At JIMTOF, DMG MORI showcased cutting-edge advancements tailored to the challenges of modern manufacturing. With a focus on automation, artificial intelligence, and environmental responsibility, the company’s latest machines demonstrate its commitment to reducing energy footprints, integrating processes, and meeting labor demands. We spoke with Shun Kawamura, Group Manager Product Sales Department at DMG MORI to gain insight into their latest innovations and how they are meeting market needs.
Can you tell us about the concept behind DMG MORI’s booth this year?
Shun Kawamura: “For the past few years, our booth has focused on the theme of “MX,” which stands for Machining Transformation. This concept includes four core elements: process integration, automation, digital transformation, and green transformation. Each of these elements aligns with our vision to enhance productivity while reducing environmental impact. Our machines are designed to combine multiple processes into one. This not only simplifies production but also reduces energy use and emissions.”
What are some examples of process integration in your machines?
Shun Kawamura: “One of our highlighted machines at the fair is the INH 63, a five-axis horizontal machining center. It allows manufacturers to handle what might typically require multiple machines in one single system. This saves space, energy, and time. We originally introduced this model at EMO, but this is its debut in Japan. It’s already available worldwide and has been well-received for its versatility.
We also have integrated our AMR 2000. This is an autonomous mobile robot developed to handle tasks that traditionally required human intervention—like transferring chip buckets. We believe chip management is a significant area for automation. AMR can be used for that and not only to move workpieces and pallets.”
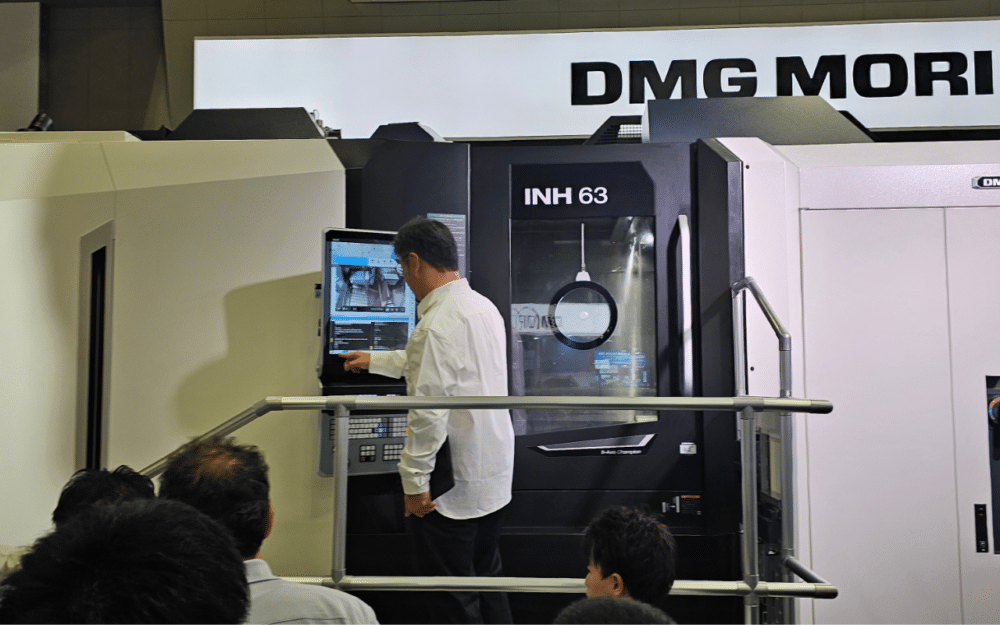
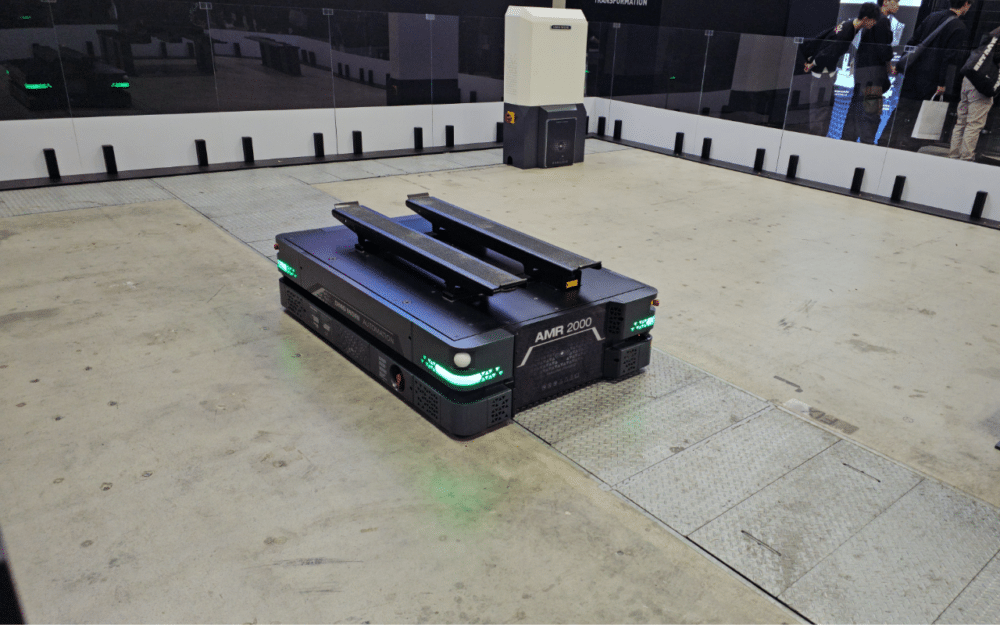
That’s a new trend, machine manufacturers are starting to develop their own AMR. Can you tell us how the AMR 2000 fits into DMG MORI’s strategy?
Shun Kawamura: “The AMR 2000 is designed as a complete solution as it integrates with our machines to automate routine tasks. This solution was developed collaboratively with Zimmer, a European partner, to meet the specific needs of manufacturing environments. It can carry loads up to 2,000 kg, which makes it suitable for carrying chip buckets or even robotic arms if needed. The AMR uses advanced mapping technology to find the most efficient route from point A to point B. This eliminates the need for manual guides or continuous supervision.”
Is artificial intelligence (AI) embedded in your machines?
Shun Kawamura: “Yes, we’ve incorporated AI in ways that directly enhance operational efficiency. For example, our machines have an AI-driven chip removal system. It uses a camera to detect where chips are accumulating and automatically activates a nozzle to clear them out without human intervention. This makes the machining process more efficient and less dependent on operators.”
Will you expand AI applications within your machines in the future?
Shun Kawamura: “Absolutely. We’re exploring additional uses for AI across various functions, like parts measurement and predictive maintenance. Our current focus is on enhancing automation and process integration, but we see a lot of potential for AI to further optimize our machines.”
Environmental sustainability is a growing concern. How does DMG MORI address this?
Shun Kawamura: “Sustainability is at the heart of our “green transformation” strategy. Each of our machines is designed to save on CO2 emissions. For instance, by consolidating processes, we help customers achieve lower energy usage. One machine performing multiple tasks requires less power than several machines performing individual tasks. We also offer a “Green Mode” that reduces energy consumption by shutting down idle components. It is similar to the auto-start-stop feature in modern cars. When not actively machining, motors and other systems enter a low-power state. This significantly reduces energy draw.”
Can you give us any figures?
Shun Kawamura: “The exact savings vary based on usage patterns. But we can say that this feature is a valuable tool for reducing unnecessary power consumption.”
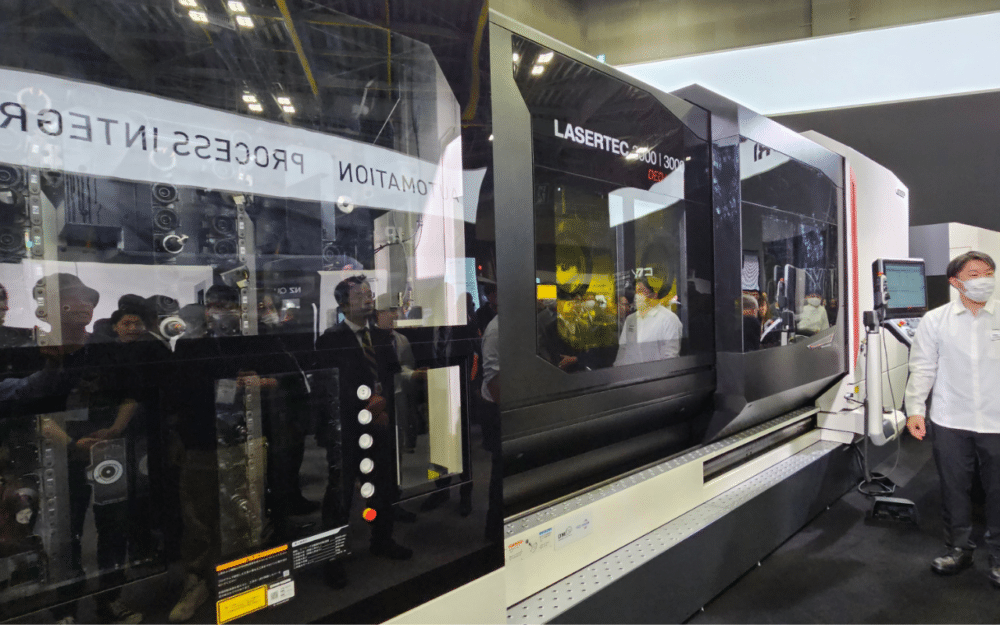
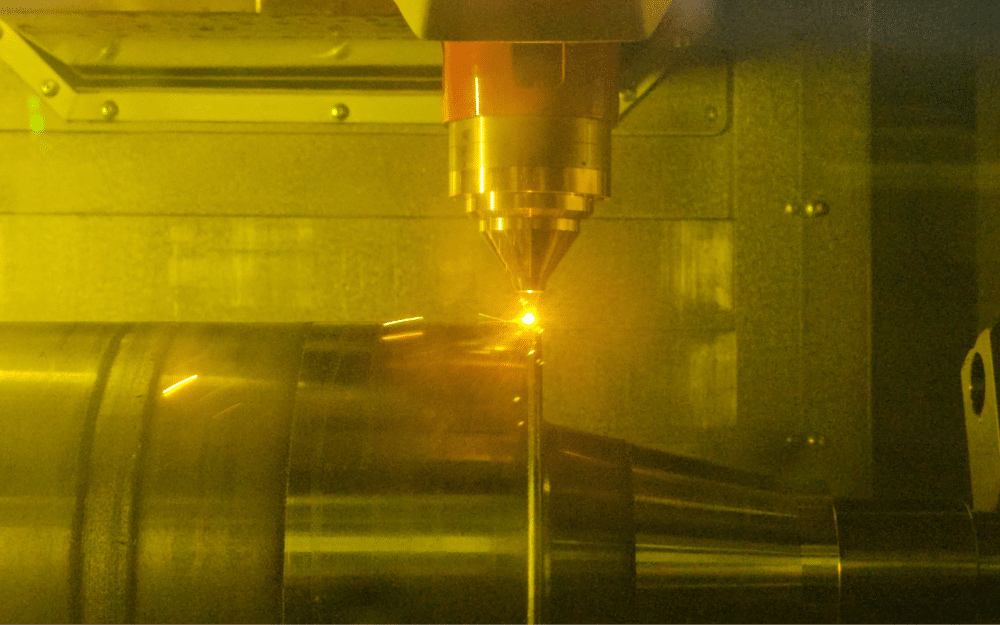
Are you involved in additive manufacturing (AM)? If so, what are some practical applications?
Shun Kawamura: “Definitely. Our LASERTEC 3000 DED hybrid machine, for instance, combines machining and additive manufacturing capabilities. This machine is ideal for repair work, such as adding material to worn parts instead of replacing them. It allows for cladding and coating applications in industries like aerospace and automotive, giving manufacturers the flexibility to repair or enhance components directly on-site. It is not aimed at making pieces from zero.”
Q: How is the LASERTEC 3000 DED hybrid machine unique in terms of applications?
Shun Kawamura: “This machine was developed based on customer feedback. It’s particularly well-suited for long workpieces, such as dye rolls in manufacturing, where coatings or repairs can now be applied in a single process. This process integration allows customers to avoid sending parts to different vendors for additional treatment, reducing both turnaround time and costs.”
Are these features unique to DMG MORI, or are competitors offering similar capabilities?
Shun Kawamura: “These features are unique to DMG MORI, especially our in-house solutions with DED (Direct Energy Deposition) technology. For example, our spindle drawbars were previously manufactured through multiple processes, including roughing and heat treatment, which took around 14 days. Now, with DED, the process has been streamlined to just two hours. This represents significant time and cost savings for us and our customers.”
Is there anything else you would like to highlight that’s new or a world premiere?
Shun Kawamura: “Yes, one more exciting innovation is our NLX 2500|700 Second Generation, which we recently premiered at the AMB trade show in Germany. We are now showcasing in Japan for the first time. This second-generation model has several key upgrades over the first generation. For instance, we’ve enhanced spindle power on both the left and right spindles. Previously, customers found they could only perform heavy roughing on the left spindle and reserved the right spindle mainly for finishing. With the new model, both spindles have the same power. It means that roughing can now be performed on either side, offering much greater flexibility and efficiency.
This model also supports larger bar feed diameters—up to 105 millimeters, or roughly four inches—which enhances its automation capabilities. Additionally, we’ve increased the milling spindle RPM from 10,000 to 12,000, allowing for heavier milling with higher torque and output. In many ways, this machine’s milling capacity is now comparable to our CMX vertical milling machine series, further expanding what customers can achieve in a single machine.”
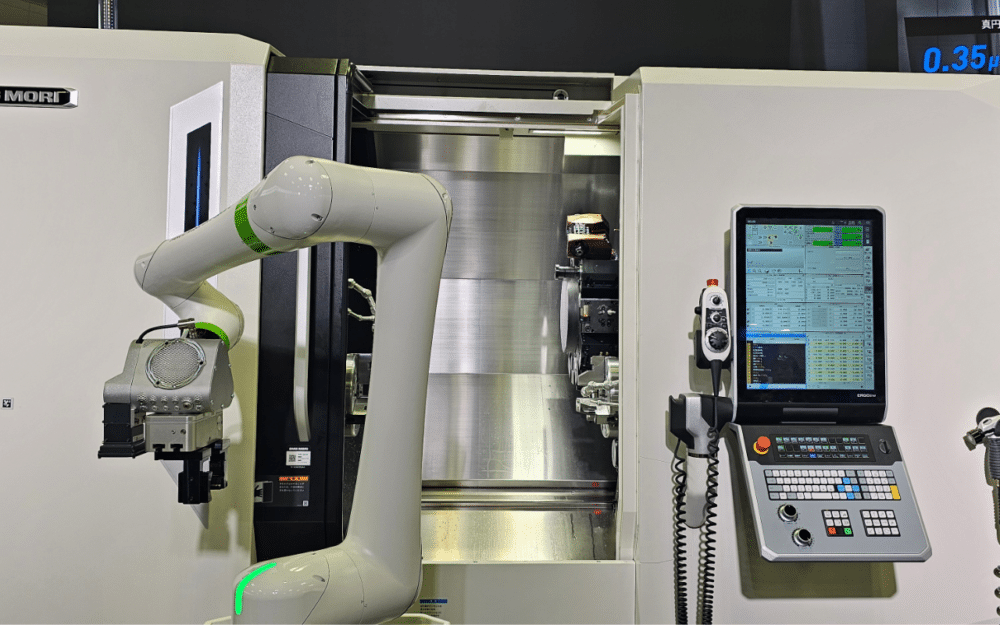
Are DMG MORI machines designed specifically for certain industries, or are they more versatile?
Shun Kawamura: “Our machines are multipurpose by design, though certain models may have features that make them particularly suitable for specific sectors, like aerospace or oil and gas. For example, our DMU 50 five-axis vertical machining center is frequently used in the medical industry due to its precision capabilities, but it’s equally at home in other industries that require high accuracy and reliability.”