Speeding up visual inspection times while slashing defect escape rates, AI-powered quality control is helping manufacturers reduce losses while protecting public safety.
The cost of defects in wastage and recalls can take a significant financial toll on manufacturers. Defects cost manufacturers around 20% of their overall sales revenue on average, according to the American Society of Quality (ASQ).
The Cost of Defects
Manufacturing defects which escape detection can also have a significant impact on public safety and the manufacturer’s reputation. This is particularly true when it comes to the batteries used in electric vehicles and solar energy storage.
Since February 2020, General Motors, Mercedes-Benz, Hyundai, Stellantis, and Volkswagen have issued recalls related to the fire risk of batteries. These were manufactured by South Korea’s LG Energy Solution.
General Motors’ US$1.9 billion recall of its 2019-2022 Chevrolet Bolts was attributed to two LG battery manufacturing defects, a torn anode tab and folded separator, which together could lead to EV fires.
READ ALSO
UnitX Labs
California’s UnitX Labs is using AI to help battery manufacturers accelerate the defect identification process and slash inspection times. They do so by training AI models to recognize abnormalities.
Established by a team of engineers from Stanford, MIT and Google, UnitX primarily offers AI-powered inspection systems for battery and automotive manufacturers. It is also working with the consumer electronics, medical, semiconductor and printed circuit board assembly industries.
Along with visible light, UnitX’s inspection systems can integrate with ultraviolet, infrared, X-ray and CT sensors for more in depth scans.
The use of AI for visual inspections reduces the escape rate of undetected defects by 10 times compared to human operators. UnitX co-founder and CEO Keven Wang also says that their system halves false rejection rates. In a recent case study, UnitX’s AI scanned one battery cell every 3.5 seconds, compared to the five minutes required by human operators.
“Humans are not always the best when it comes to repetitive tasks like quality control,” Wang says. “Visual inspections are an incredibly boring, mundane and repetitive job for people, plus they are very taxing on the eyes. People are still faster at using prior learning to recognize new types of defects, for example you don’t need to define for them what ‘scratch’ looks like, but the technology is getting better at this thanks to advancements in AI and Large Language Models.”
UnitX’s Cortex technology only requires five examples of a defect in order to detect it with a high level of accuracy, which ensures that site acceptance testing typically only takes one week.
Software-defined lighting allows dynamic control over lighting patterns and angles to support quickly examining different kinds of surfaces, in search of subtle defects such as scratches and chips.
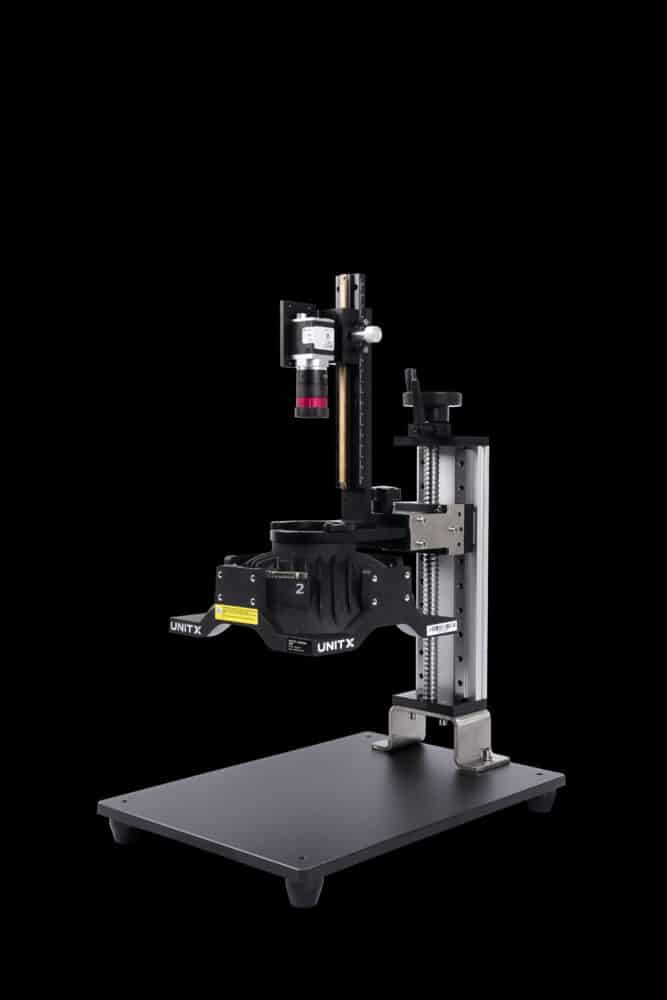
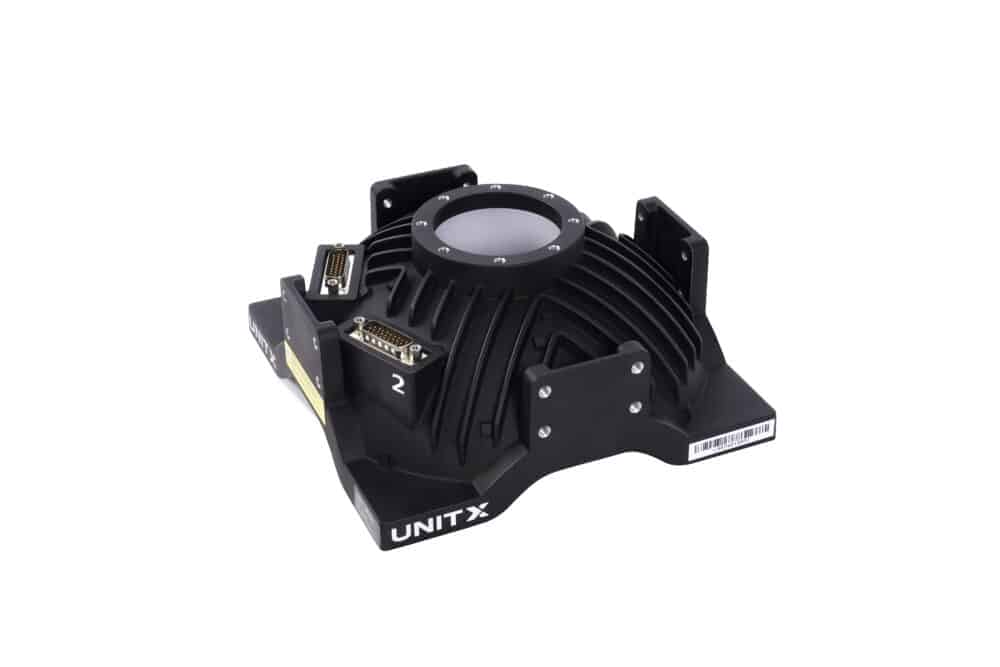
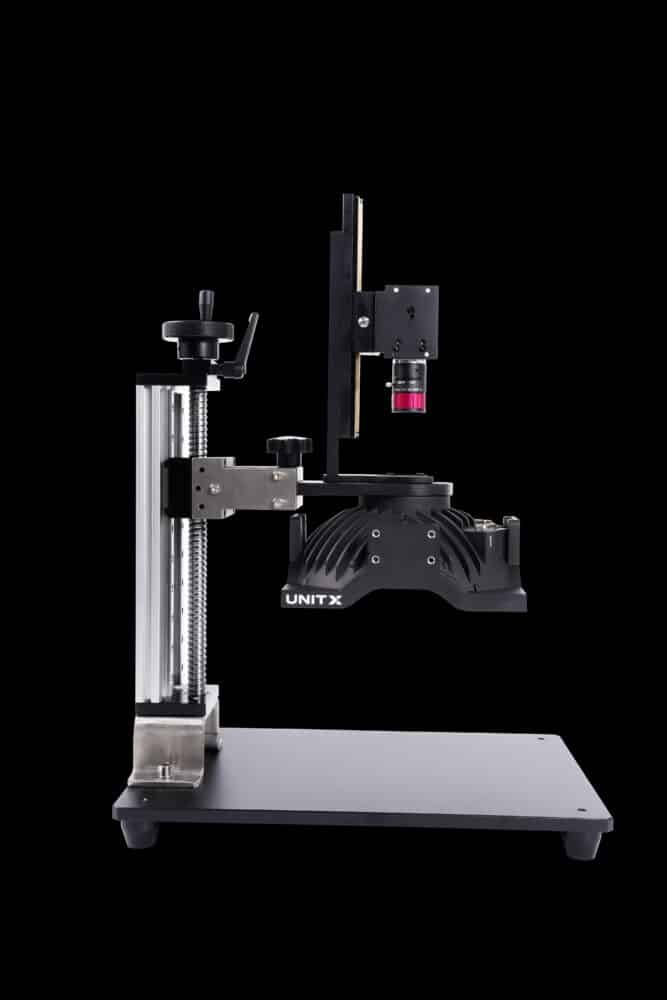
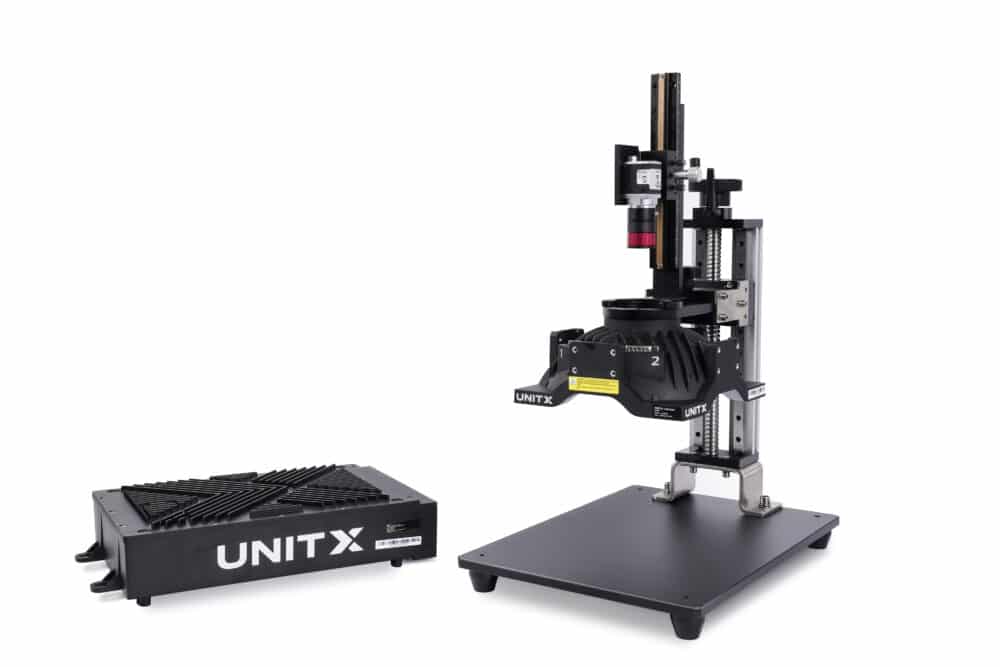
VisionAI by Rockwell Automation
Rockwell Automation introduced VisionAI, an AI-driven quality inspection platform, at the Automation Fair in November 2024, which DirectIndustry attended (read our story).
Designed to enhance manufacturing quality control, VisionAI enables real-time, precise assessments of products on production lines. It can simultaneously evaluate multiple product aspects—such as detecting bottle damage, cap defects, labeling issues, and leakage—allowing manufacturers to swiftly identify and address defects.
Integrating seamlessly with Rockwell’s existing automation systems, VisionAI feeds inspection results into programmable logic controllers (PLCs), facilitating automated actions like stopping conveyors, rejecting defective items, or alerting operators. This integration empowers manufacturers to implement automated responses based on inspection outcomes, enhancing overall efficiency.
A notable feature of VisionAI, according to Amanda Thompson, Product Manager at FactoryTalk’s Vision AI is its user-friendly, no-code interface
“There’s no special data science or machine vision expertise required to use vision AI.”
Operators and quality teams can create and train inspection models without specialized expertise.
Users simply label images of products as good or defective, enabling on-site personnel to build, train, and deploy models without the need for data science skills. Once operational, VisionAI provides a comprehensive dashboard offering insights such as defect rates, common issues, and real-time statistics.
VisionAI’s architecture combines cloud-based AI model training with edge computing for on-site analysis, ensuring minimal latency and real-time performance. This setup also supports remote access:
“Even if I’m at home in Pennsylvania and hear about a quality issue at my plant in Anaheim, California, I can log in and access the same user interface remotely. This allows me to see what’s happening and assist the local team in resolving quality issues. It reduces travel costs and increases flexibility.”
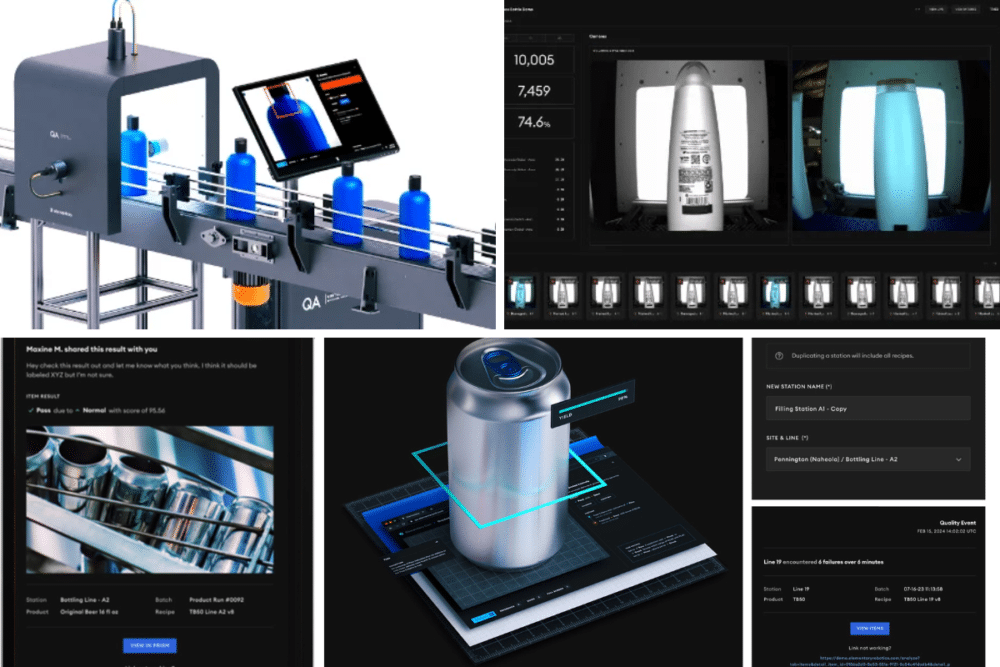
The AI Vision Inspection Market
Further afield, the AI Vision Inspection market is projected to grow from US$31.63 billion in 2025 to US$196.53 billion by 2034, according to Market Research Future.
Beyond quantity control, vision inspection applications include identification, appearance, measurement, positioning/alignment and verification.
Technology hardware giants like Intel, NVIDIA and Qualcomm have made key investments in AI vision inspection, as have cloud computing behemoths like Google, Amazon and Microsoft. Key players also include automation and logistics specialists like FANUC, OMRON, Teledyne, Rockwell, Antares Vision and OPTEL Vision.
Results from the AI vision inspection process can be fed into programmable logic controllers, which enables automated responses such as halting conveyors, rejecting faulty products and alerting operators when issues are detected.
Future advancements will include improving the ability of AI to leverage prior learning to quickly switch between inspecting different objects without the need to be fully retrained.
In the long run, UnitX’s Wang says AI visual inspections can deliver a lot more value than simply catching manufacturing defects before they leave the factory.
“AI inspection is not just about cost reduction, it can also be leveraged as a feedback tool for monitoring processes and preventing defects rather than just acting as a final gatekeeper,” he says. “The rich data from AI inspections can provide valuable insights into upstreaming processes, helping to improve quality and allow manufacturers to stay on the cutting edge compared to their competitors.”