Industrial robotics has been a relevant component of manufacturing for a long time. Yet, the idea many people still have of production floor robots as expensive, hard-to-operate machines that come with safety risks for human workers is anchored in a past that doesn’t reflect the current state of things. But lower costs and easier programming are democratizing the implementation of industrial robots.
In the past few years, the market for industrial robots has been changing and evolving at a tremendous pace, thanks to new solutions that are faster and easier to deploy and program, even for small and mid-size companies that, just a decade ago, wouldn’t have had the capital nor the know-how even to start to think about integrating robotics into their operations.
The Democratization of Industrial Robotics
What we’re witnessing is an ongoing democratization of robotics enabled by a perfect storm of economic and technological factors, such as a lower cost of components, an effective application of artificial intelligence, a strong industry push towards standardization for robotics software and operating systems, and a strong financial incentive toward industry 4.0 and digitalization.
Programming industrial robots, once a feat reserved for a circle of highly skilled (and expensively trained) experts, has also become increasingly simple. No-code or low-code solutions have revolutionized the approach to robotics deployment, enabling many companies to automate their manufacturing processes through user-friendly visual programming solutions.
The trend goes hand in hand with the growth of the Cobots market segments. Collaborative robots are lightweight, relatively inexpensive (compared to fixed large-scale robotics solutions), easy to program, and extremely flexible, allowing a fast re-deployment to different production tasks.
Low-Code & No-Code Programming
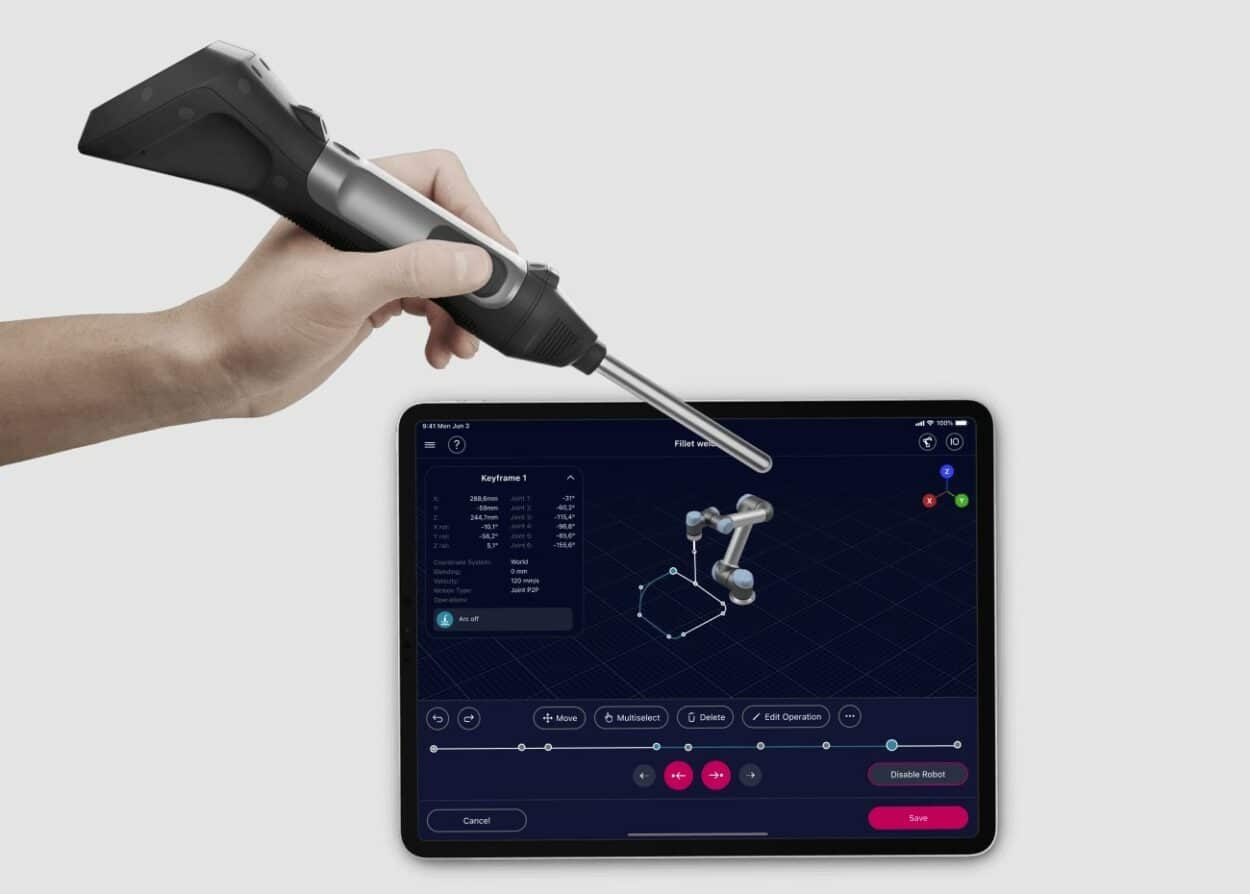
B2B startups all over Europe are taking their shots at one specific challenge of robotics: simplifying how we teach a robot how to perform a task.
German company igus, which originally specializes in motion plastic cables, has developed ReBeL, a low-cost cobot, less than 5000€, that does not need the user to have any programming skills.
For Alexander Mühlens, Head of the business unit of low-cost automation
“We do the programming for you. It is included in the price. If you did not know anything about robots or coding so far, you can ask us and we will build an automation solution for you.”
French startup Fuzzy Logic has created Fuzzy Studio, a no-code platform for robot programming that helps the user generate automation routines through a 3D simulation of the robots in their operative environment.
Dresden-based Wandelbots’ Teaching App offers a unified interface to program robots through a “pen”, a connected device that the human worker can use to design paths and actions that robotic arms will then be able to replicate with precision.
Bigger names in robotics haven’t just been watching and are working hard to capitalize on the new trends. Germany’s ABB Robotics, for example, strongly believes that no-code or low-code solutions will grow quickly in the next few years. Its Wizard platforms enable visual-based programming that’s both easy to learn and empowers a coexistence between expert programmers and newcomers. With Wizard, expert programmers can create their coding blocks and provide them as an easy-to-use component, accessible for everyone else to deploy.
According to Katja Butterweck, Global Product Specialist & Incubator Manager, Collaborative Robots at ABB Robotics:
“Ease of use is a big trend in robotics, and low-code or no-code programming is a fast-growing part of the market. It all started with cobots, but we see big demand for the application of these solutions to larger industrial robots. More and more companies want to get started with robotics and, thus, create or modify programs easily. We’ve seen that hands-on programming can work smoothly with other standard programming methods”.
While the current trend goes toward simplifying robotics deployment, there’s already who’s thinking about what will come next regarding robots’ intelligence and learning ability.
Smart Robots
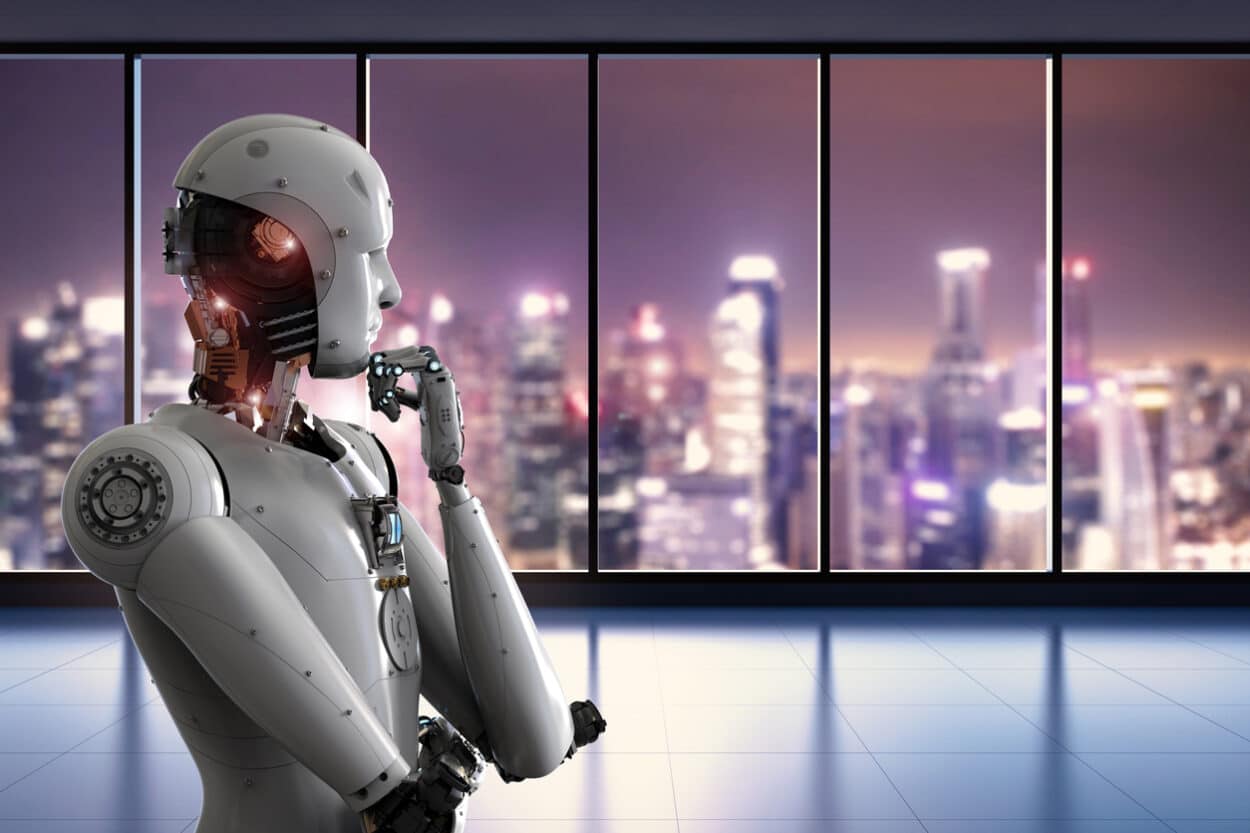
The French startup Conscience Robotics, among others, has undertaken the ambitious goal of developing a universal operating system called Conscience OS to bring generalized intelligence to all sorts of robots by leveraging a self-awareness of the machine’s components and abilities.
As explained by Conscience founder Iliès Zaoui in the company’s marketing materials:
“With our software, the robot becomes aware of its physical capacities and takes advantage of it autonomously. It becomes able to move in its environment in an autonomous and optimized way. In addition, the robot can detect objects in its environment (naval, air, or land) and interact with them to grab, move, activate a switch, or even monitor a place. The end user interacts with its robot, nearby or remotely, through a simple and intuitive mobile or web application. Robots using our system are connected and share the experience they have learned. Thus, the latter evolve autonomously and exponentially over time.”
These developments inevitably beget the question of the future role of the human workforce in an industry where automation is close to becoming commoditized.
Doomsday predictions aside, the current market reality is that a big driver for the democratization of robotics is somehow an answer to the opposite problem—the lack of enough skilled human workers.
According to a Deloitte study, from now to 2028, about 2.4 million job positions in manufacturing are poised to be left unfulfilled:
“The Fourth Industrial Revolution is transforming the world of work through artificial intelligence, advanced robotics, automation, analytics, and the Internet of Things. Despite common fears, these technologies will likely create more jobs than they replace—as illustrated by the tight labor conditions in the US and global manufacturing industry”.
NEED HELP? READ OUR BUYING GUIDES
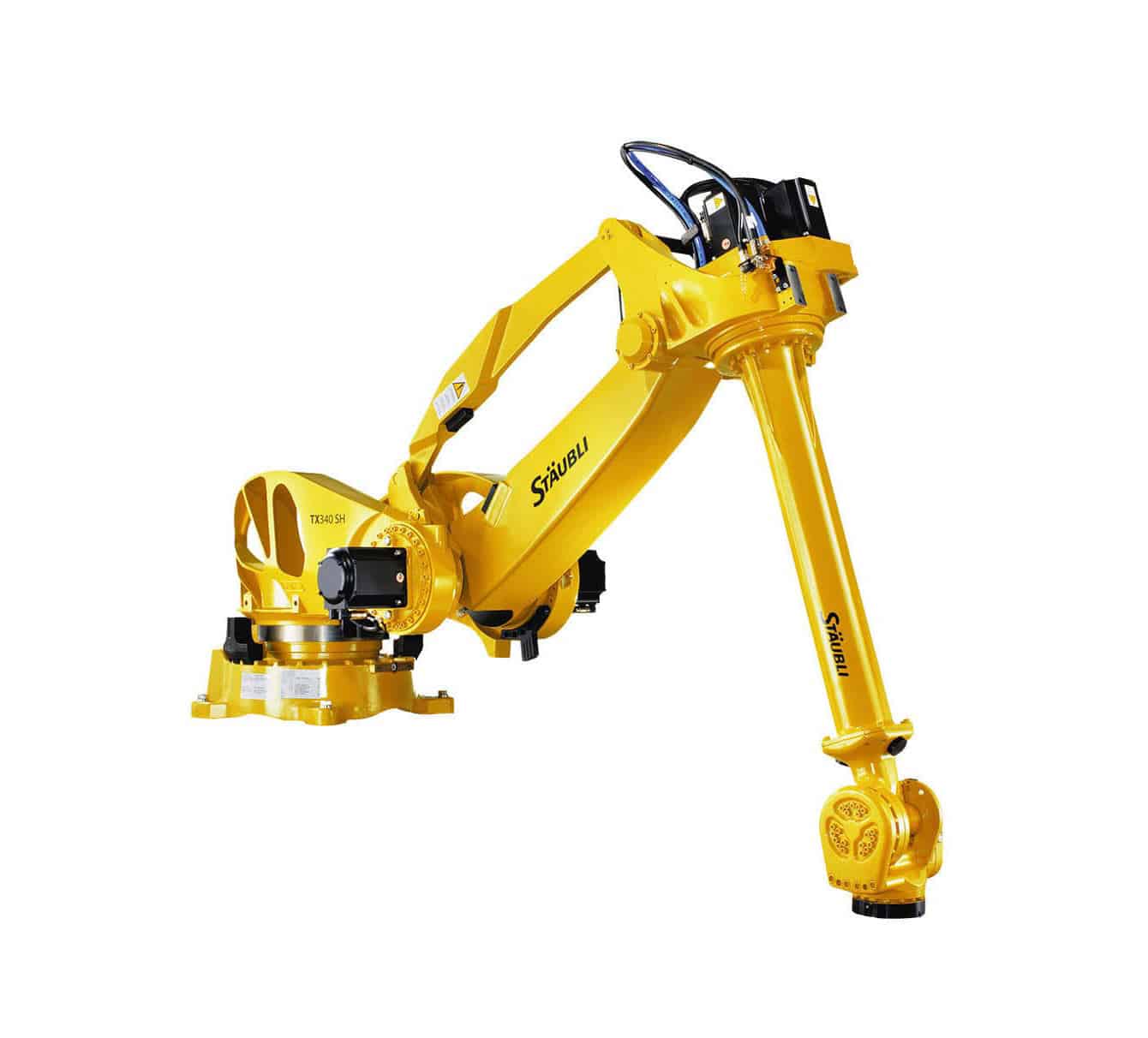
How to Choose an Industrial Robot?
Read our buying guide and make the smart choice.
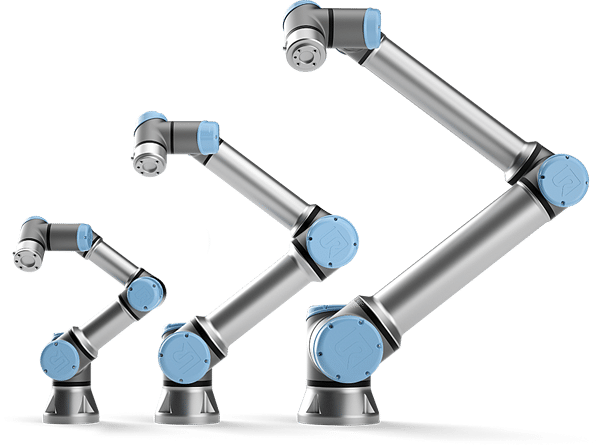
How to Choose the Right Cobot?
Read our buying guide and make the smart choice.