Our reporter Erin Tallman attended the grand opening of Etex’s state-of-the-art plasterboard manufacturing facility in Bristol, UK, to learn about its high-speed production line, zero-waste-to-landfill scheme, and energy efficiency elements.
In a hurry? Here are the main highlights of the press conference and our interview with Christophe David, Chief Manufacturing Officer:
- Production Timeline: Though the grand opening was in March 2025, commercial production began in October 2024, following dry and wet commissioning phases.
- Zero-Waste to Landfill: The factory is designed to use 30% recycled gypsum from day one. All waste from production is reused in the process, and additional gypsum is sourced from job sites and demolition.
- Energy Efficiency: The factory integrates advanced heat recovery systems, reusing “fatal heat” from processes like calcination and drying to minimize energy waste.
- Sustainability & Local Production: The plant now manufactures 98% of the UK’s plasterboard demand locally, reducing the need for imports from Spain and France.
- Recycling Gypsum: Though 70% of gypsum still comes from quarries in Spain, the CO₂ footprint of transporting raw materials by large vessels is significantly smaller than transporting finished boards.
On March 12, 2025, DirectIndustry attended the grand opening of Etex’s state-of-the-art plasterboard manufacturing facility in Bristol, UK. This milestone event marks the culmination of years of investment and innovation for Etex, a global leader in lightweight construction materials. The Bristol factory is Etex’s largest production investment to date. It is designed to meet growing local demand while showcasing cutting-edge technology and sustainability practices.
This new facility represents a significant leap forward in production capacity and environmental stewardship. This strategic investment improves plasterboard manufacturing efficiency and reduces its carbon footprint through innovative processes.
The factory houses the manufacturing of plasterboard. But the company’s product range also includes fiber cement boards, fire protection materials, high-performance insulation, and high-tech offsite construction solutions. Its renowned brands include Siniat, Cedral, Promat, URSA, EQUITONE, and Superglass. Since its founding in 1905, Etex has become a global leader in lightweight construction materials. It now operates over 160 sites in 45 countries.
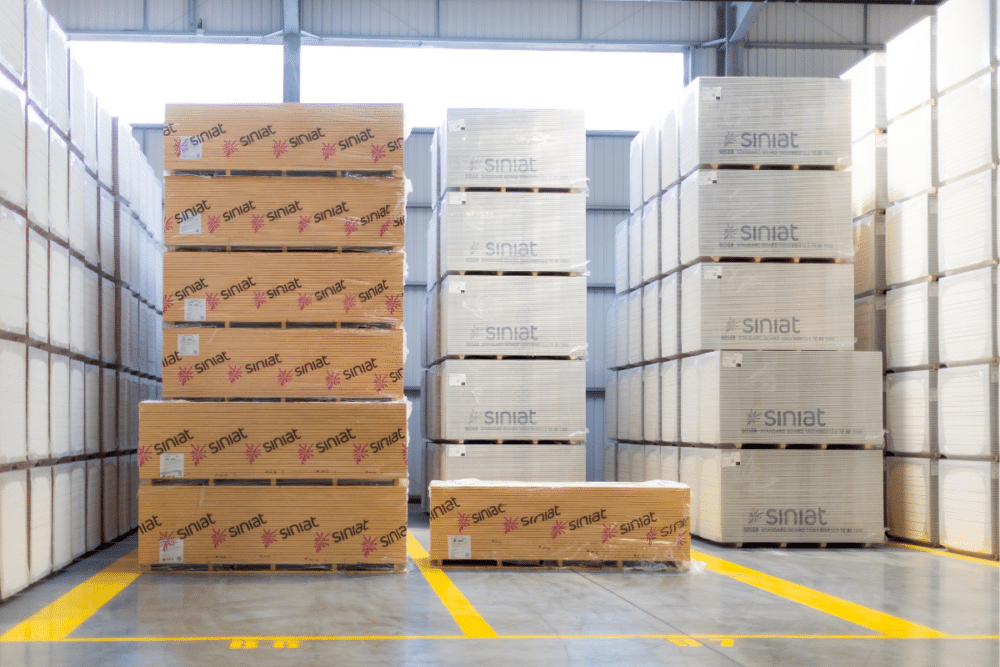
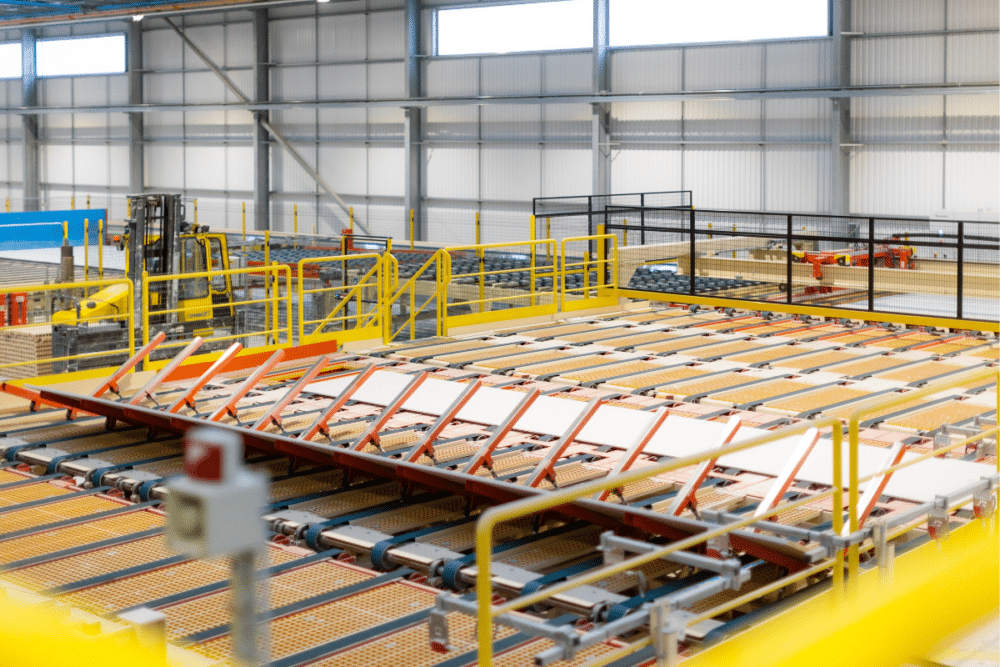
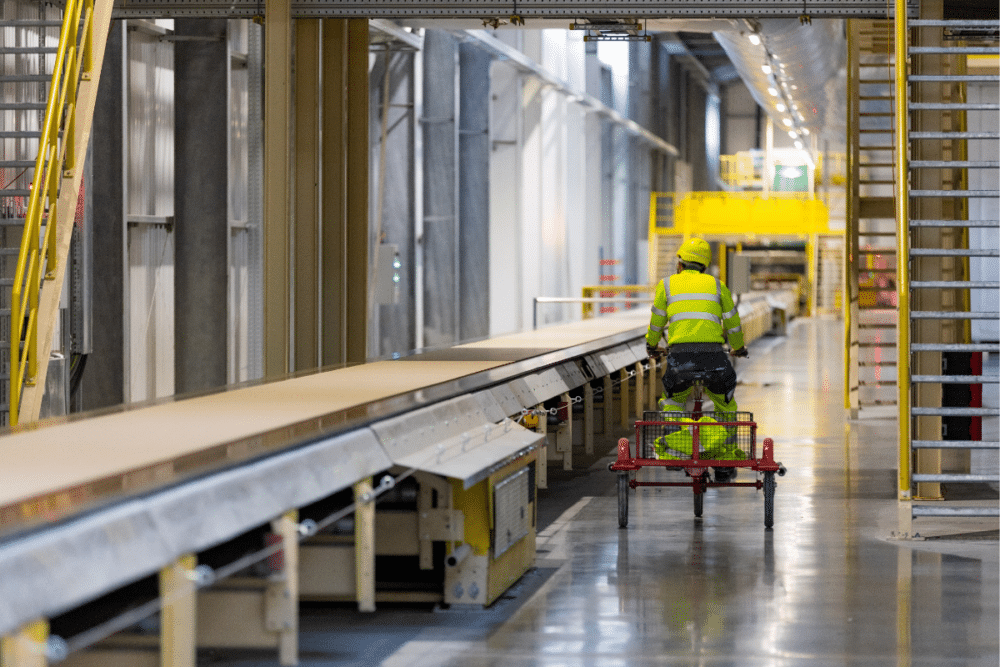
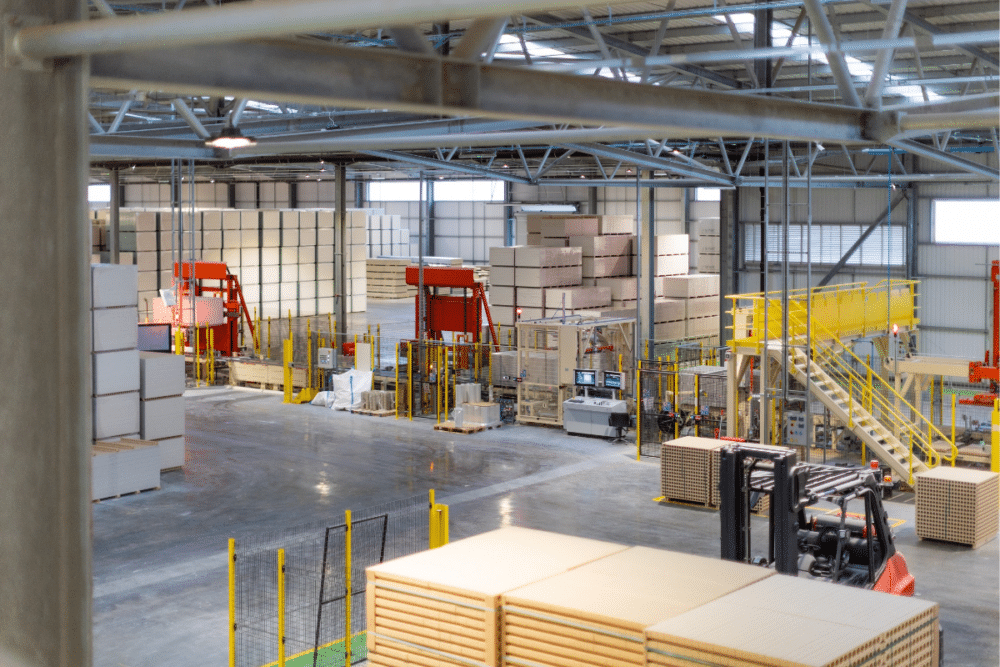
Implanting the Bristol Factory: Overcoming Challenges and Strengthening Local Production
The new Bristol facility is a major investment for Etex. It represents over €200 million (GBP 170 million) and solidifies the company’s commitment to the UK construction market. While the grand opening took place last week, the plant began commercial production in October 2024, following a phased commissioning process. Christophe David, Chief Manufacturing Officer, who supervised the entire construction, explained the timeline:
“We started with dry commissioning, followed by wet commissioning with raw materials, and then we entered full production in the second half of 2024. By October, we were commercializing products.”
Despite the excitement, the journey wasn’t without its challenges. The COVID-19 pandemic caused delays and spikes in material costs, particularly in steel, which was essential for constructing the plant’s large infrastructure. In addition, coordinating the building and equipment installation phases was a complex operation.
“Managing the interfaces between building and engineering was a big challenge,” said David. “We spent a lot of time planning to ensure that equipment could be installed while finishing work was still ongoing, helping us meet our deadlines.”
With this new facility, Etex can now produce 98% of the plasterboard needed for the UK market locally. The company will significantly reduce imports from Spain and France. This move not only enhances supply chain efficiency but also supports sustainability by cutting down on transport-related carbon emissions.
Key Features: Advanced Production Line and Heat Recovery Systems
The Bristol plant is equipped with the most efficient plasterboard production line in Europe. It is characterized by high speed, advanced technology, and energy-efficient processes. One of the key innovations is the factory’s high-speed line, which maximizes productivity without requiring additional labor.
“It’s a high-speed line, so you have the same number of workers whether the line is fast or slow. The scale effect makes it very productive,” David shared.
In addition to the high-speed production line, the factory integrates a sophisticated heat recovery system to optimize energy use. During the calcination process, where gypsum is heated to high temperatures, heat exchangers capture and reuse the “fatal heat” that would otherwise be lost. This system is also applied to the drying process, where hot air is circulated back into the system to reduce energy consumption.
“We’ve put the best heat recovery technologies in place,” David explained, noting that these systems help keep energy use to a minimum while maintaining production output.
Etex has two patents for advancements in its heating equipment. The company is always looking to improve its carbon footprint.
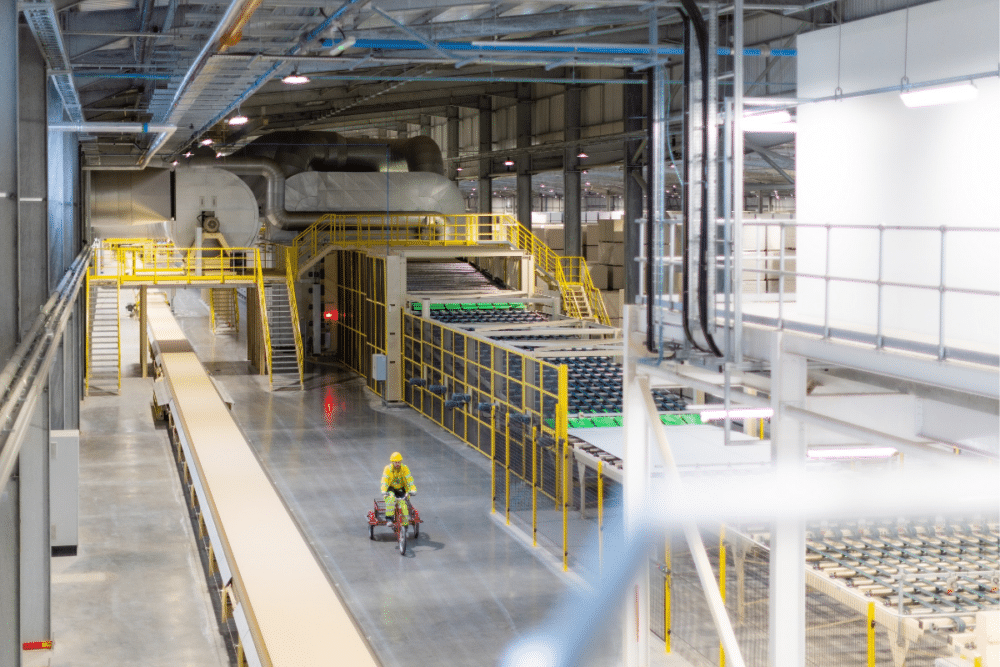
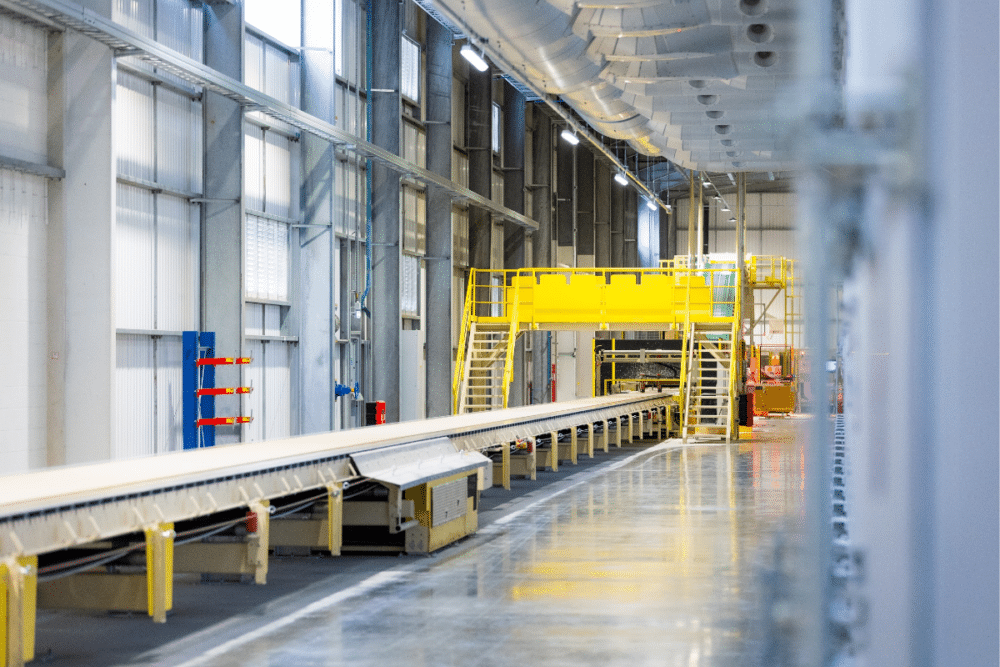
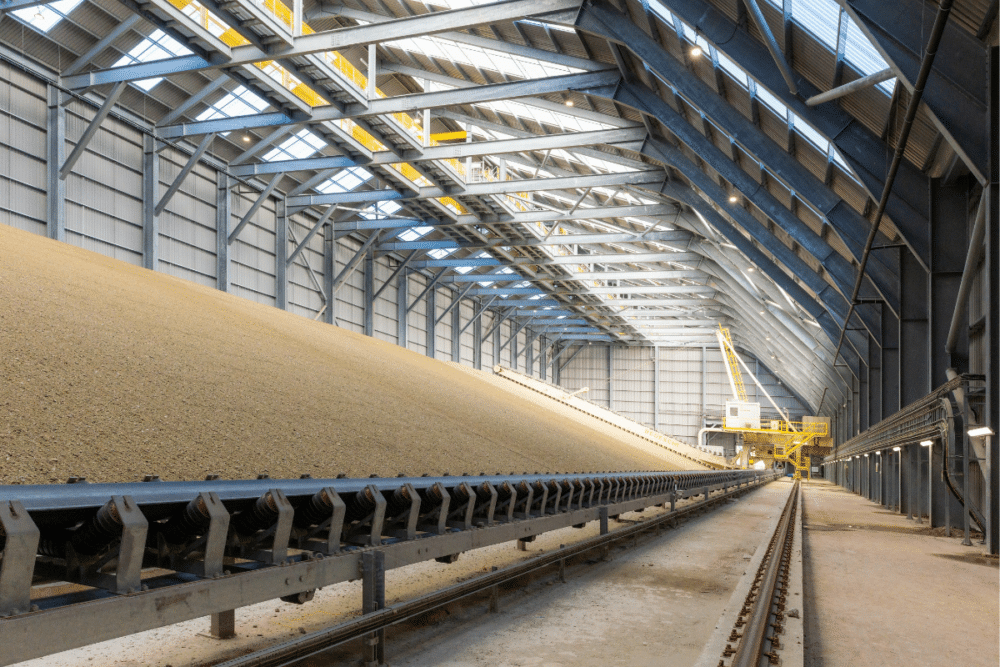
Zero-Waste to Landfill: Pioneering Sustainability
Sustainability is at the core of Etex’s operations in Bristol. The factory is designed as a zero-waste-to-landfill site. This means that all production waste is either recycled back into the manufacturing process or reused in other ways. The factory starts with 30% recycled gypsum in all its boards from day one.
“What’s unique about this plant is that we designed it from the beginning to use 30% recycled gypsum,” said David. “It’s a technical challenge, but we’ve managed it from the start.”
The recycling process doesn’t stop with in-house waste. The plant also sources gypsum from construction sites and demolition projects, further supporting its sustainability goals. This closed-loop recycling system ensures that no gypsum waste goes to landfill, setting a new standard for environmentally responsible manufacturing.
Energy efficiency is another key focus. In addition to the heat recovery system, the factory plans to install solar panels on its expansive roof to further reduce its reliance on traditional energy sources. Rainwater harvesting systems are already in place. But David mentioned that, despite Bristol’s rainy climate, this only meets 15-20% of the factory’s water needs due to the high demands of the plasterboard production process.
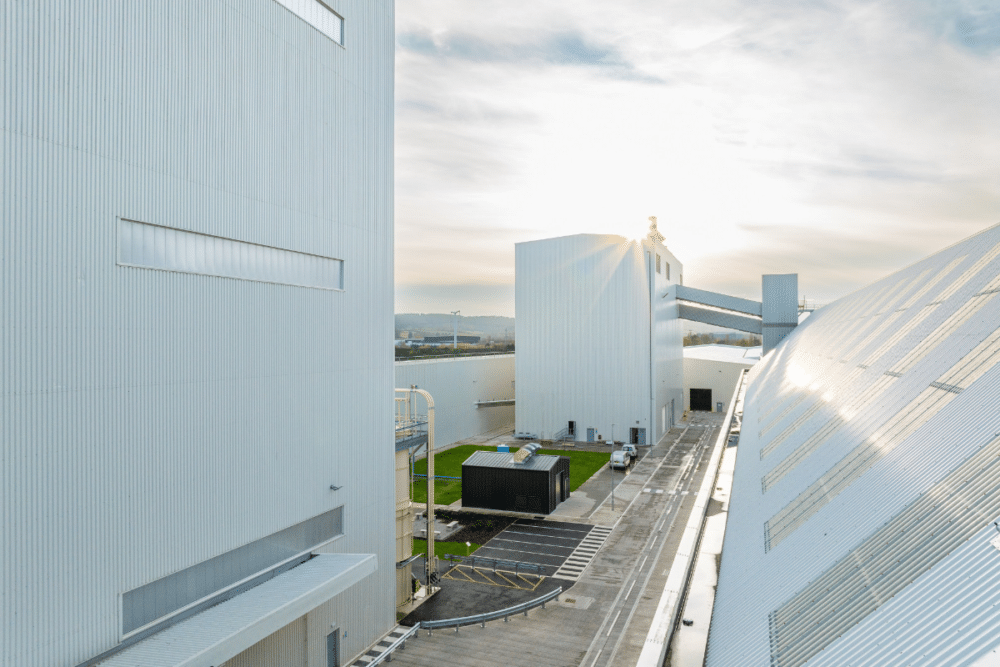
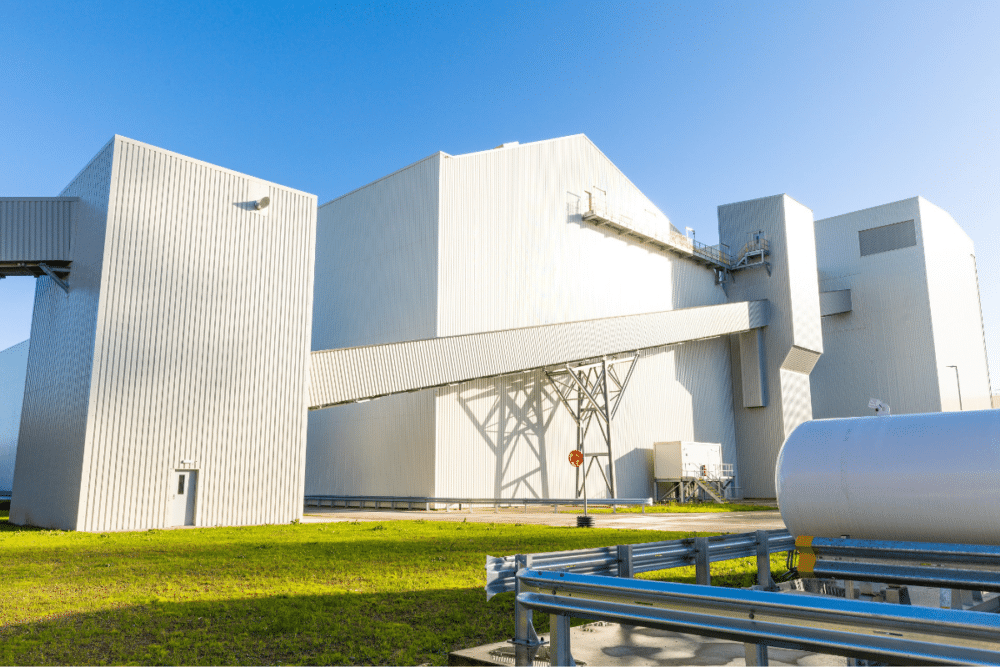
Looking Ahead: Achievements and Announcements
Etex’s achievements in Bristol are a reflection of its broader commitment to sustainability and innovation. The company has already announced that it will continue to expand its recycling efforts globally. At the press conference, Etex unveiled a new plasterboard product made with 100% recycled gypsum and 99% recycled materials overall. While this product is currently being manufactured exclusively in France, it highlights the company’s ambition to push the boundaries of sustainable construction materials.