Could digital transformation provide greater energy efficiency and extend the life of nuclear power plants well beyond 40 years? This is what Ansys believes. The world specialist in digital simulation partnered with French group EDF to foster the development of safe, low-carbon power generation technologies using Ansys’s multiphysics simulation tools. We talked to Eric Bantegnie, Vice President and General Manager at Ansys, to find out more about it.
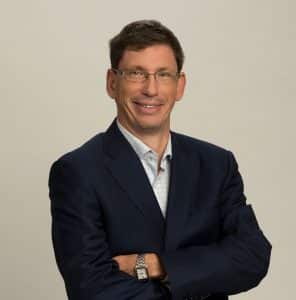
DirectIndustry magazine: Why is the nuclear sector interested in digital simulation?
Eric Bantegnie: Our customers want to know how we can guarantee the extension of the lifetime of power plants, how we can do predictive maintenance, how we can compare the way a system degrades in terms of performance compared to what had been planned, in a very individualized way at the level of each of the components. That’s how our collaboration with EDF started.
In a nuclear plant, many systems are in service. There are thousands of pumps with a wide range of operational variability, which operate under various conditions, with very long lifetimes, very high asset values etc. So it is very important to protect them and to reduce maintenance costs. There is both a safety and an economic issue. Our software offers the possibility to create a digital twin for all of the equipment in service.
DirectIndustry magazine: What kind of equipment are we talking about here?
Eric Bantegnie: This is equipment that the operator of a plant considers critical for management. It is not necessarily all of it. It ranges from complex equipment such as turbo-alternators to simple things such as pumps. There are no equipment limits. For example, if you have two identical pumps in a plant, they will not be used in the same way, they will not have the same life span. So we will create a simulation model for each pump. The data from sensors installed on each pump will allow the software to give predictions for each piece of equipment in an individualized way.
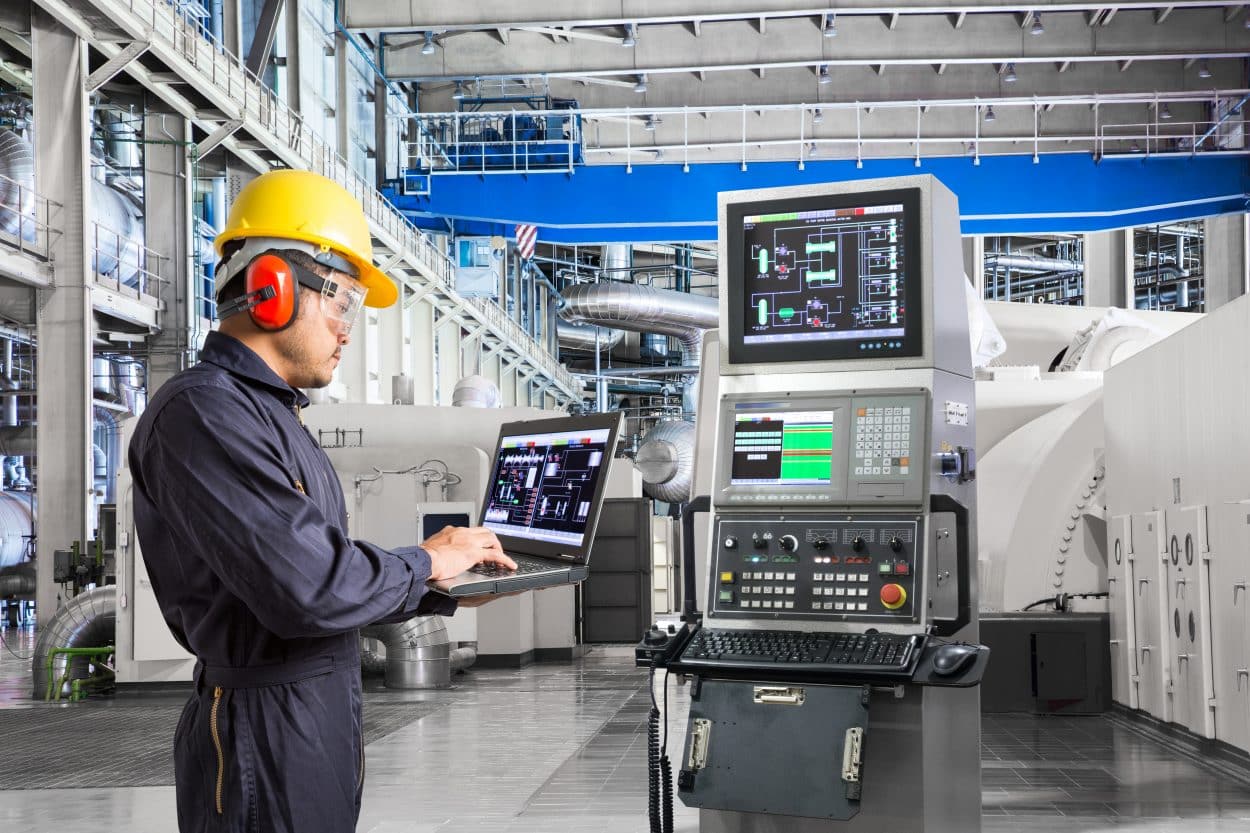
DirectIndustry magazine: How does the simulation work?
Eric Bantegnie: We offer multiphysics, multi-equipment and multi-scale simulations.
Multiphysics: for a given piece of equipment, we will simulate the combination of all physical phenomena at the same time. For an electric motor, we will simulate the electrical part, but also the thermal part, the vibration of the motor. We can mix several types of physics at the same time to have a precise simulation. Other simulation tools can only simulate one physical phenomenon at a time.
Multi-equipment: we are able to combine the affiliation of different interacting components in the software. In an alternator, there are dozens of different parts and we can simulate each of these parts and simulate the whole.
Multi-scale: we can simulate extremely fine and detailed phenomena such as an electronic chip or a small piece in a pipe, so we can simulate very small and microscopic scales. But we can also simulate very large scale physical phenomena over hundreds of meters (long range radars) and different orders of magnitude (turbo-alternators, autonomous cars). So we can zoom successively in on a piece of equipment, a sub piece of equipment, a component etc.
DirectIndustry magazine: And so, how can your software extend the life of a nuclear plant?
Eric Bantegnie: When customers use our software, they have the opportunity to use safety analysis tools which allows operators to list all the possible failure modes for their systems. It is anything that may potentially not work. So they have this catalogue at their disposal and with the simulation, they can see in real time if a system is going through a particular failure mode (i.e. abnormal vibrations, abnormal temperatures). Operational problems can be detected in real time. Normally, sensors are put where we can and not necessarily where we need them. For example, if you want to know if there is corrosion in the middle of a pump due to sand or oxidizing elements, you can’t put a sensor in the pump because that would block it. But the simulation makes it possible to predict precisely what the physical operating parameters of the pump will be. It gives very accurate prediction, alerts when there is a deviation of the systems, tells if a maintenance operation is required or if the system should be stopped. Digital twinning makes it possible to avoid breakdowns and to monitor the degradation of the systems. So to answer your question, by monitoring all the systems, this is how, in the end, we can extend the life of a nuclear plant.
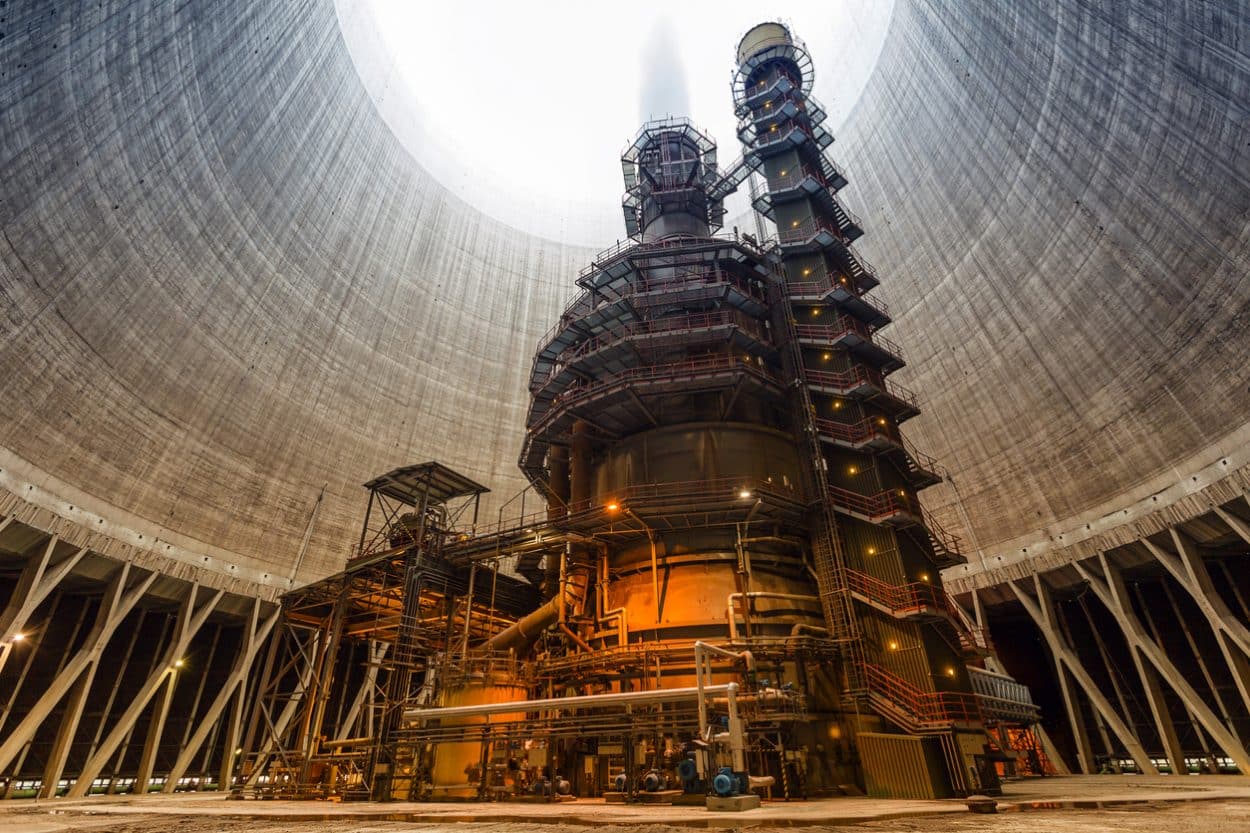
DirectIndustry magazine: So this is for future nuclear plants. What about the existing ones?
Eric Bantegnie: Power plants in France were built in the 1970s when computing and simulation power was not what it is today. But digital twinning can be used on equipment in older power plants that are still in operation. We can simulate existing equipment for which we do not necessarily have detailed 3D data. We can create close-up simulations from operating data so we can also do predictive maintenance, but it is a bit more difficult.
DirectIndustry magazine: Can you also simulate nuclear catastrophes?
Eric Bantegnie: 3 years ago, we acquired a company called Medini which is specialized in failures. Failure modes can be simulated and analyzed to meet safety needs.
DirectIndustry magazine: Your digital simulations are today massively used in the automotive and aerospace industries. Why is the nuclear sector interesting for you?
Eric Bantegnie: The nuclear industry is interesting to us because it is a test bed. It is perfect for simulation because there are a lot of things you can’t physically test in the nuclear industry. If you want to know if a plant is going to melt down, you can’t do that, you’d better simulate it. Nuclear power is a good problem for us, it raises difficult questions for us and so it helps us move forward. The solutions developed for the nuclear sector have often been adopted by the rest of industry a few years later. Our multiphysics simulation software Ansys Twin Builder™ was inspired by use cases from the nuclear industry.
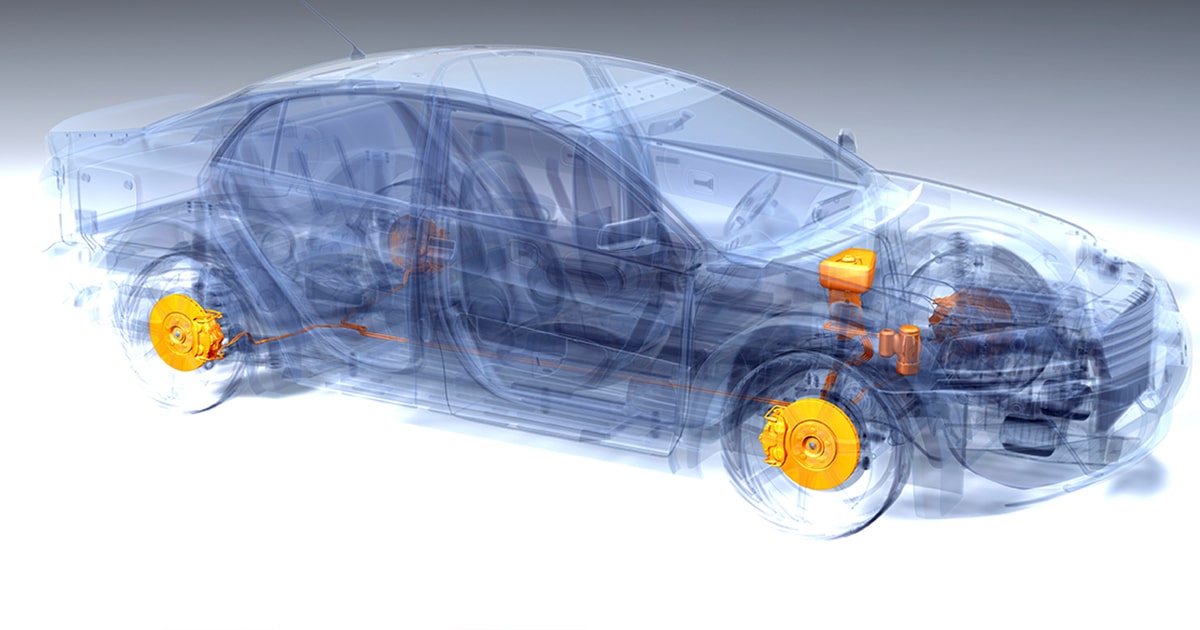
DirectIndustry magazine: Can you give us some examples?
Eric Bantegnie: The solutions we are developing and prototyping for the nuclear industry will be distributed in a year or two in other industrial sectors which have a strong demand for safety. I am thinking of aeronautics, energy, and increasingly in the automotive industry with autonomous systems. Nuclear has multi-complex problems with many interactions with mechanical and thermal systems. The thermomechanical problems are very hard, there are high temperatures, vibrations etc., the physics involved is very complex. So the advances that we are going to make on the modelling of these complex physical phenomena will serve, for example, aircraft engines. Nuclear also involves corrosion problems because the systems are here to last for a very long time. So we are addressing these problems and we could provide answers that could be applied in the oil&gas industry, where there are also corrosion issues in pipelines and refineries.
DirectIndustry magazine: What are the next difficult problems you are working on?
Eric Bantegnie: We’re already very advanced in fine physics simulation. Where collaborations with EDF are interesting is on deployment. The nuclear plants have many sub-systems that can potentially be digital twins. A nuclear power plant means potentially 20,000 or 30,000 digital twins. So when we know how to deploy all these digital twins to do the maintenance of a nuclear plant, we will also be able to deploy them on a nuclear submarine for example, or a refinery, on large and very complex systems. There is still a lot to learn about how to make deployment strategies and how to retrieve data. Today, our clients only have a few thousand digital twins in service. Going to 10,000 or 100,000 means changing scale and that’s still to come.