In an interview with DirectIndustry, Mike Domke, Executive general manager at Waygate Technologies (a Baker Hughes business unit) details the features of the new Everest Mentor Visual iQ videoprobe, MVIQ+, their 3D measurement device designed for aviation and energy applications.

How different is the MVIQ+ from the previous version? There have been improvements in the hardware and the software.
Mike Domke: “Let’s begin with the hardware. On the hardware side, we’ve doubled the processing capabilities, a crucial enhancement for the software. We now have twice the embedded processing capabilities. This is a significant factor in tasks such as advanced analytics and various AI or machine learning applications. This enhancement is particularly vital for processing imaging data.
The information originating from the imager at the probe’s tip is what the user ultimately sees. There are numerous ways we can leverage this additional processing power. With our improved measurement technology, we can process measurements much more rapidly onboard. Considering the system is self-contained, it functions as an edge device in this context.
We’ve also introduced a new steering engine, addressing the cables, servos, and the connection between the user’s joystick input and the actual steering at the end of the probe in the field.”

And regarding the battery?
Mike Domke: “Regarding the battery, we have also enhanced the hardware on the battery side. This improvement results in an additional 10 to 15% battery life, a critical factor for field users without access to AC power.
On the software side, we have implemented various improvements. The primary focus was to enhance the user experience. Workflows have been streamlined, and significant enhancements have been dedicated to improving the user interface, resulting in a more seamless interaction with the device.
We are also providing contextual help directly on the device. For instance, if the user needs a specific analytic or measurement type, it is readily available. We have introduced live video analytics and offered various types of analytics directly on the device.
One noteworthy addition is the gas power assist, our proprietary analytic designed for online video assistance in examining gas turbines. This analysis helps users identify issues like dents, nicks, missing material, or cracks, highlighting these areas for the user.
We have also incorporated an updated blade counter. Counting blades is common in power generation and aviation applications, where, for instance, inspecting 60 blades at a particular stage is necessary. The updated blade counter now employs software to identify and count multiple blades in the scene as the user rotates the core of the engine.”

A significant addition to the new system is the integration of voice control. Can you elaborate on that?
Mike Domke: “It is indeed a groundbreaking feature in the industry. During inspections, inspectors typically have one hand on the insertion tube, manipulating the camera by pushing and pulling, while the other hand manages the joystick and control buttons. Their hands are occupied. Our system introduces voice control, allowing commands such as measurements, toggling different image transforms, and performing simple tasks like saving images and videos. Directional microarrays and speakers have been incorporated into the handset to provide feedback to the user, indicating that the voice system is activated.”

Another notable feature is the integration of the turning tool.
Mike Domke: “It is primarily applicable in aerospace and aero-derivative power turbines where a separate turning tool is employed. In collaboration with Rhinestahl, we’ve established two-way communication. This enables complete control of the turning tool directly from the MVIQ+. Automation is a key highlight here, allowing you to configure it to turn to a blade, save an image, move to the next blade, and save another image, all while you can observe this process effortlessly. This integration of the turning tool represents a significant advancement.
Turning tool integration essentially involves two closed-loop systems—the turning tool and the borescope. Traditionally, they operated independently, with the turning tool having its controller. The inspector, using the borescope, would conduct the inspection and collect data. It’s akin to two gears running separately. However, with this integration, a two-way communication channel is established, facilitating automation of the inspection process. This bidirectional communication is crucial for tasks like instructing the turning tool to move to a specific blade, capture an image, take a measurement, analyze the image, and then proceed to the next blade. This automation aligns with industry trends and represents the direction we are heading in.”
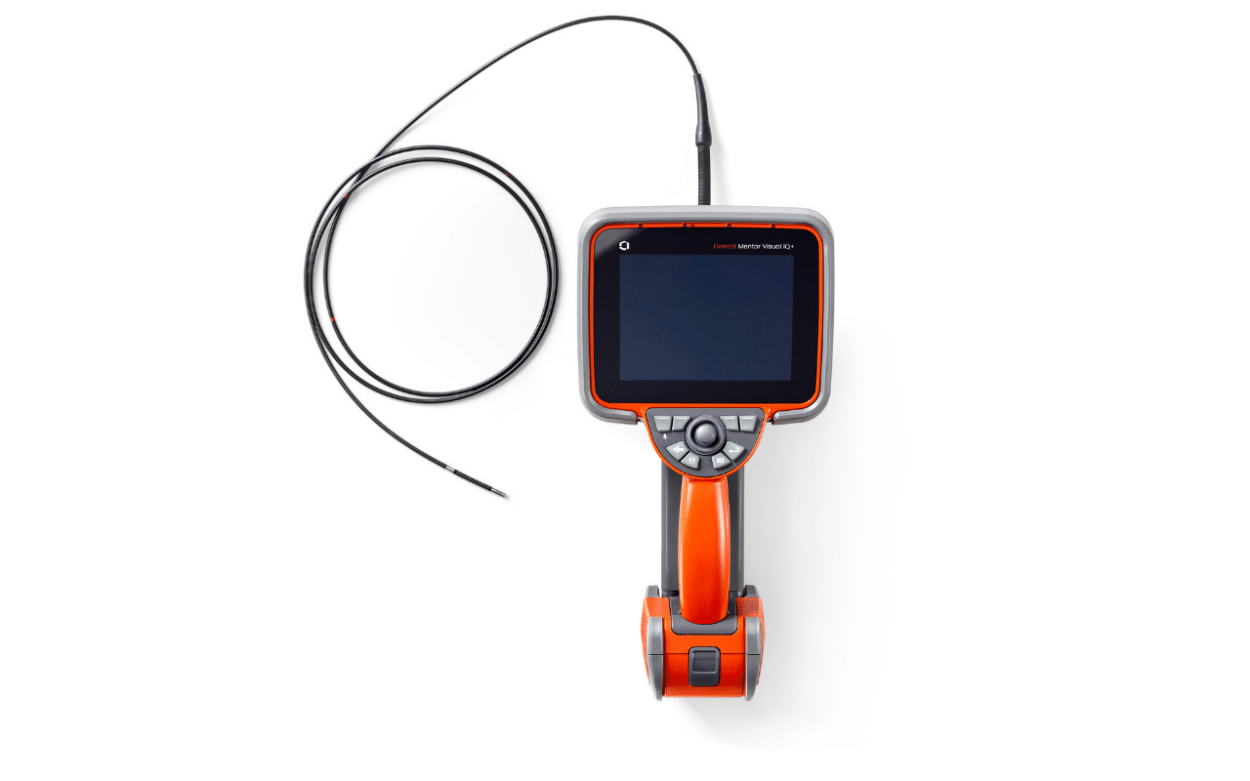

You mentioned enhancing battery capabilities while introducing voice features that may consume more power. How do you plan to manage this dual enhancement in the system’s capabilities?
Mike Domke: “We’ve achieved advancements in battery capacity, even though we anticipate increased usage during inspections. We’ve enhanced some of the onboard processing, optimizing the battery requirements for the system and increasing overall efficiency. This efficiency boost enables us to unlock greater capacity from a single-hour battery, even with the introduction of features like advanced analytics.
Warm swapping is another crucial improvement. A video borescope functions like a miniature computer, and shutting it down involves a time-consuming process similar to rebooting a computer. Enabling warm swapping in the field is a significant time-saver for inspectors, especially if they run out of battery power. This enhancement streamlines the inspection process and improves overall efficiency.”

How does the Everest Mentor Visual iQ cater specifically to professional and advanced visual inspectors?
Mike Domke: “We adhere to IP ratings, industrial standards, and military specifications. This ensures that our devices can withstand drops, varying temperatures, and exposure to specific chemicals such as jet fuel. This sets the foundation for our professional and advanced users who seek more sophisticated solutions.
Our differentiation also extends to how we process images, from the imager at the tip of the probe through the insertion tube to the user display. While adding an image to a device is one thing, processing that image to provide the best quality under different lighting conditions and when inspecting various materials involves optics and image processing is another thing. This is a key aspect that sets us apart.”

Can you elaborate on the key features that make the Everest Mentor Visual iQ stand out in terms of image quality and 3D measurement capability?
Mike Domke: “Another distinctive feature lies in our measurement technologies. We are the sole provider worldwide of 3D phase measurement and 3D automated measurement technologies for video borescopes. Users have multiple measurement types at their disposal, including depth and length, and we assist them in selecting the appropriate measurement type. Our devices offer unique capabilities, such as automated blade tip clearance measurement for engines. In this scenario, the device can intelligently recognize components, like a blade and a shroud, within the scene. The user’s specific intent is to measure the gap between these identified elements. This functionality streamlines the inspection process, allowing for efficient and accurate measurements without the need for manual intervention or explicit command inputs from the user.
When it comes to AI and ML, our goal is to assist users transparently within their existing processes, minimizing interruptions. Our on-device assistants can identify potential issues like cracks or dents in real time, catering to the needs of professional inspectors. The processing power in our hardware enables us to run these advanced techniques on the device itself, assuming no connectivity.
I will add one last thing. Our measurement technology allows inspectors to measure and analyze an indication using the same tip optic. Typically, inspectors would need to change the probe tip to a measurement-specific one, requiring them to pull the probe out, reattach the appropriate tip, and then re-enter the engine to measure an indication. With our 3D phase measurement, the same tip optic can be used for inspection, measurement, and analysis without the need to remove the probe.”

In what ways does the on-device AI enhance productivity and improve the probability of detection and inspection accuracy?
Mike Domke: “Consider large gas turbines, comparable in size to a house, where a six-millimeter borecope is used to detect indications. Utilizing AI enhances user navigation and identification of potential issues. For instance, AI can facilitate tasks like automatically counting blades, eliminating the need for users to manually keep track of complex turbine configurations. With 50 to 70 blades in a stage and multiple stages, this annotation capability boosts productivity and efficiency significantly.
Our analytics approach can be categorized into three types:
1. First-Party Public Analytics: These are analytics that we developed in-house. Examples include the blade counter and gas-powered set for detecting defects in gas turbines.
2. Third-Party Public Analytics: We partner with external companies like Air Innovations, a Dutch company specializing in borescope video analytics. Their cloud analytics are integrated into our equipment and they focus on compressor and combustion locations inside of gas turbines.
3. Third-Party Private Analytics: We collaborate with entities like Rolls Royce which developed specific analytics for precise applications and deployed them on the edge.
One of the unique aspects of what we’re doing is creating our analytics for broader consumption. Additionally, we have developed a standard API and interface for our device. This allows users building imaging analytics to look at or measure various features found in a wide range of assets, including boilers, gas turbines, aviation, power, wind applications, and gearboxes.
So, they can imagine building up anything, but deploying that and providing intelligence occurs at the point of inspection. In some instances, it is preferred to capture these things during the inspection rather than post-inspection.”

Do you plan to expand your clientele beyond the current industrial sectors you cover, aviation and energy?
Mike Domke: “Our current focus is heavily centered on aviation. In aviation, precision is paramount as the safety of flight is involved. This necessitates accurate defect identification and precise measurements. This is where our advanced measurement technology comes into play.
However, there is a clear trajectory toward expanding into additional sectors to enhance operational efficiency. In sectors like thermal power, wind power, and oil and gas, the focus shifts towards efficiency, demanding swift inspection processes. Here, our tools, like the MDI (menu-directed inspection) software, contribute to faster inspections by automating report generation and providing valuable assistance to users.
The power sector, especially involving high-value rotating equipment such as compressors in LNG facilities, stands out as another significant application of our device.
We are also looking at broader industrial domains like pharmaceuticals and food and beverage. Our technologies, which have applications in cleanliness assessments and weld integrity inspections, are poised to gain traction in these diverse sectors.”

Are digital capabilities a crucial aspect of your systems?
Mike Domke: “With Wi-Fi and Bluetooth enablement, cloud-based services, and frequent software updates, our devices offer continuous improvement, addressing bugs, enhancing user experience, and introducing new features. Our users benefit from these updates, much like the regular software updates on smartphones. Our cloud services allow automatic data backup, fleet-wide data analysis, and the sharing of inspection intelligence for further analysis and report generation.
We also provide a comprehensive software update service akin to an app store. In this store, we host public applications like the analytics I mentioned earlier, developed in-house and capable of being pushed to devices for updates. Additionally, we maintain a private store for specific cases, such as the Rolls Royce example I shared. This private store allows targeted deployment of analytics to designated devices with the appropriate access rights.
Moreover, we offer a robust data backup service for our edge devices. These devices store data either internally on the SSD or externally on a USB jump drive if connected.”

How user-friendly is the Everest Mentor Visual iQ, and what kind of training or expertise do operators need to maximize their capabilities?
Mike Domke: “The assistance feature significantly enhances user-friendliness by guiding users on the appropriate measurement types. We provide extensive help content, including starter guides and voice commands, making it convenient for users to interact with the device.
Contextual help makes even simple actions, such as accessing analytics or measurement menus, easier by providing real-time information on available measurement types and offering voice commands directly on the device.
Regarding training, various options are available. Our customers often have internal training programs to elevate the skills of their borescope technicians. We also offer training sessions to ensure users understand the basics, including when to use different measurement types and advanced analytics. Users must be aware of the device’s capabilities, similar to understanding the features of a sophisticated digital SLR camera. Our training emphasizes not only the auto mode but also the location and context for utilizing the advanced features on the borescope.”

Do you already have plans for new improvements?
Mike Domke: “Looking ahead, we anticipate a greater focus on enhancing user assistance on the devices, given the complexity of these inspections. Simplifying processes for users and providing guidance will be a key area of development. We aim to increase the utilization of automated measurement and machine learning analytics for object detection. This includes identifying what the user is viewing and tagging images with appropriate names.
Additionally, automation will play a crucial role. Whether it’s counting blades, recognizing defects, or conducting measurements, we envision creating workflows that connect these processes seamlessly. The goal is to automate various tasks and streamline the overall inspection process.”

Do clients who own the older version have the option to update their existing equipment with the new software, or is it necessary for them to purchase the entire new system?
Mike Domke: “Regarding clients with the older version, we will offer a software update that includes some features, but not the majority. Unfortunately, certain enhancements, such as voice capabilities, require new hardware, including an updated battery. To accommodate existing users, we have a trade-in program where they can exchange their current equipment for the latest hardware.”

What is the price of the new product?
Mike Domke: “The price varies, ranging from $40,000 to $100,000, depending on the selected features and bundles. Regarding sales targets for 2024, we aim to exceed 1000 units.”