At Automation Fair last month, Rockwell Automation showcased its latest innovation, VisionAI, a quality inspection platform designed to transform how manufacturers evaluate and manage product quality. DirectIndustry examines the benefits of this new tool, which is set to revolutionize quality control through a combination of AI and computer vision, all supported by an edge computing architecture.
First introduced in September 2024, VisionAI made its debut at the Automation Fair in November, showcasing its cutting-edge capabilities in streamlining quality control processes across industries.
Revolutionizing Quality Control
VisionAI leverages artificial intelligence to empower manufacturers with precise, real-time insights into product quality. For Amanda Thompson, Product Manager at FactoryTalk’s Vision AI
“It’s really designed to help our customers understand the quality of the products moving down their production line. This enables them to make informed decisions about handling both good and defective products.”
She also highlights the platform’s ability to evaluate multiple aspects of a product simultaneously. For example, in a live demonstration using shampoo bottles, Vision AI assessed various parameters such as bottle damage, cap defects, labeling issues, and leakage. By identifying defective products and pinpointing the reasons for their failure, manufacturers can quickly address issues and optimize their production processes.
Integrated With Rockwell’s Portfolio
The platform’s integration with Rockwell Automation’s broader portfolio further enhances its functionality. Results from the inspection process are seamlessly fed into programmable logic controllers (PLCs). It enables automated responses such as halting conveyors, rejecting faulty products, or alerting operators.
“We want to give our customers the power to take automated action based on the results of their quality inspections. What they choose to do is entirely up to them. But we’re empowering them to take the results of the quality inspection, integrate them into their automation system, and implement automated actions accordingly.”
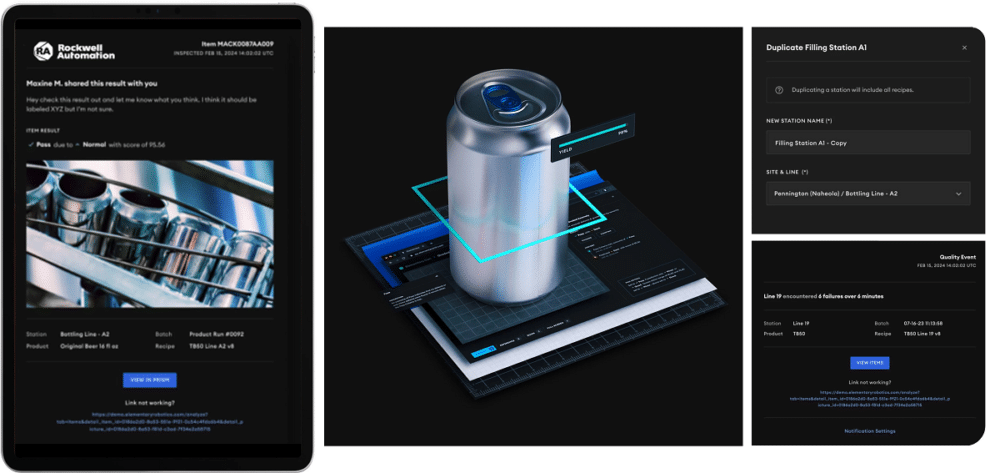
Simplifying AI for the Plant Floor
VisionAI’s standout feature is its accessibility. Unlike traditional machine vision systems that require specialized expertise, Vision AI allows operators and quality teams to create inspection models with minimal training.
“There’s no special data science or machine vision expertise required to use vision AI.”
Users simply label images of their products as good or bad, detailing any defects. This intuitive workflow democratizes AI, enabling on-site personnel to build, train, and deploy models without needing data science skills.
Once operational, VisionAI provides a comprehensive dashboard offering insights such as defect rates, common issues, and real-time statistics. Users can drill down into specific defects, viewing failed items and pinpointing problem areas through an innovative insights feature. This enables rapid troubleshooting and informed decision-making to enhance overall product quality.
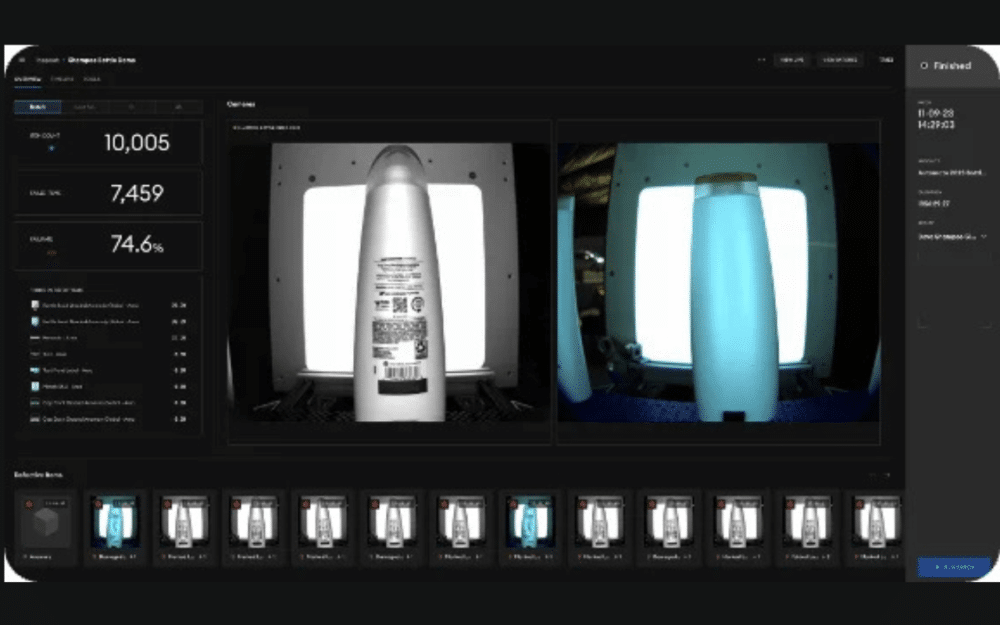
Innovative Edge-to-Cloud Architecture
VisionAI also boasts an advanced edge-to-cloud architecture. While machine vision models are built in the cloud for high accuracy, they are deployed to edge computers on the plant floor. This ensures local analysis and minimal latency.
This architecture also supports remote accessibility, details Thompson,
“Even if I’m at home in Pennsylvania and hear about a quality issue at my plant in Anaheim, California, I can log in and access the same user interface remotely. This allows me to see what’s happening and assist the local team in resolving quality issues.’
This also allows quality experts in different locations to monitor systems, label images, and update models without being physically present.
“It reduces travel costs and increases flexibility,” Thompson emphasized, noting the platform’s potential to connect teams across the globe.”
VisualAI is currently available in North America and is set to launch globally in 2025.