Plastic recycling involves several methods tailored to the specific type of plastic being processed. With approximately ten different types of plastics, each composed of varying elements and additives, not all plastics can be recycled similarly. Thierry Gauthier, Circular Economy Advisor at the French Institute of Petroleum (IFPEN) Chemistry for Industry Center in Lyon, shed light on the current recycling processes. He also highlighted IFPEN’s innovative methods to indefinitely recycle plastics like PET and integrate biomass into recycling processes.
1/ Mechanical Recycling
Mechanical recycling of plastic is a process where plastic waste is transformed into new materials or products without altering their fundamental chemical structure. This process involves several key steps:
Plastic waste is collected, often through yellow bins, then sorted by type and color. Once sorted, plastics are cleaned to remove impurities such as labels, food residues, or other contaminants. The cleaned plastics are then shredded into small pieces or flakes. These flakes are melted and extruded to form plastic pellets or new finished products.
READ ALSO
Mechanical recycling is beneficial as it reduces plastic waste in landfills and decreases the demand for virgin plastic, thus conserving natural resources and reducing carbon footprint. However, as explained by Thierry Gauthier, it has its limitations:
“The limitations of mechanical recycling are primarily due to the presence of additives contained in plastics, such as colors, stabilizers, and pigments added to provide opacity to bottles or protect the contents from UV damage. While these additives impart useful properties to plastics, they complicate recycling. Once additives like colorants are present, it becomes impossible to produce transparent bottles from colored ones.”
Moreover, with mechanical recycling, plastic tends to heat up and degrade over time.
“After 5 to 10 cycles, issues like the appearance of black spots and increased fragility during extrusion and blowing of bottles become more prevalent. This is why we need chemical recycling in addition to mechanical recycling” Thierry emphasized.
Chemical recycling addresses these challenges by breaking down plastics into their chemical components and rebuilding them into new materials, offering a promising solution to achieve true circularity in plastic use.
2/ Chemical Recycling
Chemical recycling of plastics aims to break down used plastics into their basic chemical components, known as monomers. Unlike mechanical recycling, which melts and remelts plastics to create new products, chemical recycling involves chemical reactions to break polymer chains and obtain pure monomers.
There are three main processes in chemical recycling: depolymerization, dissolution, and conversion. The choice of process depends on the type of plastics being recycled.
Depolymerization (PET)
Plastic waste is heated in specialized reactors in the presence of solvents, catalysts, or other chemical agents. This process breaks down the long polymer chains of plastic into monomers. These monomers are then purified to remove impurities such as dyes, additives, and contaminants. This results in high-purity monomers that can be reused. The purified monomers are subsequently repolymerized to form new polymer chains. These polymers can then be used to manufacture new plastics or other plastic products.
This process is particularly effective for PET recycling because it produces pure monomers that can be repolymerized with the same properties as virgin PET. They can be used to produce new transparent plastic bottles, which mechanical recycling cannot achieve.
IFPEN has developed a process aimed at enabling infinite recycling of PET and tailored for polymers:
“The industrial process we implement begins with depolymerization. We melt the polymer in agitated reactors operating continuously. This is crucial for the process’s profitability. Once the PET is depolymerized, it undergoes several purification and separation stages, involving physical operations in a furnace. The objective is to obtain a new monomer that can be repolymerized. This results in a white powder. This powder is then repolymerized into granules, which can be sent to the plastics industry to make new PET bottles. The process is very rapid. From the moment a bottle enters to when a material that can be repolymerized exits, only a few hours pass.
The first plant using this process will open in France in 2027, managing 30,000 tonnes of recycled PET.
Currently, there are four chemical recycling depolymerization projects for PET in France: the Eastman project in the Seine Valley, the Loop project in eastern France, the Carbios project, and the IFPEN project.
READ ALSO
The Dissolution Process (polyoléfines)
The dissolution process in plastic recycling, introduced to the market 2 to 3 years ago, focuses on purifying polypropylene and polyethylene to regenerate virgin-quality materials. This innovative method achieves a remarkable 99% efficiency in removing additives and organic contaminants, yielding granules ready for reuse.
“Unlike depolymerization used for polyesters like PET, which breaks down into uniform beads, polyolefins such as polyethylene and polypropylene are formed through polyaddition, resulting in a more random molecular structure. This characteristic makes traditional mechanical recycling challenging, as it produces fragments of various sizes rather than uniform pellets. Therefore, the dissolution technology employs a solvent-based approach. It dissolves the polyolefin polymers in a solvent medium, facilitating the separation of impurities like pigments and additives. This process ensures that the recovered polymer maintains its integrity and quality, suitable for reintroduction into manufacturing processes.”
The primary beneficiaries of this technology are polymer manufacturers (polymers) seeking sustainable alternatives to virgin plastics. For every ton of polypropylene produced using this method, one ton of petroleum is conserved, highlighting its significant environmental impact by reducing reliance on fossil fuels.
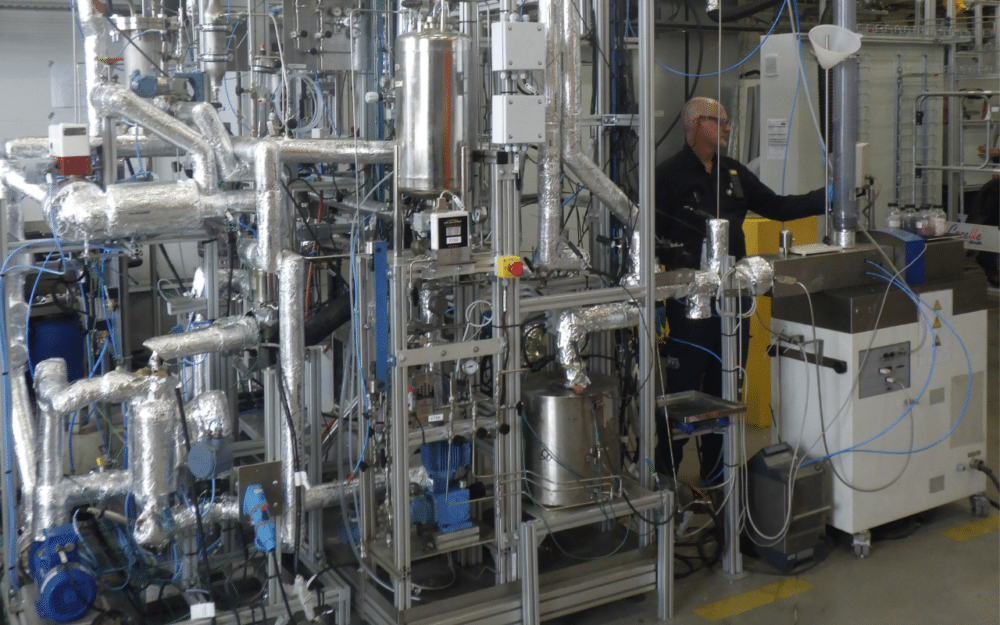
The Conversion Process
The essence of the conversion process is pyrolysis. The interest in conversion lies in addressing plastic waste streams that are less prepared and less purified compared to those suitable for dissolution (polyolefins), or depolymerization (PET) processes.
Indeed, with dissolution and polymerization, there is a strict requirement for purity in the plastic feedstock, typically around 99% or higher. Pyrolysis, on the other hand, can handle plastic waste streams that may contain varying proportions of different types of plastics, such as, for example, 90% polyethylene, 5% polystyrene, and 5% polypropylene.
These mixed streams cannot be efficiently processed through dissolution due to their impurities. Pyrolysis thus meets the needs of certain waste collection and sorting systems.
“However, the process returns to earlier stages in the petrochemical chain, converting the plastics back into intermediate petroleum cuts like diesel and gasoline. Consequently, efforts focus on purifying the pyrolysis oils. After pyrolysis, these oils contain contaminants such as chlorine. The challenge lies in hydroprocessing these petroleum cuts to remove impurities, similar to the refining process that cleans gasoline before it reaches your vehicle’s tank.”
The approach involves treating pyrolysis oils through hydroprocessing to refine them. This method, which is in development, ensures that the oils, derived from the pyrolysis of plastics, meet the purity standards necessary for reuse or further processing into valuable petrochemical products.
The primary beneficiary of this technology is the oil industry.
3/ The Anellotech Process
There is another chemical recycling process for plastics in development, to which IFPEN is contributing. This patented technology, Bio-TCat™ by Anellotech, is a thermocatalytic process that converts lignocellulosic biomass into benzene, toluene, and xylene, which are chemically identical to their petroleum-based counterparts. The goal is to create 100% bio-based PET plastic bottles.
Partner Suntory has used p-xylene obtained through Bio-TCat™ technology to produce a 100% bio-based PET plastic bottle, marking a significant advancement in the development of renewable chemicals. This innovation paves the way for the upcoming commercialization of 100% bio-based PET bottles on a large scale.
“We start with polymers and return to the polymer stage, stopping at the monomer. Using biomass, the Anellotech process produces aromatics that enable the creation of the monomer, terephthalic acid, upstream of polymerization.”
There is a pilot project in the United States, (Texas) and the IFPEN is currently working with Axens to commercialize this technology.
“There are cost and competition issues, as well as resource challenges because we are now considering using biomass for many applications. For this process, we do not use food biomass but rather biomass waste, which we transform to produce aromatics. This entire phase has been demonstrated through the pilot project, and the subsequent stages involve more conventional chemistry. The initial challenge was to produce enough high-quality aromatics to make plastic. This hurdle has been overcome, and this method is as promising as other recycling methods.”
The environmental impacts are significant because this process requires energy. But it is still better than using petroleum.