Alain Noordover, Business & Product Development Manager at SKF, shares his insights on lubrication practices and offers a comprehensive guide to help you effectively manage your lubrication strategy.
I have recently heard someone saying: “Lubrication, pfff? There is always so much to be improved….” This sentence still resonates in my mind.
When we know that poor lubrication practices and contamination account for 50% of premature rolling bearing failures and even more if we consider industrial chains, for instance; when we know that proper lubrication is part of the foundation of any maintenance program; when we understand that a lubricant should get clean and dry into a bearing– why do we still have so much to improve?
For almost 20 years, I have been working on lubrication, and very little has evolved, at least in the field. Yes, a few new lubricants, tools, or lubrication system components, and a few lubrication management software tools appeared here and there. However, the essential outcome is almost identical to what happened 20 years ago and perhaps even longer.
In many cases, if lubrication is not performed appropriately, then this could result in tremendous capital, resources, and human and environmental waste. This is unacceptable, especially at a time when the environment (CO2 emissions, biodiversity, etc.) is at the core of our concerns.
Did you know that 20% of all energy used worldwide is used to overcome friction losses? Although this is almost “inevitable,” poor lubrication practices contribute to this figure, and acting on them could have a positive effect on a large scale.
Also, a significant part of any country’s yearly GDP (a couple of % points) is used to replace worn parts yearly…
Finding a domain with so many incentives to improve isn’t easy, and a lot can be done already today.
What is Lubrication, and How Does it Work?
Simply put, lubrication is an activity that reduces friction and wear of surfaces in relative motion by avoiding metal-to-metal contact. To do so, a lubricant is placed between those surfaces. The lubricant could be solid (graphite, for example), liquid (oils), semi-solid (greases), or gaseous (air). These lubricants have a specific viscosity (resistance to flow) that, combined with the relative speed of the mating surfaces, the load, and the wedge created by the geometry of the components, will create a thin lubricant film.
Such a thin film separates the mating surfaces, lowering friction and wear. The lubricant film is relatively small, in the order of microns or sub-microns; the human eye cannot detect below 40 microns as a reference.
Oils and greases are the most important lubricants used today. Additives can be incorporated into these lubricants to provide certain properties or remove undesirable ones, such as extreme pressure, anti-wear, anti-oxidant, etc. Finally, in the case of greases, a thickening agent holds together the oil and gives the lubricant a consistency, which enables it to stay in place.
Therefore, our industry, transports, vacuum cleaners, almost anything that moves, is working thanks to a micron-thick lubricant film between the bearings, chains, cams, and cylinders in our car’s engines… the components that are providing our today’s lifestyle.
While re-lubricating, we replenish the lubricant to maintain this thin, fragile film. Thinking of it this way, one should be considered a hero when pressing grease into a grease fitting. Isn’t it impressive when you think about it?
Why Is Lubrication Still Poorly Performed?
At first, understanding why lubrication is still poorly performed is needed, and I questioned myself several times on the why.
Is it because it is a dirty and not-so-fun job, after all?
We are talking about handling lubricants – not the nicest material to handle, everyone who touched them already knows – transporting heavy material, walking long distances, and doing repetitive and routine activities. Lubrication routes are also called lubrication routines by the way…
Is it because lubricants are seen as something magical that will only reveal their secrets to some high-level chemists?
Or just that they are that oily/greasy and sticky stuff that you put in somewhere when you think about it, or when bearings start squeaking so loud that you must do something to stop the noise?
Or is it because it is a small part of a company’s maintenance budget (lubricants + tools + labor typically below 10%) and therefore tends to be neglected? It could be considered a cost rather than an opportunity.
Is it because of a need for more knowledge and skills, both at an operational and management level, when it comes to lubrication?
It could also be because lubrication involves countless tasks – an average of four to five jobs per year per lubrication point – that all need skills and best practices to be accomplished. And the management of these tasks and skills is only sometimes optimal or even at hand.
When you want to know your health status, you would go for a blood test, analyze, interpret the results, and take corrective/proactive actions based on the results. How can this be applied to lubrication? And can it even be done on-site?
Finally, what do we measure when it comes to lubrication? Sometimes lubricant consumption, but is this metric enough to know if your lubrication program is performing well?
To answer our initial question on why lubrication is still performed poorly, the most probable answer is that some of the above play a role, which can differ from company to company. Yes, lubrication is not a nice job in general. It is a small part of the maintenance budget. Yes, lubricants can be intimidating or seen as commodities that only differentiate based on their color and so on…
Based on the above, we can also start to see that lubrication is not a succession of numerous dissociated tasks but something that should be seen as a process and a living program. And for sure, it should be treated as such.
What Happens When Lubrication Goes Wrong?
Let’s have a look at two actual examples.
1/ Vertical rolling mill wheel rolling bearings in the cement industry
An end user faced a failure of expensive SRBs (Spherical Roller Bearings) in a vertical rolling mill in the cement industry. These bearings are one of the most critical assets in a cement plant, although the stock of raw material in silos can afford to have some non-operating time for maintenance.
When investigating the reasons for this failure, we found that four different lubricant names were attributed to the different parts of the lubrication management program (lubrication plan, tag on the asset, oil analysis report, and lubricant available in the storage room). In the end, the wrong oil was added to the bearing. An oil with a viscosity 20 times lower than the one required, thus not enabling the formation of the oil film we discussed earlier.
Metal-to-metal contact occurred shortly, and the bearing started to wear off, resulting in premature bearing failure. In this case, a lack of consistency between the different parts of the lubrication management program led to the wrong lubricant being added to the asset leading to a failure that immobilized the asset and incurred costs up to 5% of the yearly maintenance budget.
2/ Salt press in the food and beverage (F&B) industry
An end user faced a specific issue during the manufacture of solid salt bars (pellets type) occasionally every two weeks. The grease was dispensed via a vintage lubrication system into the medium/large SRBs and leaked into the final product. This grease contained solid lubricant graphite, black in color, and was not food and beverage (F&B) approved, which was required. In addition, the sealing proved defective and led to salt ingress into the bearings, mixing with the grease and destroying it simultaneously (grease and salt are not a good mix).
Due to this issue, the asset had to be stopped every two weeks for 8 hours for cleaning, which is a cumbersome job with greases in general, even worse when graphite additives are present. This resulted in product rejection, extra labor, and, more importantly, loss of production. This was critical as the demand for this product increased, and everything produced could be sold. Here, proper lubricant selection, lubricant application, proper sealing, and monitoring of the asset via vibration and grease analysis solved the situation.
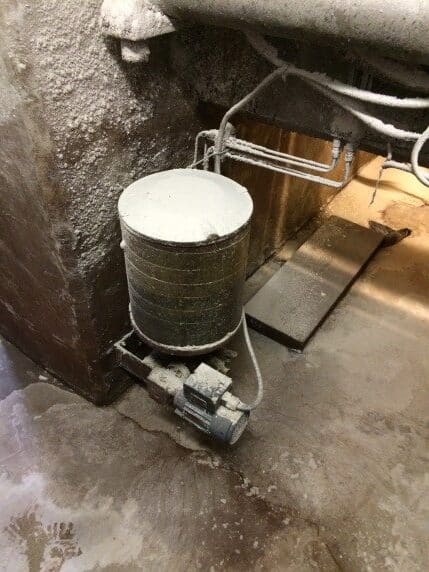
These two short examples – however, there are countless more, take a look at your premises – show that “small” lubrication issues can lead to high costs, loss of production, and extra labor, all affecting both the top and bottom lines of any company.
What Do We Mean When We Talk About Lubrication Management?
The definition we give to lubrication management is the following:
“Lubrication management is the proper organization of resources to effectively and efficiently improve reliability, reduce inefficiencies and costs and increase safety and environmental compliance.”
Or in short, lubrication management is a process to minimize capital, resources, human time, and health waste, as well as environmental impact through fewer CO2 emissions and material release.
We use the lubricant life cycle model to visualize the different parts of lubrication management (Figure 2).
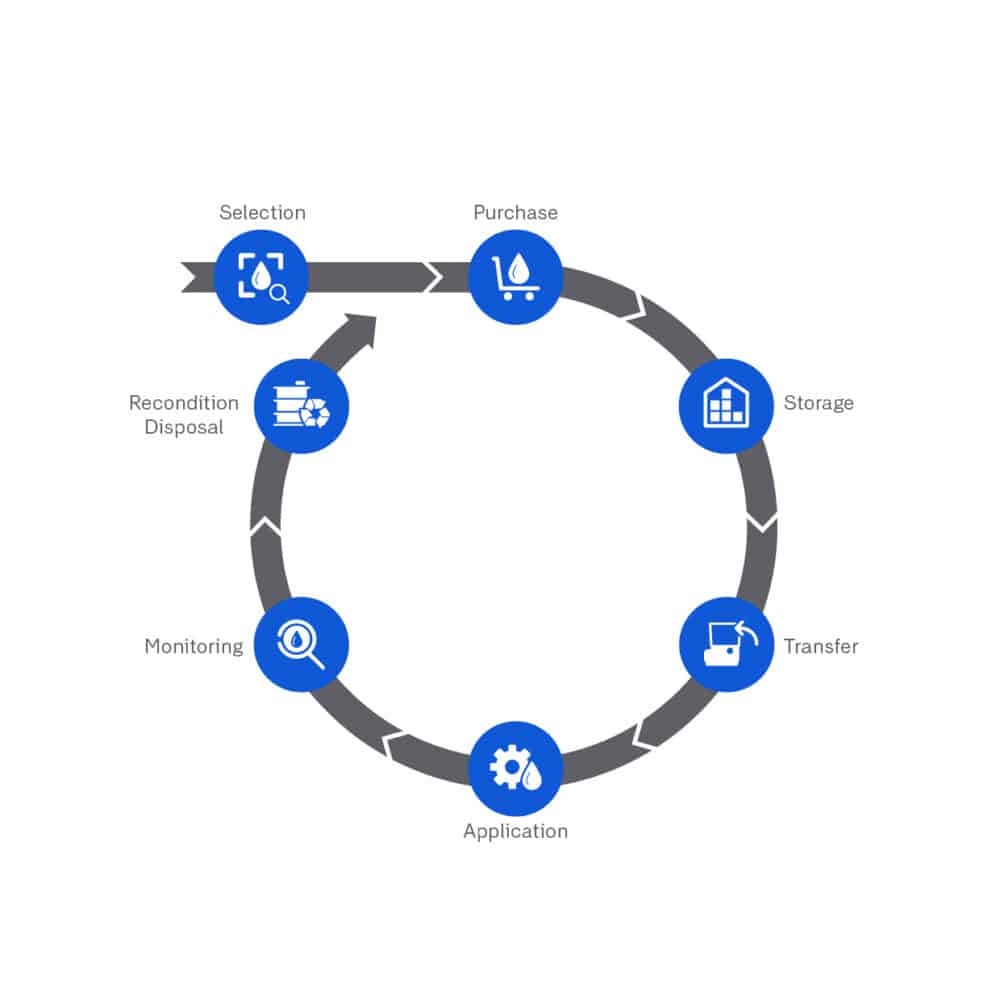
This model comprises the following elements:
1/ Lubricant selection
First, you must select the right lubricants for your assets. How do we select the lubricants? Based on engineering guidelines depending on component type and geometry, speed, load, and temperature, to name a few of the crucial parameters to consider for lubricant selection, based on OEM recommendations or obscure marketing speeches? Are the lubricants suited to the different assets?
Selecting a grease can be a delicate process. SKF has developed several tools to facilitate the selection of the most suitable lubricant. The wide range of tools available includes easy-to-use application-driven tables and advanced software allowing for grease selection based on detailed working conditions. SKF LubeSelect for Greases provides a user-friendly online tool to select the right grease and suggest lubrication frequency and quantity while considering the application’s particular conditions. General guidelines for typical greases for different applications are also available.
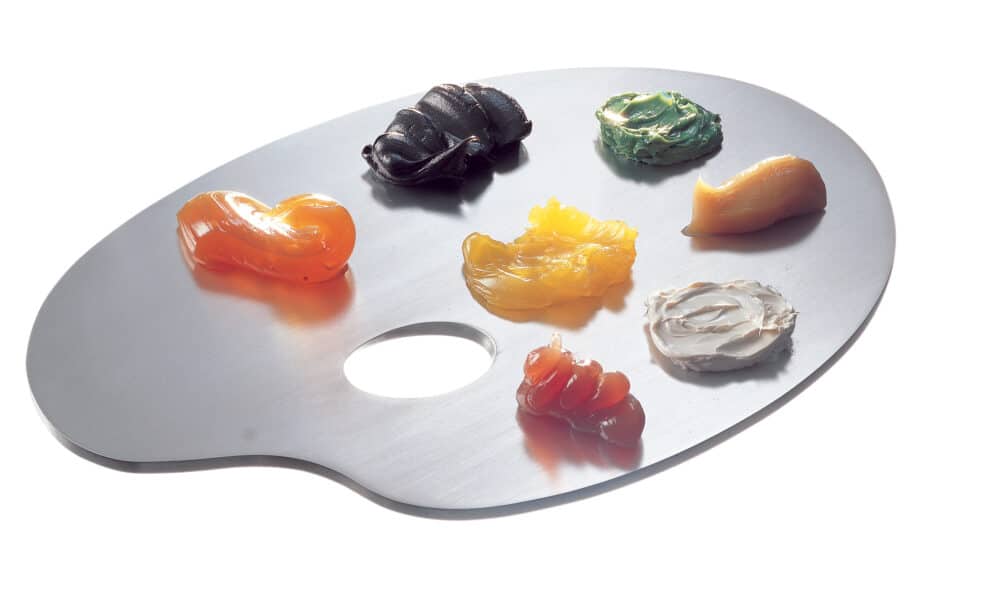
2/ Lubricant purchase
Next, you would need to acquire these selected lubricants by choosing suitable vendors who deliver on time and with consistent product quality. Also, the number of lubricant suppliers should be considered, not selecting only one but not too many either. The partners should offer lubricant consolidation and services, such as training, tools and equipment, and software.
3/ Lubricant storage
Most likely, these lubricants will not be used immediately. Therefore, ensuring proper storage for a certain time is vital. Experience shows that lubricants could degrade during storage if it is not performed correctly. The right temperature, humidity, and possible exposure to contaminants via the wrong tools and equipment are mandatory points to consider. Even when drums and pails are still sealed, lubricants can degrade even before they are supplied to the assets. Often, it is necessary to rework the storage room(s) layout and its different main components, like oil and grease storage and dispensing and the related tools and equipment.
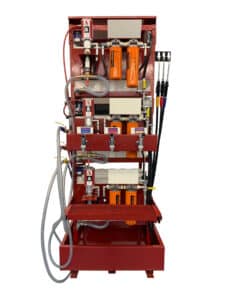
4/ Lubricant handling
The lubricants are received in different pack sizes, from totes and drums to cartridges. They must be transferred to the various lubrication tools, equipment, and systems. We need to ask ourselves; how do we ensure that this process avoids the intrusion of contaminants and lowers the risks of lubricant cross-mixing? Are our tools & lubrication points marked and color-coded? Do we have enough of them for the different lubricants? Are the tools clean?
Here, proper and identified tools and equipment are again of prime importance, including the prefiltration equipment of oils, for instance, or simpler devices, like grease gun filler pumps, which enable you to create a closed environment where lubricant hardly gets exposed to the environment, limiting thus contamination ingress during this process.
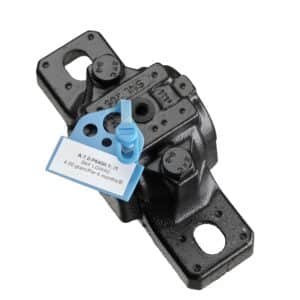
5/ Lubricant application
These lubricants are now applied to the assets. How is this being performed? By hand, simple tools, or via a semi- or fully automated lubrication system? How do we monitor the quantities and the relubrication intervals? Does the lubricant go where it is required to go? Do we insert more lubricant at long intervals or less lubricant at shorter intervals? What are the required skills of people performing these activities?
Manual lubrication tools using grease meters will help to control the right amount of lubricant supplied to the bearing. For applications located at difficult access places, automatic lubrication devices such as the connected single-point lubricator, the TLDD series, which is part of the SKF SYSTEM 24, could help to provide the required lubricant automatically and enhance the user with a remote monitor system where the user can verify the lubricator status, and alert you when to refill them or troubleshoot them. Selecting the right type of lubrication tool is assisted using the SKF Dialset, where based on the application conditions, the software will assist you in selecting the proper lubrication intervals and lubricant. An automatic lubrication system is an obvious solution for more complex multipoint applications to reduce manual lubrication tasks, improve safety and reliability, and provide many other benefits.
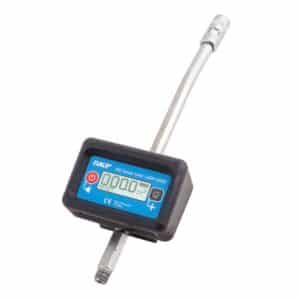
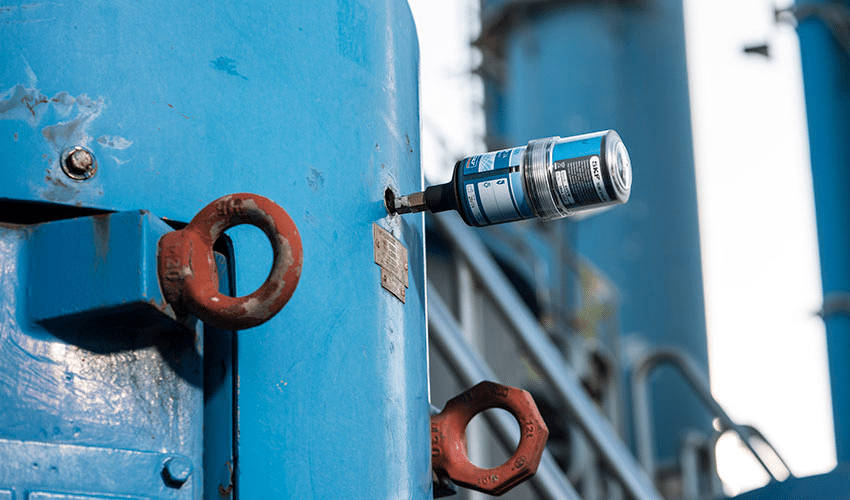
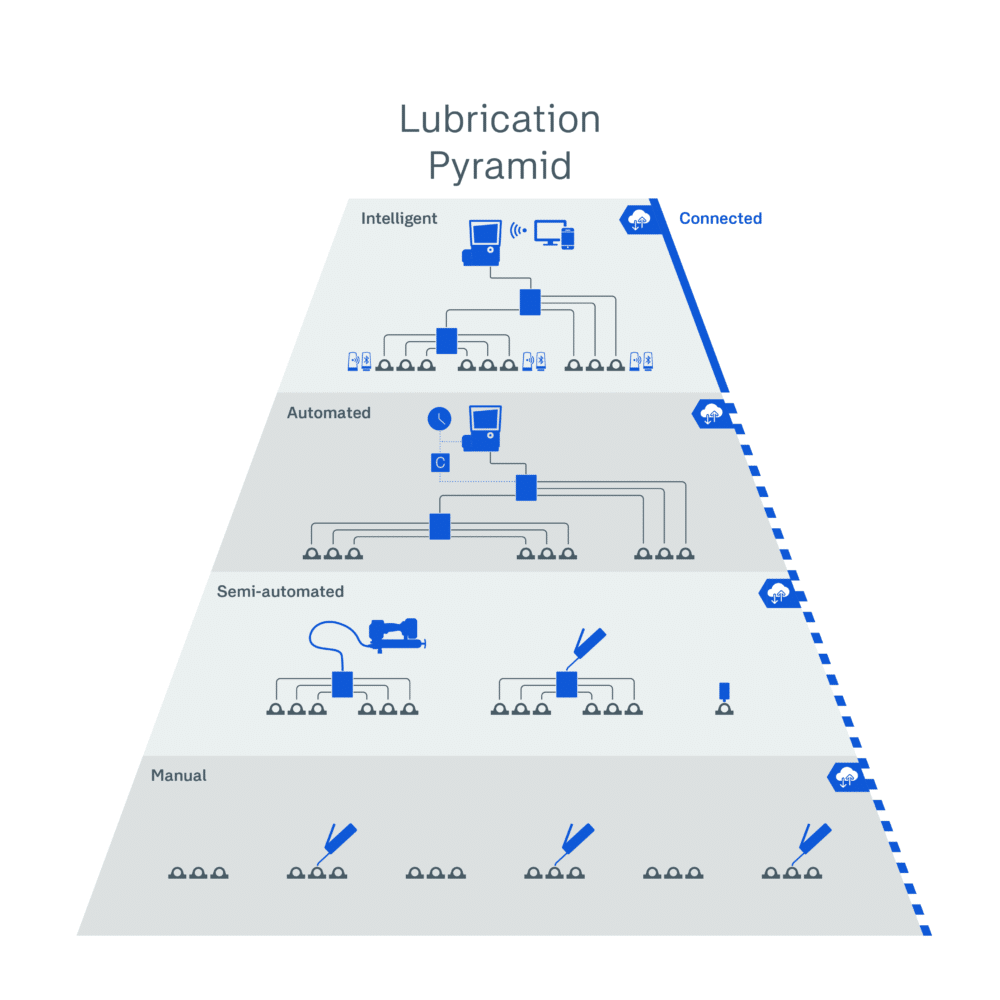
6/ Lubricant monitoring
The lubricant is inside the asset and hopefully lubricates – if not, you should notice it quickly. How do we know that it lubricates well enough? Monitoring lubricants, commonly called oil or lubricant analysis, enables us to understand if a lubricant performs as it should and will continue to serve as it should. It also gives information on the state of our components via wear material analysis.
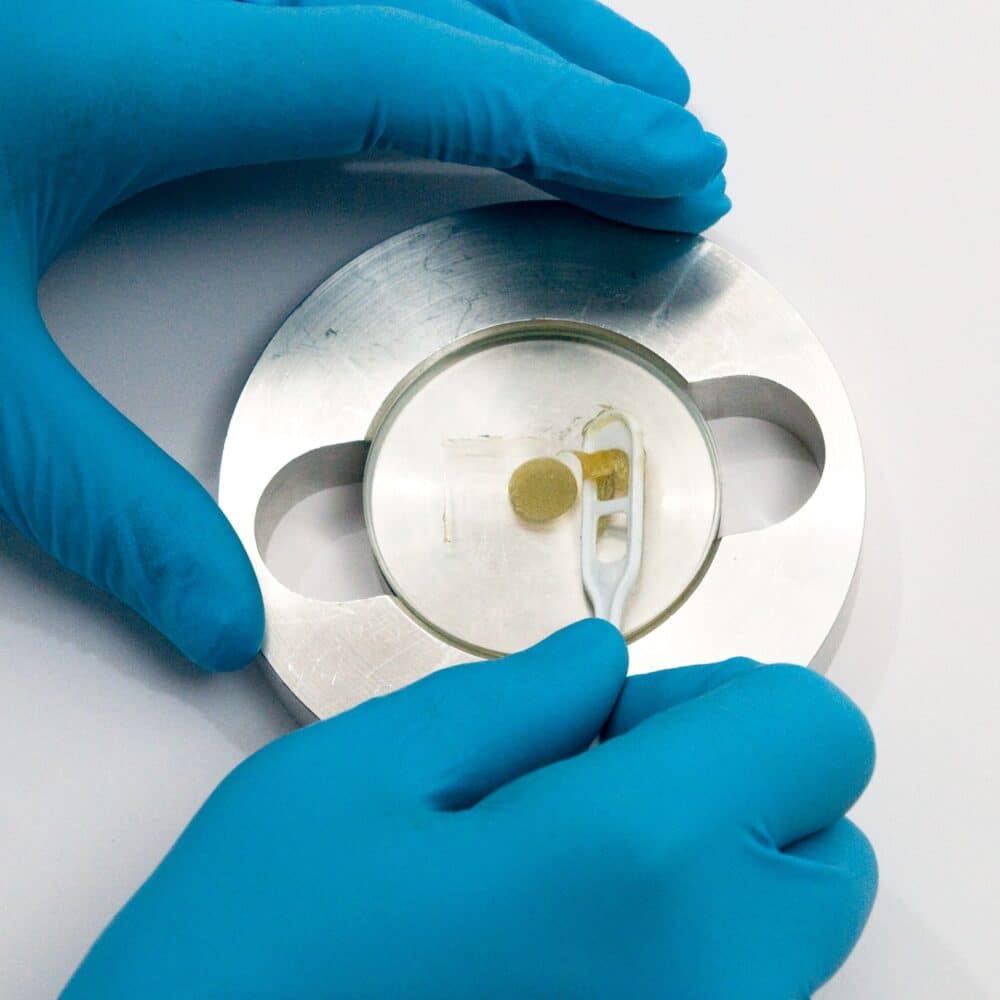
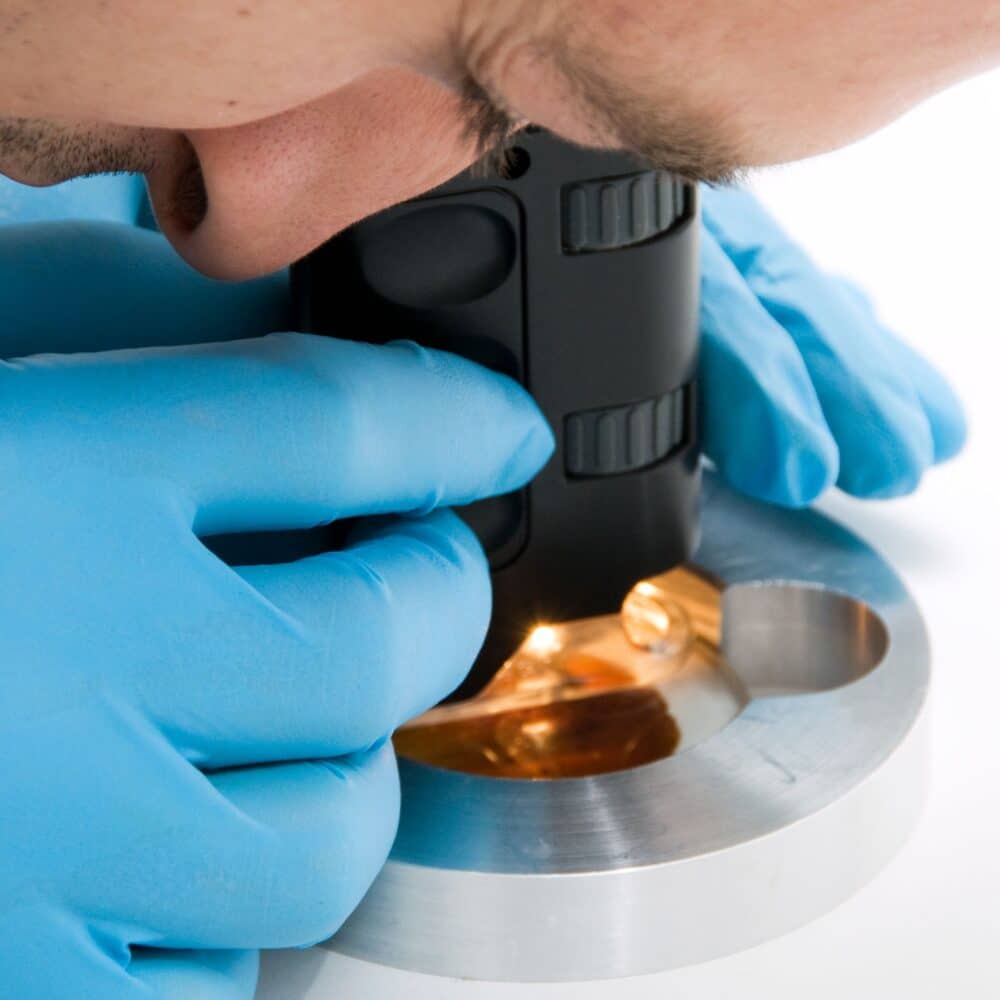
Numerous issues such as leakages, contamination ingress, overheating, unbalance or similar can be detected with monitoring techniques, including visual inspection, vibration analysis, thermography or ultrasound. Being aware of potential issues, we can take predictive and proactive steps to minimize damages and prevent them from reoccurring later. One obvious goal of lubricant monitoring is to maximize the lubricant lifetime in the asset.
Combining these methods is the best way to perform predictive maintenance. When working with external partners, the more these partners can offer integrated technology and services like vibration and lubricant analysis, the better. Their knowledge of rotating equipment maintenance is paramount.
7/ Lubricant disposal or reconditioning
In the end, the lubricant will be used up and must be replaced. The monitoring step allows us to know better when this change should occur. Now, what do we do with these used-up lubricants? How do we even collect them and address leakage? How do we make sure they are not released into the environment? And when we manage to collect them, what do we do with them? Are they collected properly according to the regulations in place? Can we recondition and reuse these lubricants when taken out of the application?
Before disposing of lubricants, especially in the case of oil, everything should be done to maximise their service life in the application. In the case of circulating oil lubrication, devices such as the SKF RecondOil box offer a great way to do that.
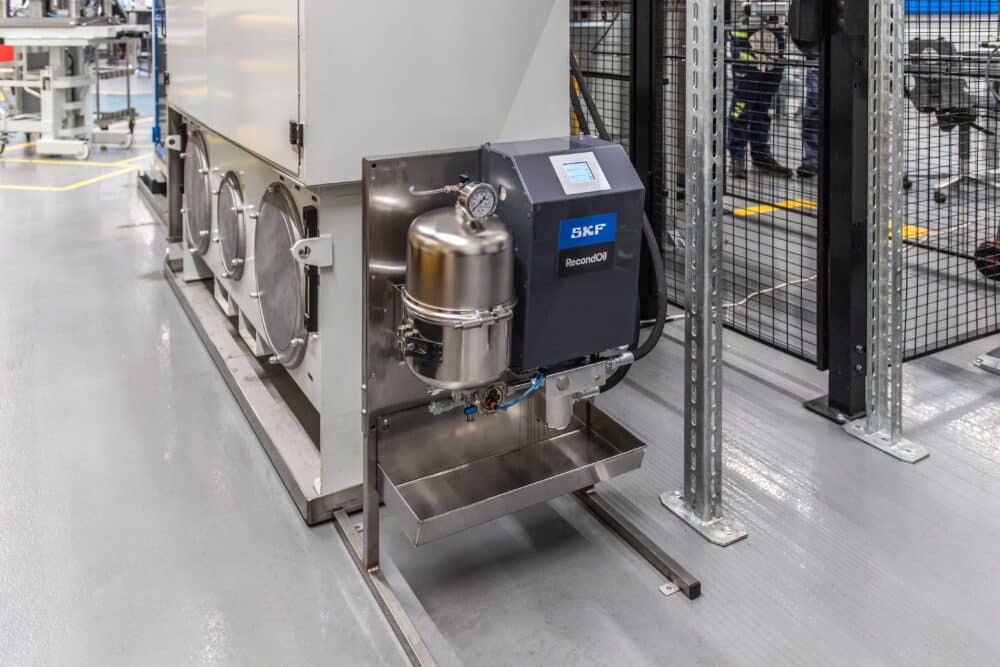
8/ Close the loop
What we learn from following the lubricant life cycle would help to close the circle. In the shown model, we link to lubricant selection again. Learning could help in selecting different lubricants based on the results of the condition monitoring stage or decisions made in the disposal/reconditioning stage. However, we could also loop directly to the purchase phase or any other step. Remember, this is a simple model helping to visualize the different parts of lubrication management.
So, we explained the lubricant life cycle, but one can observe that crucial parts are still missing here. The full lubrication management model looks rather like in Figure 12:
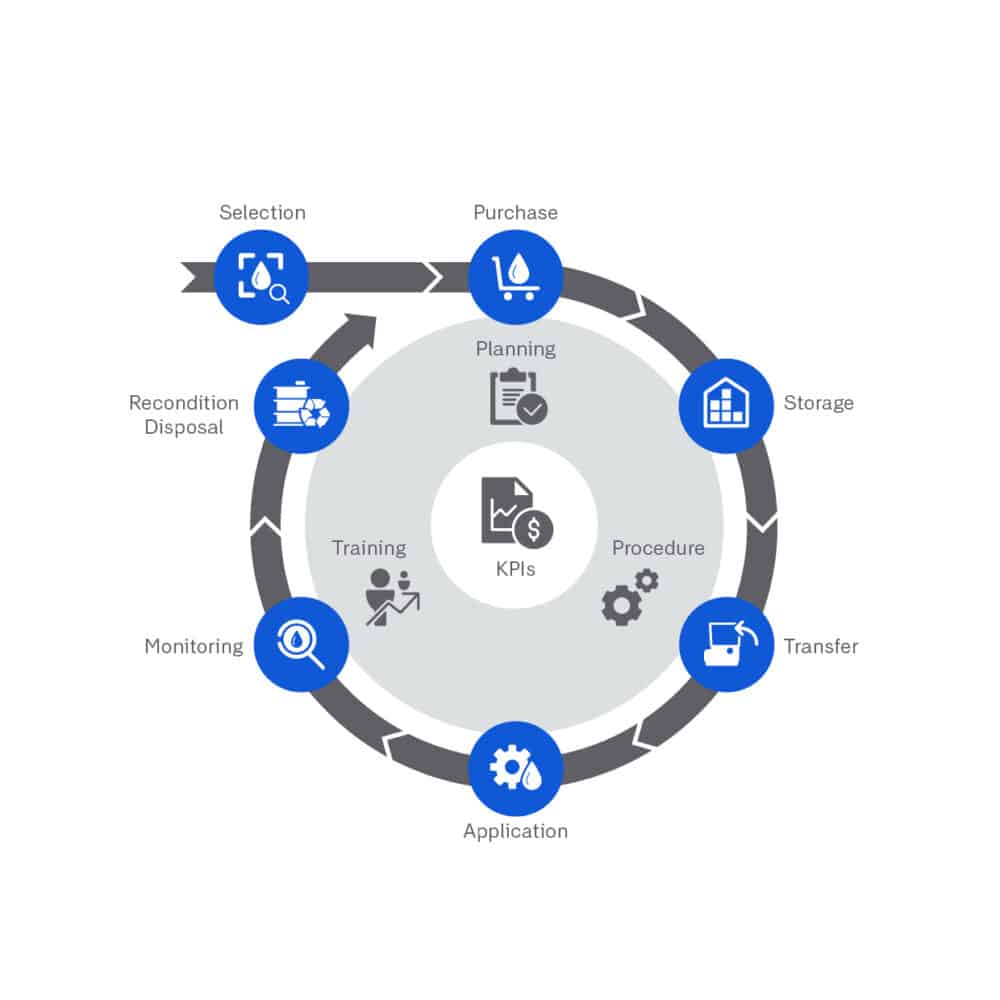
In this model, we add the following parts:
Planning & scheduling
We mentioned before that numerous tasks must be accomplished in a plant. First, we must ask ourselves whether the right tasks are designed (which lubricant, where, how much, how often, which method) and if they are required or could be removed/replaced by something else. And second, how do we schedule those tasks such that the workload stays manageable? Finally, how do we ensure to receive feedback on the accomplishment of those tasks and how deviations get reported when they appear?
Dedicated lubrication management software can show its value here compared to standard CMMS systems; it would not immerse important maintenance activities together with countless smaller lubrication tasks. This could be managed directly by lubrication supervisors or even technicians, allowing better reactivity and follow-up. SKF Software could be considered.
Procedures
To ensure job consistency and the use of best practices, procedures need to be developed and made available to the staff. Digital documentation of operations helps to update them and make them easily accessible, even remotely.
Most of the time, lubrication technicians perform their activities based on their on-the-job knowledge, whether good or not. Another issue comes from the loss of information in case of skilled technicians’ retirement.
Training & personal development
All the above points mean very little without the skills of the people involved in the lubrication activities. Lubrication should be considered a highly skilled job and should be treated as such, with training, development plans, and follow-up of our people skills development. In some cases, outsourcing lubrication tasks could be an alternative, but choosing a partner with the right knowledge, skills, and technology is paramount. Removing routine, low-added-value tasks and replacing them with more problem-solving, proactive tasks would make the job more interesting (and better paid…), and machinery would feel like they are properly being taken care of.
Management & KPIs
Last, when we look at all of this, what do we measure to know whether we are going in the right direction? This means we must set up KPIs thoughtfully and pragmatically to understand where we are and if what we are changing contributes positively to the situation and addresses gaps when found.
SKF lubrication management software helps you to monitor and visualize critical information easily and enables you to track your lubrication program.
All these points, put together, constitute what we mean by lubrication management.
How to use the model to improve your lubrication practices?
Lubrication is a process that needs to be managed. A lubrication management program consists of many parts touching the fields of tribology, filtration, oil analysis, and management and might initially look overwhelming.
We understand that only some companies have the luxury of having a lubrication expert comfortable in all these domains – anyway, there are, sadly, not enough experts available.
The good news is that significant changes can happen with small, simple and pragmatic activities. This generates the drive to undertake more considerable changes and finding the right knowledgeable partners can greatly help along the way.
So how can we improve?
- Be aware and create awareness. People are essential to make things happen. Nothing will change if understanding is not there.
- Assess your situation today: What is happening in your plant in the different parts we discussed earlier? Are you satisfied with it? Assessment tools like SKF Client Needs Analysis Lubrication Management or SKF Lubrication Audit could be considered.
- Once you know what is happening, build the business case. Use known issues and try to put a price tag on those. Also, use literature to estimate the impact proper lubrication can bring. You can also take a leap of faith. There may be a point where we should stop systematically asking for immediate return on investment and derive complicated implementation plans for a not-such-significant investment. What’s the worst that can happen? Let’s do the right thing. Now.
- Develop people skills. Move people from simply pushing grease somewhere to proactive and problem-solving tasks. You can go a long way with a few hours of awareness, training and follow-up. This little investment in time and effort will make a difference.
- Follow best practices in the different parts of the lubricant management model and derive a pragmatic activity plan. Take your time doing so and assess the outcome on your machines and the people’s morale.
- Set targets linked to the lubrication.
- Continue improving as part of an improvement plan and reassess sometime later.
The Future
Considering today’s world challenges, we see that proper lubrication has the potential to significantly improve the situation. The lubrication management mindset should be used to reach significant results.
Lubrication needs to enter a new era, and it ultimately will. Using proper knowledge, proper devices, digitalization, artificial intelligence, and reconditioning technologies, which are already becoming increasingly available today, will lead to better visibility of the current lubrication state. It will help us make better decisions, allowing us to mitigate the challenges of friction and wear. Ultimately it will allow us to decrease our consumption of resources and energy while at the same time allowing us to maintain our standard of living. Hopefully…
Make a difference, it is in your hands! You can count on SKF to support you in addressing the next step in machine care!