in assembly systems.”
Recently, Bosch Rexroth unveiled their new battery recycling solution. DirectIndustry had the opportunity to interview Franck Papon, Business development manager at Bosch Rexroth.
Their solution addresses the entire process of battery recycling, from the disassembly of the vehicle battery to refining components for integration into new batteries. It involves pre-treatment to determine the battery’s condition, health status, charge status, and also its model and what the battery is made of.
Just like KIT, Bosch bets on AI to help with the dismantling and discharging process as it is specific to each battery. AI helps for example pair the hood-opening process with the battery that will be presented.
They also create digital twins for each battery to streamline the recycling line.
KIT’s innovations will be presented at Hannover Messe, Hall 13, Stand C76