Lithium batteries are in rising demand but their risk of overheating slows the market growth. This risk can be rectified by a detection process in quality control. Most detection methods are time-consuming. Read more about laser-induced breakdown spectroscopy (LIBS) which helps you gain productivity and profitability while detecting harmful particles.
Written by Dr Kay Scheffler, Dr Konstantin Kartaschew, and Dr James DeRose, Leica Microsystems
The global lithium-ion (Li-Ion) battery market was valued at US$ 32.9 billion in 2019 and is expected to grow at a compound annual growth rate (CAGR) of 13.0% from 2020 to 2027 [1]. But issues like overheating and short lifetime [2,3] slow down the market growth visibly.
In many cases, these issues can be rectified at the quality control stage of the manufacturing process. Overheating during use can be traced back to the presence of metal particles in the electrodes, fuel-cell separators, and other parts of Li-Ion batteries. [4-6].
The challenge for battery manufacturers is to ensure their QA/QC procedures are robust enough to capture these impurities but are not so arduous as to slow down the manufacturing process or lead to significant additional expenditure.
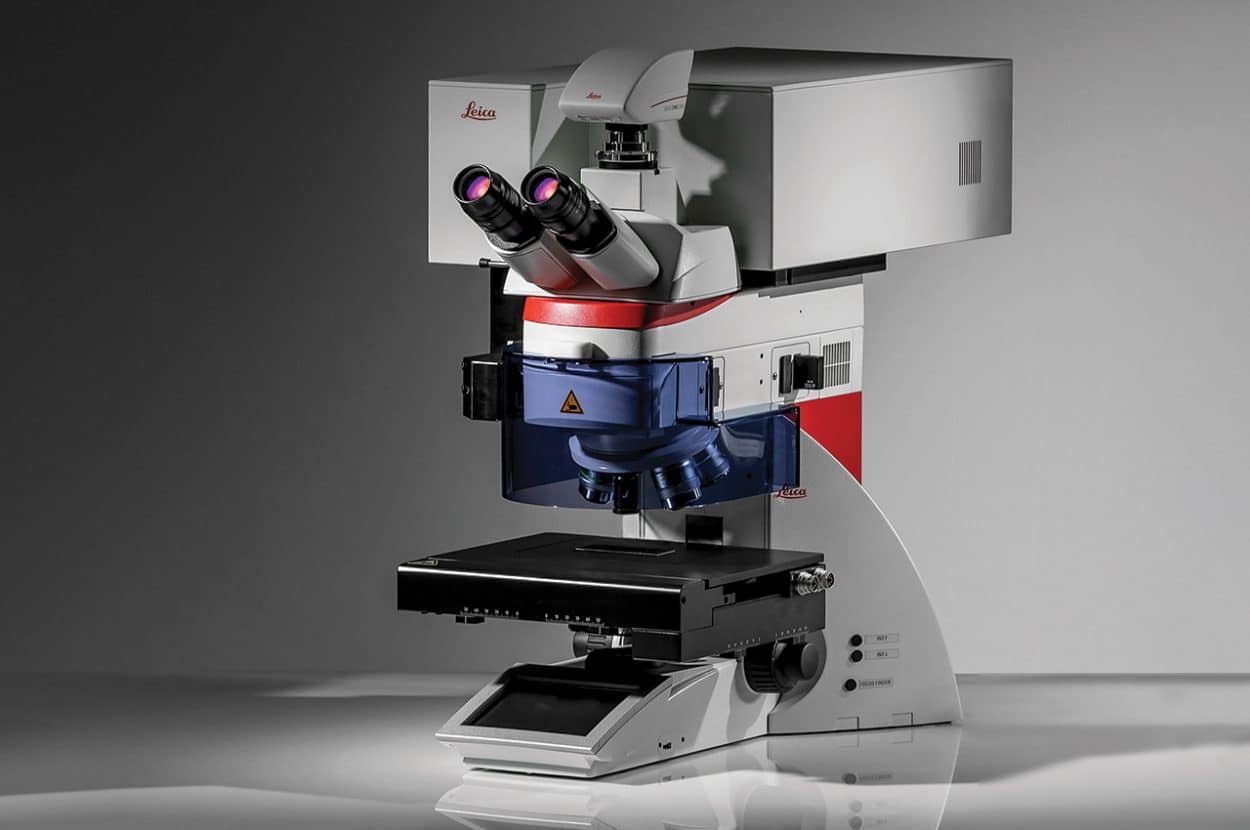
Established methods of detecting impurities are time-consuming
One of the fundamental issues facing manufacturers is that established methods of detecting impurities (https://downloads.leica-microsystems.com/LIBS%20Module/Brochures/DM6_M_LIBS_Lithium-ion%20batteries_flyer_EN.pdf) in Li-Ion batteries are complex, time-consuming, and very difficult to integrate into the production line [7].
The process normally used for quality control processes in industrial manufacturing environments is energy dispersive x-ray spectroscopy (EDS) using a scanning electron microscope (SEM). SEM-EDS often requires special sample preparation and transfer of the sample into a vacuum for observation and analysis – a time-consuming and technically challenging process.
Additionally, as it is a complex imaging method, SEM-EDS is very difficult to incorporate directly into the production line. This means samples need to be sent off of the line to be analyzed, taking hours or possibly even days before the results are available.
Methods that are easier to incorporate into the production line, like x-ray fluorescence (XRF) and glow discharge optical emission spectrometry (GD-OES) have other disadvantages. XRF cannot detect accurately light elements like Li [8,9] and GD-OES often causes significant damage to the sample and can be difficult to use with insulating materials [9-11].
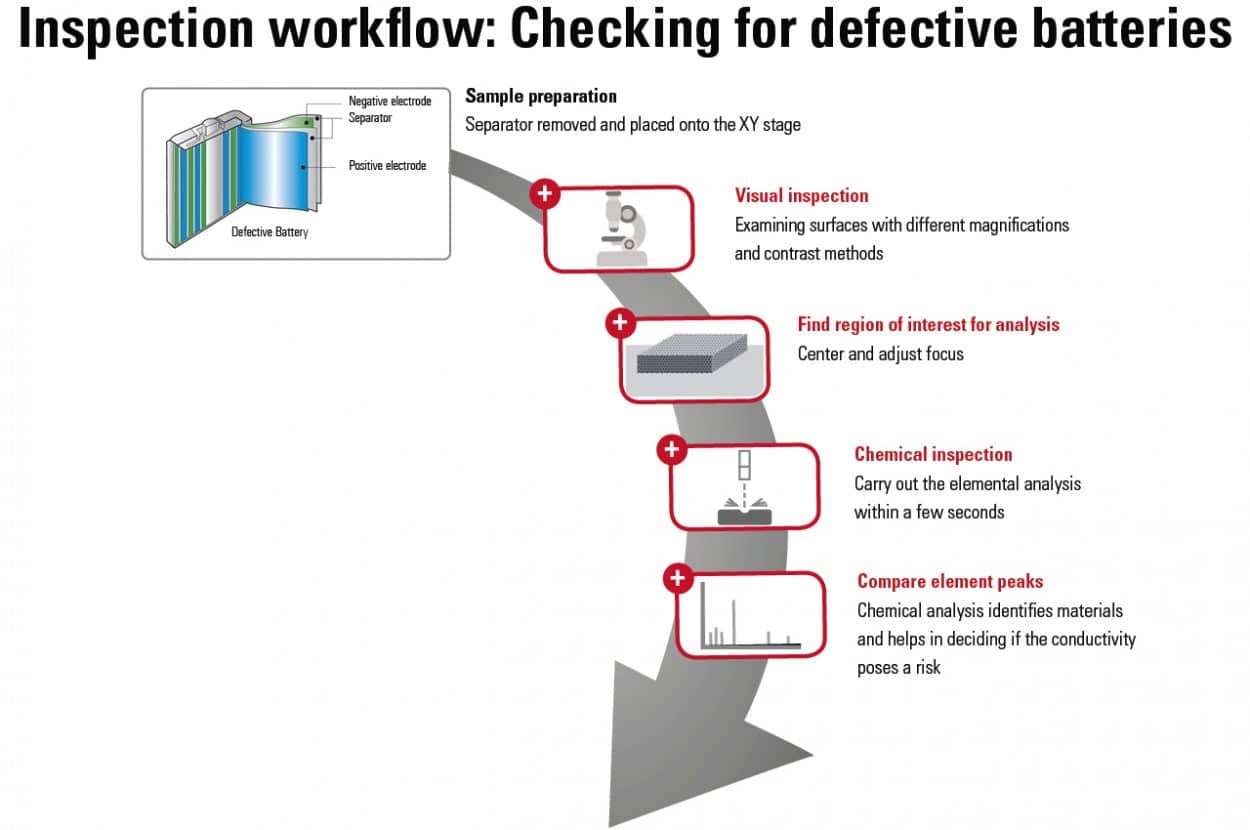
New detection method makes results available in seconds
The LIBS process (https://downloads.leica-microsystems.com/LIBS%20Module/Brochures/DM6_M_LIBS_Lithium-ion%20batteries_flyer_EN.pdf ) is a new method that combines optical microscopy and laser-induced breakdown spectroscopy to achieve visual and chemical sample information in much reduced time.
The LIBS process (https://downloads.leica-microsystems.com/LIBS%20Module/Brochures/DM6_M_LIBS_Lithium-ion%20batteries_flyer_EN.pdf ) does not require an SEM, so many of the most time-consuming steps are eliminated from the process: e.g. no additional sample preparation is required before analysis. Results are available in seconds, meaning analysis can be undertaken quickly as part of the quality control process, without needing to use laboratory support.
The DM6 M LIBS system (https://www.leica-microsystems.com/products/light-microscopes/p/libs-module/ from Leica Microsystems (https://www.leica-microsystems.com/) was designed specifically for industrial applications like battery manufacturing to deliver faster results when speed, as well as accuracy, are paramount for long-term success.
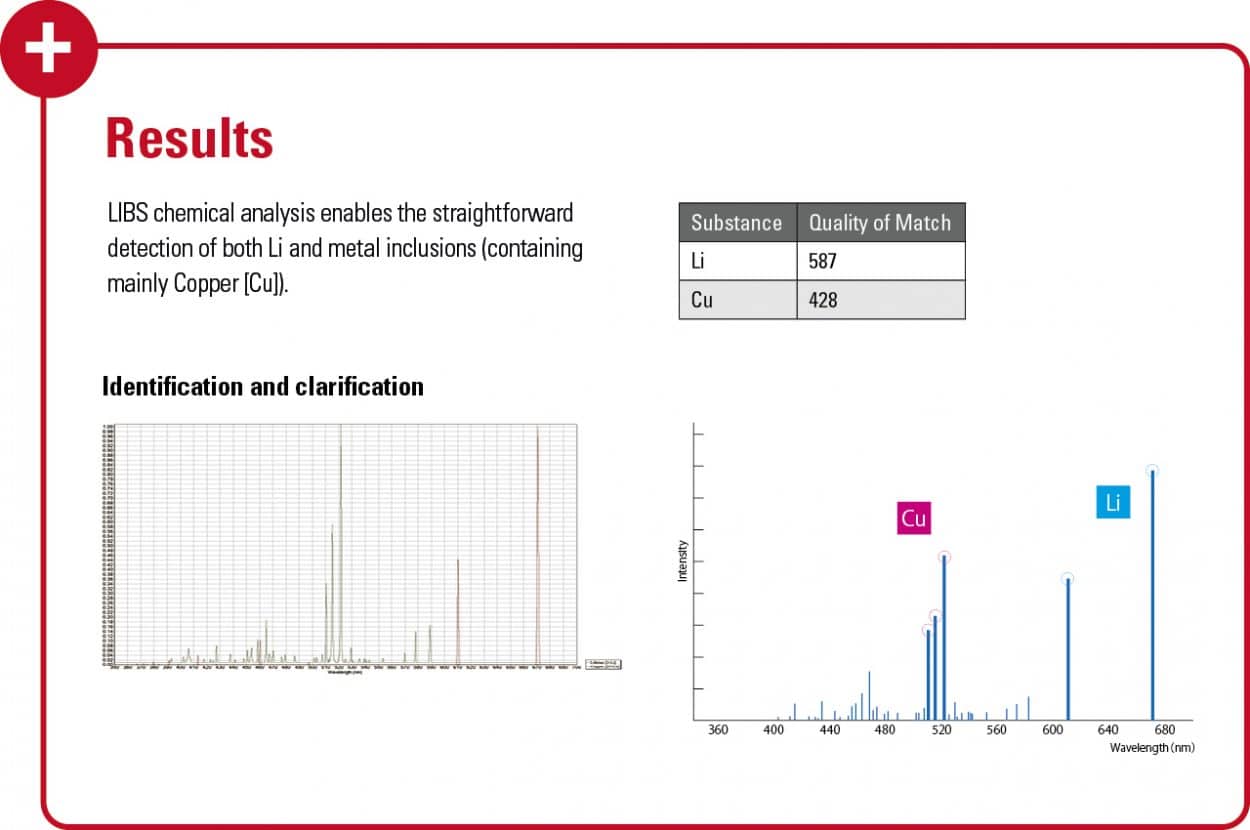
Don’t miss out on the future by staying with the accepted status quo
Many industries have not embraced LIBS (https://www.leica-microsystems.com/science-lab/see-the-structure-with-microscopy-know-the-composition-with-laser-spectroscopy/) yet, perhaps because SEM-EDS, XRF, or GD-OES are the accepted status quo solutions. Indeed, in product development, quality control, and failure analysis obtaining reliable results and achieving the desired product quality must always be the priority.
But industrial manufacturers must not let the desire to stick with the ‘tried and tested’ get in the way of progress or deny them significant gains in productivity and profitability. SEM-EDS and other techniques still add great value in certain applications, but for rapid, accurate quality control on a fast-moving production line, manufacturers should consider optical microscopy and LIBS (https://downloads.leica-microsystems.com/LIBS%20Module/Brochures/DM6_M_LIBS_Lithium-ion%20batteries_flyer_EN.pdf