In a world where most of us are now used to typing questions into chatboxes in search of ever more precise answers, why would industry not be seeking the same? Software, automation and manufacturing technology leaders are following in the steps of ChatGPT and launching their own natural-speak AI assistants to support their clients.
Earlier this year, Rockwell Automation began to commercialize FactoryTalk Design Studio Copilot, its generative artificial intelligence (GenAI) assistant for its cloud-based, system design software.
Around the same time, PTC announced the release of its ServiceMax AI field service management assistant, also powered by GenAI, which can leverage the full documented history of a field asset stored in the ServiceMax platform.
And 2025 has also seen Honeywell step into the game, with the latest release of its Forge Production Intelligence, which integrates performance monitoring with a GenAI assistant to help operators and production managers troubleshoot problems and potentially automate tasks.
For Joseph June, SVP and GM, ServiceMax at PTC, in the field service industry, one persistent challenge is the aging workforce. Many highly experienced technicians, who have accumulated years of hands-on knowledge, servicing very sophisticated pieces of equipment, are now retiring—taking that expertise with them.
“What do you do about that? Initially, there was no good answer, but when GenAI technology came, I thought maybe this was the opportunity. What if we could actually have an AI agent that is capable of accessing all the work that was ever performed within the organization – an agent aware of every customer interaction that has happened and was familiar with every piece of manual that was ever published?Five years ago, this would have been a pipedream but with GenAI technology, it seemed a possibility.”
Accelerating Design: Rockwell Automations’s Factory Talk Design Studio
Olgu Can Yilmaz, EMEA Product Manager for Controllers and Automation Solutions, explains Rockwell Automation’s FactoryTalk Design Studio was a co-innovation project with Microsoft.
“Copilot started with a simple prompt from ChatGPT – this was not of course applicable for industrial automation standards but it gave the core idea of how we could implement it to our system. This is basically prompt engineering that we have introduced to all available materials, project examples, samples and how Studio 5000 our core platform works for the design environment. The step-by-step project started with questions and answers for generic guidelines for the user or operator – how they can build up the machine or if there are any questions regarding our product portfolio that is available in the software itself. The next phase was to implement the idea of building a machine and asking Copilot to help create the code itself in the user interface of Design Studio.”
And there was some interesting and unexpected feedback:
“People were putting their own codes into it and then validating to see if there were any errors or how the operator could improve what he had created himself,” he explains.
Being able to engage with the AI assistant in natural language also proved successful.
“AI and this type of language models are now part of our daily lives, so in my opinion, this also helps the younger generation. For them, it is a very intuitive set of communication tools that they can use in a more efficient and more creative way.”
Today, he continues, there are already use cases from industry showing Copilot can help reduce engineering time at the beginning of the design phase of machine building – and this will only improve further over time.
“Once we enhance the usage of Copilot, we will definitely improve error detection and accelerate development time.”
He also aded that Design Studio is a solution that is cloud-based. Developers can therefore use their own laptop, create the project themsleves with the help of Copilot and easily go online with a controller on the other side of the world to deploy all the projects remotely to the real machine.
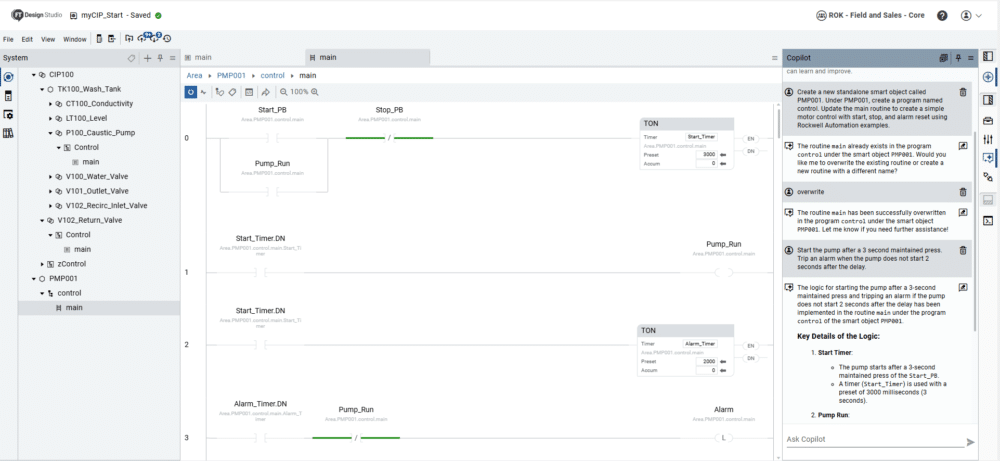
Faster Analysis: Honeywell’s Forge Production Intelligence’s Assistant
Dr. Claudia Chandra, Chief Product Officer for Honeywell Connected Industrial, explains Forge Production Intelligence’s assistant is also designed to allow engineers, plant managers and business leaders to access key insights through simple, natural language prompts.
The tool enables industrials to visualize, trend, and troubleshoot production issues from key performance indicator (KPI) deviation contributors and asset relationships.
“Without the AI assistant, a user would potentially perform exploration and do manual analysis to get the insights of what’s happening, why it is happening and what the root causes were that contributed to, for example, a KPI deviation. The user would just have to ask, what are the top KPIs that are deviating? What were the top contributors to those deviations and what would be the recommended actions to mediate those deviations? It just makes it a lot faster to analyze, provide root cause analysis and correct versus having to do manual exploration.”
Among the early adopters is one client who uses the tool to minimize the variations in crude unit yield and optimize their high-value product, she explains.
“They were able to reduce the time to identify and resolve these yield variations by 90% – this was less than the duration of one shift compared to the previous 120 hours required to do the same,” she emphasizes. The annual benefit on improving production throughput would be in millions of dollars for a complex food processing unit.”
The aim is for the tool not only to continuously learn based on expert input but also to improve accuracy.
“As confidence builds in terms of the answers it’s providing, we also want to provide AI agents to automate the recommendations,” she adds. We also want not only to be able to diagnose but to be predictive in terms of what will happen and prognostic in terms of recommendations and what could happen over time.”
Virtual Knowledge and Experience: PTC’s ServiceMax AI Chat
Via ServiceMax AI Chat, PTC’s users can find answers to questions about a specific job or asset, automate manual documentation and scheduling tasks, and review proactive recommendations for predictive maintenance, says Mr. June.
“The reason why ChatGPT got adopted so quickly was because it was in chat form. In reality, GPT has been around for a really long time but no one really knew about it until it became ChatGPT. Because it is such a natural way to be able to interact with technology we thought it was a great opportunity to solve this very well-known use case within service about an aging workforce. If you have people in service who want to tap into that wealth of knowledge and experience, this is a virtual way of them doing so.”
Moving forward, PTC will be monitoring how quickly their assistant learns.
“It’s just going to get smarter so the type of questions you can ask will just get more sophisticated. Right now, you can ask questions and it can find the data for you, but what I think is that we will start to ask for its recommendations – who is the technician that should be assigned to this job? Who is the one that will cost the least for our organization? It won’t simply answer questions but it will start to grab information and run calculations.”
Future users should also be able to converse with the assistant via other modalities – via speech, while driving, for example, or by uploading an image for the diagnosis of a problem.
“Lastly, I think that what you will see is multiagent interaction becoming more sophisticated – the reasoning part of the assistant figuring out which agent or agents it needs to talk to to get the answers it needs. By then, this will not only help technicians but also whole service organizations: they will be able to ask hard and big questions like: how do I increase the productivity and profitability of our organization while reducing costs? As it becomes smarter, and as we have agents that access systems, we will be able to start to ask questions that I think it would take human beings a really long time to figure out.”