In the world of automation, the challenges faced by businesses are ever-evolving. From cost and schedule pressures to resource constraints and data overload, companies are constantly seeking innovative solutions to streamline their processes and enhance efficiency. Honeywell’s Experion® PKS CONTROL HIVE (Highly Integrated Virtual Environment) solution aims to revolutionize the automation industry and improve system resiliency.
While on a reporting trip in Orlando, Florida, for Honeywell’s HUG event, our DirectIndustry analyst Hicham Dhouibi met with Joe Bastone, director of product management for Experion PKS, and Brian Reynolds, the Chief Technology Officer responsible for the automation solutions line of business at Honeywell Process Solutions. They shared their insights on the potential of HIVE and the future of virtual controllers.
One of the major issues faced in traditional automation solutions is the reliance on bespoke engineering efforts, resulting in increased costs and project delays. For instance, in unmanned platforms, relying on a single controller can be risky and time-consuming as any issue that could occur with the controller requires immediate attention. To enhance system resiliency, it’s therefore crucial to implement solutions that support redundancy and reliability, in order to make operations smoother and less stressful.
While some companies might prefer one-off solutions tailored to their specific needs, it often proves expensive and challenging to engineer and maintain. These bespoke solutions don’t align well with what most of them truly want – modular systems and standardization within their setups explains Joe Bastone:
“We observe that customers have distinct requirements, and they also seek standardized solutions as they prefer not to be isolated, which could lead to inadequate support. Hence, we strike a balance by offering a standard approach that can be tailored to meet their specific needs.”
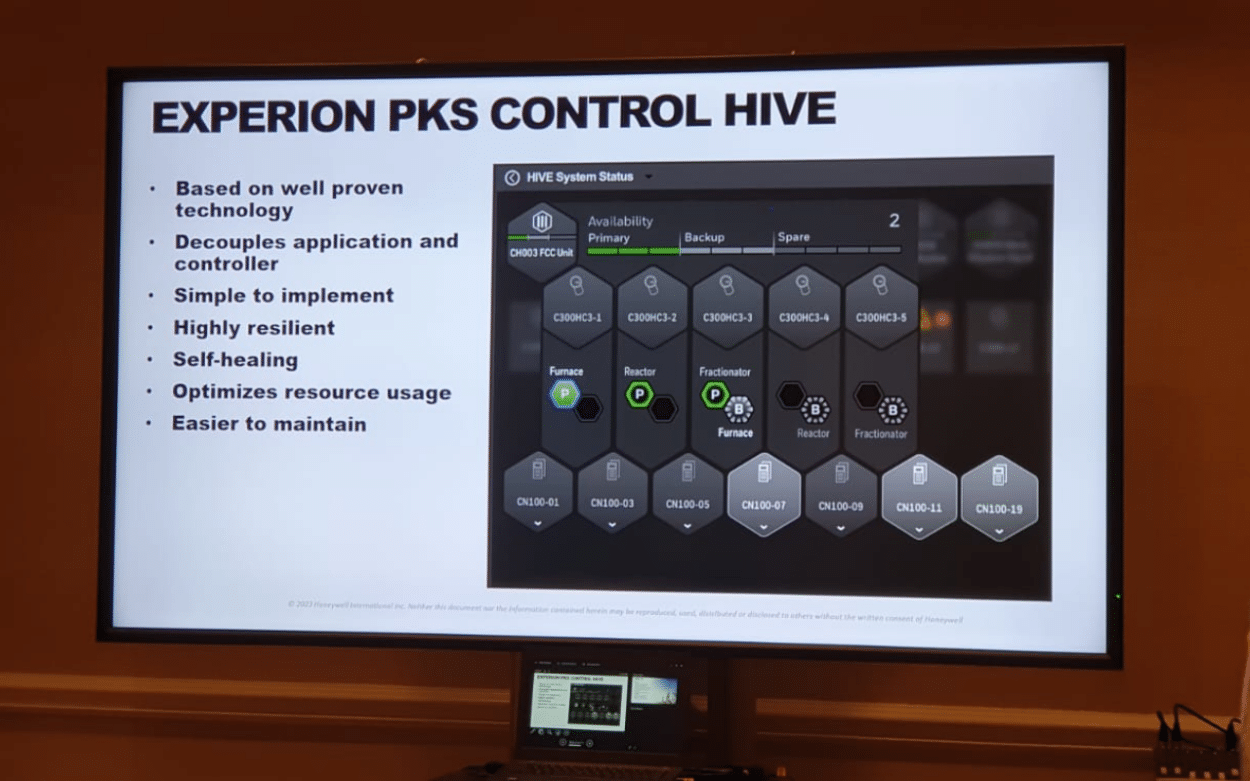
CONTROL HIVE
This is where HIVE comes into play. The system consists of three main components: IO HIVE, CONTROL HIVE, and IT HIVE.
With IO HIVE, I/O modules and assignments are decoupled from controllers, providing the freedom to assign any I/O channel to any controller.
IT HIVE reduces IT equipment at process facilities.
CONTROL HIVE seamlessly integrates multiple individual controllers, presenting them as a unified cluster of shared compute resources with universal access to I/Os.
Traditionally, control strategies were tied to specific controllers and restricted by the availability of IO modules. But with Control HIVE, the control strategies are decoupled from the controllers, enabling any controller to access any IO device.
“The groundbreaking feature of CONTROL HIVE is the decoupling of control hardware from the control application. You can envision the controller as a phone, and the running app as the control application. Now, if you wish to transfer that application to another controller, it’s entirely possible. Similarly, a controller can host two control applications simultaneously. This revolutionary aspect lies in the separation of controller hardware from the controller software, enabling seamless flow of the controller application between different hardware platforms.”
CONTROL HIVE takes a group of controllers and forms a cluster with a specific control capacity. This approach eliminates the need to focus solely on one-on-one redundancy, as an orchestrator now oversees the controllers and their applications.
This eliminates the need for peer-to-peer control and reduces complexity in system architecture. Moreover, CONTROL HIVE enhances resiliency by automatically providing backup applications in case of a controller failure, ensuring uninterrupted operations and minimizing user intervention.
“We have successfully leveraged existing functionality in the area of redundancy control. You have two controllers, Controller A and Controller B, and you connect them with a redundancy cable. Then, you inform the system that these two controllers are redundant, and it manages the rest. If Controller A fails, Controller B automatically takes over. We applied the same approach to CONTROL HIVE, but at the application layer. Each controller runs an application, and redundancy is now handled between the applications. If a controller fails, the corresponding application also fails, and another controller automatically takes over as the primary, ensuring continuous operation.”
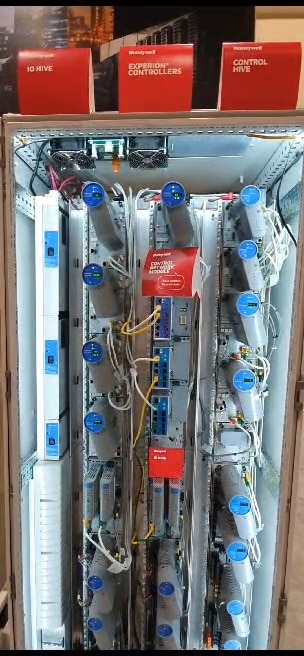
If Controller A fails, Controller B will become the primary. However, to maintain one-on-one redundancy, another controller, Controller C, with spare capacity, takes over. (H. DHOUIBI)
If Controller A fails, Controller B will become the primary. However, to maintain one-on-one redundancy, another controller, Controller C, with spare capacity, takes over. The system recognizes that Controller C only has a primary application, so it swiftly deploys a new application that synchronizes with the primary. Within minutes, another application is running as a backup. In case of a controller failure, the orchestrator can automatically activate another control application, ensuring continuous operation and maintaining the one-on-one redundancy concept.
An analogy that perfectly encapsulates this newfound flexibility is watching a movie on Netflix. As a viewer, you don’t concern yourself with the location of the streaming server; all that matters is that you receive the movie seamlessly. Similarly, with the control strategies no longer tied to specific controllers limited to certain IO modules, they can now interact with any IO. This liberates the control strategies to move freely across controllers, adapting and optimizing in response to dynamic operational needs.
The idea behind all this is to optimize the number of backups needed. Indeed, generally speaking, controllers rarely fail, and most of the time, backup controllers sit idle, waiting for action.
“Instead of having multiple idle backups, we can spread the backup capacity across a bank of applications. For example, we might deploy a few spares in place, allowing us to distribute the compute capacity efficiently among the controllers. This way, you can reduce the number of spares needed, while also having the flexibility to add more capacity later if required. Hive empowers you to make the most efficient use of your resources and be prepared for any scenario, while minimizing waste and maximizing performance.”
The advantage of HIVE lies in its compatibility and straightforward implementation. Customers don’t need to undergo a complete system overhaul to benefit from its advantages. The new module CM 100, which acts as an interface between controllers and IO modules, supports all IO modules previously compatible with the series C platform, such as the C 300. No rip and replace is required.
The Power of Virtual Controllers
HIVE’s decoupling of applications from the controller opens up new possibilities in process automation. Honeywell recognizes the potential of virtual controllers and their ability to coexist with physical controllers, offering additional resiliency and flexibility.
“We are utilizing virtualization to complement the physical controllers, creating a hybrid Control HIVE that incorporates both physical and virtual controllers working together. This hybrid approach opens up interesting use cases because customers are accustomed to having physical controllers in their plants, but may be less familiar with virtual controllers. With the hybrid Control HIVE, they can incorporate a couple of virtual controllers as backups. In case of any issues, the virtual controller can swiftly take action and step in, ensuring a smooth operation without the need for immediate replacement of a C 300 that goes offline.”
The presence of virtual controllers not only adds an extra layer of resiliency to the system but also opens up doors to larger applications with enhanced performance and capacity.
For Brian Reynolds, if some customers may initially prefer sticking with physical controllers due to familiarity, there is a growing interest and enthusiasm among others to embrace virtual controllers.
“The benefits are evident, with virtual machines offering expanded performance and capacity compared to traditional embedded controllers. Running on a virtual machine provides access to more substantial applications, opening up new opportunities for industrial processes.”
When asked if Honeywell is considering putting those virtual controllers in the cloud, Bastone replied:
“We’ve discussed this, and it depends on the latency between the cloud hosts and the site, which could impact customer decisions. Some forward-thinking customers are interested in deploying more of the Experion system to their cloud, especially those with contracts with providers like AWS, Azure, or Google Cloud. They aim to replace more IT infrastructure with cloud-enabled solutions since they already use cloud services for other critical business processes. As a result, the idea of placing backup controllers in the cloud becomes a natural thought. While it may be reasonable to consider in the future, it’s for the moment unsure if all their customers are ready for it.”
The ability to mix and match physical controllers with virtual controllers is not yet available in the current release. For the moment, customers must make a choice between either physical or virtual options. The company expects the combinations of both controllers to be available soon.