Our expert, Hicham Dhouibi, accompanied Jacques Dupenloup, Director of the Robotics Division at the Swiss robots manufacturer Stäubli, as they delved into the latest innovations during the Technical Days of the brand.
The PF3 AGV Platform
The PF3 platform is an AGV capable of moving inside a facility. It is also equipped with a lifting unit, allowing it to maneuver under spaces where it can lift loads up to 3 tons.
It measures 1750 x 970 mm (Length x Width). Its low profile, standing at 350mm without the lifting unit and 400mm with the lifting unit, ensures efficient integration into diverse environments.
It also features a safety scanner, five emergency stop buttons, and LED communication bands that provide real-time status updates. Advanced collision prevention features enhance operational safety.
Total Cost of Ownership (TCO) considerations are addressed through the PF3’s sustainable design, offering up to 7,000 recharge cycles. Rapid charging capabilities of up to 80A and technology ensuring robustness and reliability contribute to a lower TCO over the platform’s lifespan.
Maintenance is simplified with lateral access to components, and critical part replacement can be accomplished in a matter of minutes, minimizing downtime.
PF3 will be commercially available at the end of this year.
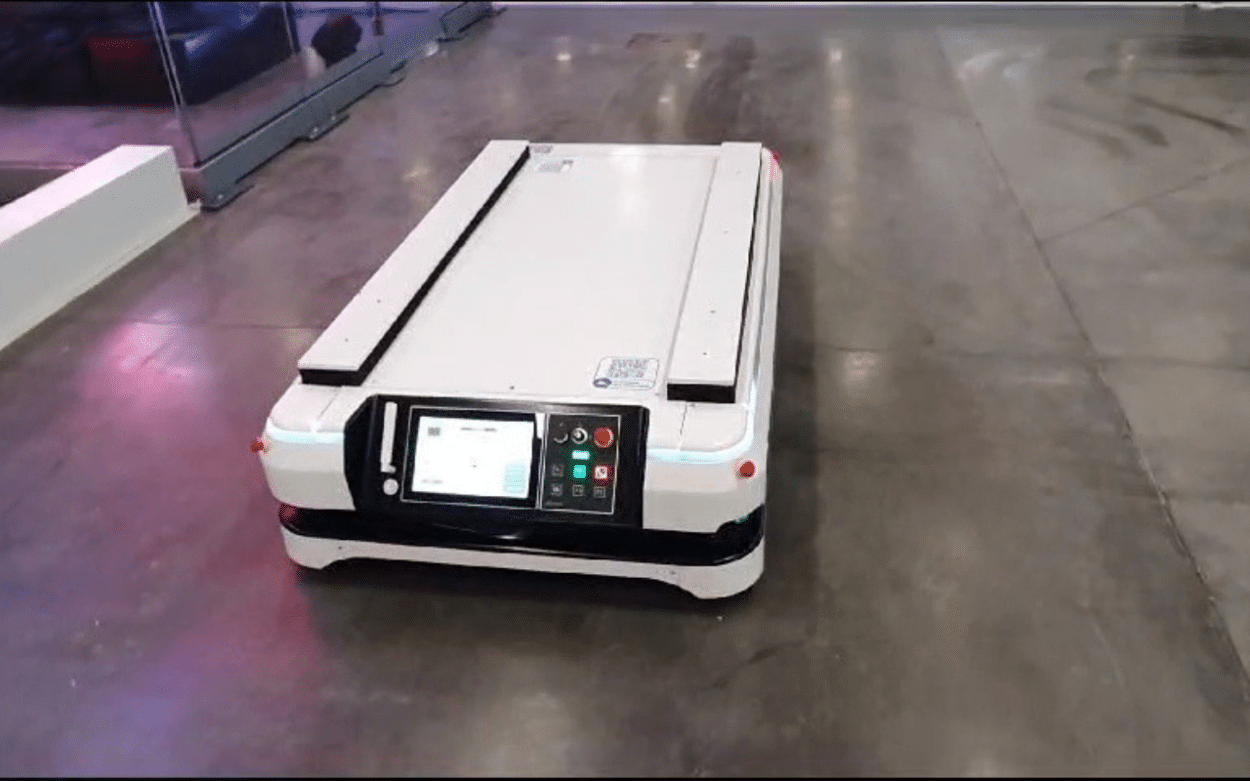
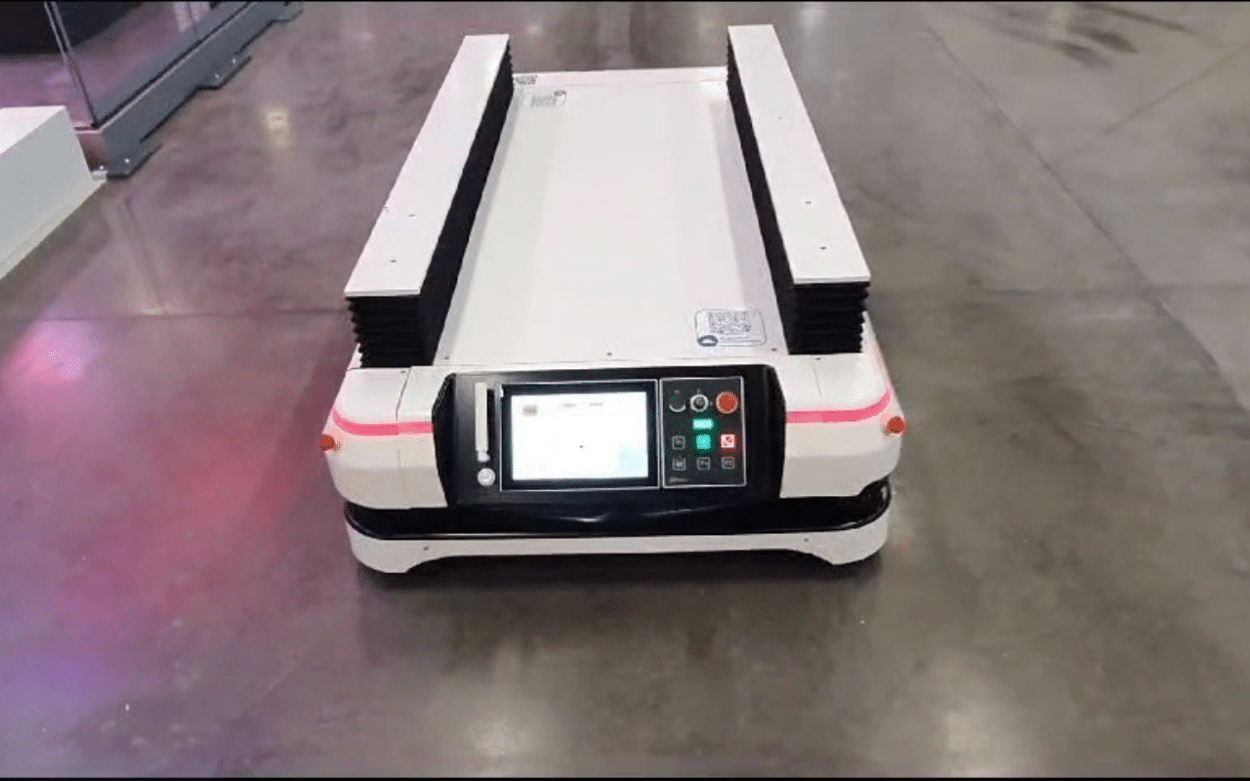
The TX2-200 Robot
The TX2-200 is the largest robot in the range and is capable of working in collaborative mode, meaning without barriers. The robot weighs one ton and can lift up to 170 kilograms.
For Mr. Dupenloup
“It’s an industrial robot, meaning it can move very quickly and it is designed to handle very heavy loads. But it can also work without a cell.”
The TX2-200 will be released at the beginning of next year.
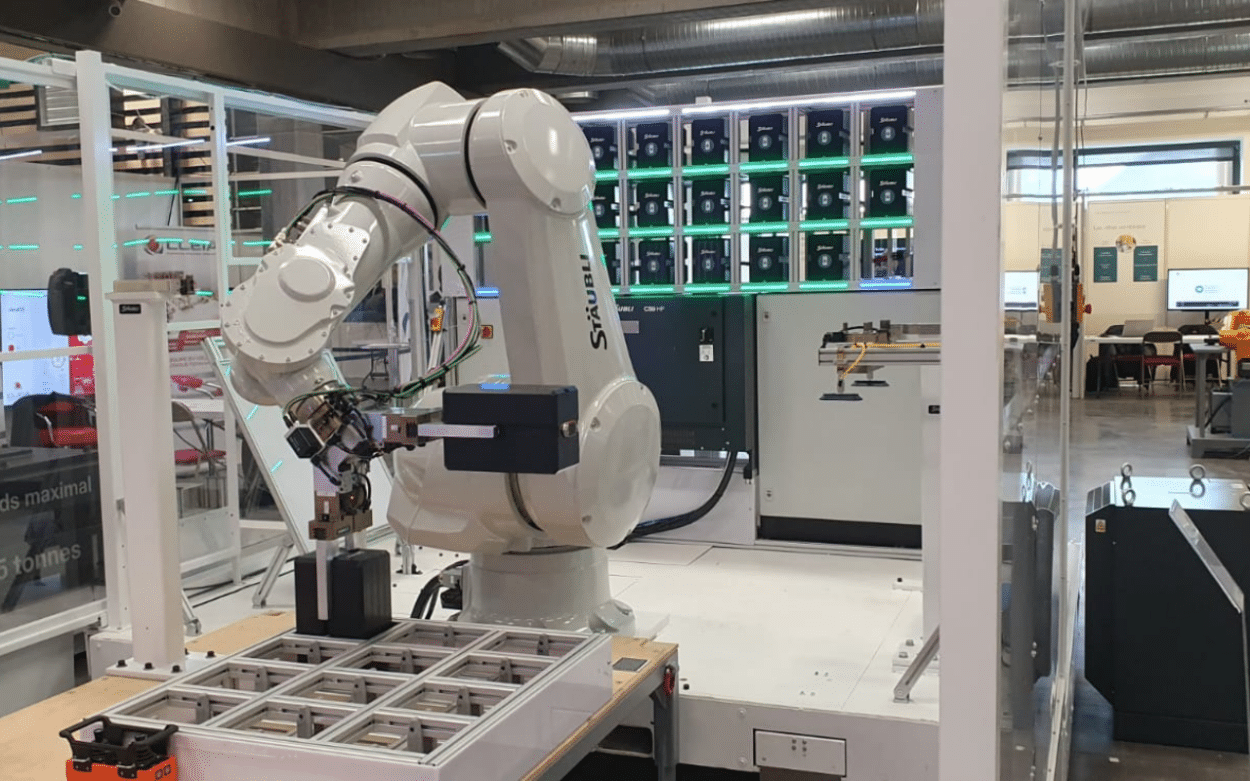
Robots Dedicated to Pharma
Stäubli showcased robots that are specialized for pharma applications. The Swiss manufacturer already has cleanroom robots and robots designed for the food industry. This new range is dedicated to the world of pharma.
“It can be washed and cleaned with hydrogen peroxide, as well as aggressive substances, and it’s designed to withstand these environments. It even features a hollow wrist, which is the latest innovation. There’s no area for bacteria retention. It’s truly dedicated to the pharmaceutical industry.”
Different sizes of robots are available to meet various needs.
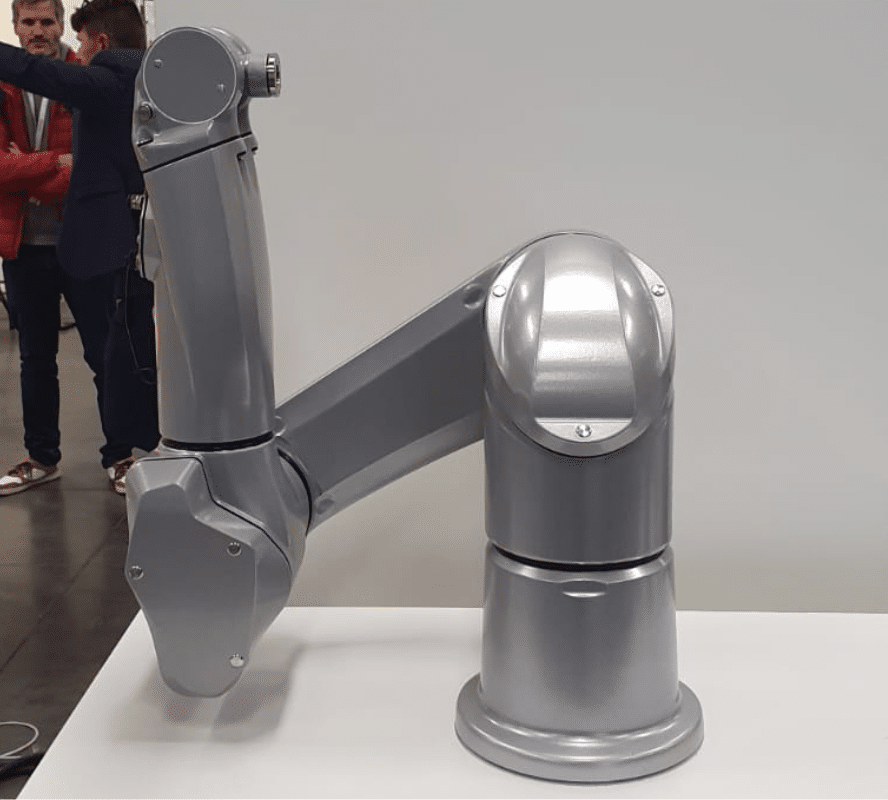
VAL Blocks, The Programming Simplification Software
This programming simplification software called VAL Blocks is designed specifically for pick-and-place applications. This software is designed to make it exceptionally user-friendly for operators, meeting the need for quick and efficient operator training. It achieves this by enabling rapid and straightforward programming simplification.
The operation is structured in blocks, allowing clients or integrators to create modules swiftly.
“This feature has become increasingly essential as there is a growing demand for robotics, but not always a corresponding availability of trained personnel. Therefore, it is imperative to swiftly deploy a robot or reconfigure it for a different application, and VAL Blocks meets this need efficiently.”
SCOPE, The 4.0 Box
SCOPE (Smart, Connect, Optimize, Prevent, and Enable) is a system designed to gather information. It acts as a hub for diverse data sources, connecting the entire factory and serving as a control center. It offers detailed insights into robot usage, and temperature, and facilitates maintenance planning and proactive detection for preventive maintenance. In essence, it captures and processes all relevant data.
“We capture several key pieces of information. We check if the robot is connected, indicating operational readiness, though not necessarily in active use. Additionally, we gather data such as the robot type, serial number, controller serial number, the running version of the software, and the version of Scop in operation.”
Moreover, the platform provides a compelling feature—a timeline showcasing recent recordings over the last hour, day, or week. For instance, in the last hour, there were one hundred and thirty-three recordings, each accessible individually. This timeline includes an interpretation of the robot’s consumption. It gives insights into its normal operation or whether it requires specific maintenance.
This comprehensive set of data empowers companies with a real-time overview of their robot fleet. It helps identify if any robot is idle, signaling the need for intervention. For example, if a robot is more used than usual, it will recommend maintenance.
“We are increasingly receiving requests for this because, in many cases, we work with clients who have a fleet of robots installed.”
SCOPE interprets continuous recordings made by robots and presents them in the form of dashboards. Stäubli offers the flexibility to integrate with MES or ERP systems using MQTT or HTTP protocols. Users have the option to relay all information or filter it based on specific criteria. For instance, when the robot is operating normally, it may choose not to transmit data continuously, focusing on anomalies.
To the question of whether there is an AI aspect to it, Mr. Dupenloup answered:
“Currently, not yet. However, it’s a product that will evolve over the long term.. Development is underway to incorporate AI for predictive maintenance interpretation. It will be a dynamic product, evolving based on the demands of different clients.”
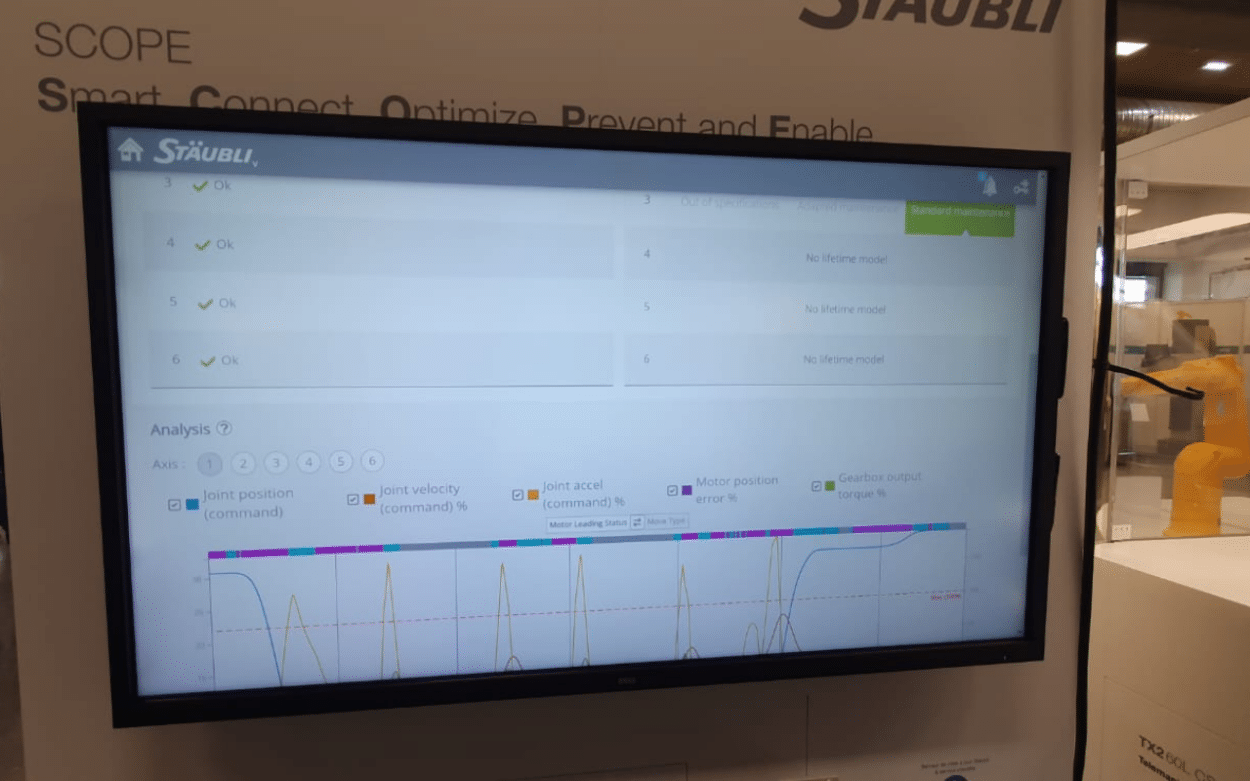
Remote Maintenance
Stäubli also developed a remote maintenance service for their clients. This technological capability directly addresses the growing need for prompt responsiveness in the industry.
For example, if a technician at a client’s facility encounters an issue with a robot, they can contact a Stäubli operator. While the on-site technician wears AR glasses, the remote operator can guide them through the resolution process.
“We are committed to providing remote assistance to clients, empowering them with the use of AR glasses. In the event of queries or issues, clients can contact our hotline, connecting with an operator who offers guidance through the troubleshooting process. The operator can visually evaluate the situation and provide step-by-step instructions to the on-site technician, whether it involves pressing a button, changing a fuse, or inspecting a specific component.”
In this scenario, the client must equip themselves with AR glasses.
Currently, three highly skilled Stäubli operators are engaged in this remote maintenance service.
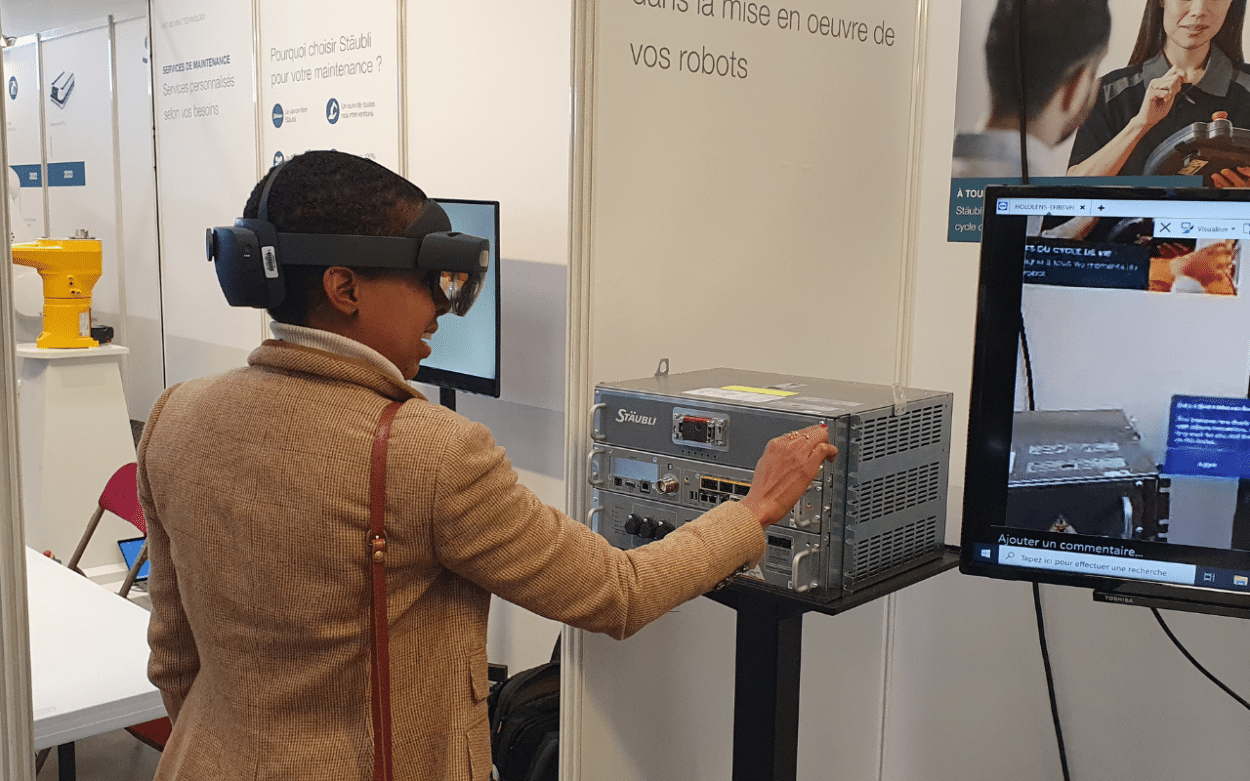
Educational Application for Robot Maintenance
This application serves as an educational tool for robot maintenance, providing a detailed view of the robot and insights into various maintenance operations.
The application breaks down different points of the robot, including the shoulder, arm, elbow, forearm, and wrist. For example, by clicking on the elbow, one can visualize the entire path of the harness, encompassing the electrical and pneumatic cables, from the foot to the wrist.
“The primary purpose of this tool is to demonstrate all maintenance operations performed on the robots to the client. The client can have a firsthand experience using their tablet, providing a detailed understanding of the maintenance processes. This virtual exploration enables clients to understand the internal structure of their robot and the specific maintenance tasks performed annually under their contract.”
The application explains maintenance operations visually through a 3D model, demonstrating various tasks. For instance, it showcases lubrication and the replacement of bearings on the elbow. The application also includes maintenance operations on the wrist, such as tensioning and greasing red belts, and replacing black belts when tension is compromised.
Educators have expressed interest in the application for student learning. It allows students to understand maintenance operations without physically performing them on the actual robots, ensuring safety and preventing damage.
The virtual representation of the robot enhances understanding, especially for clients familiar with the external appearance but lacking insight into the internal components.
Although currently presented as a demonstration, plans involve making the application available for clients on tablets.
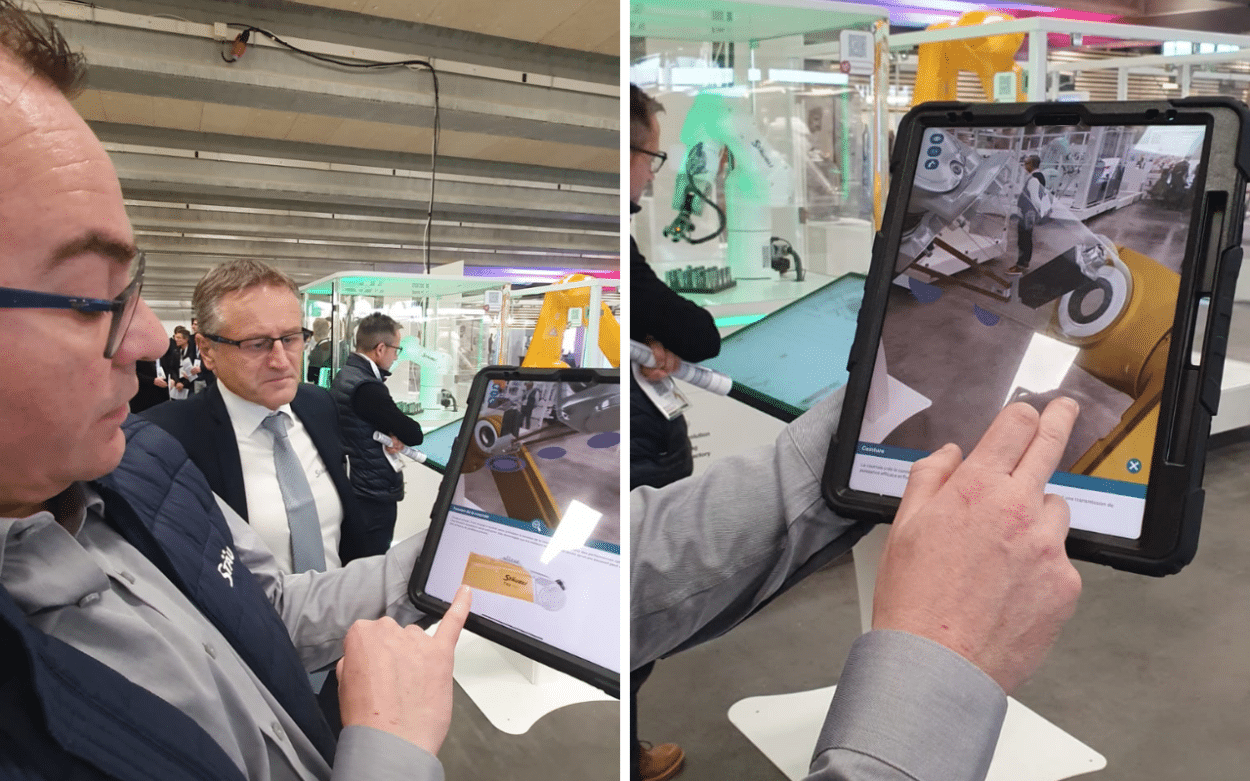