In an additive manufacturing ecosystem that is both constantly evolving yet still fragmented, Tessa Blokland, Industrial Design Expert and Co-Founder of LEO Lane, looks at why the need for companies to play well together is critical to realizing strategic objectives. And how, whilst unleashing the full benefits of additive manufacturing, knowledge sharing can be achieved securely without giving away the farm.
By Tessa Blokland, Co-Founder of LEO Lane
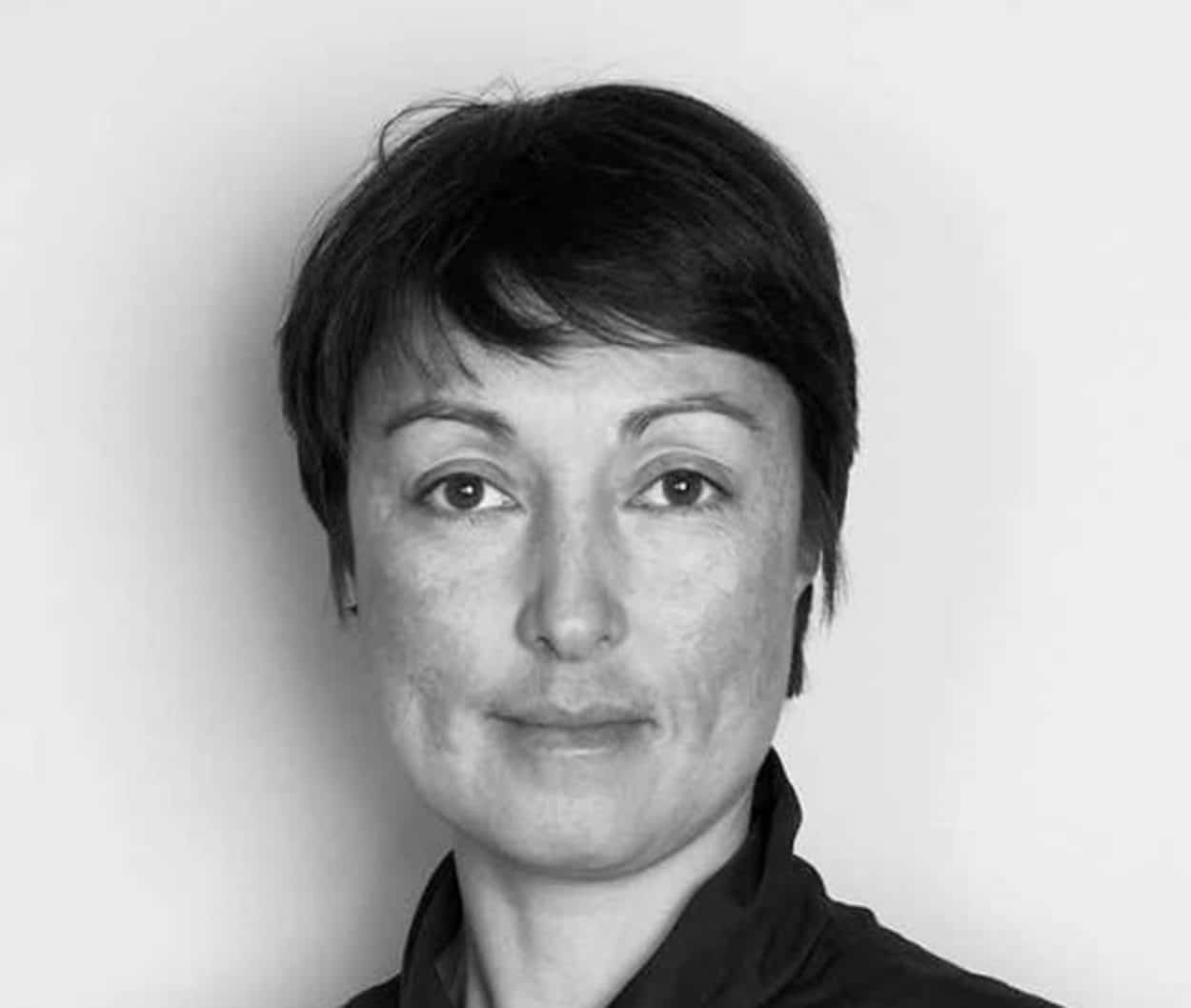
For many years, the additive manufacturing (AM) ecosystem has addressed important ongoing needs: reducing the cost of 3D printing, expanding the selection of AM ready materials, improving skills and training, and addressing design needs. It is widely recognized that the AM ecosystem is highly fragmented, which creates certain difficulties when requiring an end-to-end solution. Consequently, partnerships and collaborations are crucial for the ecosystem to succeed. We continue to see many such relationships form through cumbersome legal agreements and joint ventures – that are often both laborious and complicated to establish. In addition, as more and more industrial applications come forward, additional needs have come to the fore.
For many years, the additive manufacturing (AM) ecosystem has addressed important ongoing needs: reducing the cost of 3D printing, expanding the selection of AM ready materials, improving skills and training, and addressing design needs. It is widely recognized that the AM ecosystem is highly fragmented, which creates certain difficulties when requiring an end-to-end solution. Consequently, partnerships and collaborations are crucial for the ecosystem to succeed. We continue to see many such relationships form through cumbersome legal agreements and joint ventures – that are often both laborious and complicated to establish. In addition, as more and more industrial applications come forward, additional needs have come to the fore.
Some needs are pervasive, such as the need for repeatability, consistency across time and location, and intellectual property (IP) protection throughout the AM process. Others are specific to certain applications, these include: automation, post processing control, and workflow solutions. However, all these needs raise a common requirement that stems from how fragmented this ecosystem is: the need for integration and playing well with others, which is a key emerging need. Without seamless, easy integration, automation will be clunky and potentially impossible, workflows will be chopped up and manual, and the mind share and attention of highly skilled expensive personnel will be needed next to each and every 3D printer.
If COVID-19 has taught us anything, it is that the AM process needs to be automated, able to run remotely when necessary, and with as minimal disruption as possible to normal company operations. Integration is essential for that. Moreover, simple integration – including easy-to-use Application Programming Interfaces (APIs) – must be addressed by all ecosystem players; there is no magic glue that can integrate everything with everything. At least not yet.
Turn on the APIs
So, what are these APIs and why are they crucial? API is a software intermediary that allows one software application to communicate with another.
A good example would be your phone’s photo app; when you share a photo in another application, such as WhatsApp, the photo app will use an API to communicate with the WhatsApp app. Imagine if there were no APIs on your applications: you would have to manually move information from one app to the other or use files to save it in between apps. Cumbersome and inefficient, but not unlike any workflow where the vendors do not provide sufficient APIs to carry it out seamlessly.
In AM, where the workflow can be quite complicated, it behooves all the ecosystem players – from printer manufacturers through software providers to post processing equipment – to provide a sufficient set of APIs that allow seamless integration and automation.
We, at LEO Lane, pride ourselves on the richness of our APIs and the ease of integrating with us and we are fortunate to have like-minded partners. Recently several 3D printer manufacturers have indicated they are releasing their APIs to partners to enable just such integrations – an important step in the right direction.
Ultimately, the complexity of the total AM process, the 3D printing itself, and achieving a repeatable manufacturing technology, necessitate seamless integration and secured knowledge sharing in the end-to-end process. When collaboration and knowledge sharing is needed for practically every item and process, this becomes a key problem to solve.
AM Through and Through
Let’s take an imaginary AM-manufactured part for the passenger area of a car and assume it has some material and strength requirements. The car part manufacturer most likely has internal engineers that can design the part. If optimization for AM is desirable, that might be another expert, potentially outside the organization. Next, the material properties need to be considered, so an AM materials expert is needed, and if there are special requirements an external specialist might also be called in. Finally, the part’s exterior texture needs to be the same as other interior car parts, requiring a texturing expert.
This is daunting for any sized company – even more so when we dive into the details of this arrangement. Let us consider that a specialty material is needed. The material expert will need to make sure the company has all the information for the correct material properties in the part. How much should such an expert charge for their services? Is it the same price if the car part company plans to use it for 1 part (SKU) or for 10,000 different parts? How about for 10,000 of the same part? How about 10,000 each of 200 parts? If the expert is paid a lump sum, that lump sum is hard to determine. They could use a retainer, but once the company knows how to create the correct material properties, why continue the retainer? Finally, it makes a lot of sense to pay by the number of parts produced, but how would the expert know these numbers? Would the company be willing to open its books? Probably not. What can be done?
Software Answers Your SOS
Luckily, there are software, especially SaaS (Software as a Service, or cloud), solutions that can help. First, there are those that enable the uninitiated to benefit from expertise in a particular area. One example is a 2020 announcement of a texturing solution which is itself a collaboration of Adobe’s Substance and CoreTechnologie, combining both companies’ know-how. The software provides the user with a menu of different textures they can apply to their parts. Even more interesting, there are software solutions (most prominent among them, LEO Lane) that allow you to securely share a wide variety of knowledge without revealing it and support per part arrangements without the need for the company to open its books.
Secured knowledge sharing allows different entities to apply their specific expertise to an AM part without revealing this expertise to other parties contributing to the part or the part owner. Importantly, the solution makes sure the expertise is applied correctly, securely, and repeatably every time the part is produced. Furthermore, it allows the knowledge sharing expert to know their expertise was used without revealing proprietary information on how it was used. These types of solutions can speed up collaborations and allow for more AM applications to get to production faster.
United We Stand!
In our experience, once we delve into conversation with customers, we often find out that their requirements are more intricate than first thought, involving more vendors, such as workflow software or various optimization solutions. We are always happy to suggest other parts of the end-to-end solution to address particular needs that we are integrated with (or can easily integrate with, based on customer needs). Occasionally, another alternative is referring them to a turnkey solution provider that is our customer.
We work closely with turnkey solution providers including supporting them in their interactions with their clients, when needed. Turnkey providers have also witnessed that some well-placed questions can bring to light important information regarding the use cases the customer is targeting for AM and why they were chosen. They can also highlight unmet needs and suggest additional use cases that can be considered either now or down the line.
So, what should we ask customers about to clarify their needs? One aspect to focus on is the context, especially these days. COVID-19 has raised the awareness of supply chain failures and the likelihood that they will recur. If previously companies would treat these failures as one-off events, the pandemic has made it clear that future supply chain disruptions are to be expected. This is evident in various shortages still in place in 2021, such as for some white appliances. With the robustness exhibited by digital supply chains with AM in 2020, it is clear that there are additional use cases that should be (and are) considered by the OEMs. These use cases are relatively new and often require a wider end-to-end solution – but the devil is in the details.
In particular, putting in place a digital supply chain with AM fulfilment could be either for day-to-day or specifically for activation when the regular supply chain fails. Each of these scenarios has somewhat different needs but the latter (“emergency only”) is trickier. Every vendor strives for quick wins once its solution is available and normally an ‘emergency only’ deployment is not as popular since it may take a while to see a visible win. However, given the pace of recent failures, 2021 is shaping up to be the exception where these use cases will both be popular and provide quick wins for a new deployment. Furthermore, the champions of such projects will show their foresight and forward-thinking mentality at a time when others are struggling. A win-win!
Onward and Upwards – Cautiously!
A critical part of any such digital supply chain is to make sure it is indeed robust and secured when it is triggered, providing repeatable parts at different times and in different locations. The last thing anyone wants is to have a failure or inconsistency in an AM part from the digital supply chain. Consistency enforcement is therefore a key component that must be part of any end-to-end solution, often coupled with IP protection and tracking to ensure the peace of mind of top executives and the company’s bottom line.