At Stäubli Technical Days last week, Bosch Rexroth showcased their innovative solutions for factory automation. The spotlight was on groundbreaking technological components designed for both production processes and the recycling of electric vehicle batteries. DirectIndustry met with Franck Papon, Business development manager at Bosch Rexroth to know more about the new solution.
As the demand for electric vehicles is expected to grow in the future, the handling of their batteries becomes a concern. Some are already envisioning new solutions to recycle batteries and reuse their components. This is precisely what Bosch Rexroth is accomplishing with its innovative circular solution.
The recycling initiative is particularly noteworthy, as it enables up to 95% of chemical elements from batteries to be reintegrated into the battery manufacturing process.

Can you introduce the solution you’re presenting, focusing on the technological aspects dedicated to battery recycling?
Franck Papon: “Our solution addresses the entire process of battery recycling, from the disassembly of the vehicle battery to refining components for integration into new batteries. Bosch primarily focuses on the upstream part of the process, specifically on the pre-treatment after the battery is removed from the vehicle.
Pre-treatment involves diagnosing the battery to determine its condition, health status, charge status, and also its model and what the battery is made of. The diagnostic process includes opening the battery hood using AI-driven methods tailored to each battery model. Once the battery is diagnosed, we can load all the machines in the recycling line.
The dismantling and discharging process is specific to each battery. This is where artificial intelligence comes into play to handle the diverse range of batteries efficiently. When the batteries arrive on the production line, they are in an undefined order with different models, as many models as there are existing vehicles. It is impossible to standardize something. Therefore, artificial intelligence is mandatory to pair the hood-opening process with the battery that will be presented. We also create digital twins for each battery to streamline the recycling line.”
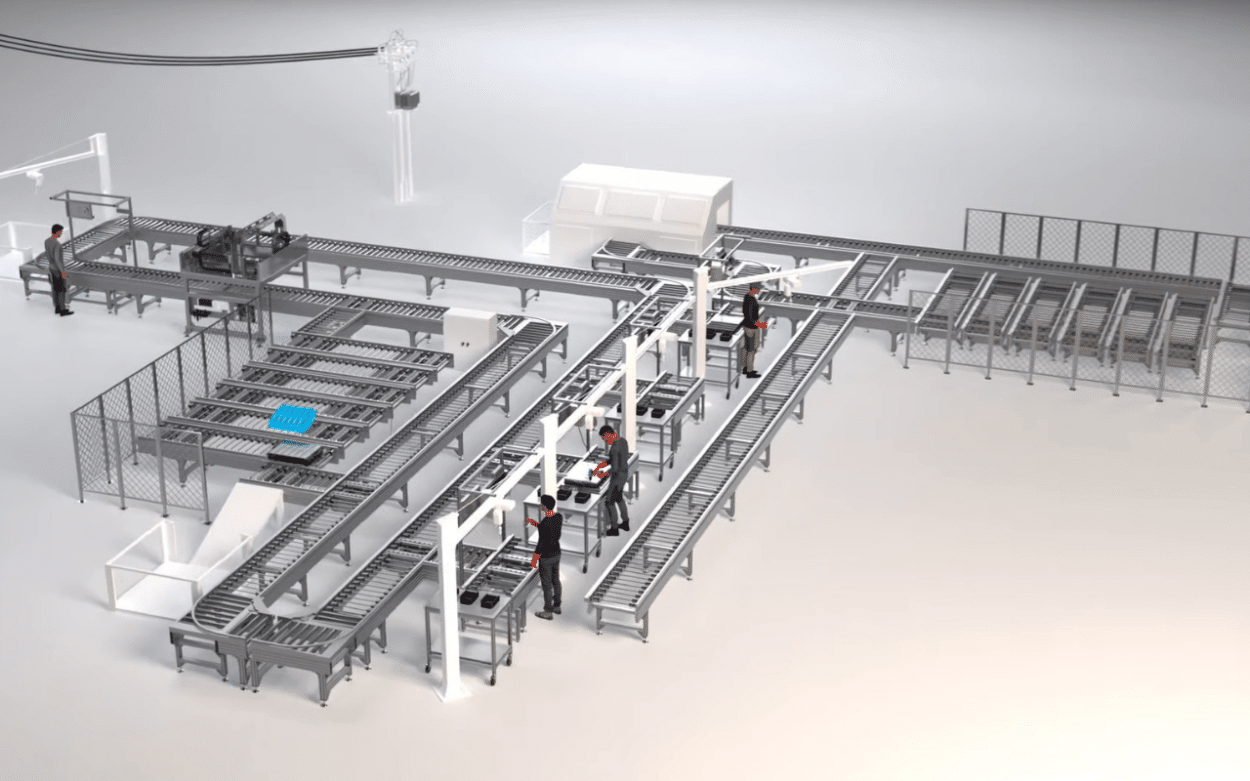
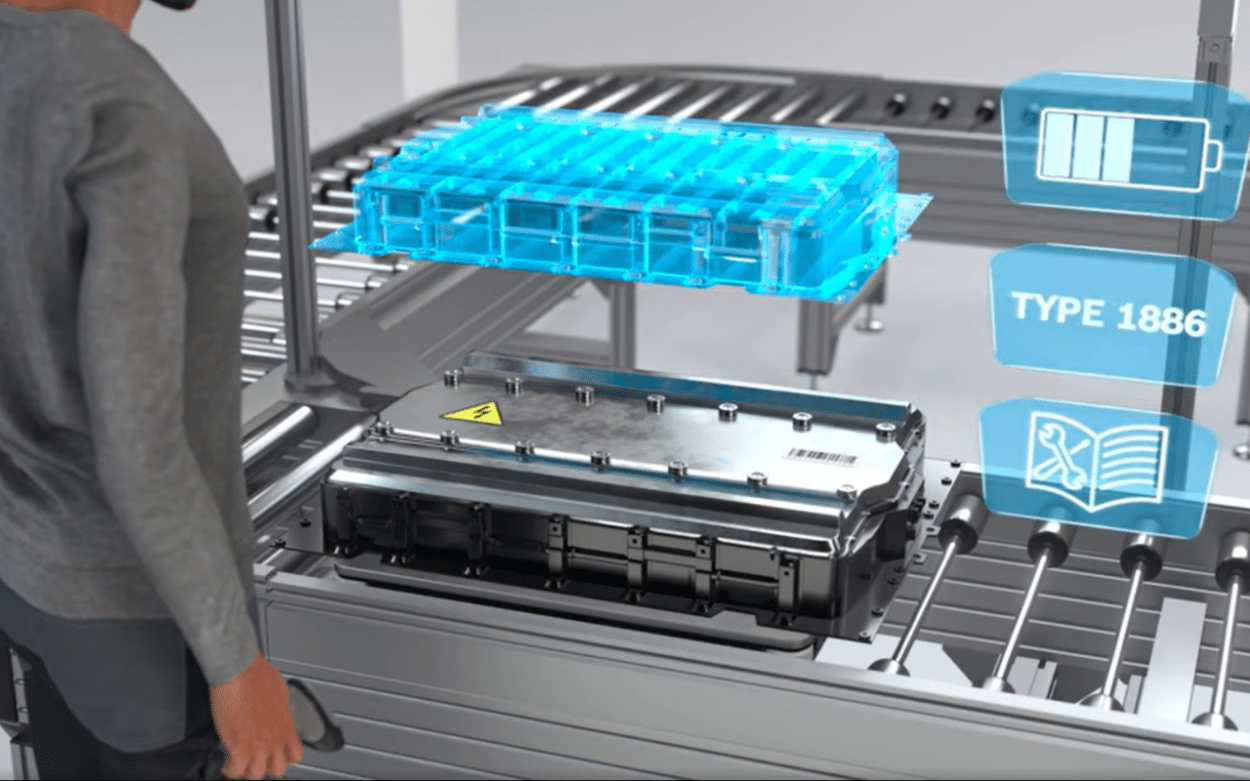
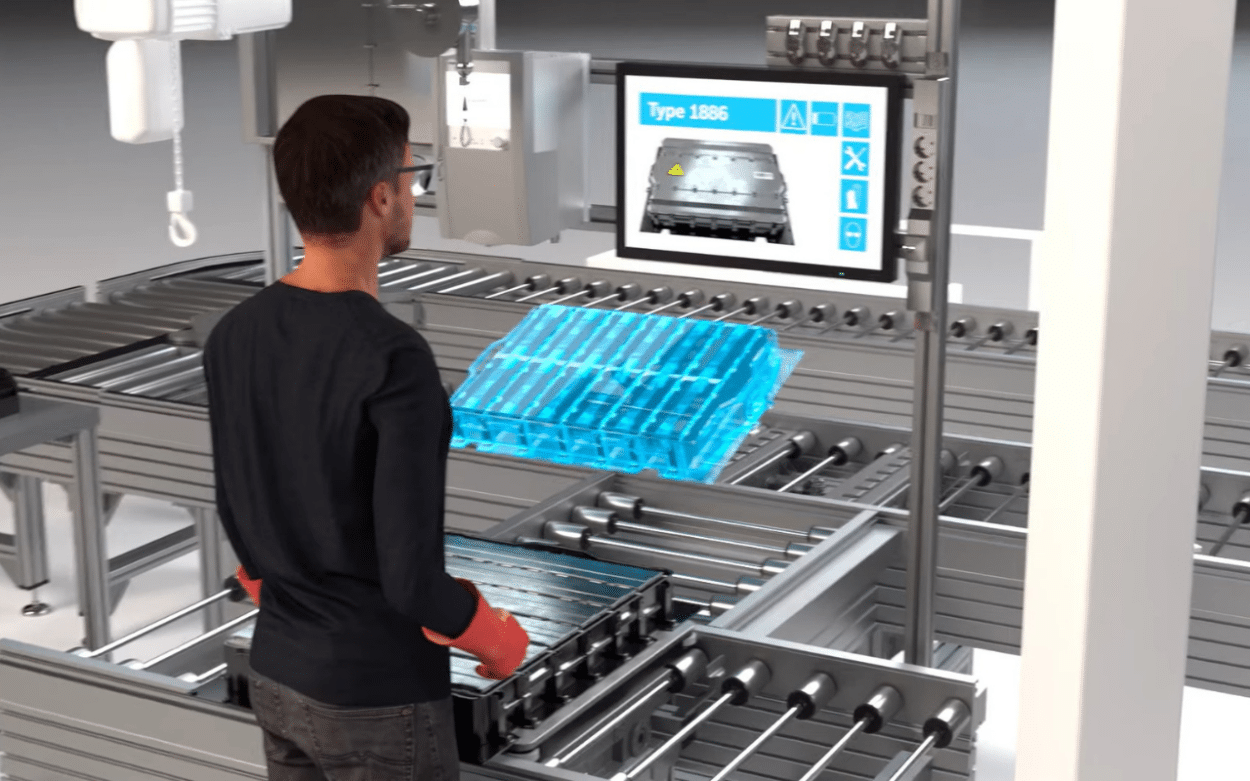

Could you elaborate on the different technological components, such as diagnostics and the discharge process?
Franck Papon: “So, when a battery arrives from a vehicle that is no longer in use or simply for recycling due to wear, this battery still has energy, so it needs to be discharged. Otherwise, if we put a charged battery into recycling, i.e., into a shredder, there is a risk of fire.
Therefore, we have developed and patented a deep discharge solution to safely de-energize batteries before recycling, minimizing the risk of fire. We first discharge the battery quickly to a certain level, and then we apply another discharge process that chemically renders the battery inert, meaning there is no longer a risk of fire. The energy is completely reduced to zero.
We then have a series of workstation arrangements to disassemble the different modules and recover valuable components such as bus bars, aluminum, connectors, and plastics. Everything recyclable must be recovered.”

How does technology assist in the disassembly process?
Franck Papon: “AI guides operators through workstations, adapting to variable battery or module types. Like the battery, the battery modules arriving at the workstation vary depending on whether it comes from a vehicle X, a certain generation, or another.
Our method involves displaying information on a screen and projecting it onto the component using a beam of light for dismantling. Validation is ensured through 3D sensors, which confirm that the operator has performed the task correctly in that specific area and has extracted the necessary element.”
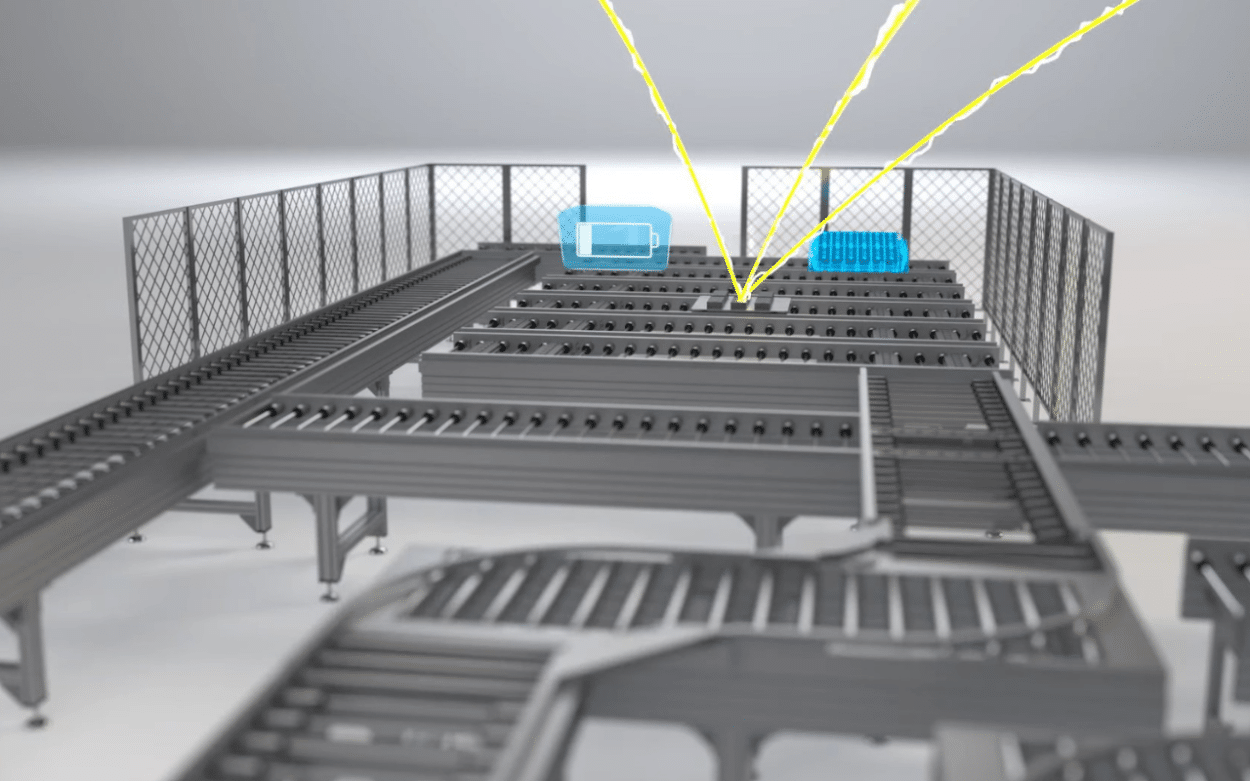

Moving on to data management, how does AI contribute to calibrating machines and overseeing the entire production line?
Franck Papon: “Artificial intelligence is designed to calibrate all machines and all stations and oversees the entire production line. Our control platform collects battery data to comply with European regulations. In Europe, each battery must have a digital passport. It is imperative. When we manufacture a battery, it will be listed. When we disassemble and recycle it, it must be listed again. This is a European regulation to ensure that we recycle the maximum number of batteries in the future. Otherwise, we won’t have enough material resources on Earth to produce new batteries.”

With the increasing need for battery recycling, how does automation play a role in this process?
Franck Papon: “Automation is essential to handle the growing volume of batteries for recycling. Tomorrow in France, we will need to recycle two thousand batteries per year. Therefore, it will be essential to automate this process because this is extremely time-consuming. Quick discharge systems, data management, and automation will save a lot of time and significantly improve efficiency, quality, and safety. Because there is a risk of fire for both the operator and the machines.”

Are there any real-world applications or successful cases?
Franck Papon: “Yes, there are successful applications in Germany, where the initial cases have been implemented and are operational.”