At Hannover Messe, DirectIndustry met with Denis Mugrauer, from Festo’s Bionic Learning Network. The new project they are showcasing is a Bionic Bee.
Festo is renowned for presenting products inspired by nature. In previous editions of Hannover Messe, they showcased robots modeled after ants, kangaroos, and octopus.
Festo’s Bionic Learning Network, a specialized lab, is where engineers study nature to find innovative ideas for energy efficiency, alternative propulsion, and ultra-lightweight design. They then translate these natural concepts into industrial applications.
This year, Festo is showcasing a bionic bee. Our industry analyst, Hicham Dhouibi, visited Festo’s booth at Hannover Messe and talked to Denis Mugrauer to learn more about their new creation and its potential applications in the industry.
What kind of new technology is in this bee?
Denis Mugrauer: “Our latest project, the Bionic Bee, draws heavily from our studies of real bees. What makes bees so remarkable is their agile flight and swarm behavior. By analyzing these natural characteristics, we were able to learn a great deal about lightweight design and the mechanics of bee flight.
With this knowledge, we set out to create a robot bee that weighs just 30 grams. It contains a multitude of components, including advanced electronics for flight control and attitude stabilization, mimicking the way bees navigate and maneuver.
Each bionic bee is equipped with an indoor GPS system that allows it to determine its position in 3D space and share this information with the other bees in the swarm. This communication among the bees is crucial for replicating the complex, coordinated behavior observed in natural swarms.
Using real-time positioning data, our system predicts the optimal flight path for each bee to maintain swarm formation and avoid collisions. This approach enables our robotic bees to move as a cohesive group, much like their biological counterparts.”
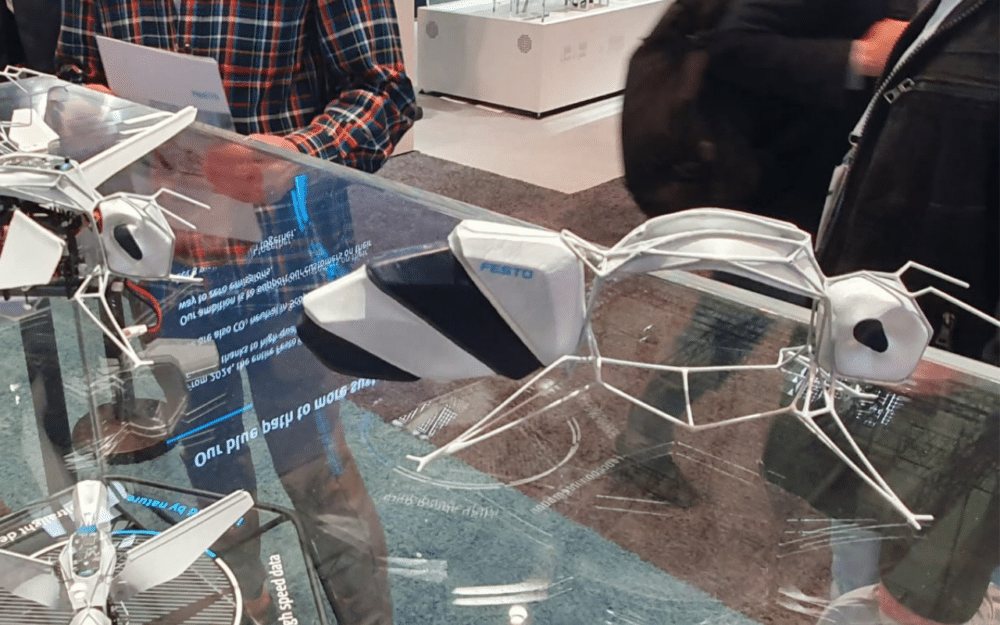
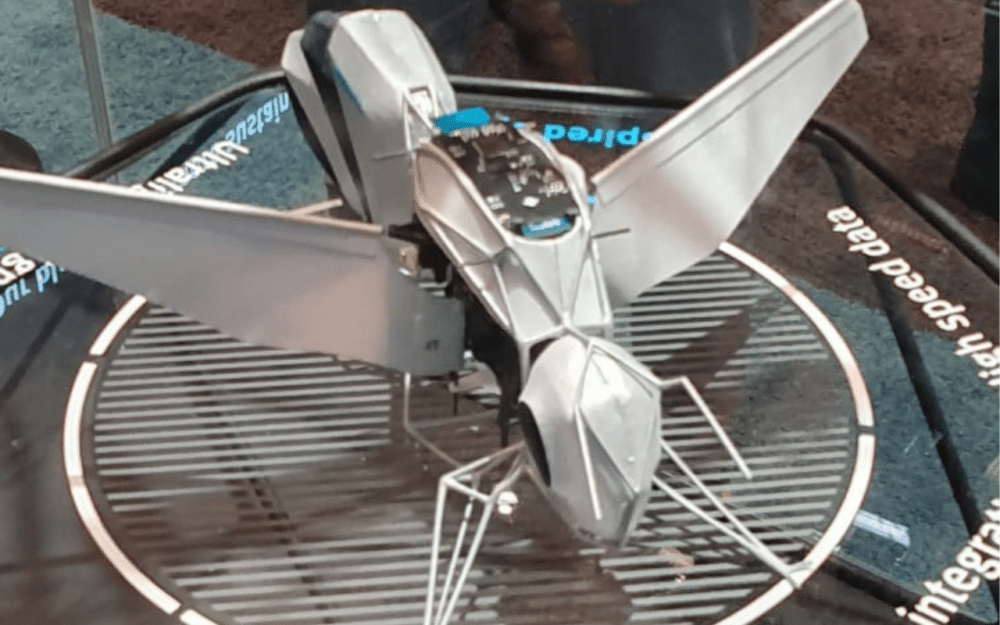
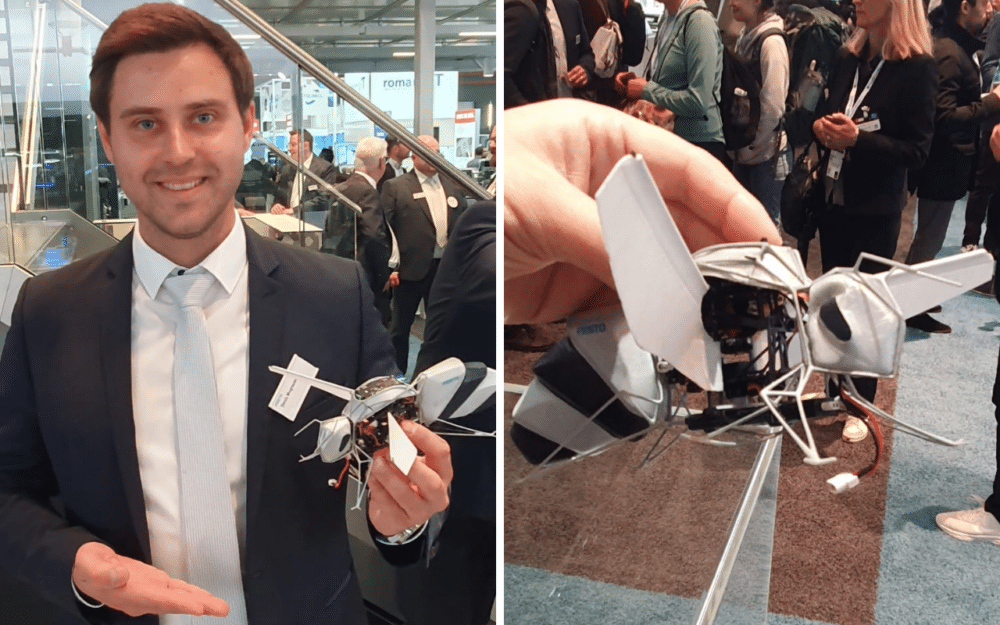
What are the industrial applications for such technologies?
Denis Mugrauer: “Our lightweight design owes much to the SLS 3D printing technology we used. This technique allowed us to create a remarkably light structure, thanks to a specialized type of printing.
Another key component of our project is the communication and localization system. Each robot communicates with the others, functioning through an intelligent, decentralized system. This approach eliminates the need for a centralized server to manage multiple nodes, allowing for more autonomous and efficient operations.”
Can you provide examples of bionic technologies you’ve developed that are now being applied in real-world industrial settings?
Denis Mugrauer: “For us, these projects serve as a form of brainstorming, allowing us to experiment with different ideas and approaches. Over time, we determine how these concepts can be integrated into real-world applications.
Take, for example, our past projects within the Bionic Learning Network. We once explored the structure of a fishtail, which eventually led to the development of a Festo product designed for the gentle grabbing and handling of objects. Similarly, our research into the anatomy of an elephant’s trunk inspired a robotic system used in our soft robotics products.
It’s a creative process, where each experiment has the potential to yield a practical, real-world solution. However, sometimes these projects remain prototypes, paving the way for new technologies and future innovations.”
How long did it take to develop those bees?
Denis Mugrauer: “The entire development process took two years. Initially, we focused on the kinematics and control systems necessary to achieve a flying bee-like robot. Next, we worked on the electronics and stabilization, addressing challenges such as the vibrations caused by the flapping wing mechanism and the noise filtering required for precise localization.
Navigation was another significant aspect that required extensive time and effort to get right. However, we’re very proud to present the final result at the Hannover Fair.”