In March 2024, Chinese smartphone manufacturer Xiaomi introduced its first electric car, the SU7. The launch surprised the automotive industry, as many thought it impossible for an electronic manufacturer with zero automotive experience to go from the idea of producing a car to actually selling one. Along with the SU7 project, Xiaomi designed and built a dedicated facility to assemble all its cars. Our reporter Andrea Nepori had the opportunity to visit the factory, located on the outskirts of Beijing.
The “EV Factory” is a highly automated facility. It is located in a state-assigned Economic-Technologic Development Area on the outskirts of Beijing. On a recent trip to the Chinese capital, we had the chance to visit it and learn more about Xiaomi’s approach to building electric cars.
Watch our video
Hyper Die Casting
Unlike other car manufacturers approaching EV production from a long legacy of thermal vehicles, many new Chinese EV brands have the paradoxical advantage of starting from scratch. They are then able to rethink how to produce cars. The first aspect that stands out when entering Xiaomi’s facility is how much it resembles the concept and structure of a smartphone assembly plant rather than the traditional layout of an automotive production line.
It all starts with the Hyper Die-Casting 79100 Cluster, a new system Xiaomi developed that combines the car’s rear underbody from a proprietary die-casting titanium-based alloy. The die-casting block occupies an area of 840 square meters and is central to Xiaomi’s EV Factory manufacturing speed. By casting 72 components into one, the process avoids welding about 840 joints.
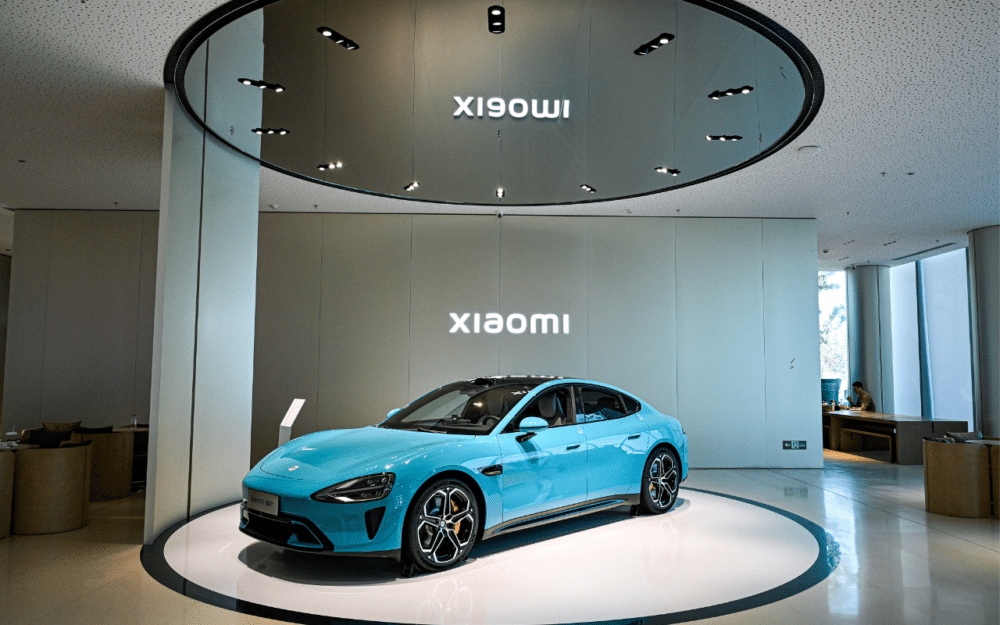
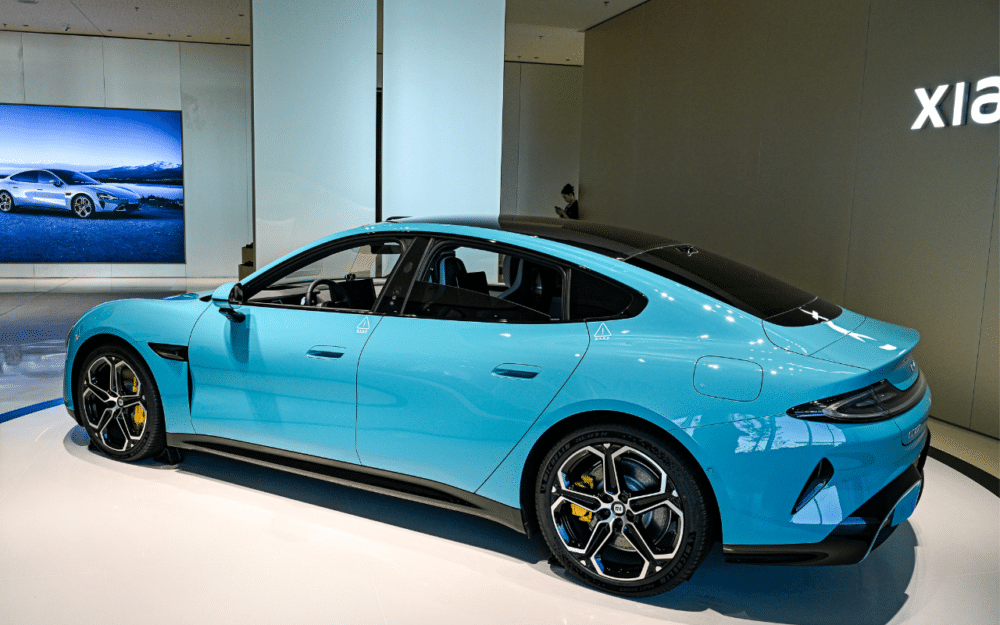
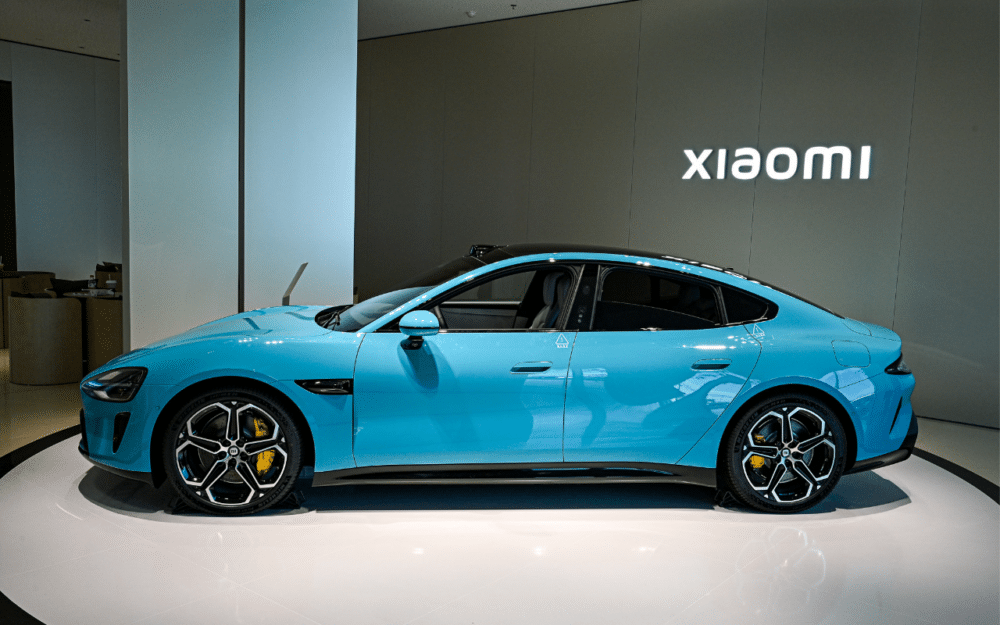
Robots Everywhere
As we taxi through the factory floor on a visitors’ cart, we also notice how low the human presence is. Short of the workers who oversee some of the larger machinery and push side doors out of a conveyor belt, we encounter countless rows of robotic arms picking and placing parts around or welding the chassis. Several self-driving robots move pallets and parts through the factory and politely stop to let us drive through as we cross their programmed path.
Xiaomi says that in the Body Workshop area, 100% of the key production processes are fully automated, with an overall automation rate of 91%. The assembly line is also highly automated, thanks to 39 robots.
According to the company’s official information, this is one of only two systems in China that have achieved 100% automated assembly of “four doors, two hoods, and fenders.” The accuracy is set at ±0.5mm, resulting in ultra-narrow body gaps that would be harder to achieve with non-robotic systems.
Robots are also responsible for painting and finishing the SU7 body. The paint, with an average thickness of 120μm, is applied using a “3C2B” method – three coats and two bakes. This process, which includes two additional steps compared to the traditional methods employed in the industry, is said to improve the paint’s smoothness by 8%.
The real advantage of the full automation of the painting process is Xiaomi’s ability to re-program it very quickly. Thanks to a “Quick Color Change System,” the company can switch the paint in about 40 minutes. That’s why Xiaomi can offer the SU7, SU7 Pro, and SU7 Max in 9 colors. For comparison, according to a 2023 study by iSeeCars, the average car model in Western markets is currently offered in about 6 colors.
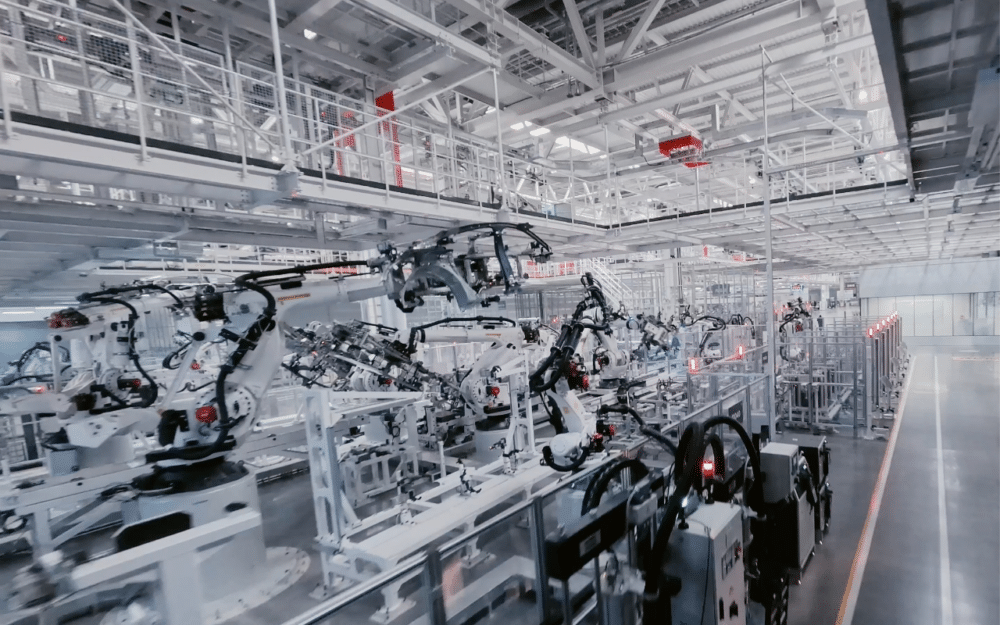
Quality Control
In its EV factory, Xiaomi even automated the quality control processes in their entirety. To detect defects in the large die-cast pieces and assess the precision of the body dimensions, the line employs a lidar system with an accuracy of ±0.05mm. Each die-cast part is also checked through an AI-based detection system that analyzes 28 high-resolution X-rays.
A high-precision detection process is in place to ensure that battery packs are in perfect shape to achieve what Xiaomi calls “zero defect delivery” of the battery pack. An ultraviolet scanner detects defects in the complete vehicle exterior, including transparent parts such as the sunroof and headlights.
One Car Every 76 Seconds
Each and every Xiaomi SU7 car is currently manufactured in the Beijing plant we visited. According to the company, production speed is the main benefit of automating so many processes and rethinking car making with the experience coming from the smartphone and electronics industry.
At full capacity, the EV Factory can produce about 40 SU7s every hour. This means that one new car is ready to roll off the production line every 76 seconds.
Xiaomi will need each and every unit it can produce. As of June, the EV Factory has already started working on double shifts. Xiaomi indeed, faces a very high demand for the SU7.
Back in March, Xiaomi received 88,000 preorders for the new car in less than 24 hours. It beat its goal of 75,000 units for the entire year. The company has revised its sales metrics. It now expects to sell about 120,000 SU7s before the end of 2024.
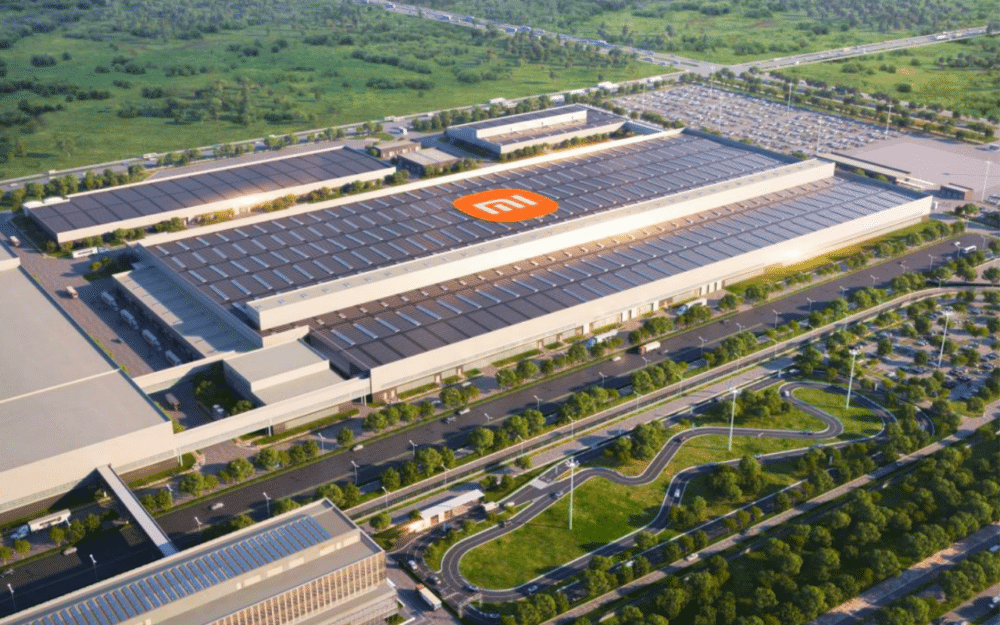