Researchers from the Tokyo University of Science have developed a new digital twin technology for laser-directed energy deposition (LDED) repair, which automatically determines optimum forming conditions and reduces metal powder waste. Their conclusions were published in the Journal of Thermal Spray Technology
Content provided by Tokyo University of Science
A group of researchers from the Tokyo University of Science (TUS) has developed a repair technique using LDED (Laser-directed energy deposition). They found that the residual stresses in the deposited layer were significantly lower than those obtained through conventional repair methods.
A New Repair Technique
The researchers’ new technique uses a mathematical model to automatically generate a metal powder deposition region, eliminating the need for guesswork and improving the repair process. The technology has been verified through experiments and has been found to produce lower residual stresses than conventional repair methods.
Conventional metal 3D-printed repair methods require bulky equipment and result in a lot of wasted metal powder. LDED, on the other hand, uses a laser beam to melt and fuse metal powders in a more compact and efficient process. However, determining the optimum forming conditions for LDED has traditionally been a trial-and-error process, as Dr. Masayuki Arai, Professor of Mechanical Engineering at Tokyo University of Science explained:
“Using our technique, the surface shape of a metal structure can be completely restored on-site, and the disposal of the metal powder required for repair can be significantly reduced. However, the optimum forming conditions required for the widespread application of this technology in the industry had to be hitherto determined by a trial-and-error process.”
The new model, which incorporates thermal radiation-thermal conduction and viscoplastic-thermoplastic constitutive models, can simulate a wide range of state changes from melting to solidification of the deposited metal powder layer. It can also predict the forming process conditions, temperature distribution, deformation state, and residual stress distribution in advance.
Improving Industrial Sustainability
Repairing damaged mechanical parts in industrial machinery and structures is becoming increasingly important for improving industrial sustainability.
LDED not only offers the benefit of compact equipment but also a marked decrease in metal powder waste. Additionally, this technology allows for in-situ metal powder fabrication in a 3D shape on the surface of a substrate, making it a viable option for repairing metal machines.
This new digital twin technology can be applied to various industrial applications in the future, improving the efficiency and sustainability of repair processes.
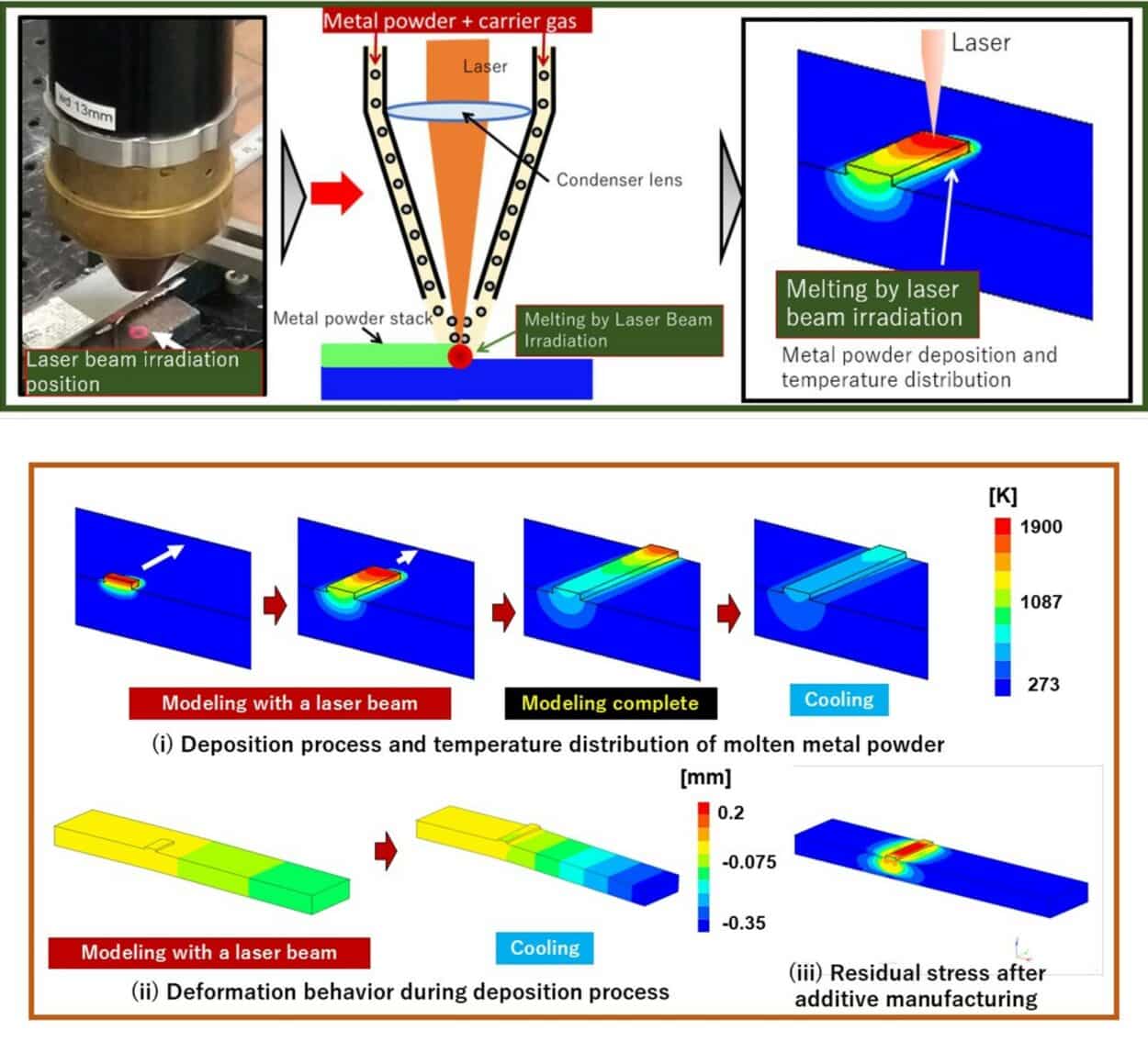