Japanese manufacturer Nagase debuted its Integrex AI system at JIMTOF 2024. This advanced AI solution redefines grinding precision and workpiece measurement in machining. DirectIndustry had the opportunity to test the system while in Tokyo last week.
Built to gather and analyze large volumes of data during the grinding process, Nagase’s Integrex AI system allows for live monitoring, measurement, and predictive insights, all aimed at improving accuracy and minimizing downtime.
How Integrex AI Works: Real-Time Data Collection and Analysis
The Integrex AI system is designed to work with Nagase’s machines, particularly through the NPX spindle, a highly specialized component that captures critical data in real-time during the grinding process. The AI system monitors the grinding force, measuring both vertical and horizontal forces on the grinding wheel. This is combined with torque data, which indicates the stress on the spindle during operation, and measurements of the workpiece straightness. Collecting these data points in real-time allows the AI to form a comprehensive view of the grinding process as it unfolds.
This real-time data is compared to an extensive database of historical grinding data. This results in a model that the AI can use to predict the straightness and accuracy of a workpiece before grinding is even completed. Traditionally, operators would need to stop the machine, remove the workpiece out of it, and take it to a separate measurement device to measure accuracy. Now, Integrex AI enables in-situ measurement, eliminating the need for machine stoppage and manual handling, which are especially labor-intensive for large-scale workpieces.
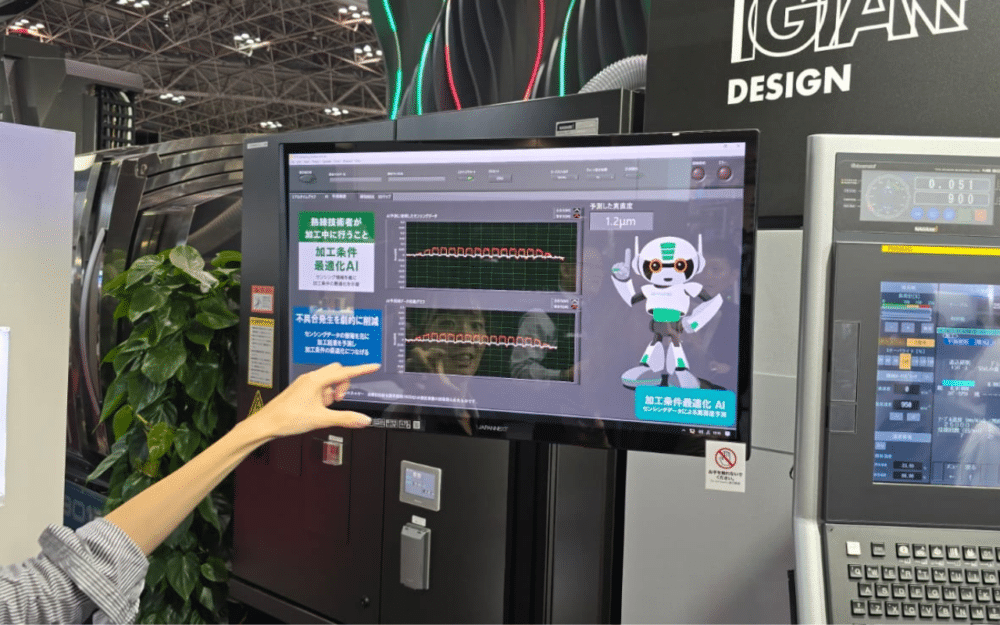
Key Advantages of Integrex AI
Nagase developed Integrex AI in response to customer feedback, particularly from clients who work with heavy, oversized workpieces. Removing these workpieces from the grinding machine just to measure them is not only time-consuming but physically challenging. Incorporating measurement capabilities directly into the grinding process allows operators to verify accuracy without interrupting the machining workflow.
Moreover, because the system continually evaluates the workpiece’s straightness and overall accuracy, operators can make real-time adjustments to maintain desired tolerances.
Besides, Integrex AI also leverages the collected data to perform predictive maintenance. By monitoring patterns and detecting anomalies in the machine’s performance, the system can anticipate potential breakdowns before they occur, helping users avoid unplanned downtime and manage maintenance more efficiently.
Additional Innovations: Predictive Grinding Pressure Mapping and Green Design
In addition to Integrex AI, Nagase introduced other innovations at JIMTOF aimed at enhancing grinding performance and sustainability. One noteworthy feature is a predictive grinding pressure mapping tool. This new capability allows the AI to predict and adjust for grinding pressure, optimizing the process to reduce unnecessary wear and enhance surface quality.
Nagase has also made strides in designing smaller, more efficient machines that minimize their environmental footprint. By reducing the machine size, Nagase lowers material usage and operational costs.
Global Reach and Future Expansion Plans
Nagase’s machines, including those equipped with Integrex AI, are manufactured in Japan and exported to numerous countries, including Korea, China, Taiwan, Germany, Sweden, and Malaysia. While the Integrex AI system is currently offered for specific machines, Nagase has expressed interest in potentially expanding this AI capability across other models in the future, depending on market demand and evolving customer needs.
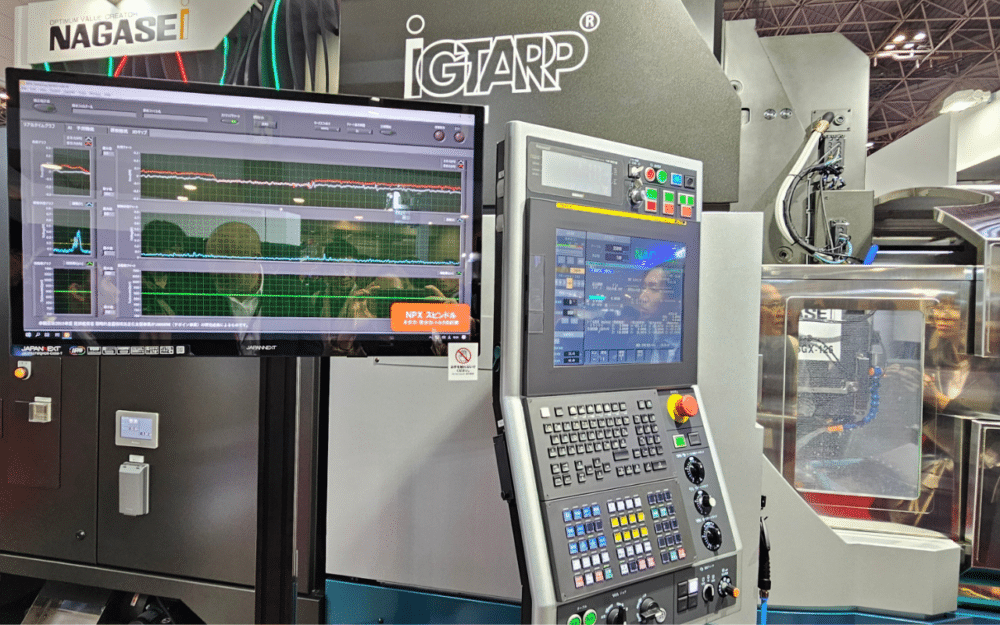