Ten years ago, 3D printing was very rarely a topic of discussion for manufacturing at scale, despite the technologies’ inherent advantages. In this feature, Daniel Princ, Head of Production, P3 EMEA & APAC at Stratasys, examines why manufacturers should look again at the latest generation of 3D printers when seeking flexible production solutions.
By Daniel Princ, Head of Production, P3 EMEA & APAC at Stratasys
From Design Desk to Factory Floor
One of the biggest buzzwords in the 3D printing/additive manufacturing (AM) industry is ‘production’. The technologies that make up the AM ecosystem have for over 30 years established themselves as the ‘go-to’ solution for prototyping across nearly all manufacturing sectors. They have even gotten a foothold for end-use applications like spare parts or manufacturing tools. The industry’s dream, however, has always been to see AM as a true production technology, able to compete with injection molding and machining for mass manufacturing applications.
Reaching production capability isn’t easy. A combination of material qualities, repeatability, process stability, process speed, part quality, and cost per part must be superior to the entrenched traditional processes. When competing with decades- or even centuries-old technologies, those bars are set very high indeed! However, with the latest advances, manufacturers should now be considering AM at every stage of their process, from design to volume production.
Optimizing Additive Manufacturing for Production Scale
With Stratasys’ Programmable PhotoPolymerization P3 platform, manufacturers can solve hundreds of production challenges with a single highly flexible system. Initially conceived as a materials development reactor, the P3 platform has proved itself a production-capable 3D printing technology that opens up a new world of opportunities.
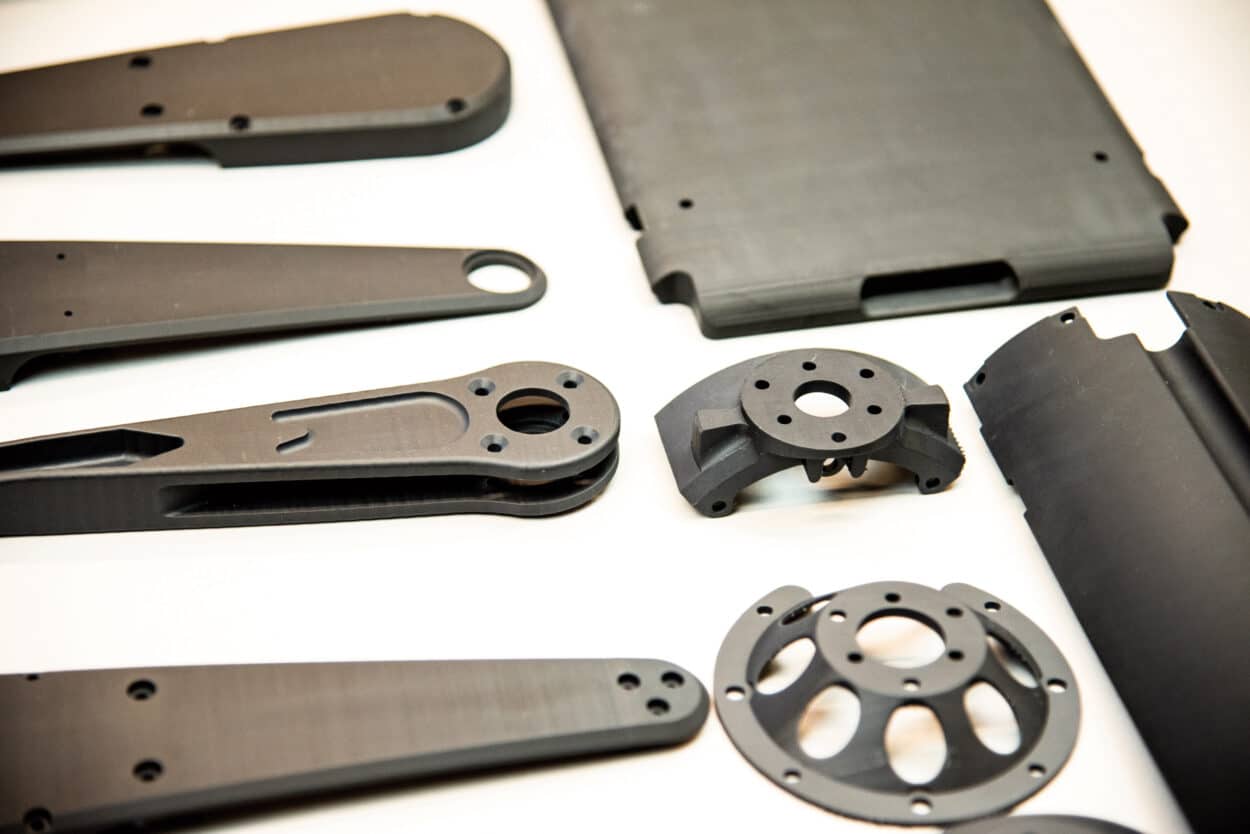
P3 is an evolution of the well-established digital light processing (DLP) technology application for AM. Part files are sliced and these slices are projected, one at a time, up onto a resin-covered build tray. By manipulating four highly-controllable physical parameters (light, environmental stability, pneumatic separation, and motion) with a powerful software engine, P3 is able to maximize the inherent benefits of DLP and unlock greater material choice, higher throughput, and increased repeatability.
Need for Speed
Because the P3 platform projects a whole ‘slice’ of a part as a single image, it cures the entire area in one go rather than tracing it out point by point. This makes the printing process significantly faster, while still allowing parts up to 192 x 108 x 370 mm or multiple nested parts to the same volume.
Part quality
Another historic limitation of AM that technological innovation helps to address is the finish of the final part. Traditionally injection molding could not be beaten when it came to surface finish. But through tight control and the inherent stability of the process, parts produced using P3 technology rival injection molding for surface finish and aesthetic appeal. And, of course, they can be produced in geometries impossible to recreate with molding.
Materials Matter
A decade ago, available photopolymer materials immediately removed AM from consideration as a production technology. Characteristics such as strength, toughness, temperature resistance, and elasticity were insufficient for many potential uses. In contrast, today, with advancements in digitization, we can now measure and control the polymerization process to a much greater degree. As a result, a large and growing number of specialty materials companies have been able to harness the power of the P3 platform to push materials technology to new levels. BASF, Covestro, Henkel, and others have created a photopolymer materials selection that would have seemed unthinkable even a few years ago.
We now see:
- Applications requiring high-temperature resistance — with a heat deflection temperature of up to 80 °C.
- Biocompatible materials with ISO 10993-5 and ISO 10993-10 certification.
- Materials with properties analogous to polypropylene, ABS, and commercial-grade TPUs
These material properties are available via traditional manufacturing methods, but with additive manufacturing, they are accessible with new levels of production flexibility and design freedom.
Software to Scale
In addition, Stratasys’ recent creation of its GrabCAD® Additive Manufacturing Platform, an open and enterprise-ready software platform, enables manufacturers to manage production-scale AM operations. This provides manufacturers with software designed for the unique needs of at-scale AM across the entire digital thread – from design through production – while also integrating with Industry 4.0 infrastructure and enterprise applications.
Trailblazing Use Cases
There are so many things manufacturers can do with P3 technology, the question really becomes what should they do? Here are four great opportunities today:
- Electrical connectors, adaptors, and wiring brackets: Small enough to be nested efficiently within the P3 build volume and built-in significant production scale. Can make use of the high-temperature, impact-resistant, or ABS- and PP-like materials
- Industrial machine components —Housings, buttons, clips, seals & gaskets: Takes advantage of the production throughput for volume manufacturing and the excellent surface finish. Can make use of ABS- and TPU-like resins, clear flexible resins, or durable low-cost resins.
- Medical device components: Capitalise on the medical grade and biocompatible ABS- and PP-like materials on the P3 for maximum flexibility for flexible production of biocompatible housings, fluid delivery systems, and more.
- Molds for low-pressure, low-temperature molding: Using the quick-printing and -processing resins exceptional surface quality can be used to generate mold for footwear components, PU molds, or sample moldings.
Beyond these examples, a world of opportunity awaits, and with materials development continuing at a pace the P3 platform will only become more versatile and solve even more manufacturing challenges, in the future. Once the part, material, and process are running in harmony, AM really can challenge other technologies in true production.