At JIMTOF 2024, Japanese manufacturing leader AMADA showcased three groundbreaking machines that redefine capabilities in laser cutting, welding, and manufacturing automation. Our industry analyst Hicham Dhouibi took a tour of the Regius 3015 AJ fiber laser cutting machine, the Alcis 1008 multipurpose laser machine, and the FLW 6000 ENSIS laser welding machine.
At JIMTOF last week, AMADA showcased their three latest machines—the Regius 3015 AJ, Alcis 1008, and FLW 6000 ENSIS. These machines, which combine powerful laser technology, IoT connectivity, and AI-driven processes cater to diverse applications including, for example, the booming EV market.
1/ The Regius 3015 AJ Fiber Laser Cutting Machine
The Regius 3015 AJ represents AMADA’s cutting-edge technology in high-power fiber laser cutting and targets the sheet metal industry. Designed with a 26-kilowatt fiber laser, it offers a combination of speed and accuracy, outpacing many conventional laser cutters.
Built for maximum efficiency, this machine not only cuts a wider range of materials but also minimizes downtime and maintenance requirements, making it a valuable asset for industries requiring high precision.
Key Features and Innovations:
- Laser Power: The Regius 3015 AJ boasts an upgraded 26-kilowatt fiber laser, allowing it to cut up to 50 millimeters of mild steel, aluminum, brass, and copper. This is a significant leap from conventional machines, which generally max out at 25 millimeters.
- Automatic Nozzle Adjustment: The machine uses an advanced automated nozzle system to optimize settings for different material types and thicknesses. It aligns and adjusts the nozzle automatically, enhancing speed, accuracy, and safety, as no manual intervention is needed.
- Predictive Maintenance with IoT: Equipped with IoT-enabled sensors, the Regius 3015 AJ can track critical metrics like cooling flow rate and nozzle wear, notifying AMADA’s service center of potential maintenance needs before they become issues.
- AI-Driven Path Optimization: The machine utilizes AI to determine the most efficient cutting path, reducing cutting time and maximizing productivity. AMADA’s proprietary software programs also optimize the entire process, from cutting to bending and welding.
- Energy Efficiency: AMADA’s fiber laser technology cuts faster and consumes less power than traditional CO₂ lasers. While higher laser power might imply greater consumption, the Regius 3015 AJ’s faster throughput means it operates for shorter periods, resulting in a lower overall energy footprint.
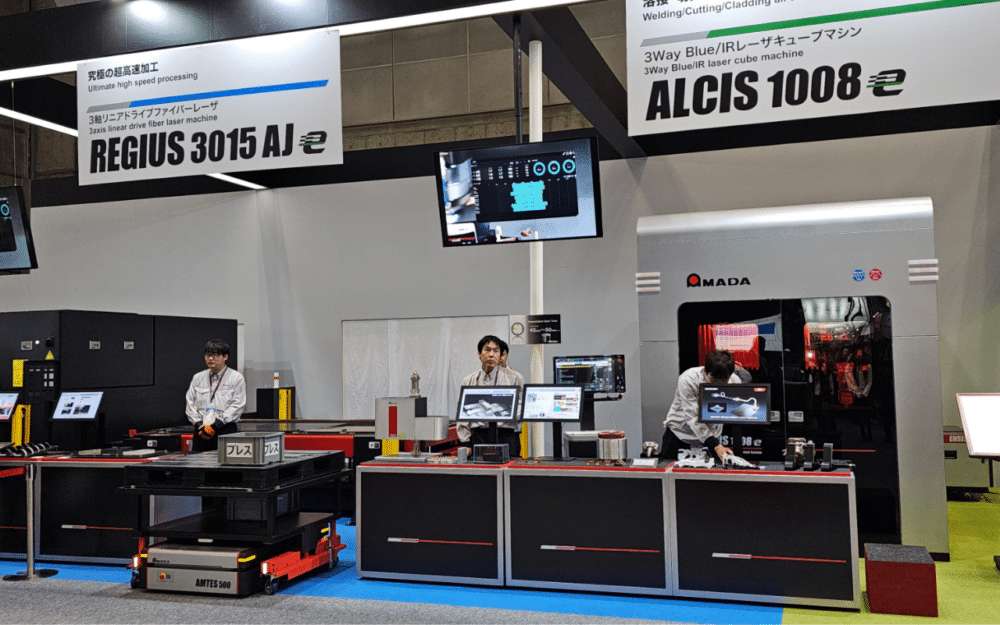
2/ The Alcis 1008 Multipurpose Laser Machine
The Alcis 1008 is a versatile powerhouse, integrating cutting, welding, and additive manufacturing into one machine. This multi-functionality makes it ideal for industries requiring flexibility in material processing, especially as electric vehicles and advanced manufacturing demand more specialized solutions.
Key Features and Innovations:
- Dual-Laser System: The Alcis 1008 comes equipped with both blue and infrared (IR) lasers. The blue laser is particularly effective for welding copper, a critical component in electric vehicle motors and other electronic applications, while the IR laser handles materials like steel and stainless steel.
- Additive Manufacturing Capabilities: The Alcis 1008 can add material to existing parts, allowing manufacturers to repair or enhance components rather than replace them entirely. This feature, referred to as “additive manufacturing,” can extend the lifespan of tools by repairing damaged surfaces.
- Automatic Laser Switching: The machine can seamlessly switch between the blue and IR lasers, allowing for multi-material processing without manual intervention. This efficiency supports high throughput, especially for industries dealing with multiple metal types.
Market Availability: Currently available only in Japan, AMADA has plans to expand its market reach based on customer demand, particularly as the electric vehicle market and related sectors grow globally.
3/ FLW 6000 ENSIS Laser Welding Machine
The FLW 6000 ENSIS laser welding machine offers a comprehensive solution for sheet metal processing, integrating cutting, bending, and welding functionalities with state-of-the-art automation. This machine is ideal for manufacturers seeking a fully automated production process, especially in industries where accuracy, speed, and flexibility are paramount.
Key Features and Innovations:
- Advanced Automation for Welding: Traditionally, laser welding requires operators to program robotic positions, a time-intensive process known as “teaching.” The FLW 6000 ENSIS automates this, using AI to adjust each part’s position for optimal welding alignment, which reduces the need for human intervention.
- AI-Based Real-Time Adjustments: The machine is equipped with sensors and AI-driven algorithms that monitor each part’s position, automatically making fine adjustments as needed. This feature is particularly beneficial for complex assemblies, where exact positioning is crucial.
- Integrated Software for Total Process Control: The FLW 6000 ENSIS connects with AMADA’s software to coordinate the entire sheet metal production cycle—from cutting to bending and welding. This integration ensures a seamless transition between manufacturing stages, improving overall efficiency and productivity.
Target Market and Applications: This welding machine is designed for industries requiring precise sheet metal welding, such as automotive, aerospace, and heavy machinery. It streamlines production, minimizes errors, and supports high throughput in complex assembly processes.
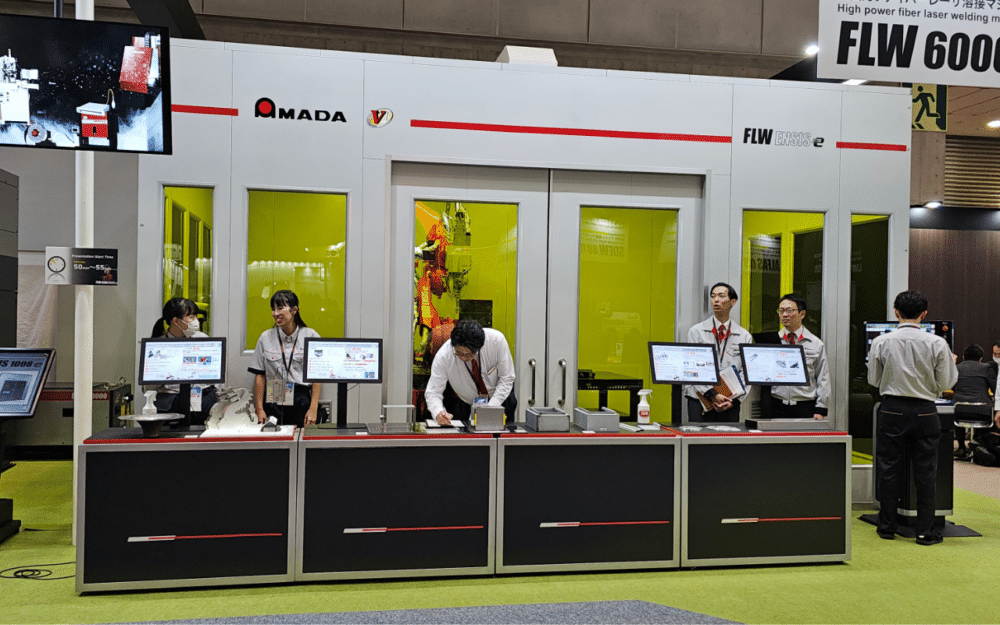
Total Solution Approach with AMADA’s Autonomous Mobile Robot (AMR)
AMADA’s machines are complemented by its newly developed AMR designed specifically to transport sheet metal parts within manufacturing facilities.
In an interview with DirectIndustry, Kazuhiro Kishimoto, Executive General Manager Innovation Center at AMADA said,
“Our focus is on providing a complete, integrated solution—from cutting all the way through to transporting finished goods. Many large companies require this kind of total solution, and it’s something our clients have specifically requested. Our AMR (Autonomous Mobile Robot) was recently launched in Japan, tailored specifically to serve the needs of sheet metal companies by efficiently transporting sheet metal materials within their facilities.
The AMR integrates with AMADA’s software and machine network, autonomously moving materials from one stage of production to the next:
“ It monitors when parts are ready and autonomously moves to retrieve them, transporting parts to the next stage of production—whether that’s bending, welding, or another process. With this full software linkage, the entire production process flows smoothly and efficiently, with minimal manual intervention.”
This robot is a significant asset for manufacturers seeking a fully automated, end-to-end solution. The AMR is currently available as a standalone solution, but only in Japan.
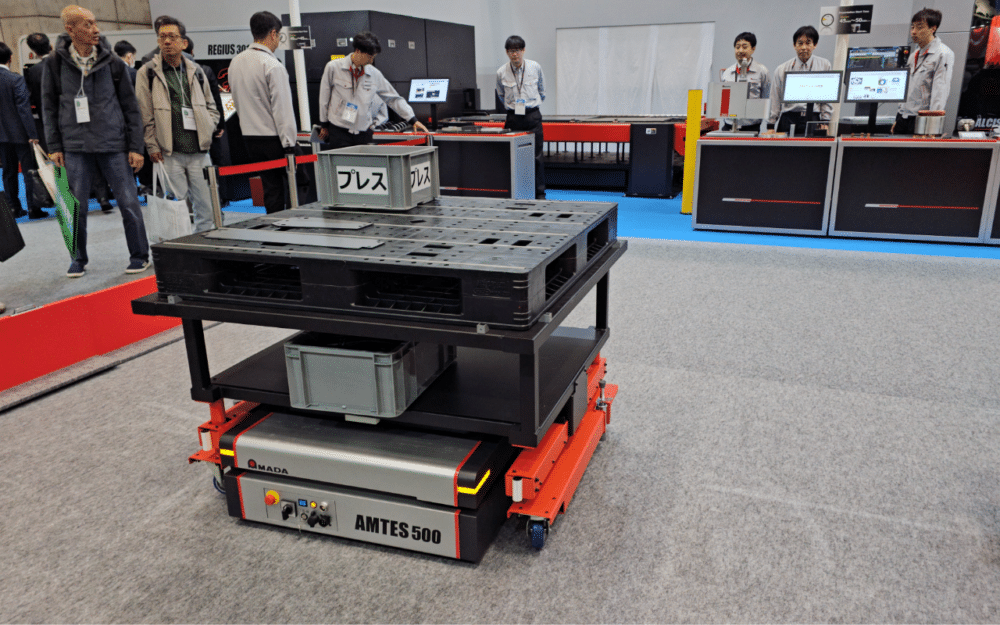