For inspection of components and parts with multiple-layer coatings in the aerospace industry, depth profiling is advisable. The ability to make confident decisions quickly during production, quality control, failure analysis, or research and development depends greatly on the rapid availability of relevant, accurate, and reliable data. With a 2-in-1 solution like the DM6 M LIBS from Leica Microsystems, significant cost and time savings can be achieved.
Written by James DeRose , PhD 1 , Kay Scheffler , Dr. 1 , Konstantin Kartaschew , PhD
Ensuring product quality in the aerospace industry with a 2-in-1 solution
Maintaining a cost-effective way to ensure product quality or reliable research results has ceaseless importance in the aerospace industry. [1-3]. Much time and money is spent using multiple techniques to visually inspect a material and identify its local composition [1-3]. Visual inspection is done with high resolution and high contrast microscopy and composition is determined with chemical/elemental spectroscopic analysis.
The LIBS method (which is used by the DM6 M LIBS exploits laser ablation to microdrill (µ-drill) into coatings and the component material. The ability to µ-drill allows the following:
- Depth profiling to determine composition change with depth into the material bulk;
- Layer analysis of painted or coated materials with multiple layers;
- Surface cleaning to remove oxides or contamination.
Example of depth profile analysis with the 2-in-1 solution
In the following example the depth profiling analysis was performed on a garter spring made of copper (Cu) and coated with nickel (Ni) and silver (Ag). Garter springs are coiled springs connected at each end which results in a circular shape. They are used for motor seals, belt-driven motors, and electrical connectors. (See figure 2). The analysis was done using µ-drilling and LIBS with the DM6 M LIBS solution. Each layer and the bulk of the spring were analyzed.
Figure 1 shows an example of µ-drilling holes into a steel alloy.
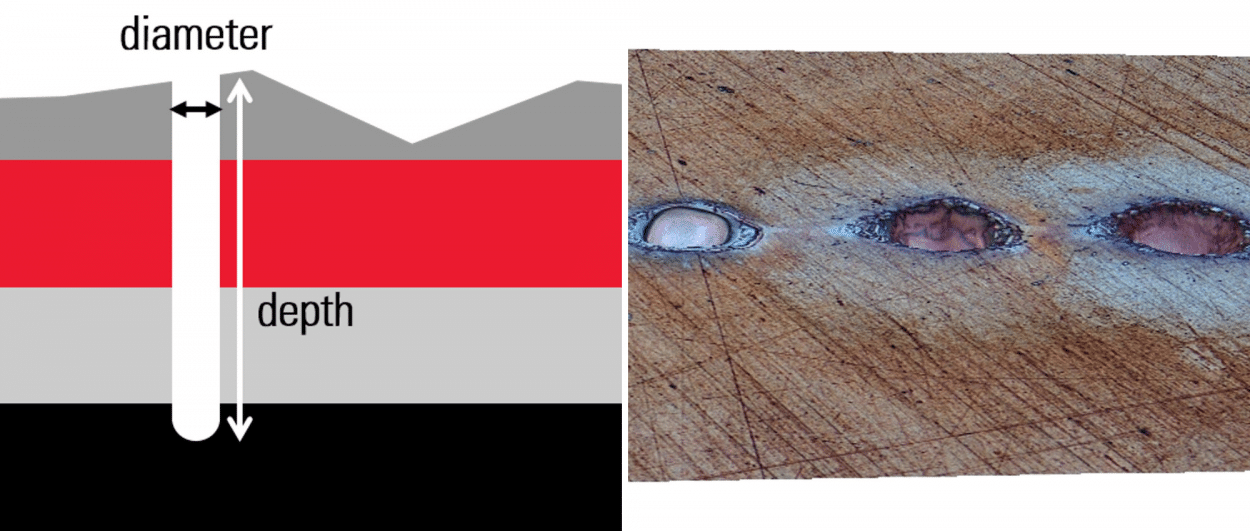
Results of layer analysis were acquired within 1 – 2 minutes
Micro drilling with up to 8 laser shots was done on the spring material to analyze from the top layer to the bulk. Depending on the material, approximately 5 µm can be ablated at the focus position by each laser shot. The entire time needed to make the 8 laser shots and acquire the data for the 3 spectra was between 1 and 2 minutes.
The results in figure 2 show that the spectrum of the:
- Top layer was obtained with the 1st laser shot and it is composed of Ag;
- Next underlying layer was obtained with the 4th laser shot and it is composed of Ni;
- Bulk was obtained with the 8th shot and it is composed of Cu.
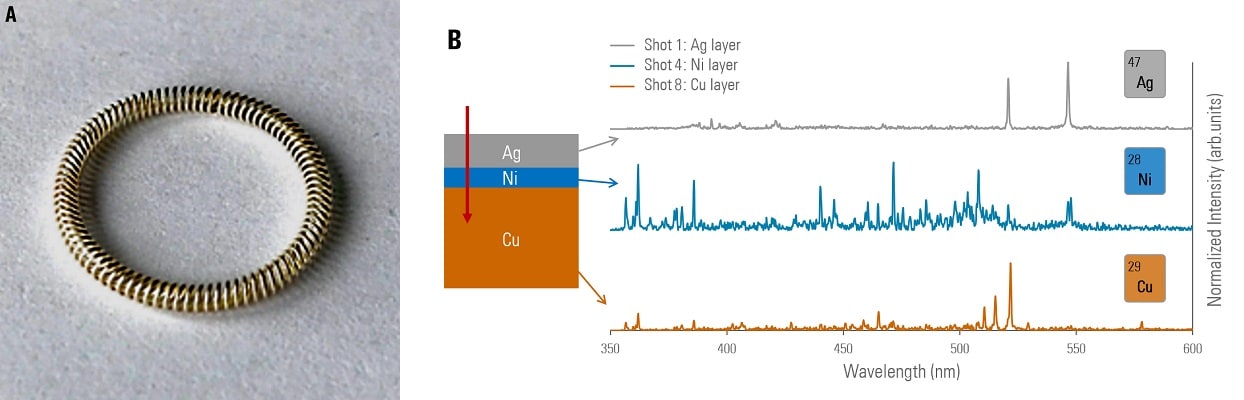
In Table 1 you can see the quality of match values for the garter spring spectra obtained with LIBS when compared to reference spectra from the database for the specific elements Ag, Ni, and Cu.
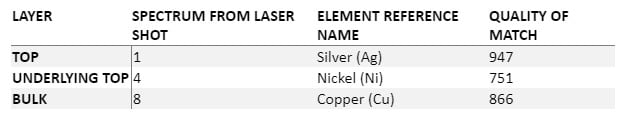
A valuable alternative to established profile analysis methods
Often the time and expense allocated for materials analysis are limited, but obtaining reliable results and achieving product quality always remains a priority [1-3]. The 2-in-1 solution by Leica Microsystems is a valuable alternative to established methods of profile analysis to provide you in a very short time with reliable results for your quality control.
Further Reading
- J. DeRose, K. Scheffler, See the Structure with Microscopy – Know the Composition with Laser Spectroscopy: Rapid, Complete Materials Analysis with a 2-Methods-In-1 Solution (2018) Science Lab, Leica Microsystems
- J. DeRose, K. Scheffler, K. Kartaschew, M. Horz, T. Locherer, Visual and Chemical Analysis of Steel Microstructure: Faster Rating of Steel Quality: A 2-Methods-In-1 Solution Combining Microscopy and Laser Spectroscopy (2020) Science Lab, Leica Microsystems.
- J. DeRose, K. Scheffler, Cleanliness Analysis with a 2-methods-in-1 solution: See the particles and know their composition at the same time (2019) Science Lab, Leica Microsystems.
- H. Kondo, M. Aimoto, H. Yamamura, T. Toh, Rapid Inspection of Defects of Steel by Laser Induced Breakdown Spectroscopy, Nippon Steel technical report no. 100 (2011).
- T. Kim, C-T. Lin, Laser-Induced Breakdown Spectroscopy, Chapter 5 in Advanced Aspects of Spectroscopy, M.A. Farrukh, Editor, IntechOpen (2012) DOI: 10.5772/48281.
- C. Meinhardt, V. Sturm, R. Fleige, C. Fricke-Begemann, R. Noll, Laser-induced breakdown spectroscopy of scaled steel samples taken from continuous casting blooms, Spectrochimica Acta Part B, vol. 123 (2016) pp. 171–178, DOI: 10.1016/j.sab.2016.08.013.