Micro Additive Manufacturing continuing to establish itself as the go-to technology option for manufacturers. Ziki Peled, GM – Additive Division at Nano Dimension, looks at its potential to transform the way miniature polymer parts are designed and produced.
In recent years, additive manufacturing (AM), has made significant strides in transforming traditional manufacturing processes. Among the various applications of 3D printing, microadditive manufacturing (Micro-AM) has emerged as a disruptive force in the production and prototyping of microplastic products and components. This technology has the potential to revolutionize the way manufacturers design and manufacture miniature plastic parts for a wide range of industries. These include electronics, medical devices, aerospace, and more.
Some of the most advanced Micro-AM hardware systems available on the market enable designers and manufacturers to exploit the ability that exists through 3D printing to build complex parts in small, medium, and high volumes in a timely and cost-effective fashion.
Redefining Prototyping for Microplastic Products
Historically, producing prototype runs of microplastic products has involved expensive and time-consuming processes, such as micro-injection molding or micro-machining. These traditional manufacturing processes typically require the creation of specialized molds or tooling. This makes it impractical for small-scale production or rapid iteration. Micro-AM, however, introduces a cost-effective and “rapid” prototyping solution for microplastic components.
With Micro-AM, designers can directly translate their digital designs into physical objects with minimal lead time. This capability accelerates the product development cycle, allowing for rapid iterations and design improvements. Additionally, the lack of expensive tooling requirements and reduced material wastage compared to traditional manufacturing methods significantly lowers prototyping costs. As a result, even small businesses and start-ups can explore innovative ideas without breaking the bank.
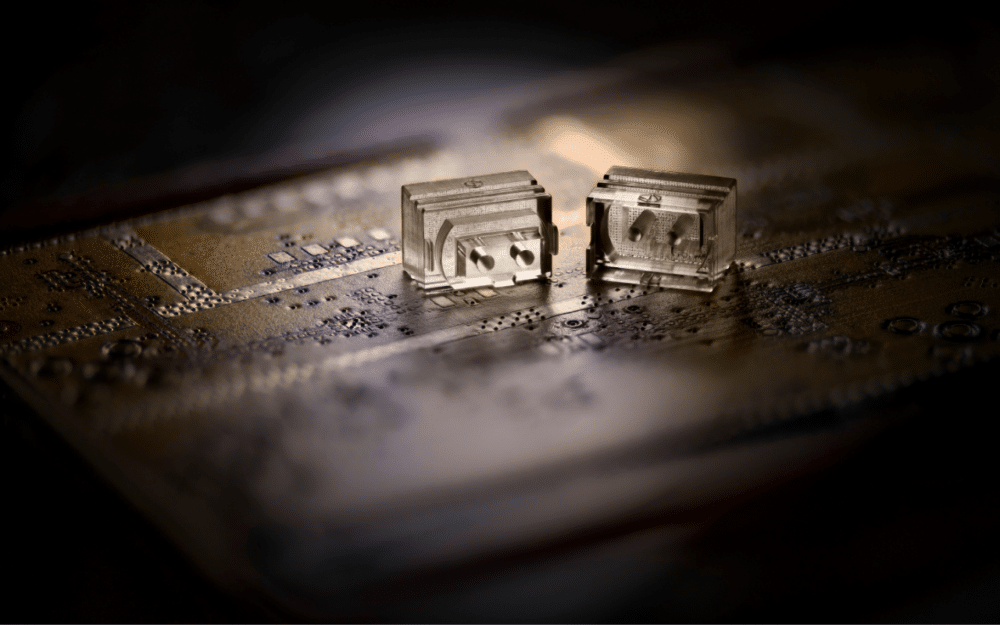
Complex Geometry and Customization
Micro-AM’s ability to produce functional prototypes with complex geometries also facilitates the validation of designs before full-scale production. Engineers can test various designs, dimensions, and tolerances without incurring substantial costs or long lead times. This iterative approach enhances the quality and reliability of final products. It enables to identify and rectify potential issues at the early stages of development.
With Micro-AM, designers are no longer constrained by the limitations of conventional machining or molding processes, which often restrict the shapes and geometries that can be produced. Instead, Micro-AM enables the creation of highly intricate and complex designs, such as lattice structures, interlocking parts, and miniaturized features. This newfound design freedom empowers engineers and designers to explore unconventional concepts, experiment with novel shapes, and push the boundaries of what is possible. As a result, product development becomes an iterative and creative process, encouraging the generation of innovative ideas and driving the evolution of products and technologies.
Furthermore, Micro-AM facilitates the production of custom designs tailored to specific applications, enabling personalized solutions that were previously unfeasible. This customization potential extends to a wide range of industries. In electronics, for example, custom Micro-AM components can be designed to fit complex electronic assemblies or integrate seamlessly into miniaturized devices.
This design freedom fosters a culture of innovation, where products can be optimized for specific purposes, leading to enhanced performance, efficiency, and user experience.
Accelerating Time-To-Market
In some highly competitive market niches, time-to-market is a critical factor for success. Micro-AM expedites the product development and manufacturing process, giving companies a competitive edge. As micro-AM allows for rapid prototyping and low-volume production on demand, companies can quickly respond to changing market demands and emerging trends.
By reducing the time spent on traditional manufacturing setup and tooling, Micro-AM minimizes production delays. This capability is particularly valuable in industries where fast response times are crucial. These include consumer electronics and aerospace. It enables companies to bring products to market swiftly and efficiently.
Micro-AM also enables “just-in-time” production, where components are fabricated exactly when and where they are needed. This lean manufacturing approach reduces the need for extensive inventory management, leading to cost savings and improved supply chain efficiency.
Micro-AM for Volume Manufacturing
As Micro-AM matures as a process, not just for prototyping but for true production, there is excitement about what the future may hold for medium- to high-volume manufacturing. There has recently been increased interest in using Micro-AM for the production of mold tools themselves. This is called Direct Rapid Soft Tooling (DRST).
DRST is well suited to scenarios when the goal is small series production where the cost of a traditionally manufactured tool is prohibitive. It is also much easier and inexpensive to apply design changes. In addition, increased tool complexity can be accommodated at no extra expense.
The time and cost associated with the fabrication of conventional micro tooling for micro injection molding have led to a sustained focus on the creation of Micro -AM produced DRST for short-run production parts and functional prototypes. Indeed, via our own Fabrica line of 3D printers, we have fine-tuned the manufacture of DRST through a combination of design optimization, material improvements with respect to temperature resistance and strength, and process improvements (focusing on improving the impact pressure and stiffness of the printed soft tool). The aim is the handling of tougher injection conditions and a bigger array of injected materials.
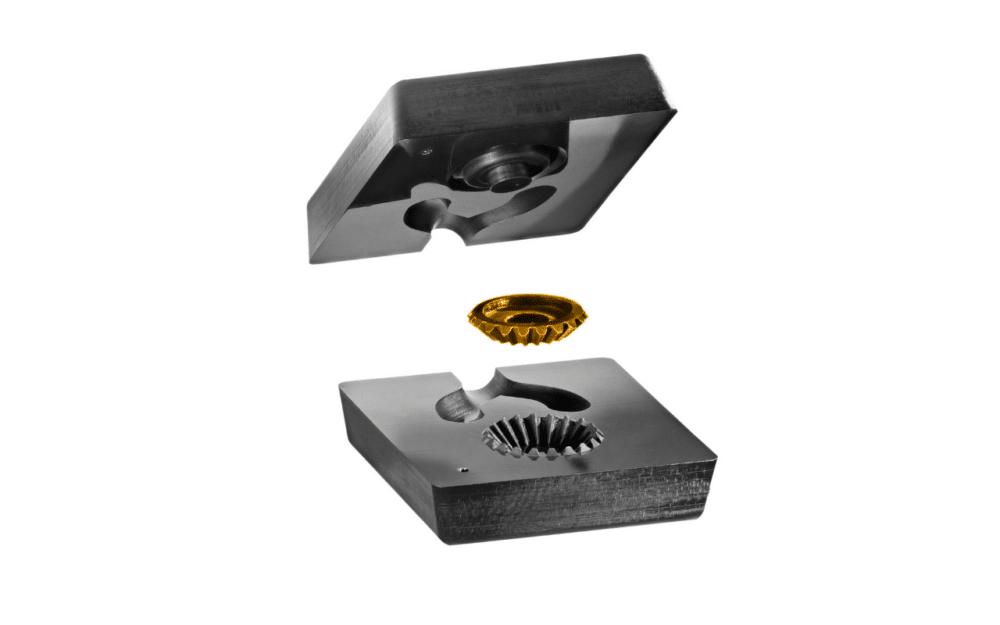
Business Case for DRST
Mold Makers
DRST unlocks new business possibilities for mold makers and manufacturers.. Up until this point, they were restricted to the use of long lead time and expensive traditionally manufactured mold tools for the achievement of any volume of molding, from prototype runs through to mass manufacture. Positive results today stimulate the business case for a process chain that includes DRST. This means a dramatically shorter lead time of around a few hours from file to injected part. Costs are also reduced from thousands of dollars to tens.
Geometric Complexity
DRST opens up the possibility of small and even medium and high-volume batch manufacturing depending upon part size and geometric complexity. Manufacturers can produce numerous replacement tools at extremely low cost. For the cost of one aluminum precise mold, which costs about $10K, it is possible to manufacture 500 soft molds, each producing hundreds of shots, leading to large amounts of final parts through a significantly faster process. In addition, each tool can be adapted as required. This opens up the possibility of speed to first part out. It also offer the ability to correct during the manufacturing process according to market and customer needs.
When AM-produced DRST and traditional injection molding are compared, the savings in terms of product development time and cost are seen as the most compelling benefits of using AM. However, the fact that AM is agnostic to complexity means that AM-produced DRST could also stimulate innovation in product design and manufacture. As mentioned, AM can achieve very complex geometries at zero added cost. It alsi enables geometries impossible using conventional processes. As such, it is a key enabling technology driving the production of cutting-edge products as well as shortening the product development cycle. Product design updates are shelved by manufacturers due to the cost of new traditional molds.