Toyota Material Handling, an official partner of the Paris 2024 Olympic and Paralympic Games, is responsible for the mobility of goods, sports equipment, and athletes’ gear, as well as the construction and dismantling of stadiums and the catering for stadiums and the Athletes’ Village. To achieve this, the Japanese company has deployed zero-emission pallet trucks and forklifts and adapted them to the outdoor environments of these city-centered Games. DirectIndustry visited the Toyota House, located at the foot of the Eiffel Tower Beach Volleyball stadium, to discover this unusual setup featuring equipment typically used in closed warehouses.
The Paris 2024 Olympics encompass 41 competition sites in the Paris region and across France, expecting 10,500 athletes and 16 million visitors. This edition is also one of the first to take place in exceptional outdoor and urban conditions, not just in stadiums. This presents a significant logistical challenge, explains Benoît Meunier, Manager of Product Management in France for Toyota Material Handling (TMH). The teams need to handle over 170,000 pallets of goods during these Games to ensure smooth and timely delivery.
“The Olympics are not normal operations for forklifts. Here we are outdoors, in the heart of Paris, in open environments and not just in enclosed stadiums. We are working with forklifts that are usually meant for warehouses. Using them in these exceptional circumstances shows the flexibility of our solutions. It’s a showcase for us, demonstrating that our equipment can be effective in specific conditions.”
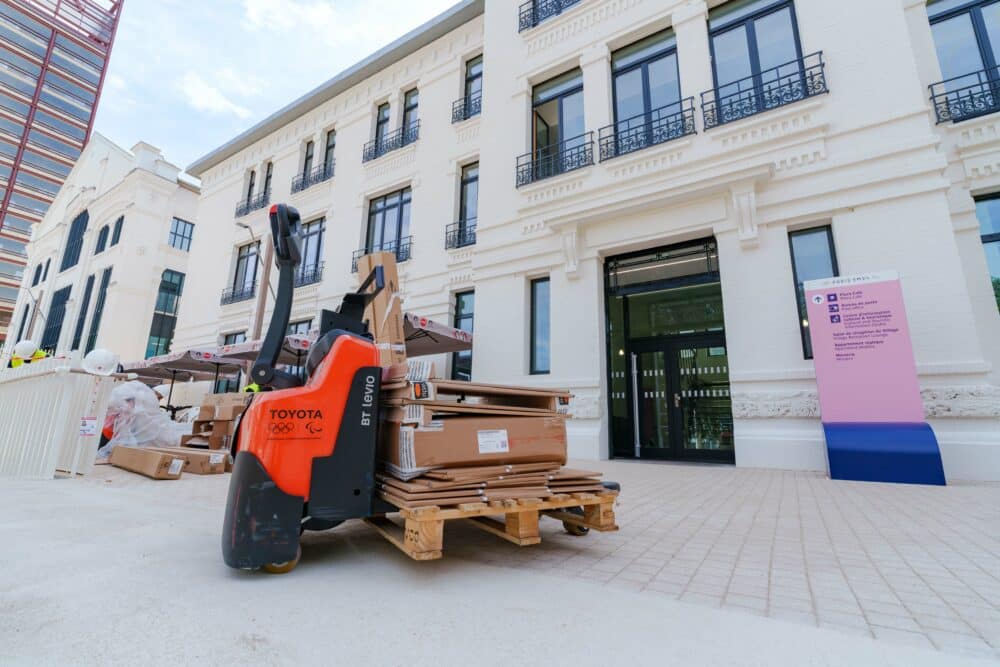
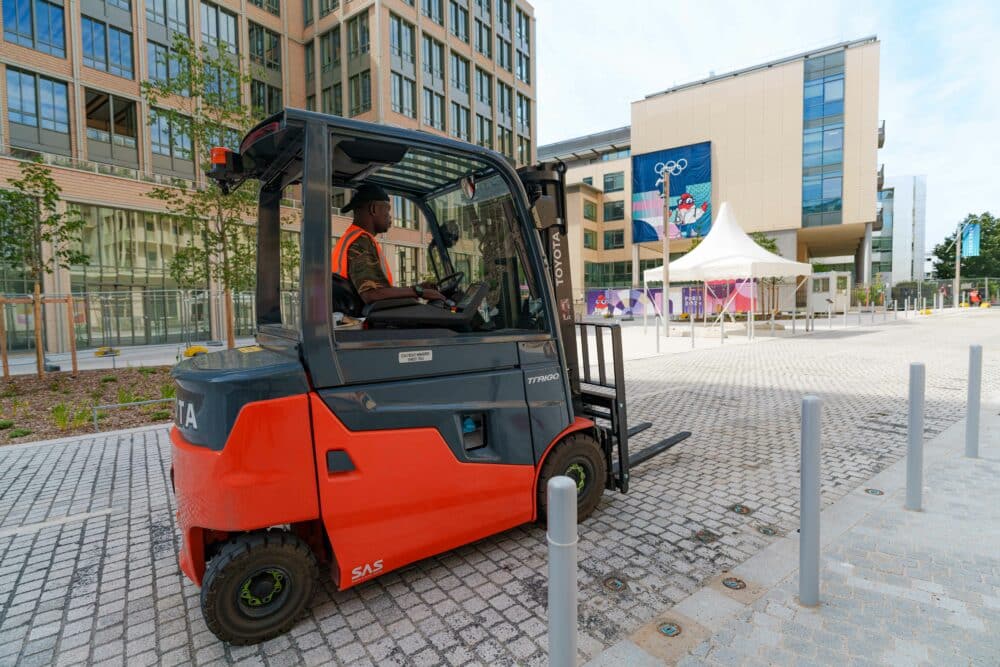
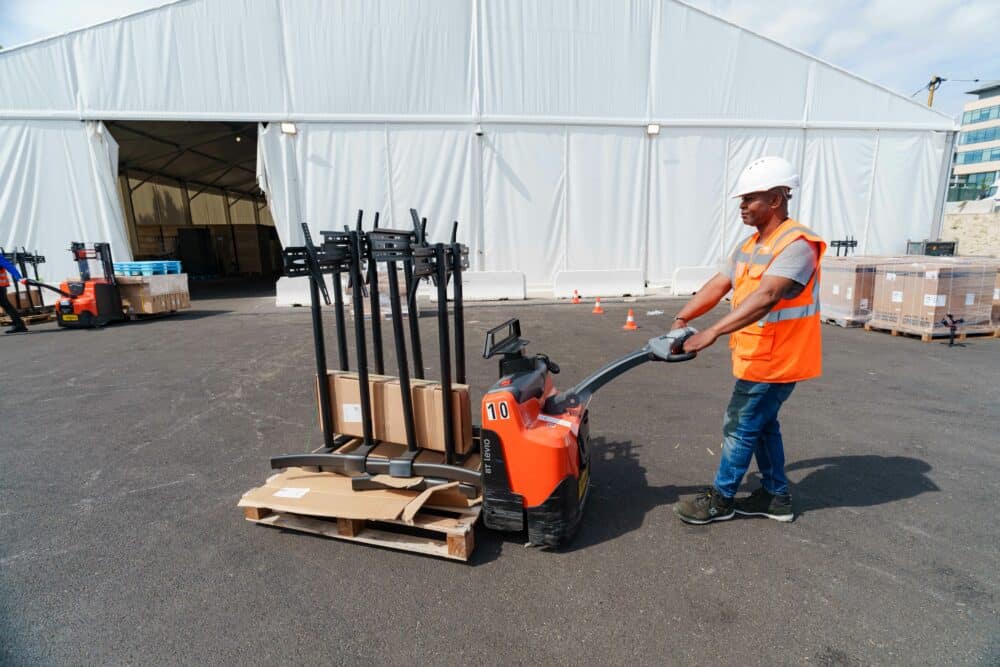
Two Models
To achieve this, TMH deployed two models of handling equipment: Levio LWI 1.6t electric pallet trucks and Traigo 80 counterbalance forklifts. In line with the Olympics’ goal to reduce its carbon footprint by 50% compared to the London Olympics, TMH only used zero-emission electric equipment equipped with lithium batteries and hydrogen fuel cells.
The organizers deployed a total of 250 machines for the Olympics to supply stadium stands with food and beverages, construct the stadiums, move and assemble basketball panels and seating, and handle all traditional logistics, including food for the Olympic Village. They will also use these machines for dismantling after the Games.
Levio LWI 1.6t Electric Pallet Trucks with Lithium Batteries
The Levio LWI 1.6t electric pallet trucks have a load capacity of up to 1600 kg. The Click-2-Creep feature allows operators to use the tiller in a vertical position for better maneuverability.
TMH designed and assembled the trucks with lithium batteries, which provide energy savings, as Benoît explains:
“Sustainability is part of the Olympics’ requirements. With our batteries, we achieve 30% less electricity consumption compared to a machine equipped with a lead battery. The compact lithium technology allows us to make very compact machines, enhancing operator safety.”
More compact machines can access tight or difficult-to-reach areas, providing operators with a clear view of the forks for more comfortable working conditions.
According to Eric Loustau, General Manager of TMH France, lithium batteries offer great flexibility to users. Unlike lead batteries, which require a full discharge before recharging, you can charge lithium batteries at any time without causing damage. A 30-minute charge can replenish the battery to 50% capacity.
“During a work cycle, a logistics worker can plug in their forklift for a short time while doing another task and then resume use without affecting battery life or power. Besides, lithium batteries last 5 to 7 years, compared to 3 to 4 years for lead batteries.”
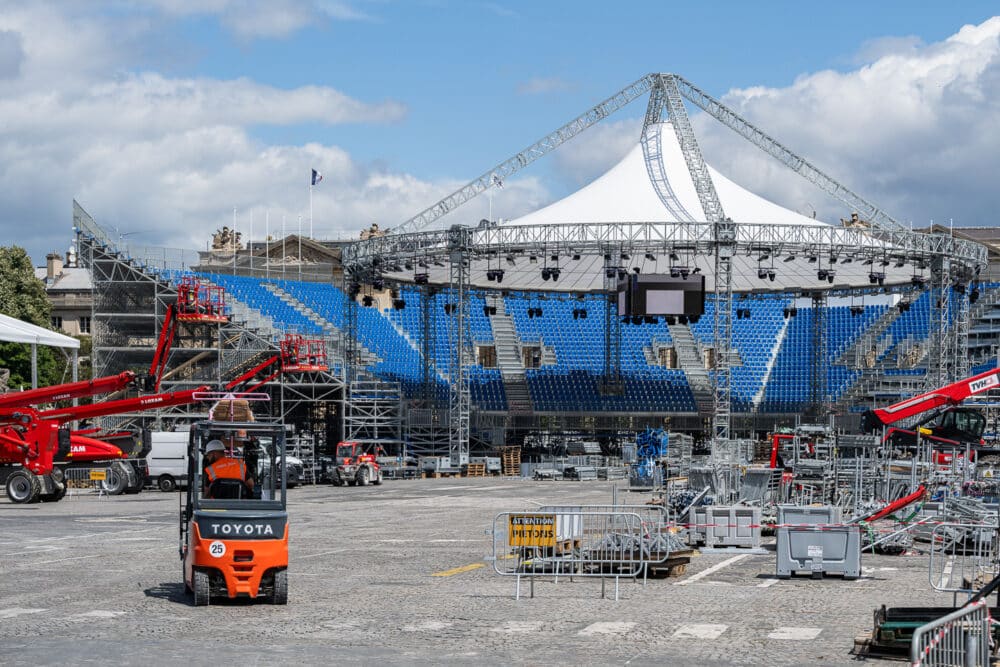
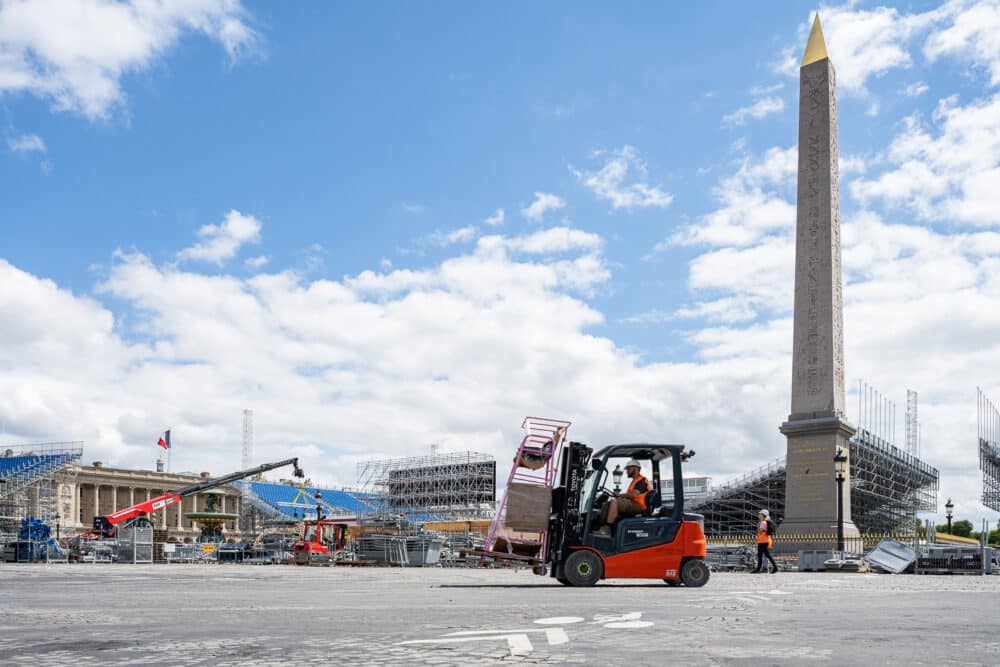
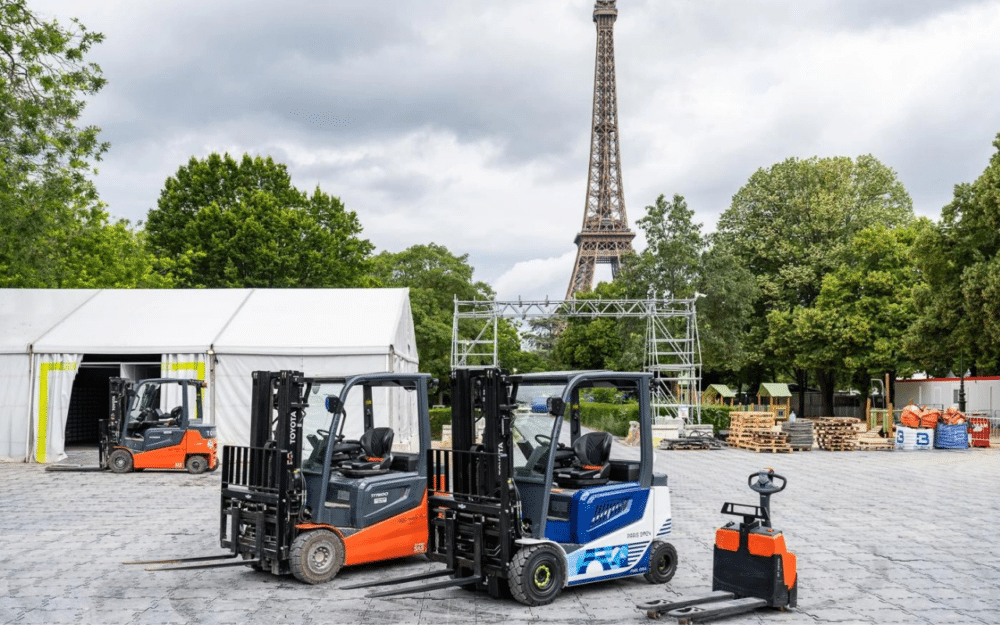
According to Benoît Meunier, another advantage of lithium is the intelligent chargers equipped with Dynamic Power Limitation. These chargers better manage electrical consumption, especially when multiple forklifts charge simultaneously.
“Our lithium chargers communicate with each other to assess the charge levels of machines and distribute energy appropriately. If a battery is nearly full, the charger will not charge quickly. However, if it is empty, it will charge at full power to recharge faster and avoid significant current spikes on electrical lines. Chargers need to communicate if you charge all your forklifts at the same time.”
By optimizing the charging times of an entire fleet, TMH promises greater energy efficiency for the entire charging process.
Traigo 80 2.5t Counterbalance Forklifts
The second type of handling equipment deployed for the Olympics is the Traigo 80 counterbalance forklift. This four-wheeled forklift, designed for the toughest environments both indoors and outdoors, has a load capacity of 2500 kg and a lifting height of up to 6.50 meters.
The work environment of the Traigo 80 is spacious. The driver’s seat is isolated from the rest of the chassis, reducing vibrations felt by the operators.
Like the pallet trucks, the forklifts come with lithium batteries. Additionally, the fleet for the Olympics includes five forklifts equipped with hydrogen fuel cells.
The team uses these forklifts at Olympic sites located near hydrogen refueling stations, such as the Golf National and the Champ de Mars.
According to Benoît:
“Hydrogen offers the best of both worlds between combustion and electric power. Electric forklifts emit no emissions, making them a clean way to transport goods. However, they can’t work continuously due to recharge times. Diesel emits but allows continuous use since it can be refueled in three minutes. Hydrogen, when produced cleanly, emits no gases and enables continuous operation.”
Indeed, it takes only 1 to 3 minutes to refuel a forklift with a fuel cell, allowing continuous work for logistics operators. The electric pallet trucks and forklifts are used an average of 4 hours per day.
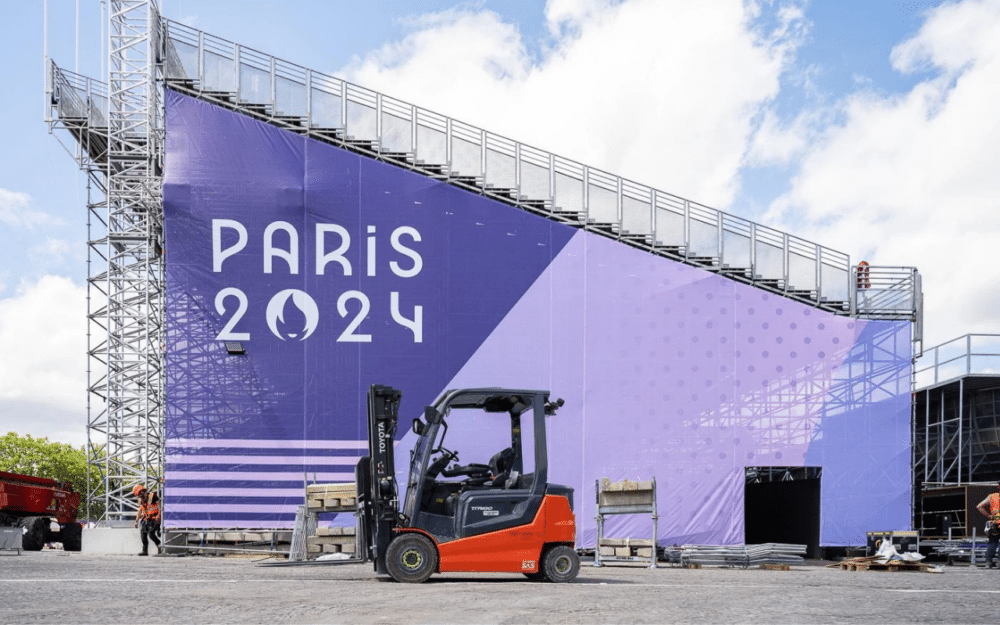
Each Olympic site has 4 to 5 forklifts in reserve. They operate mainly at night when the sites are empty. A hub in northern Paris stores all the equipment, which is then deployed as needed to the Olympic sites in the capital.
The handling equipment is rented for the Olympics for short durations. Some vehicles are rented for 2 to 3 days, while others have been on site for six months, such as those used for stadium construction.
A dedicated Toyota team manages the scheduling, allocation, transportation, retrieval, delivery, 24/7 maintenance, and repairs of the forklifts at industrial sites across France and near the Olympic venues.
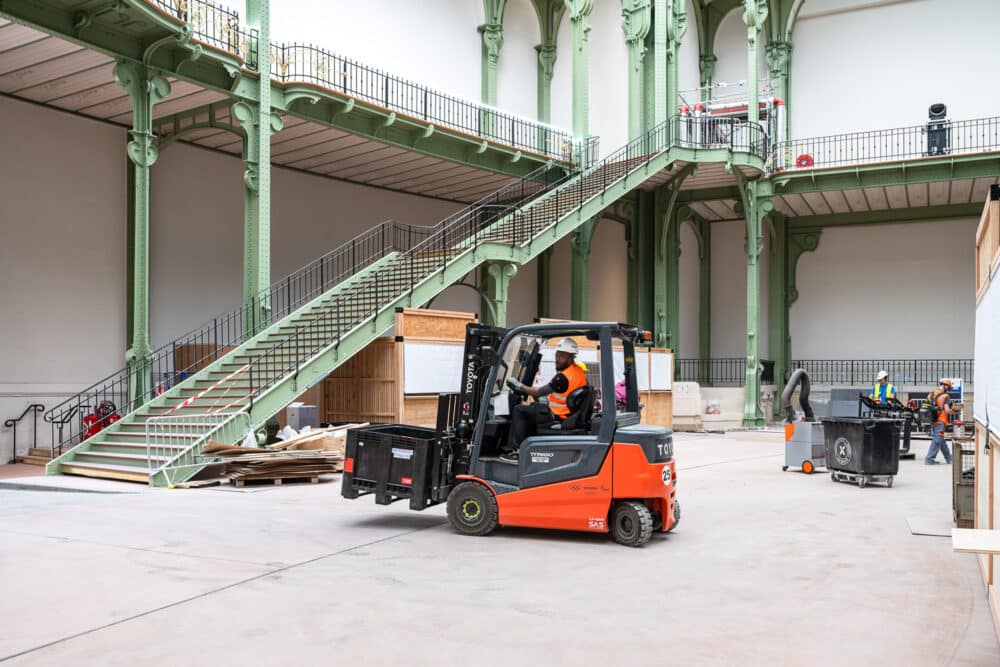
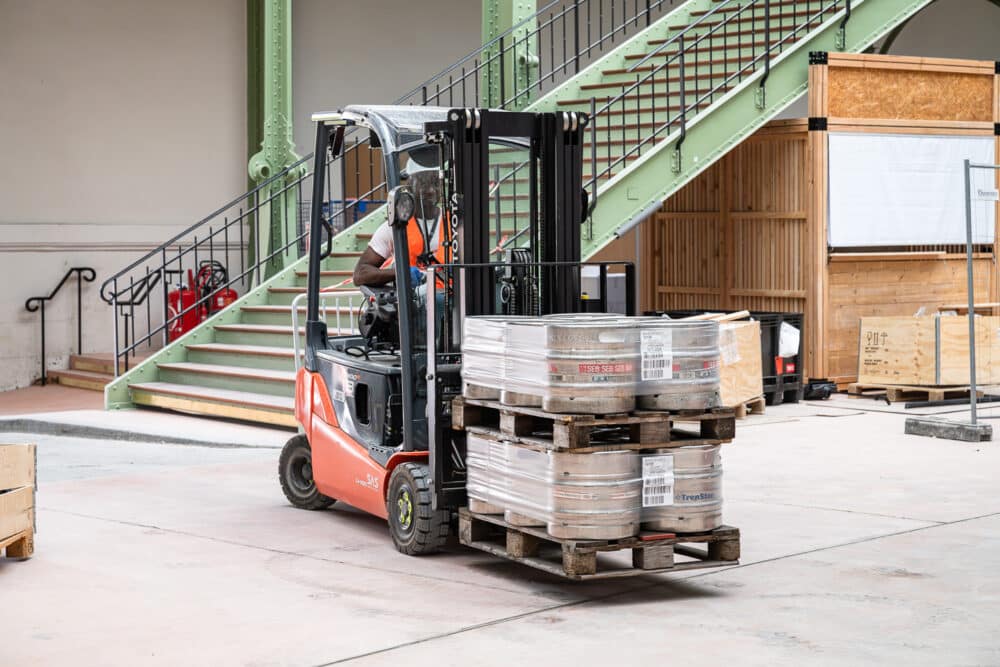
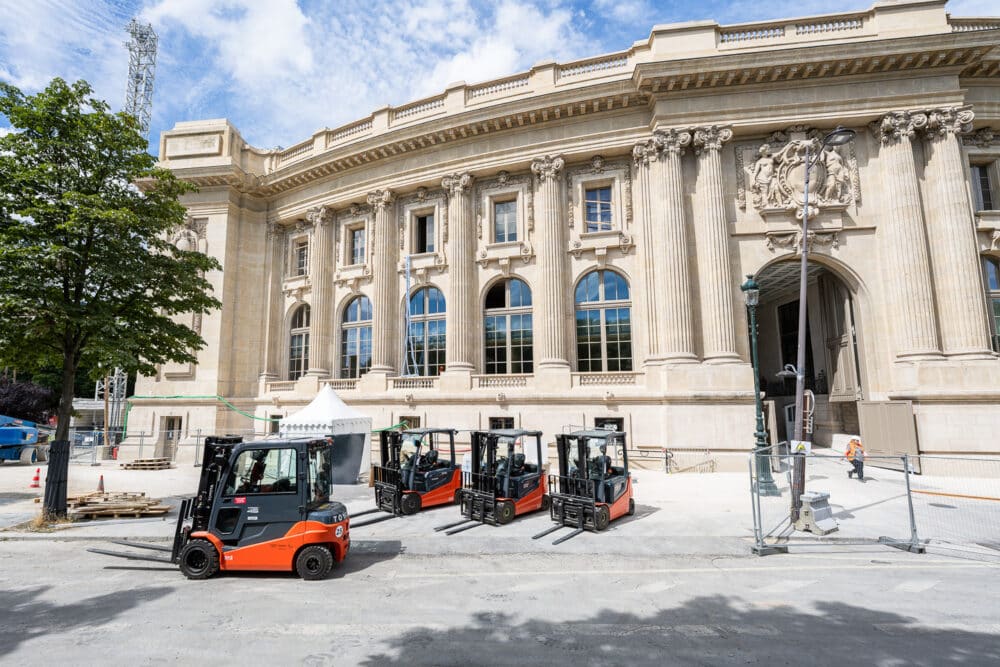
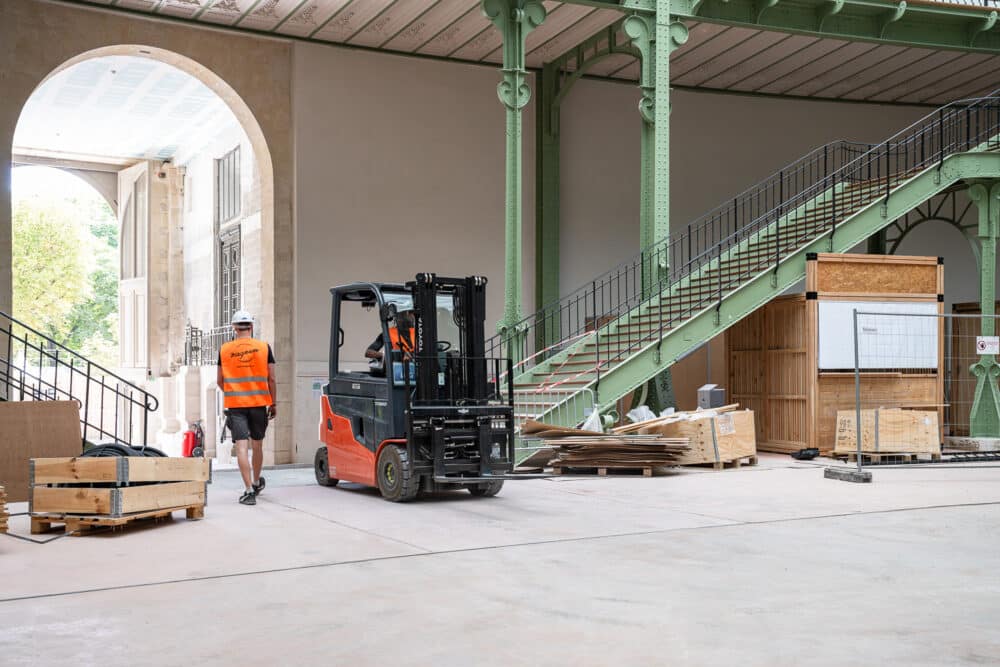
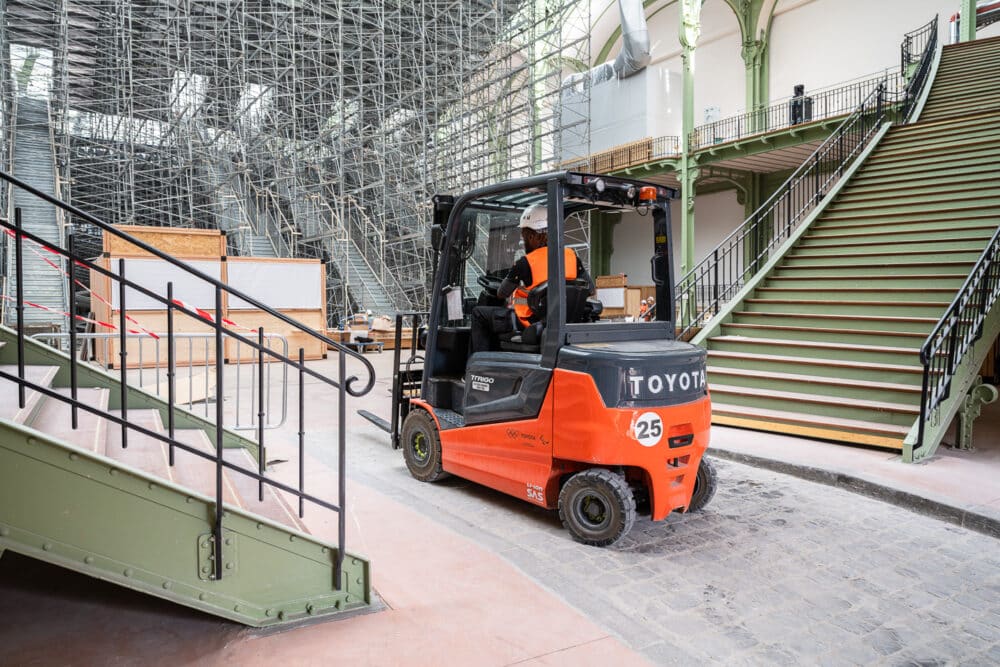
Adaptation to Challenges
To meet the unique demands of these outdoor Olympics, held in one of the oldest cities in the world, near historic monuments, and on Parisian streets often paved with cobblestones, TMH had to adapt its solutions to all these constraints.
Sustainability
First, regarding sustainability, as Eric Loustau explains:
“The Olympics’ specifications were very strict. The most challenging aspect was indeed the zero-emission requirement. We committed to using only electric forklifts with lithium and hydrogen power, avoiding diesel and gas.”
Training
Training, particularly for forklift operators, was also a significant challenge for the group. Due to the scale of the event, more operators were needed than usual. TMH offered to assist Olympic partners in training their operators, including their temporary recruits, with safety training modules.
Additionally, Benoît adds:
“Given the outdoor environment and knowing that many of the operators would be young professionals not necessarily experienced with handling equipment, we limited our forklifts’ speed to 12 km/h, whereas normally it is up to 20 km/h, to ensure safety and prevent accidents.”
On each site, a trained site manager is responsible for recharging the forklifts, not the operators. With several thousand operators at this event, it would have been challenging to train them all in recharging procedures.
Outdoor Terrain
A major challenge for TMH was the terrain and ground conditions, Benoît notes:
“Normally, we operate on concrete surfaces, but that’s not the case here. At the Champ de Mars, for example, the ground underneath is soft. We had to coordinate with the organizers to choose the most suitable ground for the forklifts to move safely without getting stuck.”
The organizers laid down plastic trackways, similar to those used at concerts.
“We’re not using 4x4s; these are still industrial forklifts,” jokes Eric. “So, we had to adapt our standard equipment to the environment.”
Weather Conditions
Finally, the risk of rain has been and remains a concern, Eric Loustau reveals.
“Our vehicles are electric, and rain and electricity do not mix well. The main concern is recharging. At the Olympics, forklifts are recharged outside, whereas typically, they are recharged indoors in warehouses.”
Now that the Games have started, the TMH team says they are relaxed and confident in handling logistics for the sites and the Olympic Village. Next, they will work on dismantling the Olympic stadiums and setting up the Paralympic venues.