Hannover Messe ended last Friday. Hundreds of start-ups and companies showcased their latest products aimed at transforming industry. We selected 4 innovative technologies.
Hannover Messe 2023 brought together 4,000 exhibitors and 130,000 visitors from all around the world.
For Dr. Jochen Köckler, during the closing ceremony last Friday,
“In the 5 days of Hannover Messe, there was a spirit of optimism. It is because there are technologies for a competitive future.”
Here are 4 technologies we selected from the fair.
1/ Giving the Robot a Human Touch
Developed by Bosch Rexroth, the Smart Flex Effector is a sensor-based compensation module, which is situated between the robot and the gripper and makes the robot as flexible as the human hand. This product won the prestigious Hermès Award for its innovative approach to automation, during Hannover Messe 2023 opening ceremony on Sunday, April 15th.
In a press release, Prof. Reimund Neugebauer, president of the Fraunhofer Society and chair of the Hermes Award jury said:
“The Smart Flex Effector is driving efficiency and diversity in the uses of robots, creating quantifiable value for industry, the environment and society.

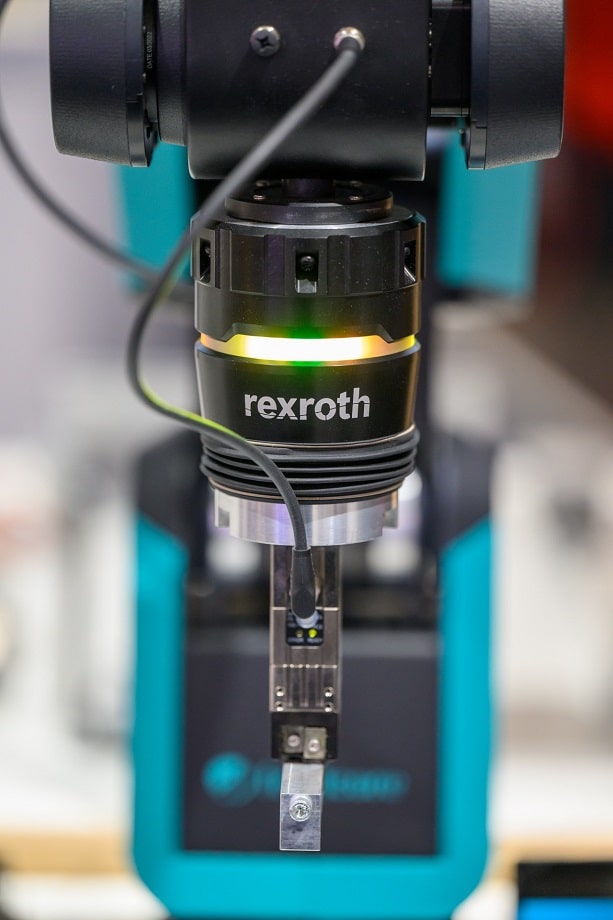
One of the key features and most significant advantages of the Smart Flex Effector is that it compensates for tolerances in real time, sensing the exact position of workpieces to be gripped and reporting the position in real-time to a controller. The compensation module is so sensitive that it can safely handle workpieces made of fragile materials such as glass.
Besides, operators without programming knowledge can teach robots manually by moving the gripper into the correct position by hand. Besides,
This enables the automation of processes and tasks that were previously impossible to automate. This product can be retrofitted and added to any robotic arm, making it accessible to a wide range of industries, from medical technology and biotechnology to electronics and automotive.
According to Thomas Kober, Director Sales Bosch Rexroth whom we met at the booth,
“The Smart Flex Effector’s six degrees of freedom of movement, with 3mm in each direction, replicate the movements of the human hand. As a result, there is no need for a precise machine or vision system to carry out tasks. This product is a game-changer in automating manual or semi-manual processes, even in Bosch plants. The Smart Flex Effector has the capability to automate these processes and improve overall productivity.”
The Smart Flex Effector can handle loads of up to 6kg, making it a particularly effective tool for cobots and robotics applications. It can be used to automate joining processes, complicated assembly movements, or difficult handling tasks, increasing the range of applications for industrial robots. It is designed for use on articulated robots or Cartesian linear systems and can be retrofitted to existing robot applications.
Looking to the future, Bosch Rexroth is working to integrate AI into the Smart Flex Effector. With AI, the product could be beneficial for areas that require high technical requirements, especially in biotechnology.
The Smart Flex Effector is already available on the market.
2/ The DIY Robot
The ATRO system already made a debut at Automatica in Munich last June. But it was also one of Beckhoff’s main highlights this year at Hannover Messe.
The ATRO system is a modular industrial robot system that enables users to assemble the optimal robot structure for different applications on an individual and flexible basis. With this Lego-like system, users can create their own robot configuration that suits their specific needs.
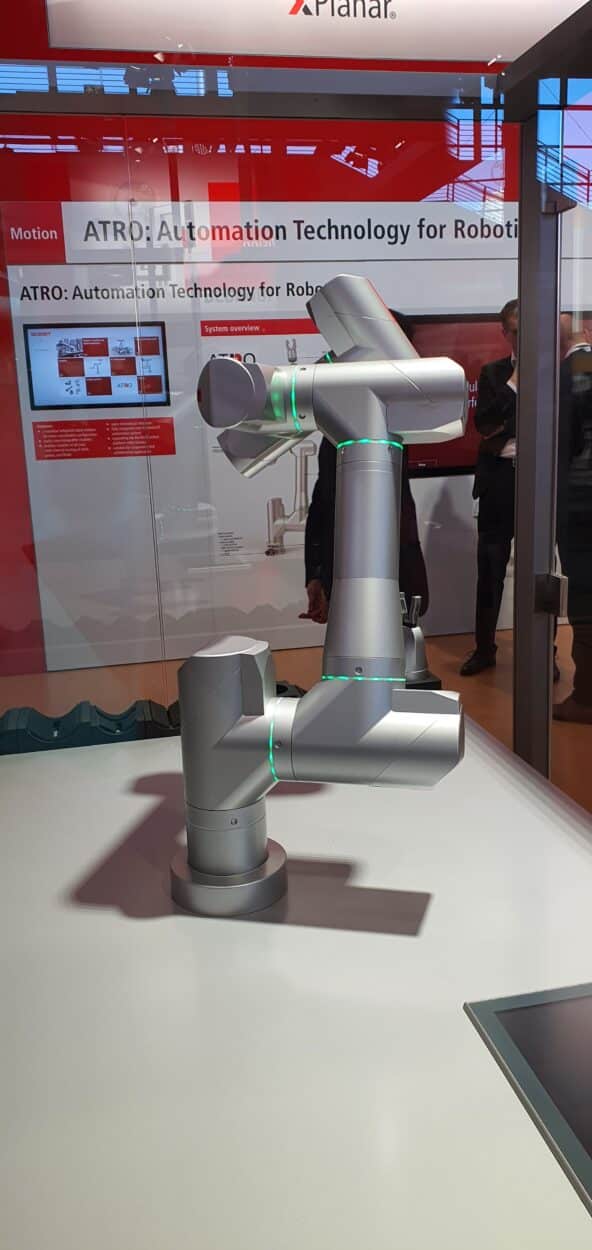
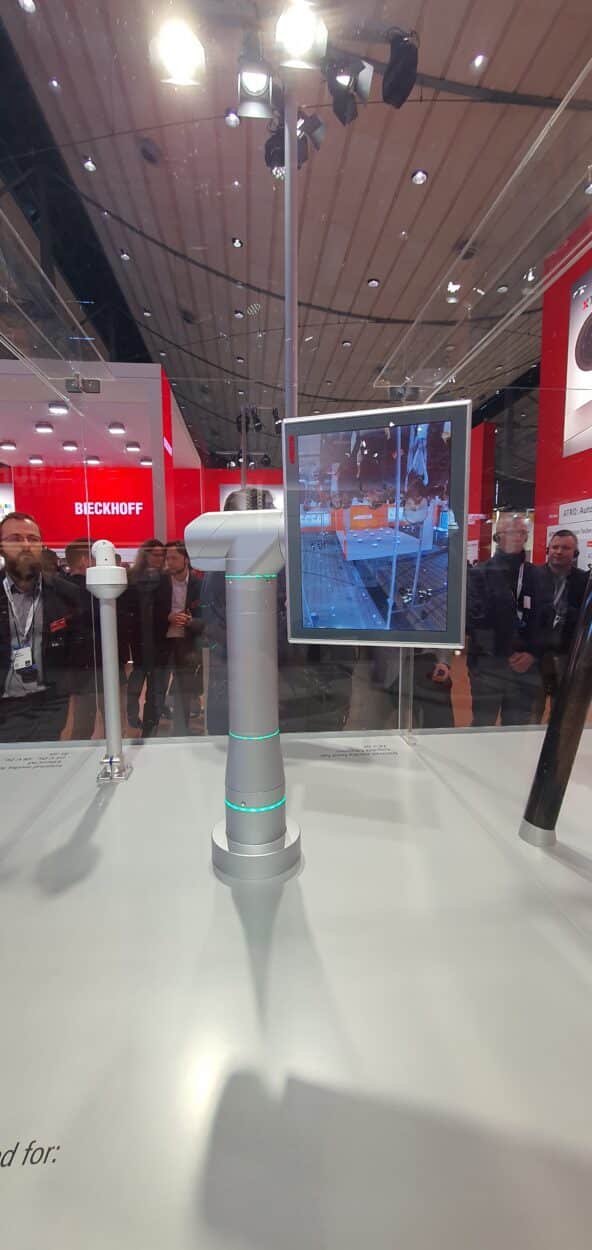
The system consists of standardized motor modules with integrated drive functionality, link modules of different designs and lengths, and the TwinCAT control platform. With these components, users can create robot systems ranging from single-axis rotary indexing tables and three-axis delta robots to six and seven-axis articulated robots.
Unlike most robots on the market such as ABB or KUKA which typically come with a set number of axes, generally 6 axes, the ATRO system offers the flexibility to choose only the necessary number of axis modules for each application. For example, a pick and place application may only require three or four axes, so using only these axis modules would save energy and money, as less energy is required to move a three-axis robot compared to a six-axis robot.
The arms can rotate constantly and autonomously, allowing for greater flexibility and efficiency in various applications.
Besides, the ATRO system offers various robot configurations such as the Octopus, which can replace three delta robots, while some arms can do one thing and others can do something else. This makes it a versatile system for various applications, especially for small productions and packaging.
The ATRO system can be a standalone robot or mounted on an AGV. The body is made of lightweight aluminum, and the robot uses servo motor AC instead of brushless motors.
The ATRO system is set to be released next year, in 2024, and could potentially be one of the first do-it-yourself modular robot technologies for the industrial market.
3/ The Key-in-Pocket Maintenance System
Maintenance tasks on machines can be dangerous, and it is important to ensure that only authorized personnel are given access to the machines to avoid accidents. Pilz has developed an innovative solution to ensure safety in maintenance tasks through its human-machine interface.
Once this has been done, the operator enters its key in the interlock system on the door, the door opens and the operator can enter the enclosure and conduct the necessary maintenance tasks. The key is designed to ensure that only authorized personnel can access the machine, thereby reducing the risk of accidents in the workplace.
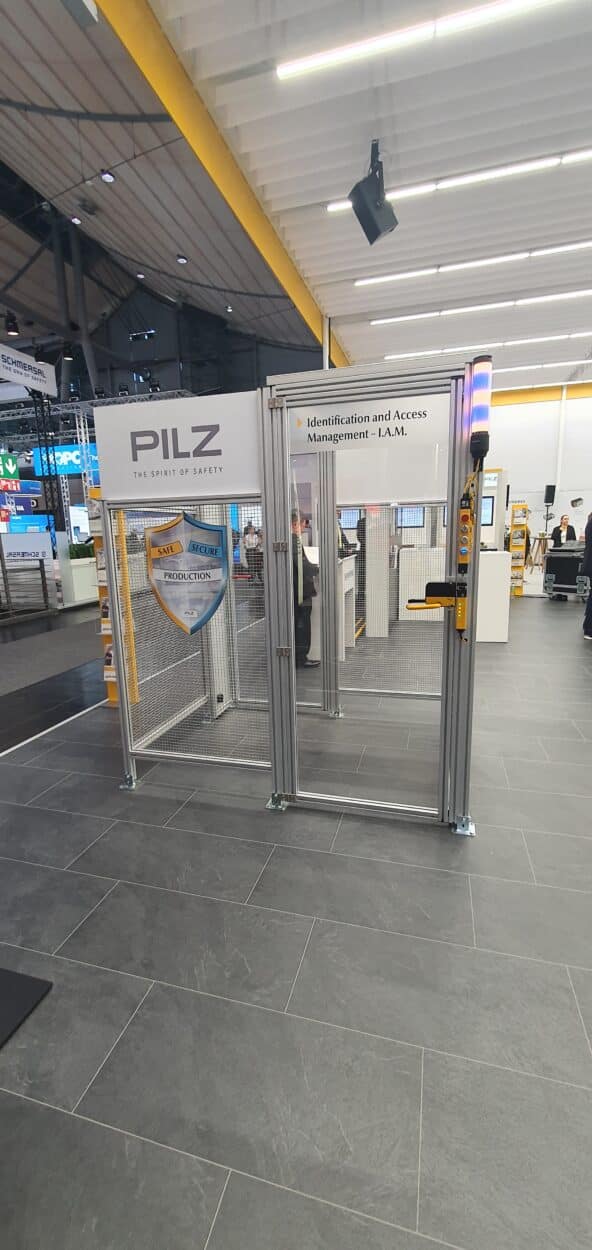
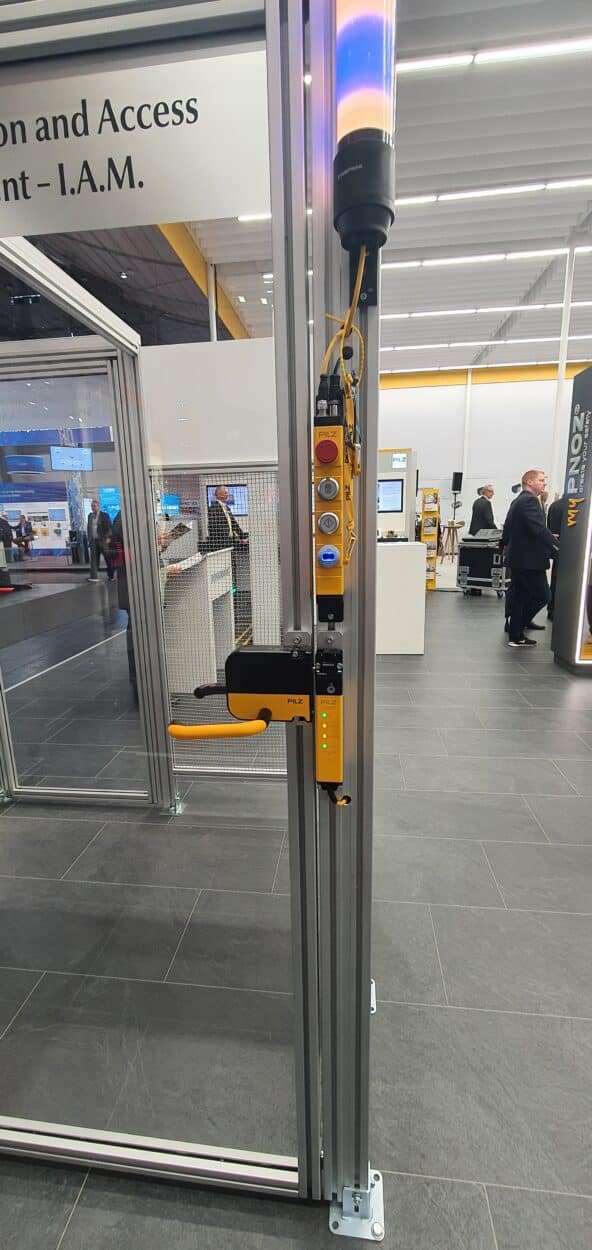
Their solution called “Key-in-Pocket” provides access control inside machine enclosures. This solution allows operators to identify themselves at the safety gate through PITreader, utilizing a personalized transponder key. The Pilz controller (PNOZmulti 2 or PSS 4000) stores a security ID in a safe list. After the machinery has stopped, workers can access it to perform maintenance duties. Once the personnel leaves the machinery area, they are required to sign out through the PITreader to restart the plant. The security IDs are then removed from the safe list. When the list is empty, the machinery can be activated and restarted.
The access permission system is essential for safety. For example, an operator may be conducting maintenance on machinery, but due to blind spots, the operator is not visible. If another operator launches the machine without realizing that someone is inside, the operator inside could be seriously hurt, or worse. With Pilz’s solution, a blue light system outside the cage indicates how many people are inside the cage. One blue line means one person is inside, ensuring that operators are always aware of the number of people inside the cage. This guarantees that no personnel is within the hazard zone while potentially hazardous machinery is reactivated.
Furthermore, the total number of people and their names are written on the panel PC outside the cage. This feature ensures that every authorized personnel is accounted for and ensures that no one is left behind or forgotten.
Pilz sells the gate box, the interlock system, and the lamp, providing a comprehensive access control solution for maintenance tasks. The safe list works with Pilz’s controller, and the software enables users to see which key is in the machine. This allows for a clear overview of who has access to the machine and when. With this level of control, the likelihood of accidents due to human error is significantly reduced.
4/ The Connected Tool Holder
Traditional tool holders have been existing for a long time. But SCHUNK has taken them to the next level with their iTendo2 product, introducing connected and Industry 4.0 technology.
The company has embedded sensors inside a tool holder to measure vibrations during the machining process. Thomas Wittkowski, product manager at SCHUNK, explained that this real-time sensor technology allows for easy process monitoring and maximized tool service lives.
“The challenge was to take our best tool holders and put sensors inside to measure vibrations of a process. This technology can detect chattering inside the process, wear time of a tool, and parts quality, which can help differentiate between a good and bad process.”
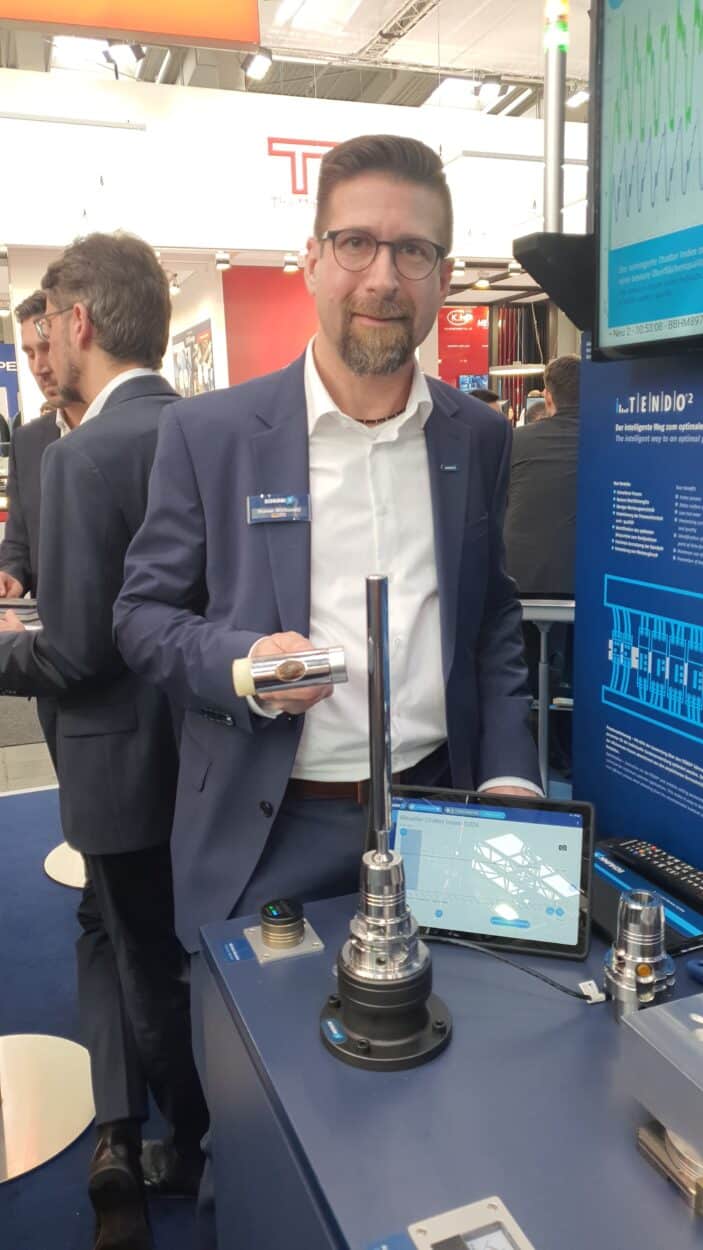
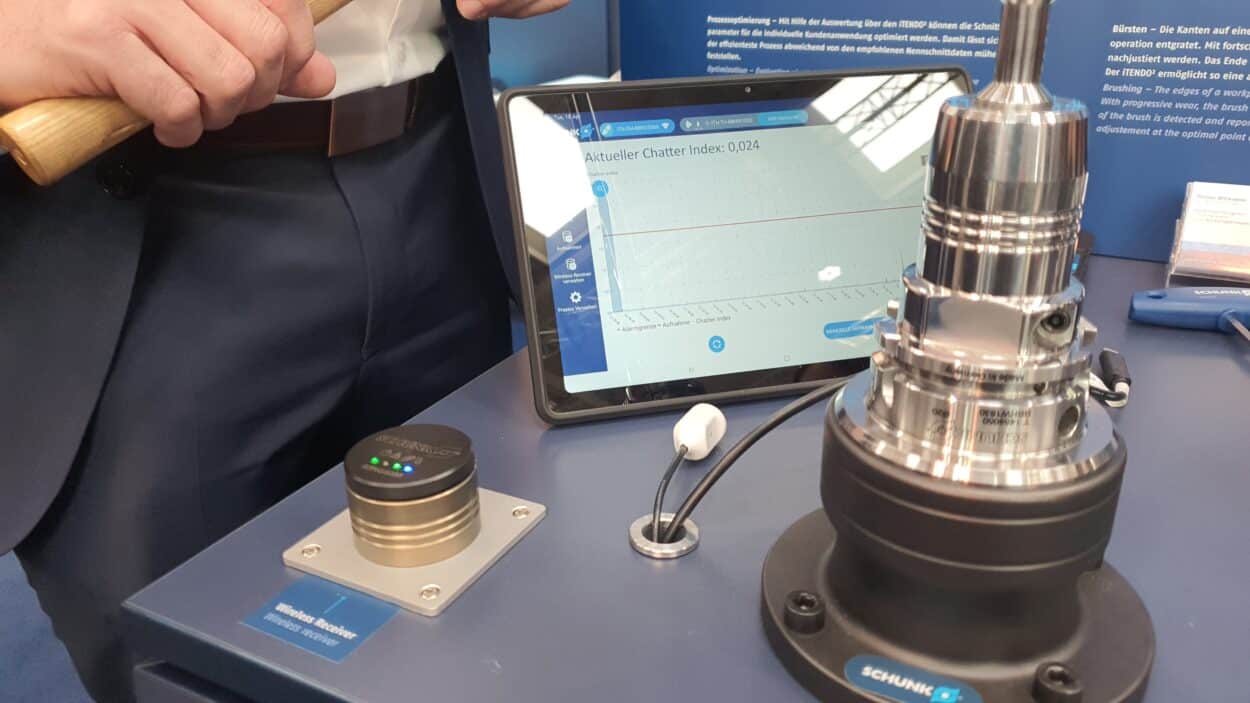
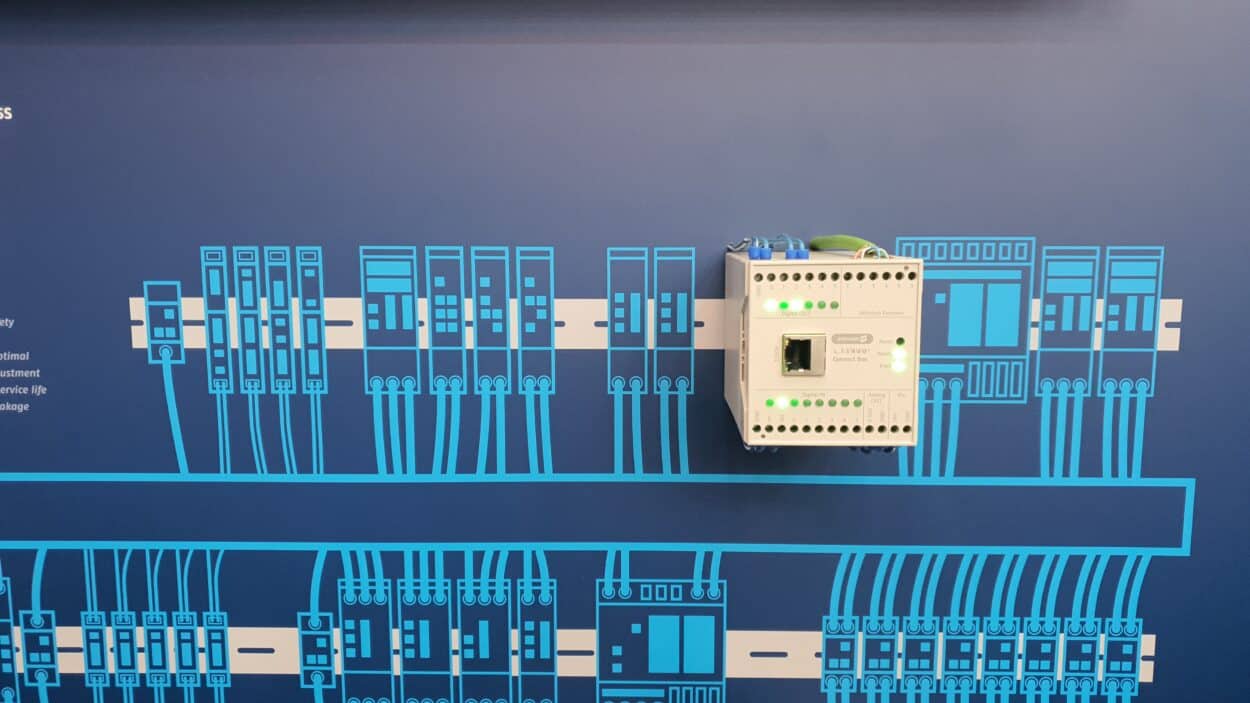
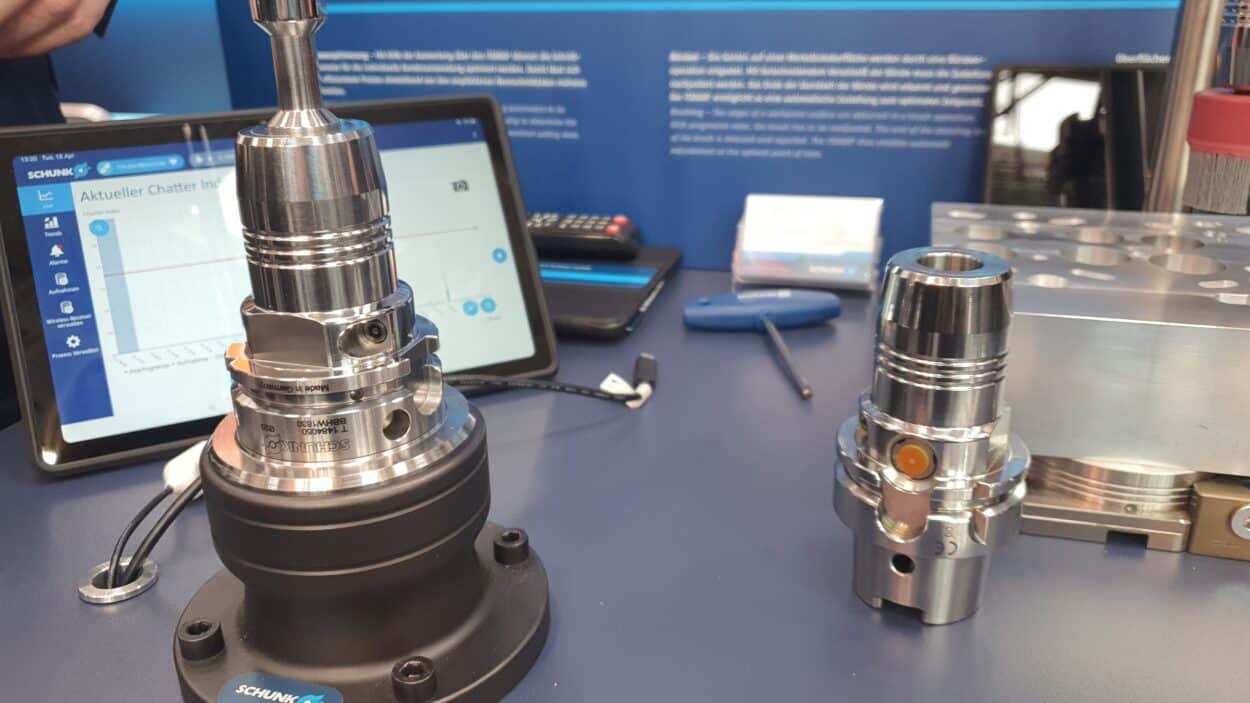
Pictures: Credit: C. Rustici / H. Dhouibi
iTendo has speeds of rotation of up to 30,000 RPM and is compatible with SCHUNK standard tool holders. It can monitor compliance with surface quality when countersinking. It can also detect vibrations in tools as small as Ø 3 mm in diameter, indicating tool breakage due to wear or a feed rate that is too high. It can also compare recorded vibration data so that the best parameters can be chosen, therefore optimizing the cutting process even more.
The product comes with software that allows users to set limits for the vibration data. When the vibrations go beyond the value set in the software, a signal alert appears requiring action to be taken.
The idea for the iTendo came from customer feedback, particularly from the milling and aviation industries, where quality parts are crucial. But it has a variety of applications across many other industries including the glass industry.
The company has also introduced a wireless receiver inside the machine and a connection box, allowing for iTendo to give signals to other systems. This feature helps monitor processes and provides a digital output to the machine.
If iTendo was launched at EMO in 2021, the wireless receiver will only be on the market next month.